Understanding Comminution: Compression versus impact crushing
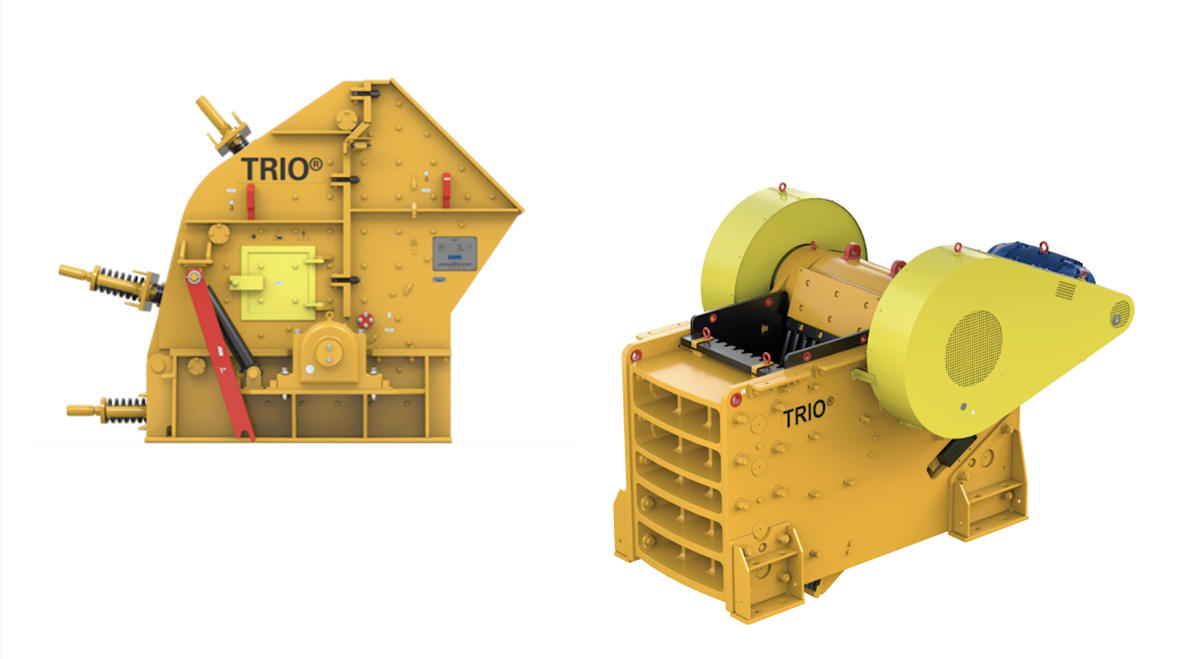
First published in the September 2020 issue of Quarry Management
By Dr.-Ing. Ekkhart Matthies, global applications director and global product manager, crushers, Weir Minerals
Today, quarry operators crush and process more variations of rock in larger quantities than ever before, but without taking the time to carefully analyse and consider the circuit’s throughput requirements, operators risk excessive consumption of power and wear parts/materials, as well as possible equipment failure. The most important factor when designing a crushing circuit is how to apply the two primary methods of crushing aggregate – compression and impact.
Before analysing the differences and benefits of each method, it is important to understand what is being processed and the effects the rock product has on the equipment. There are three main ‘families’ of rock – igneous, sedimentary and metamorphic. Formed under different conditions and containing different minerals and ingredients, not only does each family react differently when crushed, but each contains a plethora of different sub-types of rock.
A common misconception is that ‘a rock is a rock’, but no matter how close one plant may be to another, the rock being sourced can have quite different characteristics. For example, two granite crushing circuits can be (from the flowsheet perspective) set up very differently. Weir Minerals recently worked with two customers planning a crushing plant for the same type of rock less than 10 miles away from one another, but local differences in the material meant they faced contrasting crushing and flowsheet challenges.
This variability means that testing is paramount. Before any investment or planning takes place, it is vital to understand how hard, brittle or abrasive the material is that is to be crushed. The three most important characteristics of a rock that need to be obtained by testing are:
- Wi (work index) – this is essentially how hard the product is and how much energy must be applied to reduce its size
- Si (silica content) – the more silica a rock contains, the more abrasive it will be
- The moisture and clay content of the processed rock.
These three elements are a good starting point for designing a successful process and must be analysed before selecting equipment for crushing. The more information that can be obtained the better.
