Ancient And Modern
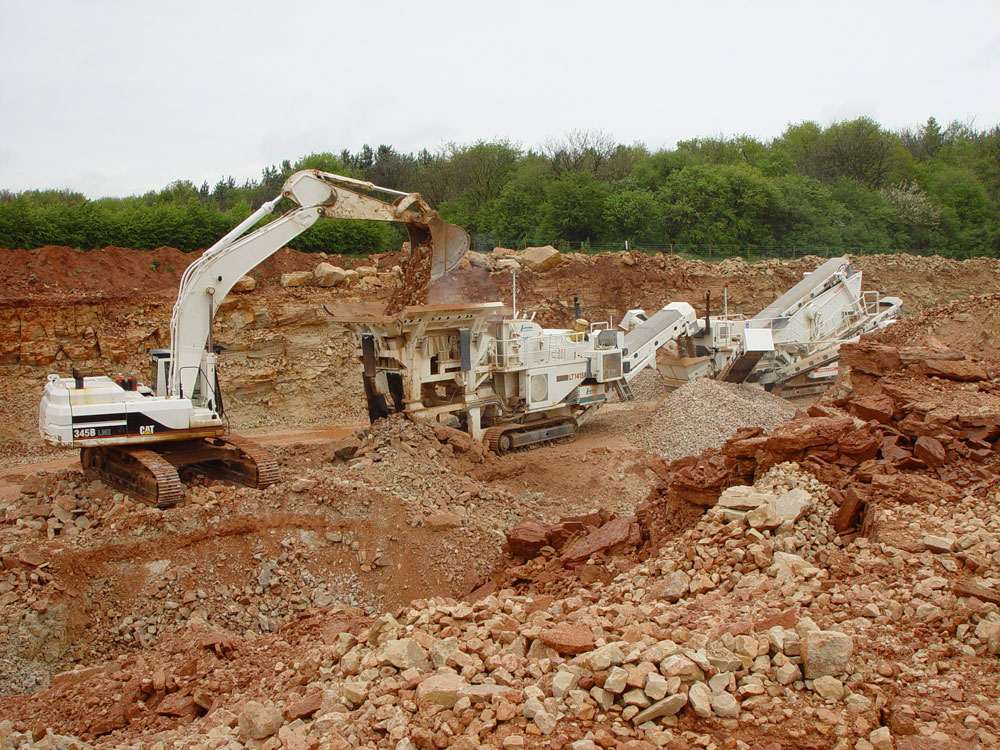
Lafarge Aggregates’ Nether Langwith Quarry comes on stream
Environmental considerations were to the fore when Lafarge Aggregates received planning permission to develop a new limestone quarry on greenfield land at Nether Langwith, near Mansfield. Identified as a potential mineral site in 1995, the reserves of Magnesian limestone at Nether Langwith underlie a tract of productive farmland that nestles alongside and area of ancient woodland – a remnant of Sherwood Forest which once covered a great swathe of this part of north Nottinghamshire.
However, with the county’s Minerals Plan in urgent need of a new source of hard rock, permission to work the 60-acre site was granted in March 2000 but with strict conditions attached, including precise control over the removal and storage of different soil types, a limit on the number of delivery trucks leaving the site, and over 30 separate discharge consents.
Work on the site was started in June 2001 by Universal Construction Services of Lincoln, with WA Fairhurst acting as consulting engineers. The work entailed upgrading 500m of public highway to improve access to the A632, constructing an 800m long by 6m wide quarry access road through the woods, and installing an underground fuel interceptor, weighbridge, site office and secure site-facilities compound.
During construction, which was completed last October, over 5,000 tonnes of asphalt were supplied by Lafarge Aggregates’ Renishaw Works, near Sheffield, while some 15,500 tonnes of Type 1 and crusher runs came from nearby Whitwell and Harrycroft quarries. Full production at Nether Langwith itself began in the last week of November 2001.
