Cairneyhill Gears Up For Growth
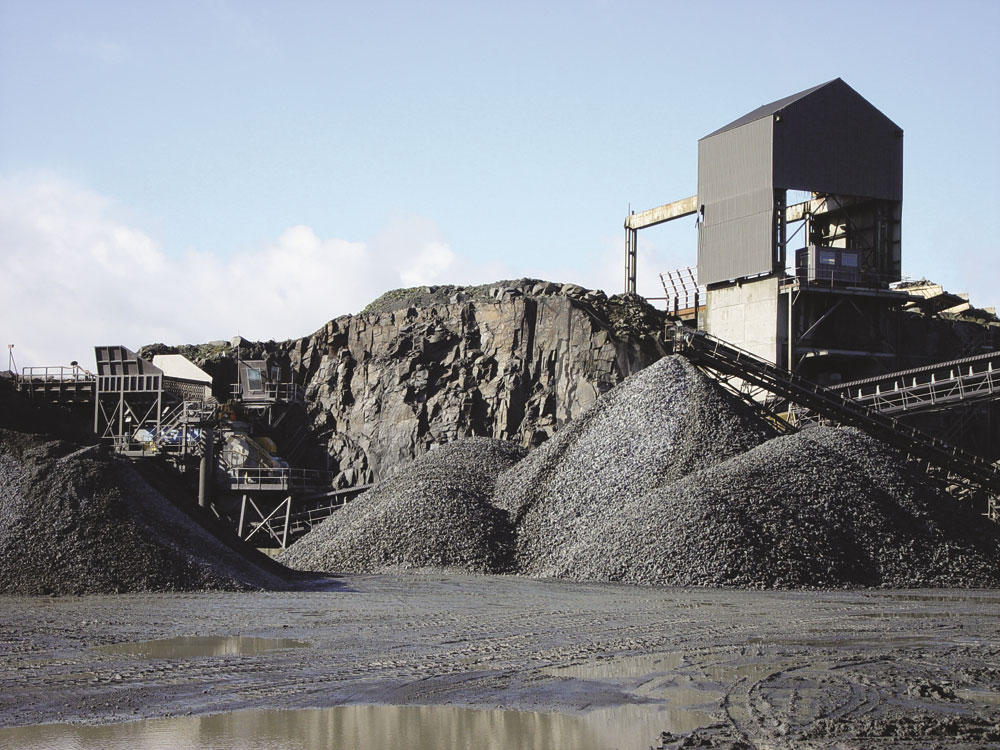
Major replant boosts product quality and productivity at key Scottish site
Last year Cairneyhill Quarry, near Caldecruix, in Scotland’s central belt, underwent a major programme of investment worth close on £4 million that has transformed processing operations at the site and firmly established the quarry as one of the key units within Tarmac Northern Ltd.
With approximately 27 years’ consented reserves of high-psv quartz dolerite or ‘whinstone’ remaining at the site, and significant potential resources available after that, the expenditure has provided Cairneyhill with a modern and efficient plant to cater for operations well into the future.
The replant included the installation of a new primary crusher, together with new mobile plant to feed it, as well as extensive modifications to the tertiary and quaternary crushing sections and a new state-of-the-art coating plant. These changes were designed to alleviate a number of production bottlenecks in the existing operation and have allowed an additional 400,000 tonnes a year to be produced without increasing working hours.
Before selecting a new primary crusher for the site, a careful assessment of different machines and manufacturers was undertaken, including investigations into the possibility of using a tracked mobile crushing system. However, because of the particular face configurations at Cairneyhill, which stem in part from the presence of three major faults that pass through the quarry, mobile techniques were found to offer no real operational advantages or cost savings over a fixed plant. It was decided, therefore, that ‘moving the quarry to the crusher’ remained the best option.
As a result of these evaluations Sandvik were awarded the contract to supply the new primary crusher, a decision made largely on the basis of the proven longevity of the company’s machines and also due to the complete package they were able to offer in terms of cost, performance guarantees and extended warranties.
In addition, Sandvik were appointed as the lead contractors for the project, with responsibility for selecting and co-ordinating the various installation, mechanical and electrical engineering teams, as well as carrying out final commissioning.
Primary stage
Prior to the recent investment, the task of primary crushing at Cairneyhill was carried out by an ageing Allis Chalmers 3655 cone crusher. Already second-hand when installed at the site in the mid-1990s, this machine was well over 30 years old and proving increasingly problematic and unreliable in this particularly arduous application. Consequently, lengthy breakdowns and expensive stripdowns were becoming increasingly frequent and having a detrimental effect on productivity and costs.
To take advantage of the existing in-line plant layout at the site, the replacement machine — a Sandvik 1511HD single-toggle jaw crusher — was installed just a few metres away from the old primary station, thereby simplifying the task of linking into the quarry’s existing in-line feeding/conveying system.
