Environmental Success At Gallstown Quarry
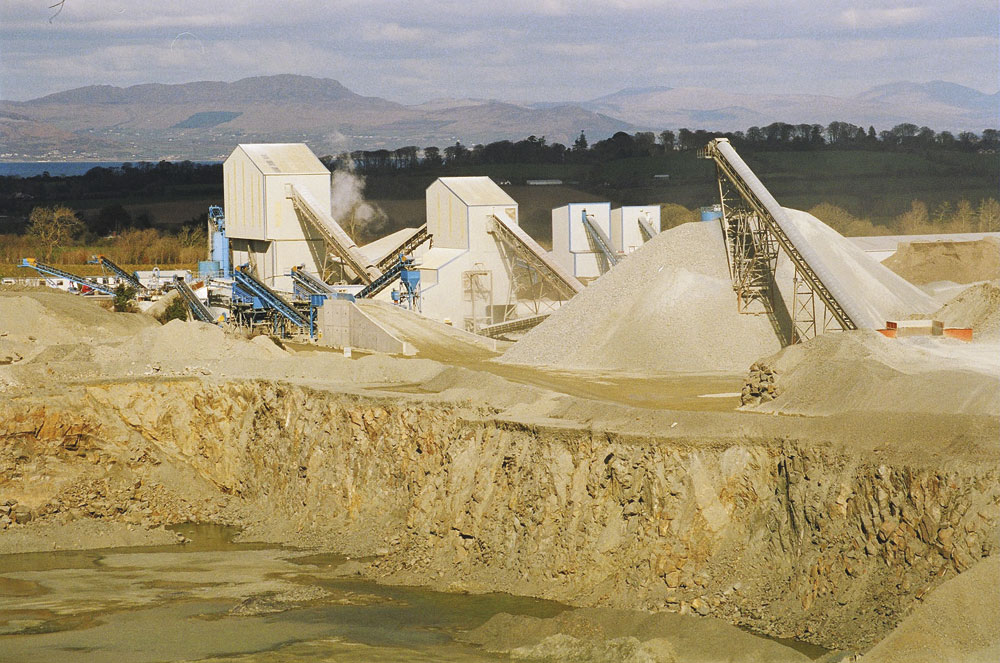
High environmental standards bring rewards for Irish quarry operator
Kilsaran Concrete’s Gallstown Quarry is located due north of Drogheda and south-east of Dunleer in Co. Louth, not far from the Dublin–Belfast motorway. County Louth itself is located on the north-eastern coast of Ireland, forming part of the border with Northern Ireland.
The existence of high-quality greywacke sandstone has been proven within the company’s extensive landholding and planning permission has been granted for quarrying over an area of approximately 43ha.
Kilsaran Concrete commenced commercial rock extraction at Gallstown in 1995 and since then routine environmental monitoring of noise and dust has been carried out on a regular basis. Likewise, every blast that has ever take place at the site has also been monitored.
The quarry is operated to the very highest environmental standards, with procedures, practices and policies adopted to minimize the impact of the quarry on all aspects of the local environment; this includes the implementation of a self-imposed environmental management system.
In addition, a pioneering approach to production helps to maximize the potential of the natural resource, which has a doubly positive impact on the environment by reducing waste and the need to source additional reserves from elsewhere.
The water resource at Gallstown Quarry is carefully managed as the bedrock is an aquaclude, ie it does not hold or transmit groundwater readily. All available water on site is accounted for and utilized in dust suppression and in the various manufacturing processes. Water is recycled and reused utilizing specialist plant and any controlled discharge from the site is treated to comply with a discharge licence.
The greywacke deposit at Gallstown possesses significant attributes in terms of its quality and physical properties, including a high polished-stone value of 65 and low aggregate impact and aggregate abrasion values.
The stone is used as a construction material in a broad range of applications, including high-quality surface-dressings. It is suitable for use in all road-surfacing projects including motorway construction.
