GR Plant show their mettle in steel slag contract
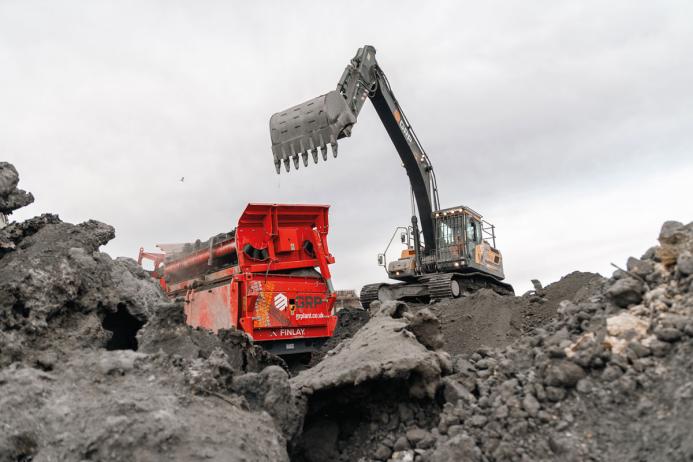
First published in the April 2025 issue of Quarry Management
Molson Group support key to success in challenging Celsa steelworks application
GR Plant have built themselves an enviable reputation across the UK for delivering a variety of crushing and screening services, largely for the construction and demolition industries. Working on Hinkley Point C for nearly a decade, and Cardiff steelworks for even longer, GR Plant specialize in recycling and processing materials for new purposes. Arising from owner Gareth Rees’s passion for cycling, the company has also successfully delivered numerous high-profile mountain bike trails, including Lee Valley Velopark at the Queen Elizabeth Olympic Park in London. Since starting out in 1989 with a Ford H45 excavator at the age of 22, Mr Rees has grown the business into a multi-faceted operation with a fleet of 50 machines and a staff of 20, and last year the company celebrated its 35th anniversary.
One of GR Plant’s largest contracts is at the Celsa steelworks in Cardiff, South Wales, where the company undertakes the recycling of steel production waste materials, recovering any metals before resizing the slag for reuse in construction projects. The expansion of the company to undertake this work has involved massive investment in purchasing the right kit to do the job – something GR Plant have undertaken hand-in-hand with Avonmouth-based Molson Group.
Sitting on the banks of the river Taff, the Celsa steelworks is one of the UK’s largest producers of steel reinforcement products, delivering more than 1.2 million tonnes of material to the UK and Irish markets annually. The enormous electric arc furnace at the state-of-the-art plant produces thousands of tonnes of steel on a daily basis as well as creating huge quantities of arc furnace and pit waste. This waste, which comprises a mixture of lime, steel, and other aggregates from the steel-making process, has traditionally been sent to landfill. Like any typical steel-making process, various elements are mixed according to the precise requirements of the steel and once melted, the remaining slag is taken from the mill at 800°C and transferred to a tip where it is turned on a regular basis until it has cooled down to a more manageable 80°C.
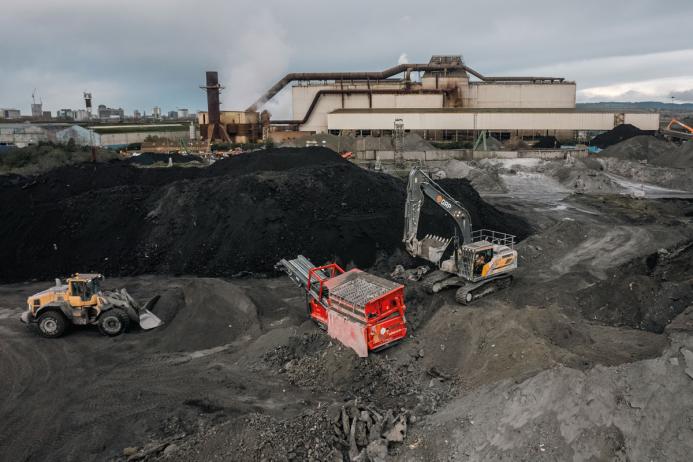
In line with the steel company’s desire to explore sustainable options, recycling alternatives have been explored and instigated. Working with Swansea-based GR Plant and other providers, Celsa have built a system that can take the waste material from the production process and recycle it almost entirely.
‘The job calls for a range of machinery that is not only capable of dealing with the excessive temperatures in the material, but also with its abrasive qualities,’ explained GR Plant’s contracts manager, Rob Jones. ‘When we won the contract, we quickly realized this and needed to ensure that future purchases were of the quality and durability we needed to ensure we could produce both the right grade and the right quantities of finished material that our client required.’
With more than 25,000 tonnes of furnace residue being handled annually, GR Plant wanted the backing of a machinery provider who would not only supply them with a range of equipment designed to do the job but would also ensure their targets are achievable by making sure the kit keeps running.
‘We sat down with the team from Molson in the early days to discuss what we were being asked to do on site,’ explained Mr Jones. ‘We quickly found the experience of the team at Avonmouth to be extremely helpful in developing the machinery to handle the highly abrasive material. We wanted assurances that the kit that they were supplying would do the job and manage the process, and whilst some of the early trials with screens and crushers proved challenging, not once did Molson back away from us.’
GR Plant have two separate parts of the steel making and recycling process to handle and have put a fleet of 17m reach Sennebogen 830E material handlers to work sorting and loading incoming scrap metals ready for the electric arc furnaces. Whilst this is a standard task for these 36-tonne material handlers, there is a need for the machines to work around the clock as the steel-making process, once started, only stops for maintenance and breakdowns. ‘The Sennebogens have been reliable machines for us,’ said Mr Jones. ‘They have done exactly what we expected them to do, and whenever there has been an issue, Molson have always been on hand to respond quickly.’
