The Move To Barmac Sand
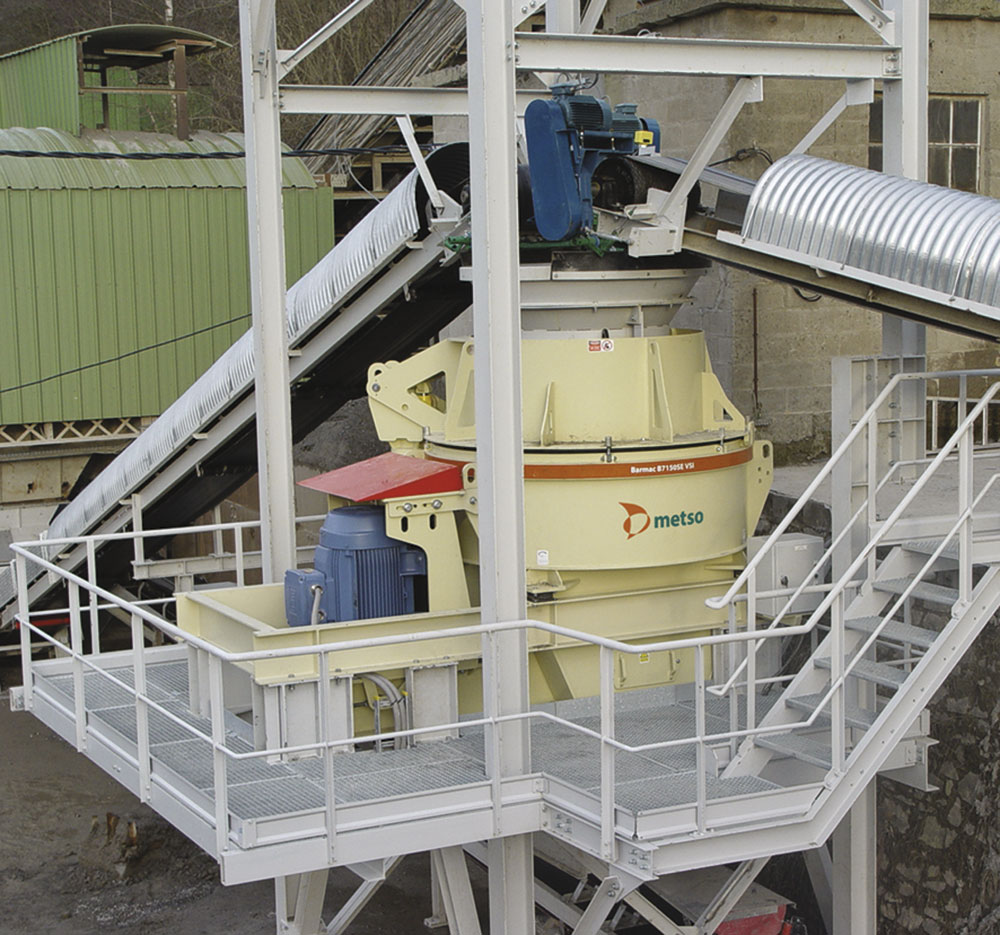
Since the inception of rock-on-rock crushing in the late 1960s it has been possible to produce manufactured sand that performs better than natural sand. This has led to the use of Barmac VSIs as the leading crusher for producing high-quality manufactured sand as well as coarse aggregates.
The overall crushing action in a Barmac B-Series VSI is more complex than many other crushers because several different crushing mechanisms are involved. The Barmac is, in essence, a high-energy centrifugal rock pump with several fracture mechanisms — impact, shatter, shear, attrition and abrasion — being used to achieve size reduction. Reduction results from the high-intensity inter-particle and particle-to-rock-bed collisions occurring within the crushing chamber and rotor.
This continual process replenishes the rock lining while at the same time maintaining a rock-on-rock chain reaction of crushing and grinding. The particles in the crushing chamber collide until they have lost sufficient energy to allow them to drop out of the particle cloud and leave the crushing chamber. The residence time in the crushing chamber is typically 5–20s.
The end product from the Barmac crushing action is a superior shaped and textured aggregate. The nature of the crushing action ensures that all the material will be of superior particle shape, resulting in no waste material.
PARTICLE SHAPE AND TEXTURE
Particle shape is perhaps the most important factor to consider when producing a high-quality concrete aggregate. Cubical-shaped aggregate, as produced in a Barmac, performs better than aggregate of a poorer shape. The advantages of using cubical-shaped aggregate in concrete are:
- improved workability in placing the mix with less time and effort required
- mixes are more pumpable
- concrete is easier to finish and gives a better surface with less time and effort required
- less cement is required per cubic metre of concrete for a given strength
- higher strength for a given cement content
- higher strength aggregate in the mix
- better mixing of ingredients, fewer voids, less bleeding and better consistency
- better shape leads to better packing of the particles, resulting in less voids and structurally sound in-situ fill materials.