Impact crushing
Impact crushing is essentially like opening a walnut with a hammer – when the hammer meets the shell, the nut instantly cracks into a number of smaller pieces. Mining equipment creates impacts by using a rotor to violently hit and throw rock against the walls of a crushing chamber.
As a basic rule, impact crushing is suitable for rocks with a low work index (<12) as well as low silica (<20%) and moisture levels (<5%). Rocks with these characteristics are soft and non-abrasive, and easily broken within the crushing chamber, keeping wear rates at a minimum, and producing high reduction ratios with a better-shaped end product.
Compared with compression crushing, impact crushing will create more fines within the circuit, which will cause greater wear if processing abrasive material. This is why rocks with lower silica content are more suited to reduction by impact crushers.
When compared with cone crushers, impact crushers often have a lower capital cost, but can potentially incur high operating costs if the application has not been evaluated properly and has high abrasive qualities.
Weir Minerals offer two types of impact crusher suitable for primary and secondary crushing: horizontal-shaft impact (HSI) crushers and vertical-shaft impact (VSI) crushers.
HSI crushers can achieve very high reduction ratios. They work by accelerating the rock as it is fed from the top, from where it is caught by the upward facing rotor, accelerated inside the rotor and then released against the crushing chamber.
VSI crushers are very flexible and their configuration can be changed to suit the application. Machines can be run in rock-on-rock, rock-on-steel and steel-on-steel configurations to suit different applications – and this can be altered throughout the machine’s lifespan to accommodate changing needs.
Compression crushing
The term ‘gentle crushing’ may sound somewhat contradictory, but compared with the raw power of impact crushing, compression crushing could be considered a much gentler method – which makes it more favourable for harder, abrasive rocks.
If impact crushing is opening a walnut with a hammer, compression crushing is the nutcracker method. A steady compression force is applied by closing the product between the mantle (or jaw) dies and the crushing chamber’s wall.
Compression crushers such as cones and jaw crushers normally have lower reduction ratios than HSI or VSI crushers, but do offer much greater control over the output – as they allow users to define their desired settings to the millimetre. Weir Minerals’ range of Trio jaw and cone crushers allow users to change these settings at the push of the button.
Compression crushers can easily process hard and abrasive material and, due to their crushing method, expel fewer fines while doing so, thereby increasing the efficiency of the circuit. This is because cone crushers utilize interparticle crushing, where rocks are also compressed against each other in addition to the crushing chamber and mantle, thus reducing the need for each rock to make contact with the crusher’s wear parts. This ‘choke fed’ aspect is an important operational feature of cone crushers.
Weir Minerals offer two types of compression crusher: Trio jaw crushers and Trio cone crushers. Jaw crushers are generally considered a primary or first-stage crusher. The maximum feed size can be as large as 80–85% of the crusher’s gape or depth, while reduction ratios range from 2–3 times.
Cone crushers are typically used in the secondary or tertiary stage after a jaw crusher has begun the reduction process earlier in the circuit. They process smaller-sized materials and operate under choke-fed conditions, where the feed chamber is consistently full. Weir Minerals offer two types – the TC series and the TP series – for use in different applications.
Ensuring success
While the process of testing and evaluating the rock type adds both time and another layer of complexity to the process, it is vital to the success of a circuit. Whether a compression crusher or an impact crusher is needed, each type has its own benefits and is designed to excel in different applications. The more information that is known about a rock’s material characteristics – the easier that choice will be and, in turn, the more optimized the process will be in terms of cost per tonne of product.
Crusher Type Comparison
Crusher Type | Industries | Application | Material Hardness | Material Abrasion | Elongated Material | Installation Cost vs Capacity | Maintenance Cost | Operating Cost |
Jaw | All | Primary | Medium to Hard | Medium to High | Average | Low | Low | Low |
Primary Impactor (HSI) | Quarry, Recycle | Primary | Soft to Medium | Low to Medium | Good | Very Low | High | High |
Cone | All | Secondary, Tertiary | Medium to Hard | Medium to High | Average | Low | Low | Low |
Vertical-Shaft Impactor (VSI) | All | Secondary, Tertiary, Quaternary | Soft to Hard | Low to High | Good | Very Low | High | High |
- Subscribe to Quarry Management, the monthly journal for the mineral products industry, to read articles before they appear on Agg-Net.com