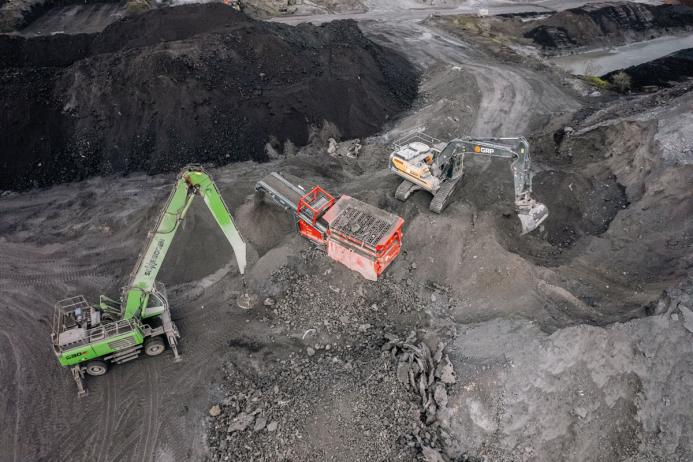
Moving on to the back end of the recycling operation, once the slag has cooled sufficiently it is stockpiled ready for pre-screening prior to the final crushing and screening operation. A pair of Hyundai HL980 wheel loaders play a key role in the management of the material both before and after processing. Like the Sennebogen material handlers, the wheel loaders have a key role to play in keeping the back-end operations running smoothly. Moving the material from process to process could be undertaken using an excavator and truck, but with the material and processing points located some distance apart, a wheel loader load-and-carry system was regarded as the most efficient process.
The cooled slag is first passed over a heavily modified Finlay 595 screen. Modifications include a reinforced and lined hopper, upgraded rip-stop belts, additional magnets, and protective plates to the external sides of the hopper to prevent potential damage to the machine. These modifications have been undertaken as the slag contains large quantities of metals left over from the steel-making process. A 125mm hexagonal punch plate has been installed over the grizzly bars on the hopper to divert as much steel as possible from entering the screen deck itself. Metal coming off the magnet and grizzly falls to the floor where one of the site’s five Sennebogen material handlers sifts through it with a magnet before depositing it to one side. This material is transferred to the other Sennebogens for shearing before being set aside ready to re-enter the steel-making process.
The screened material coming from the Finlay 595 is moved to the second stage of the process where it is crushed and screened. Site foreman Kevin Norton said: ‘Over the years, we have used a variety of crushing and screening equipment to get the right size and cleanliness of material. This train we are running now does exactly what we want and can produce a steady quantity of material, so long as what we feed in isn’t too wet.’
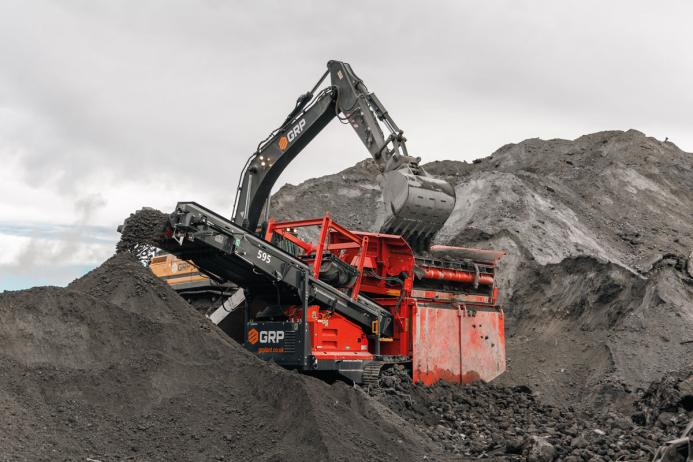
The processing plant employed by Mr Norton’s team consists of a Hyundai HX300AL which loads a Finlay 883 scalping screen that produces three products. Oversized material from the screen is fed back into a Finlay J1170 jaw crusher, which reduces it in size before it goes back to the screen. Using this process, GR Plant can produce a variety of sized products to the clients specification. In addition to the 883 scalping screen, GR Plant use two Terex Ecotec TTS 620T trommels, especially during the winter months when material becomes sticky. The trommel screens are also efficient at extracting excessive dust when clean materials are required.
Whilst GR Plant are not contracted to produce a minimum tonnage of material per week, Mr Norton and his team have to ensure that the incoming material is handled as quickly as possible. ‘We need a reliable fleet of machines and Molson have been able to supply us with just that,’ he said. ‘On the rare occasions when we have had an issue, they’ve responded very quickly to our call. The kit here takes a fair beating but has stood up to the test, although we do tend to change some of the machines sooner than we would normally, due to the work we do.’
Rob Jones is also very pleased with the service and back up they get from Molson. ‘We do have issues occasionally, but overall, they are a great company to deal with. We ask them to supply [machines] to our specification and they do just that. They look after us from a service point of view even though they know the pain we put the machines through.’
Working closely with the Molson team to develop an efficient material handling and recycling process has worked well for the GR Plant team. ‘Having Molson as a single-source solution to all of our material handling and recycling applications on site has made our Celsa operation run efficiently and smoothly,’ concluded Mr Jones. ‘Whatever our issues are, we know it’s a single call or email to get it sorted. We also know that when we are looking to upgrade a piece of kit, Molson know what our requirements are. Having their support behind us has allowed us to develop ourselves as a company and explore projects which at one time would not have been on our radar.’
Subscribe to Quarry Management, the monthly journal for the mineral products industry, to read articles before they appear on Agg-Net.com