Lightweight Advantage
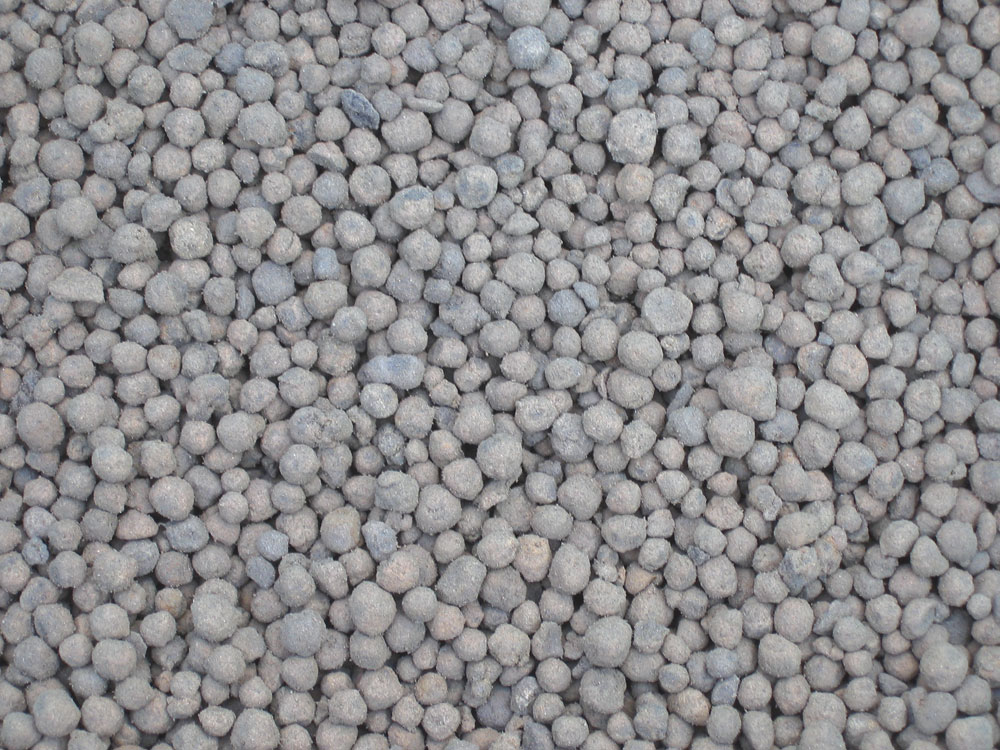
As the construction industry looks to the new financial year with hopes of economic revival, it is important that recovery is sustainable. Gareth Moores, executive chairman of Lytag Ltd, explains how secondary aggregates can help meet the needs of construction projects against this backdrop
The Mineral Products Association’s latest trend report highlighted the impact of the recession on the aggregate industry: the cumulative effect of 2008 and 2009 has seen aggregate and cement sales fall by 35%. With sustained public investment in construction at the levels witnessed in 2009 looking doubtful, the industry must be careful that the ‘green’ agenda does not slip. This is not only because of the importance of lowering the industry’s environmental impact and complying with legislative requirements, but also because a sustainable approach will be key as the industry works to leave recession behind.
Sustainability and efficiency
Secondary aggregate is one ‘green’ material that can provide a project with the efficiencies and performance benefits that are essential for construction businesses now and in the coming years. Providing a viable alternative to quarried aggregate, using secondary aggregate reduces demand on primary materials and diverts waste from landfill. Crucially, its use also provides similar, or often improved, performance credentials and can lead to considerable project efficiencies.
Lightweight secondary aggregate
It is this marriage of sustainability and efficiency that makes secondary aggregate particularly attractive in a variety of construction applications, including structural and precast concrete, screeds, fill and use as a drainage medium. For example, when used in precast concrete – from smaller concrete products such as lintels, posts and street furniture, to large-scale units for bridges and stadia – Lytag lightweight aggregate (LWA) provides a weight saving of approximately 25% over normal-weight precast concrete.
