Coating Plant Upgrade In Ipswich
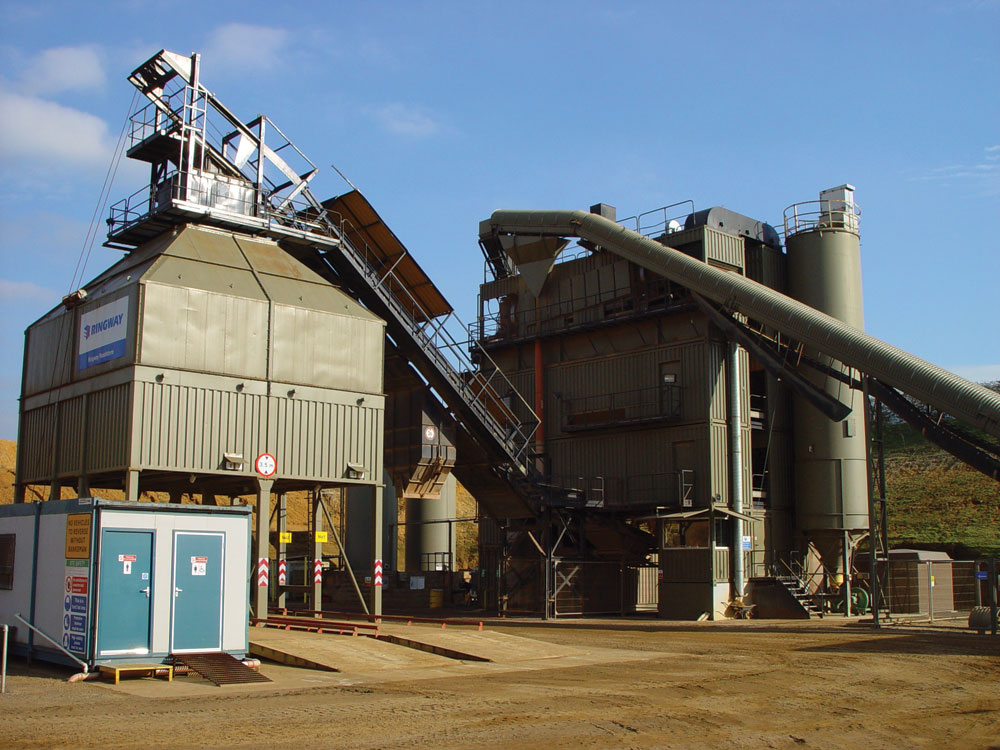
Ringway adopt German drum-screen technology at key East Anglian site
Since their formation over 30 years ago, Horsham-based Ringway Group have charted a successful course that has seen them develop and grow with the highways maintenance sector, accumulating skills and expertise along the way and pioneering innovative partnering and service solutions for maintaining and improving the nation’s roads. Today, with operations stretching from Devon in the south to the Scottish Highlands in the north, Ringway are one of the key players in the highways maintenance business in the UK, with an annual turnover in excess of £400 million and a workforce totalling some 4,000 employees.
Following their initial independence and a subsequent period under the ownership Jean Lefebvre, Ringway now benefit from the technical expertise and resources of parent company Eurovia, the road construction and materials resource division of Vinci – the world’s largest construction and infrastructure group. Eurovia themselves are one of Europe’s largest roadworks and materials recycling companies, and the biggest French producer of road aggregates with over 200 quarries largely located throughout continental Europe. As such, the company provide a guaranteed source of supply for many of the raw materials required by Ringway, who operate a number of coating plants but have no aggregate resources of their own.
As suppliers of a full range of quality-assured hot-rolled asphalts and proprietary products, Ringway Group have recently conducted a significant programme of investment to ensure the highest standards of efficiency, quality control and environmental protection are maintained at several of their key strategic locations. This programme has resulted in upgrading of the company’s Thames-side facility at Dagenham, the development of a new coating plant facility at Immingham docks, and the formation of Northfleet-based North Kent Roadstone in a 50:50 joint venture with Foster
Yeoman.
Meanwhile, in East Anglia, the company have recently brought their Ringway Roadstone asphalt operation, located on the eastern outskirts of Ipswich, fully up to date by replacing an ageing 55-tonnes/h Goodwin Barsby mobile asphalt plant, which had been in operation at the site for 18 years, with a fixed plant capable of producing up to 140 tonnes/h. The main driver behind the change was the need for increased efficiency and volume capacity, as well as an improved recycling capability. Unlike the replacement plant, which is equipped with 10 in-line cold-feed hoppers, two RAP feeders and 400 tonnes of mixed-material storage capacity, the old Goodwin Barsby unit had just six cold-feed bins, no hot recycling facilities and no hot storage capacity.