Industry-standard blasting methods are used to extract the rock, which a hydraulic excavator feeds directly to a mobile primary and secondary crushing plant at the working face. The material is then transported by dumptruck to a fixed tertiary crushing and screening plant. The quarry produces a range of aggregates, asphalt and macadam, hardcore and fill materials. Ready-mixed concrete and concrete blocks are also manufactured on site in a modern plant utilizing raw materials from the quarry.
Originally Kilsaran Concrete hauled the aggregates produced at Gallstown some 12km to the company’s long-established depot at Kilsaran village, where ready-mixed concrete and concrete blocks were manufactured. However, this was not environmentally or economically sustainable, so a decision was made to relocate these facilities within Gallstown Quarry. By the late 1990s, following planning approvals, operations had been switched to the quarry.
At this time the majority of the aggregate supply for the production of value-added products was sourced from the quarry, however there existed a mix-design prerequisite for sand, which still had to be imported.
Significant effort has been made to maximize the potential uses of the quarried stone by minimizing waste.
KEY ENVIRONMENTAL BEST PRACTICE
Noise
Noise minimization
Site-specific measures that have been implemented or contribute to noise reduction at Gallstown are:
- The quarry workings are remote from neighbouring residences.
- Operators of mobile plant are instructed to throttle down or switch plant off when not in use.
- Primary and secondary crushing takes place within the quarry void at the working face.
- Fixed crushing and screening plants are fully enclosed.
- The fixed plant is computer controlled to ensure only that part of the plant required at any given time is switched on.
- Regular and effective maintenance of fixed and mobile plant is carried out.
- The asphalt, ready-mixed concrete and concrete block plants are modern, well maintained and fully enclosed.
- The block machine is enclosed within a triple-glazed acoustic room within the block plant.
- Trafficked areas around the manufacturing facilities are fully paved.
- The quarry access and entrance area is paved, helping to minimize potential noise associated with transport operations.
- Extensive landscaped screening mounds have been constructed along the site boundary between the working area and local residences/public road.
- Adjoining county road has been upgraded resulting in less noise impact from transport vehicles.
Noise limits and monitoring
A planning condition noise threshold of 55dB(A), when measured at any house in the vicinity of the quarry, has been imposed by the planning authority. Kilsaran Concrete have carried out regular monthly noise monitoring at a number of locations around the quarry since the commencement of commercial extraction in 1995. The results demonstrate compliance with the imposed noise threshold.
Blasting and vibration
Measures to minimize effects
Good blasting practice is carried out at the quarry under the expert supervision of specialist contractors Irish Industrial Explosives.
Shotfiring rules are in place and strictly adhered to, blast design is cognisant of the location and proximity of neighbouring properties, and emulsion is used in preference to cartridges. Blasts are bottom initiated by delayed detonation to minimize the maximum instantaneous charge of the blast and its impact on the environment.
Blasting is confined to the hours between 11am and 5pm Monday to Friday, with notification of each blast given in writing, 24h in advance, to the occupiers of all houses within a 500m radius of the quarry.
Thresholds associated with blasting
The planning conditions state:
The transmitted ground vibration arising from any blast at the site shall not exceed a peak particle velocity of 12mm/s in any of the three mutually orthogonal planes at the threshold of any house in the vicinity of the site.
The air overpressure arising from any blast carried out at the site shall not exceed 125dB (linear) maximum peak at frequencies of 2Hz or over when measured outside the nearest house to the blast.
Blast monitoring
Every blast at the quarry is monitored with records kept of vibration, air overpressure, the explosives charge and the distance from the blast to the monitoring location.
Dust and air quality
Measures to minimize dust emissions
Measures that have been adopted to effectively minimize dust emissions are:
- Quarry drill rig is fitted with a skirt and bag filter.
- Spray bars are fitted to the primary and secondary mobile crushers.
- Quarry haul routes are maintained and sprayed with water during dry periods by on-site mobile dust-suppression unit.