Site preparations for the new crusher began in March 2003 with excavation work and pre-split blasting of the face to create a suitable niche. The machine itself, together with its associated dump hopper, feeder unit and control cabin, was installed three months later following the construction of a robust support structure complete with stairways, platforms, catwalks and guardrails to allow safe access to all levels.
Thanks to careful planning and design, the engineering work required to link the new primary station to the quarry’s existing conveyor system was completed in just one week, during which normal daily production was maintained using stock from the main surge pile.
The primary station, which has a design capacity of 575 tonnes/h but has already delivered tonnages well in excess of this figure, is fed by means of an 80-tonne capacity dump hopper and a Roxon 15–60 (1.5m x 6.0m) vibrating horizontal grizzly feeder arrangement. The crusher has a generous feed opening measuring 1.5m x 1.1m in size and operates with a closed-side setting of 150mm, the resulting crushed product rejoining the –150mm underflow from the grizzly feeder.
The crusher is powered by a 200kW high-efficiency Brook Crompton squirrel-cage motor coupled to a Vector Microdrive inverter; this configuration was installed at Tarmac’s request in order to move away from the use of slip-ring motors, which are becoming increasingly harder to source in the larger kilowatt sizes.
To ensure that the crusher continues to provide trouble-free operation, the machine is serviced and maintained on a regular basis by local Sandvik engineers. They conduct a thorough inspection of the unit every three months and carry out a complete stripdown of the machine twice a year, during which state-of-the-art crack-detection techniques are used to check the condition of the jaw stock.
New mobile plant
The new primary installation at Cairneyhill has also benefited from the replacement of three ageing Aveling Barford dumptrucks with two 60-tonne payload Caterpillar 775E Quarry Trucks. Equipped as standard with durable Hardox steel bodies and fitted with Michelin X-Quarry tyres, the increased payload capacity of these vehicles means that the quarry’s haul operation can be carried out with one less truck.
The dumptrucks are loaded at the face by another new machine, a 90-tonne Cat 5090B faceshovel. This particular mobile plant combination was sized and matched specifically to cater for Cairneyhill’s maximum anticipated haul run of 800m. Replacing an earlier Cat 5080 model, the new faceshovel is equipped with a 5.7m3 capacity bucket and loads each dumptruck in six passes in 2min 35s.
In accordance with Tarmac uncompromising policy on health and safety, the new loading and hauling fleet is equipped with a wide range of safety features including reversing camera/radar systems as well as inclined stairways, extended catwalks and additional guardrails where appropriate.
All three machines are maintained under the terms of a routine service contract through Cairneyhill’s local Finning service centre in Blantyre. A dedicated engineer with sole responsibility for the quarry visits the site on a weekly basis as part of a planned maintenance regime to guard against any unexpected downtime.
Tertiary and quaternary modifications
The recent modifications to the tertiary and quaternary crushing stages at Cairneyhill have also been successful in eliminating earlier production bottlenecks, resulting in an increased output of better-shaped final products.
To achieve this, the quarry’s existing Allis Chalmers 836 tertiary crusher has been replaced with an inverter-driven Nordberg GP300 cone crusher, which had previously been used at the company’s Furnace Quarry, near Inveraray, while one of the quarry’s two existing Nordberg 1211 quaternary cone crushers has been replaced with a new Sandvik H4800 Hydrocone unit capable of operating with greater efficiency at the required closed-side setting of 12mm.
The net result of these modifications is an improved level of comminution at the secondary and tertiary stages together with more effective product shaping by the two quaternary crushers. This is reflected in the amount of +14mm material being recirculated from the final product bins to the quaternaries for recrushing, which has reduced significantly from around 100 tonnes/h to approximately 40 tonnes/h.
Coating plant
The final element of the recent investment programme involved the replacement of two ageing Dawson Fawcett coating plants of mid-1970s vintage with a brand new Benninghoven TBA320 high-level installation — Tarmac’s first ever coating plant from the German manufacturer.
Fed by conveyor from the quarry’s existing cold-feed arrangement and retaining the original bitumen storage and delivery system, the new, fully enclosed plant has a design capacity of 280 tonnes/h coupled with 200 tonnes of mixed-material storage, making it almost twice as productive as the combined output of the two previous plants and infinitely more flexible in its operation. Designed to produce around 150,000 tonnes of asphalt a year, the new facility has also been instrumental in the recent growth in ‘grocery’ trade at Cairneyhill.
Standing 30m in height, the plant is equipped with a 4-tonne mixer and features an integral granulate system for SMA production, a RAP system for anticipated future use and full stairway access throughout. With regards to energy efficiency, the main extraction fan is powered by a 200kW motor with variable-speed drive, while the other large electric motors within the plant are all high-efficiency models. The plant is fully computer controlled from a workstation in the weighbridge office and features a modem link to Benninghoven in Germany.
Acknowledgement
The editor wishes to thank Tarmac Northern Ltd for permission to visit the site and, in particular, David Chalmers, area engineer, Jack Marshall, area business manager, Gary Jones, quarry manager, and Michael Butler, assistant quarry manager, for their help in the preparation of this article.