Why Manufactured Sand?
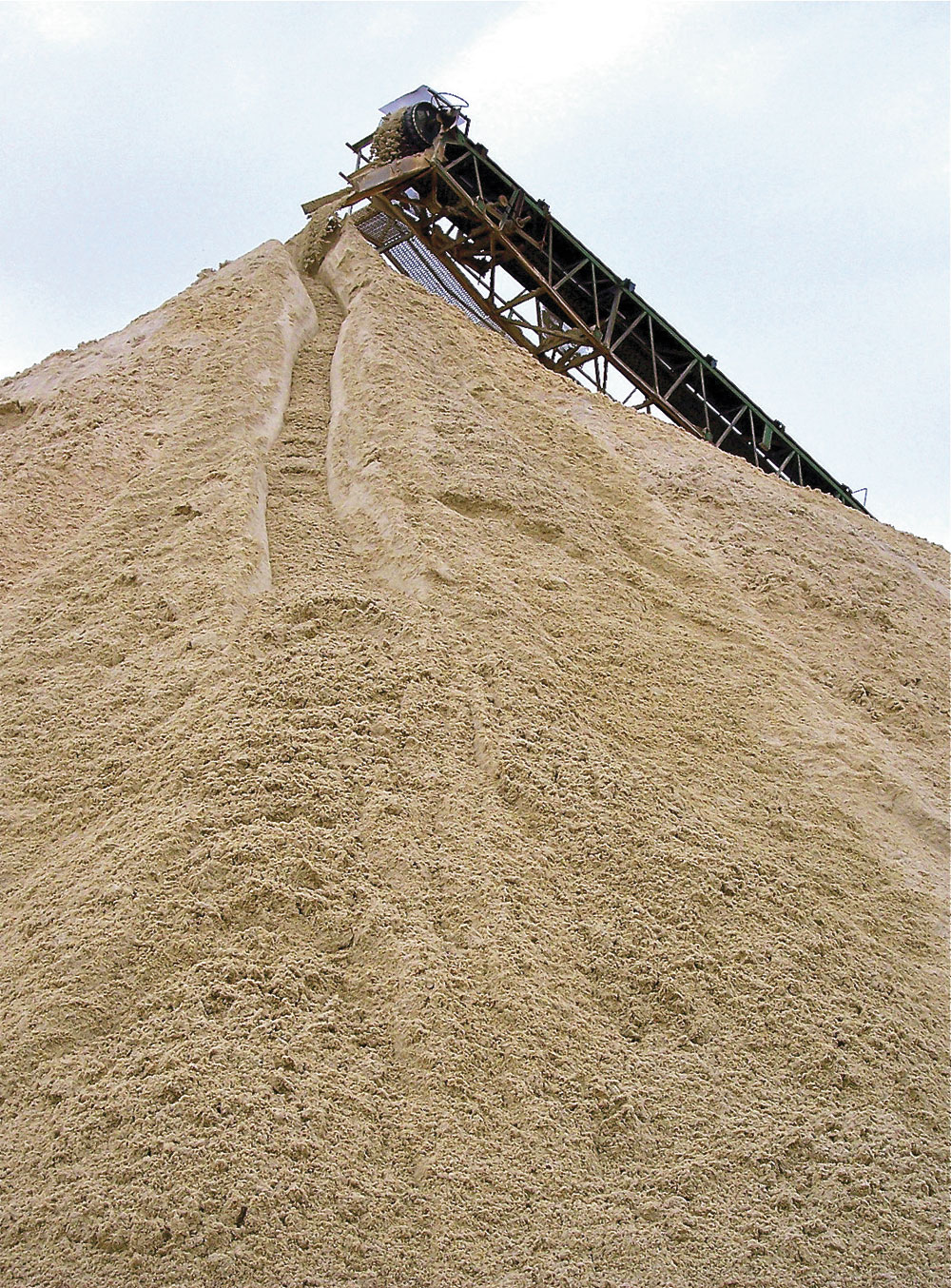
Globally, natural sand and gravel extraction is becoming less of an option. New pit location opportunities are fewer, further from the marketplace and harder to secure. In the past, natural sand and gravel extraction has been the backbone of the aggregate industry; this is increasingly less the case. Operators now wish to produce high-quality manufactured sand. Why? There are two main drivers, as David Morrow of Metso Minerals explains
First, there is a lack of natural sand reserves. Urban expansion, local legislation and environmental constraints have made the extraction of natural sand and gravel an expensive activity. Application processes for greenfield sand and gravel extraction are often long and expensive affairs with a high chance of site applications being rejected.