- Fixed plant is fully enclosed and fitted with an automatic wet dust-suppression system comprising 21 spray points controlled by 18 solenoid switches.
- Transfer conveyors at the fixed quarry plant are enclosed.
- The access roads, car and truck parks are surfaced with asphalt and kerbed.
- A powered wheelwash is installed within the paved area of the quarry. This self-cleaning unit is fully automatic with horizontal and vertical spray bars.
- The ready-mixed concrete and block batching plants are enclosed.
- A mobile dust-suppression unit is used to wet internal areas of the quarry during dry periods.
- The cement silos are fitted with high level alarms, to prevent overfilling, and reverse-air jet filters, to intercept cement particles dislodged during the filling process.
- Exhaust gases from the asphalt plant dryer pass through a dry scrubber and the recovered solids are recycled as filler.
- A contract road sweeper is employed to sweep the entire yard surface on a twice weekly basis and also in the event of an accidental spillage.
Dust thresholds
The planning conditions state:
The total dust emissions arising from on-site operations associated with the proposed development shall, when measured at the boundaries, not exceed 130mg/m2/day, averaged over 30 days.
Dust Monitoring
Fugitive dust is monitored at two locations at the boundary of the quarry using the Bergerhoff standard method.
Resource conservation and waste minimization
This part of Co. Louth is generally devoid of natural sand and gravel deposits, so sand originally had to be hauled to site by road from up to 40km away.
Following a decision to start manufacturing an artificial sand, however, the first phase made use of the 0–3mm dust being produced at the quarry, which in the past had been a low-value by-product. The dust was fully analysed and a specialized sand-washing plant incorporating hydrocyclone technology and a dewatering screen was commissioned from CDE.
A thickener receives the overflow (comprising waste water and waste fines) from the washing plant, to which a flocculant is added. The resulting sludge is pumped from the thickener, by a heavy-duty slurry pump, to a remote settling pond.
Meanwhile, clean water is steadily released to an adjacent freshwater storage tank.
From here it is pumped back to the washing cycle, thereby greatly enhancing water recycling and reducing freshwater requirements to top-up only.
As well as reducing waste to an absolute minimum, the washing plant allows water resources to be fully managed.
Once this plant had proven effective in recovering a high-value product from a low-value by-product, a review of the quarry operations highlighted another area of production that could also benefit from the appliance of new technology.
At the primary crusher a grizzly screen is used to remove any –40mm material prior to crushing. In the past this material was sold periodically as a fill material of low value but over time a large stockpile had accumulated. This was obviously not an efficient use of the natural resource.
An additional plant has since been commissioned incorporating a vertical-shaft impactor (VSI), coupled with technologically advanced Bivitec screens from Binder & Co. This plant crushes, reshapes and screens the –40mm feed to produce a 0–8mm material, which in turn is washed by the CDE sand-washing plant.
The main benefit for Kilsaran Concrete stemming from the introduction of this new crushing and washing system is a 50% reduction in the amount of natural sand that now needs to be imported.
Apart from cost savings, this is also of great benefit to the environment as there are fewer heavy goods vehicle movements, less fuel consumption and less impact on the roads. Moreover, the demand for natural aggregate supplies has been reduced and the full potential of the resource at Gallstown has been met.
Water management
Because the bedrock at Gallstown is a poor aquifer, all available groundwater and surface-water run-off are managed to ensure a consistent supply of water is available for dust suppression, manufacturing processes and to prevent pollution.
A detailed water-management plan is in place at the quarry and sources of water have been identified and developed.
Top-up water for the CDE sand-washing plant and dust suppression at the VSI plant is supplied directly from the quarry sump. Water for the ready-mixed concrete and concrete block plants are sourced from a dedicated well developed under the supervision of a hydrogeologist.
Site surface water is utilized for dust suppression and potable water is sourced from another dedicated well. Water usage at the wheelwash is minimized by recycling the wash water.