The replacement plant, which was acquired second hand from an existing Eurovia site on the continent, is believed to be the first of its kind to be installed in the UK. Manufactured by German firm Lintec and housed within a series of twin-stacked and bolted together ISO sea containers, it features horizontal dryer drum-screen technology, which eliminates the need for a conventional hot-stone elevator and vibrating screen deck. Both plants were operated in tandem for a six-week period during construction and commissioning of the new plant in order to maintain continuity of supply.
The new cold-feed system is charged with aggregates drawn from ground stockpiles. With no in-house aggregate supplies, Ringway Roadstone’s ‘higher end’ raw material requirements are sourced from parent company Eurovia and externally from Lagan, with all materials imported via Brett Aggregates’ wharf on the river Orwell in Ipswich. Sand is supplied by Brett’s Foxhall Quarry, which is located directly adjacent to the coating plant. Materials are fed from the cold-feed hoppers, via speed-calibrated belt feeders, a collecting belt and a link conveyor equipped with a check weigher, on to an inclined chevron belt for delivery to the dryer drum-screen, which is situated at the highest point of the plant. Mounted on four individual drive rollers, the gently inclined drum measures 8.5m in length by 1.8m in diameter and is equipped with a 13MW burner.
Once the raw material has passed through the dryer drum, aided by internal lifters, the heated aggregates are fed on to the drum’s integral screening section whereupon they are carried along in a counterflow direction by the rotational movement of the drum and its external feed spirals until they pass through one of the five screen surfaces (set at increasing apertures) and drop into their respective hot stone bin.
A key advantage of the Lintec dryer drum-screen system is that it offers considerable energy savings by eliminating the hot-stone elevator and vibrating screen associated with conventional tower plants. By combining the heating and screening of the aggregates in a single process, the heat loss resulting from material transportation is eliminated, while the heated material itself benefits by absorbing radiated heat from the drum shell during the screening phase, thereby effecting further savings. Ringway have also found screen wear to be very evenly distributed across all five screen surfaces, which is delivering further savings through reduced wear and tear and less-frequent maintenance. In addition, thanks to a highly efficient exhaust gas/dust extraction system, fugitive dust emissions of around 14ppm are being recorded, well below the site’s 50ppm limit set by the local authority.
From this point on the materials are processed in the conventional way with the hot aggregates, filler and bitumen being delivered into the plant’s 2,500kg capacity twin-shaft paddle mixer via their respective weigh vessels. Ringway currently add 10% recycled asphalt planings (RAP) into all basecourse and binder mixes. This material is fed by one of two highly calibrated volumetric cold feeders, via a secondary inclined chevron belt, to the dryer drum-screen, where it is discharged directly into the first hot-stone (sand) bin via a slotted bypass arrangement. In addition, to cater for the production of thin surfacings and SMAs, the plant is equipped with polymer-modified bitumen handling equipment and an automatic pelletized-fibre handling system, as well as a facility for the manual addition of small batches of loose fibres.
A travelling skip is used to carry mixed materials from the coating plant to the adjacent hot storage/lorry load-out facility, which comprises four 100-tonne capacity heated and insulated storage bins mounted in a cluster directly above two new Avery Weigh-Tronix Bridgmont weighbridges. This combined load-out/weighing arrangement helps improve on-site safety by eliminating the requirement for delivery vehicles to drive to a separate weighbridge office, thus reducing traffic movements around the site and helping to prevent accidents by keeping people and vehicles apart.
The fully automated plant is monitored and controlled from a control room housed within the lowest container facing the load-out section. Operational control is via a PC-based Lintronic computer control system, which incorporates full batching, production, delivery ticketing and management statistics capabilities. Supplied by Lintec, the system provides for sequential start-up and shutdown of the plant and incorporates and number of self-checking routines, with double checking of all critical systems. The system is also modem linked to Lintec’s headquarters for troubleshooting and maintenance purposes.
Ringway Roadstone now have the capacity to supply a full range of products to suit their local market, which covers mid-Essex and the whole of Suffolk. As well as supplying larger volumes of HRAs and proprietary products for major customers and local authorities, the plant is also well equipped to cater for Ipswich’s large, low-volume, collect-trade client base. As part of Ringway Roadstone’s integrated quality, safety and environmental management system, the new plant has recently been re-audited for accreditation to the ISO 9001 quality management standard, and the next goal is ISO 14001 environmental accreditation, which the company confidently expect to achieve by mid-2007.
Acknowledgement
The editor wishes to thank Ringway Group for permission to visit the site and, in particular, Patrick Riley, divisional director, and Colin Adams, site manager, for their help in preparing this article.