Structural concrete manufactured using this material is also 25% lighter than traditional concrete and with the same structural integrity. This means that spaces can be designed with larger structures and greater spans, and a reduced number and width of columns, ultimately providing building owners and occupiers with maximized usable floor space and increased commercial value. As a secondary material manufactured by sintering pulverised fuel ash (the by-product of coal-fired power stations), it can also improve a project’s ‘green’ credentials.
Advantages and advances
Using lightweight secondary aggregate can deliver real advantages in terms of production techniques, reduced fixings, logistics and crane requirements, and by combining both coarse and fine LWA, benefits be further increased. Lytag LWA, for example, can be used to make structural lightweight concrete with oven-dry densities in the order of 1,750kg/m3, and strengths exceeding 70N/mm2 achievable using lightweight coarse aggregate and natural sand.
Advances in admixture technology and tailored aggregate gradings have resulted in the availability of a wider range of concretes made using secondary aggregate, and a greater selection for architects, engineers and contractors. Pumpable and self-compacting concrete made with secondary LWA, both coarse and fine, can be produced with oven-dry densities in the region of 1,450kg/m3 and strengths in excess of 40N/mm2. As a result of such developments, even greater weight reductions of around 35% can be achieved by combining coarse and fine LWA. This lighter-weight concrete offers opportunities for efficient working and innovative designs that would not be feasible with traditional concrete.
Looking to the future
Those looking to win work must combine this design flexibility with growing client requirements for sustainability. Reducing the environmental impact of construction has risen high up the industry’s priority list over recent years, and it is now widely recognized that sustainable working is central to the industry’s recovery.
Government legislation and targets, such as halving the amount of construction waste sent to landfill by 2012 (a goal set out in the 2008 Strategy for Sustainable Construction), are driving the industry towards a ‘greener’ future and there is a role for everyone to play, from client and engineer to contractor and product supplier. Using secondary aggregate can help a project towards meeting such targets while providing important performance and efficiency benefits – a ‘quick win’ opportunity to deliver against agendas that are likely to top the industry’s priority lists for some time to come.
For further information on Lytag LWA and its applications, visit: www.lytag.net
Case study 1: 7-10 Old Bailey, London
The seven-storey office development built adjacent to the Old Bailey High Court in the City of London and constructed within the existing structure’s footprint has been designed to remain sympathetic to the site’s historic surroundings while also exemplifying the best of modern design. Reducing the impact on the remaining archaeology was a key consideration, as was the stability of the ground.
Reducing the dead weight of the 7,904m2 building helped the project team to overcome both of these challenges. Engineering consultants Pell Frischmann were able to greatly reduce the structure’s weight by using Lytag LWA in the concrete for the floors of the building. The lighter-weight concrete slabs on metal decking were combined with a lightweight steel frame structure, significantly reducing both the impact on the remaining archaeology and the pressure on the soil. Using LWA allowed Pell Frischmann to design spans of 9m with 203 UC sections, which allowed for greater services flexibility without increasing the frame costs.
Sustainability was a key element in this development, with design and construction best practice implemented wherever possible. The building was designed with an efficient heating and lighting system and has a number of sustainable features, such as rain water harvesting and solar hot water, and the use of secondary aggregate contributed to the project’s excellent sustainability credentials.
Case study 2: St Pancras Station, London
In 1996 St Pancras was nominated to become the new UK terminal for Eurostar and a five-year redevelopment was undertaken to modernize the station. The redevelopment has substantially added to the weight of the structure – and because much of the building is over tunnelled, void or unstable ground, the challenge for the main contractor (joint venture group CORBER) was to create a station that delivered the architect’s design without needing to compromise because of the additional load bearing.
CORBER used concrete made with Lytag LWA in part of the refurbishment and in the underground station, and a Lytag LWA no-fines screed, topped with paving, to bring up levels on the existing platforms to accommodate the new Eurostar trains.
Using the material substantially reduced the weight of the concrete and screed, while maintaining the structural integrity and the performance of the materials, thereby allowing CORBER to achieve the redevelopment of St Pancras station without having to undertake extensive and costly strengthening work to the existing structure or the unstable ground.