Surface water is collected from the paved areas of the site by means of a series of settlement ponds located adjacent to the ready-mixed concrete plant. This water is used in a closed circuit to wash-down (and wash out) the concrete truckmixers and also as an additional source of water for batching concrete.
The CDE sand-washing plant has been specifically engineered to minimize the use of water by careful recycling and the appliance of best practice.
Surface-water cut-off drains are provided along the lower sections of the site to collect and divert surface-water run-off through an oil interceptor before being discharged off site.
Surface and groundwater protection
Discharge of water from the quarry is conducted under a licence granted by the local authority under the Local Government (Water Pollution) Acts 1977 and 1992.
Significant improvements have been made on site in recent times with regard to water pollution prevention and site water management, including:
- Discharge of waters under licence through water-treatment area (settlement pond and oil interceptor). Discharge and receiving waters are monitored on a monthly basis and discharge volumes are measured.
- Dewatering – a ‘cleaner’ electric pump is used instead of a diesel pump.
- Diesel tanks are bunded.
- Foul waters are treated at a septic tank and proprietary effluent treatment tank, discharging through a constructed percolation area.
- Recycling of wash water at the CDE sand-washing plant utilizing flocculants.
- Wash-out water used at the ready-mixed concrete operation is recycled and reused.
- Provision of site personnel training in oil spill emergency procedures, and provision of various strategically located oil spill kits.
Water discharge thresholds and monitoring
Detailed thresholds for water effluent are given in the discharge licence; they include thresholds for suspended and dissolved solids, dissolved oxygen, pH, temperature and maximum permitted volume of discharge. A sample of water from the discharge point is taken and analysed every month, in compliance with the terms of the discharge licence.
Waste management
Domestic waste generated at the offices and employee facilities is collected by a licensed waste-collection contractor. Likewise, used batteries are removed from site by a licensed contractor for disposal.
Truck maintenance/servicing is carried out within a dedicated workshop building where provision is made for the safe handling and storage of oils and lubricants. Drip-trays, spill kits, dedicated waste filter containers etc are provided. All waste oil that arises from the servicing of mobile or static plant is removed from site by a licensed contractor.
Kilsaran Concrete have applied for a waste-recycling permit and associated waste-collection permits to allow them to recycle material produced by their road-contracting business. At present, returned concrete and asphalt products are stored in a segregated area and periodically recycled for resale as a general fill material.
Significant effort has been made by the company to maximize the potential of the rock deposit by minimizing the generation of low-value material and waste. What was once a very low-grade by-product of the aggregate production process has been turned into a valuable sand grade using the new techniques outlined above.
RECOGNITION OF ENVIRONMENTAL BEST PRACTICE
Kilsaran Concrete are members of the Irish Concrete Federation (ICF), which represents 95% of the production output in the quarrying/concrete products sector in the Republic of Ireland. Earlier this year Gallstown Quarry received a Five Star Award in the ICF’s biannual national Green Aggregates Award, an initiative promoting good environmental-management practices and operational performance.
Following hard on the heels of this achievement, Kilsaran Concrete entered the UEPG (European Aggregates Association) Sustainable Development Awards. The objective of these awards is to reward those aggregates companies that have successfully integrated the social, economic and/or environmental dimensions of sustainable development into their operations by solid achievements beyond what is expected, and to encourage the whole industry to reinforce its commitment to sustainable development.
At a ceremony in Brussels on 24 May 2005, in the presence of around 165 representatives from the European Commission, European Parliament, NGOs, academia and national UEPG member associations, Kilsaran Concrete were presented with a Special Award for Outstanding Team Dedication in the Environmental Best Practice category, in recognition of the good practice in evidence at Gallstown Quarry.
ACKNOWLEDGEMENT
The editor wishes to thank Fergus Gallagher, chartered minerals surveyor with Kilsaran Concrete, for his help in the preparation of this report.