In tandem with site construction, the soil and overburden works for phase one of the quarry were carried out by Powerplant Excavations during the summer, under the watchful eyes of Nottinghamshire County Council and English Nature. This 12-week operation was complicated by the need to translocate the woodland soils and quarantine three other individual soil classifications. The woodland soil is being stored in bunds for the entire working life of the site and will then be replaced, while the other soils will be similarly stored, but relocation will begin after five or six years, to allow progressive restoration back to agriculture.
The consented reserves will be worked in seven phases over a period of 16 years. The quarry is being run in conjunction with Lafarge Aggregates’ existing Harrycroft Quarry, a dolomitic limestone operation located some 10 miles north of Nether Langwith.
The two sites share a mobile processing plant which is transported between the sites as production and sales requirements dictate. The plant comprises a 60-tonne Lokotrak LT1415 primary impactor and a 28-tonne ST620 tracked screening unit, both purchased from Metso Minerals last summer.
Although Lokotrak units are now a familiar sight in many UK quarries, the new 134kW Cat diesel engine-powered ST620 is believed to the first of this particular model to be sold in the UK. It features PLC logic control and Metso’s new hydraulically driven DS303 high-performance triple-deck screen; this provides a screening area of 11m2 per deck and achieves a high-capacity, accurately sized throughput by means of a steeper inclination angle at the loading end followed by a shallower screen angle at the discharge end. Discharge conveyors for up to four separate product sizes are provided.
The limestone deposit at Nether Langwith extends to a depth of 28m, however, under the terms of the planning consent, extraction is only permitted to a depth of 11m to avoid interference with the water table. Shotfirers from Whitwell Quarry carry out routine blasting every three weeks to produce a rock pile of around 40,000 tonnes. The mobile plant team works on this for three or four weeks at a time, building up product stockpiles at the site, before the equipment is transported to Harrycroft.
The LT1415 is loaded from the face by a Cat 345B backhoe excavator and feeds crushed product directly to the ST620 mobile screening unit. This produces around 350 tonnes/h of Type 1, the primary product at Nether Langwith, but has the capacity to achieve throughputs of up to 600 tonnes/h if necessary. In addition to Type 1, the site also produces 3–6in crusher run. Similar products are produced at Harrycroft, but here Type 1 is subordinate to crusher-run production. Whitwell Quarry, which focuses on the supply of single sizes, also forms part of this north Nottinghamshire limestone cluster.
Stocking and load-out duties at Nether Langwith are performed by two Cat wheel loaders, a 972G and 980G, but for around 30 weeks a year (when the crushing and screening plant is at Harrycroft) the site effectively functions as a depot, manned by just one loader operator and a weighbridge clerk. Operations on site are permitted from 7.00am to 7.00pm, Monday to Friday, and from 7.00am to 1.00pm on Saturdays (sales only), however in practice production tend to shut down at 5.00pm weekdays. When the mobile plant is on site, the target is to crush and screen material for 81/2h a day, allowing an hour or two for maintenance.
Despite its rural location, the site is supplied with mains electricity and mains potable water, however water for dust-suppression and other non-domestic uses is provided by an on-site borehole.
The site serves markets in and around the Mansfield–Newark–Worksop area of north Nottinghamshire, with deliveries generally being effected by the company’s owner-driver vehicle fleet based at Whitwell Quarry. All wagons entering and leaving the site are weighed in and out on a 50-tonne Avery Berkel concrete weighbridge which features maintenance-friendly side-access load-cells and is mounted over a generously proportioned drainage sump. Trucks follow a clearly signposted one-way circuit around the well-maintained site and are requested to cover their loads at the sheeting bay before leaving. Under the site’s planning conditions, the level of traffic travelling to and from the quarry is closely monitored, and there is a requirement for all lorry movements to be logged and reported to the local authority every six months.
Lying amid ancient woodlands, Nether Langwith is an excellent example of how a modern quarrying operation –– developed in accordance with the latest environmental controls –– can exist in harmony with the natural environment. Indeed for most members of the public, the only indication that the site even exists is the Lafarge sign that stands at quarry’s attractive woodland entrance.
Acknowledgement
The editor wishes to thank Lafarge Aggregates for permission to visit the site and, in particular, Miles Dobson, cluster production manager, for his help in preparing this article.