The Simple Solution
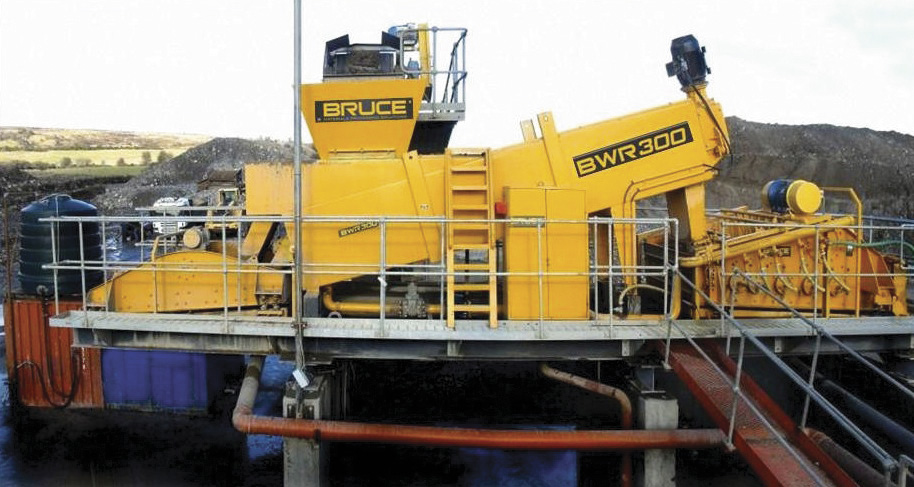
Bruce Materials Processing Solutions launch their BWR300 washing plant on home soil
Galway-based Martyn Sand & Gravel are long-established suppliers of washed stone aggregate to concrete paneling manufacturers in Ireland – customers who demand a clean, high-quality product. Brian Martyn, owner and director of the company, previously achieved this by running his quarry’s face gravel through a washing screen, to remove the sand, and then through a second screen to ensure it was of a clean enough standard to meet his customers exacting requirements.
When supplies of gravel at the company’s original pit had been exhausted, Martyn Sand & Gravel began extracting material from a second site where the gravel had a much higher sand content. It was at this stage that Mr Martyn decided to look at ways to make his plant more manageable and power efficient, yet with the ability to provide a cleaner product.
As Cookstown-based Bruce Materials Processing Solutions had previously supplied his company with bespoke feeding and screening plant, Mr Martyn invited them to have a look at the problem. After carrying out a sieve analysis and various other tests on the material, Bruce came up with a cost-effective solution – their new BWR300 washing plant, which has been operating successfully at various locations in the UK since its launch more than 12 months ago. Comprising a fully integrated coarse-material log-washer, double-deck washing screen and trash screen, the plant is designed to increase the proportion of reusable products that are produced, and is available as a mobile unit for ease of manoeuvrability.
In operation, raw material is loaded into the plant’s feed hopper and transferred by conveyor to the coarse-material log-washer. Any light debris flows back to the trash screen while the water is sent to the cyclone sand plant. The material remaining in the coarse-material washer is thoroughly scrubbed to loosen the mud and sand from the stone and is then fed over a double-deck, high-frequency, 10ft x 5ft washing screen, which splits it into +20mm and –20mm +5mm fractions. The –5mm passing this screen is also sent to the cyclone sand plant, where it is dewatered to provide a concrete sand and/or plastering sand specification.
‘I am extremely pleased with the BWR300 and have found that the plant delivers a much cleaner finished product with a lot less power consumption; my water usage has also dropped significantly, giving me a further benefit of a drier finished sand with less silt reclamation,’ commented Mr Martyn. ‘The plant is also a lot more compact and requires less maintenance than some other systems I have seen working.’
Bruce say the BWR300 is a highly compact and economical system which is easy to operate in confined areas and can be easily transported from site to site. The system is suitable for washing primary aggregates, sand and gravel, recycled and reclaimed aggregates, secondary aggregates, as well as foundry slag and metals.
For further information visit: www.bruce-eng.co.uk