The increasing difficulty in extraction has had a negative effect on the bottom line for many producers. Concrete plants require a consistent, quality sand to optimize their production and minimize their cement usage. In many regions of the world, the extraction of sand and gravel is heavily taxed or banned completely to try to preserve remaining deposits. The industry must find alternatives to meet the growing demand for fine aggregates.
Urban expansion and depleted resources have increased the distance between the point of extraction and the point of use. Road congestion has increased the travel time from pit to batching plant for many operators. This, coupled with a decline in the number of pits, has increased prices for the end consumer.
The second driver is purely economic. A growing number of quarry operators have found that processed, high-quality manufactured sand can improve their bottom line and significantly reduce the percentage of waste and low-value by-products. Customer requirements for production less than 20mm, especially for 7–10mm, mean that significant amounts of 0–7mm are produced as a by-product.
By utilizing the correct processing equipment, low-value crusher dust can be processed into a high-value premium product. Concrete, mortar and asphalt sand production is possible depending on the material characteristics and regional regulations. The benefits of this process are twofold: the producer secures new product offerings and reduces low-value product; and the customer has access to a secure supply of sand with a stable grading curve.
End-product performance
Production of high-quality manufactured sand requires specialist knowledge in fine crushing and separation technology to achieve end-product performance.
Processing is the key to producing a marketable product. The production of quality manufactured sand, along with its process and process control, is integral to customer success.
The two factors that are of the greatest concern to the end users of manufactured sand are compliance with local regulations and the consistency of the product.
Compliance with manufactured sand gradation is required not only at the bottom of the curve, but throughout the product envelope.
Product consistency allows a more predictable mix to be produced than is achievable with natural sand due to normal natural variations in dug sand gradation. This means that end-users of manufactured sand do not have to allow a safety factor to mitigate for natural gradation variations and can achieve binder savings.
Sand solution equipment
Operators generally have exacting requirements. Specifications vary from region to region and successful implementation of manufactured sand differs from operator to operator. Solutions should be modelled on best practices to meet market requirements.
Metso provide complete crushing and separation solutions for greenfield sites or solutions that can be incorporated into existing plants to achieve well-graded, quality manufactured sand.
Cone crushing technology gives the producers high energy efficiency and capacity, good product gradation, a high reduction ratio and low sensitivity to rock hardness.
Cavity design for cone crushers should be optimized to ensure that crushing occurs along the full length of the crushing zone between the liners. This causes inter-particle crushing to occur, leading to the highest possible generation of the required fines and cubically shaped products.
Advances in high-speed cones with high clamping forces offer the opportunity to produce well-graded and shaped –20mm product, including well-graded manufactured sand.
Vertical-shaft impact (VSI) crushing technology has the advantage of being able to process fine, unscalped, heterogeneous and irregular feeds. Unlike cones, VSI shaping is not influenced by the closed-side setting (CSS), and shaping occurs throughout the product curve.
The sand produced from rock-on-rock crushing is proven to have sound performance in concrete and mortar products. Such sand is well known for its cubical shape and consistent gradation. The gradation and quality of the product from the VSI does not tail-off with increased wear on parts. This leads to the highest possible quality of performance in concrete and mortar mixes, leading to reduced production costs.
Air-classification technology
A growing trend is the use of dry classification solutions to produce manufactured sand. The dry separation process separates fine and coarse particles. This allows a reduced percentage of superfines in manufactured sand, thereby meeting specifications and achieving quality products.
Metso offer aggregate producers two classifier options. The gravitational inertial classifier is typically fed with 0–4mm or less and makes separations between 300 microns (50 mesh) and 63 microns (230 mesh). These units are ideal for use in the manufacturing of concrete and asphalt sands that typically require a reduction in the amount of 63 micron material present. Such units are designed with an internal recirculating function that allows the efficiency of the separation to be adjusted depending on the desired grading curve.
When finer separations are required, the centrifugal classifier can make separations of between 100 microns (140 mesh) and 20 microns (625 mesh). This makes these units suitable for the production of very fine products, such as lime, fly ash and fertilizers.
Metso’s air-classifier range provides versatile, economic technology that can be combined with a range of different crushing and screening equipment to produce a tailored plant. It allows for the production of dry products so there are no dewatering or drying costs. Process water is not required, which significantly reduces quarries’ water demands, settling pond requirements and makes production in arid regions viable.
No moving parts and ceramic linings mean exceptionally low maintenance and wear parts costs, even with the most abrasive of rock types. Highly efficient separation, even at very fine particle sizes, produces quality product and limits the amount of product in waste.
For further information contact David Morrow on tel: +1 717 849 7161; or email: david.morrow@metso.com