The Barmac brings both a shaping and cleaning mechanism to the production of these types of coarse and fine aggregates. The crushing action breaks down soft material at a faster rate than the harder, tougher particles, resulting in a product that is free of the softer materials that would perform poorly when subjected to the loads and conditions involved.
Concrete producers worldwide are moving towards the use of crusher fines — traditionally a waste material — as manufactured-sand products. Extensive testing is showing that manufactured sand, when processed by a rock-on-rock crusher, can be used to make concrete with superior strength characteristics and at a lower cost than concrete made with natural sand.
HIGH MICROFINES
Traditionally, sand specifications have limited the use of microfine material because of the negative effects of its use. In naturally occurring sands this fine material generally contains mineral clays and/or organic material that will increase the water demand required to produce a workable concrete mix and reduce the strength of hardened concrete.
Microfine material that is created as part of the crushing process will, in elevated quantities, improve both the fresh and hardened properties of concrete. Current research and practice proves that microfines are beneficial to most properties of concrete. Sands with a high microfine content (>15%) have been used successfully to produce workable concrete. Because the particles act in a similar way to that of coarser particles there is no additional water demand.
CASE STUDIES
Taranaki — New Zealand
As part of their business, Freight & Bulk Transport (FBT) extract sand, gravel and rock from a quarry on the west coast of the North Island of New Zealand. The site has traditionally produced roadbase products for the local market but FBT wanted to increase the profitability of the quarry so they approached Metso Minerals to assist in diversifying the range of products produced.
The company wanted to make a range of value-added products, such as sealing-chip and concrete aggregates. It was recommended that FBT invest in a final-phase crusher to produce the right shape and gradation requirements for the desired products. A Barmac VSI was selected and to ensure the machine could produce a sand that would satisfy the demands of both the concrete plant they supply, along with local sealing-chip specifications, laboratory trials were performed using a B3000 test machine.
After consultation with both Metso Minerals and the concrete company, FBT purchased a Barmac B6100 VSI. The laboratory tests proved that, with the addition of a Barmac VSI, the quarry could consistently produce a high-quality sand that the concrete plant could use with confidence in their concrete mixes. In addition, the Barmac VSI also produces a sealing chip that easily exceeds the required shape specification.
The Barmac B6100 is set up in a closed-circuit post-screen arrangement, which ensures that all material passing into the crushing circuit achieves a superior final product shape.
Ian McCrae, quarry manager, said: ‘The Barmac B6100 has given FBT the opportunity to produce a high-quality sand for supply to our customers. Because of the advantage we now have over other quarries in the area we are looking at increasing plant production.’
The sand supplied to the concrete plant is a blend of excavated natural sand and Barmac-produced sand. Blending allows all the material processed in the crushing circuit to be sold at a premium and maintains desirable properties in the final concrete. The Barmac sand is not washed and up to 10–12% that passes the 0.075mm (20#) test sieve is included in the supplied concrete sand.
The previous sand supplied to the concrete plant was alluvial pit sand. Since the concrete plant has switched to sand from FBT the improvement to their concrete has been substantial. As proven by the laboratory tests, the elevated levels of –0.075mm material included in the blended sand have not adversely effected the performance of the sand. Instead it has assisted in increasing the compressive strength and the density of the concrete. The users of this concrete have been impressed with the properties and finish of the concrete.
The improved performance of the sand delivered to the concrete plant has given it a competitive advantage in the local market. The geological setting of this area of New Zealand makes the production of quality sand difficult, while the haulage of sand from outside the area is not economically viable. Therefore the concrete plant has gained a clear market advantage. Customers have also remarked favourably on the ‘finishability’ of the concrete.
The inclusion of a high-microfines Barmac sand has improved the compressive strength and density of all the concrete mixes that the plant produces.
Ian McCrae commented: ‘The assistance we have had from Metso has allowed us to produce high-quality sand and sealing chips. Metso not only provided technical advice on what is right for our crushing circuit, but have also worked with our customers to provide the best product, better than any other in the area. The results speak for themselves.’
Owing to the demand for the value-added products the quarry now produces, the crushing circuit requires expansion and FBT have contacted Metso Minerals to provide technical support for their expansion plans.
Belo Horizonte — Brazil
Transport and Commercial Ltd (TCL), located in Contagem in the metropolitan area of Belo Horizonte, Brazil, operate one of the oldest and most important quarries in the region. In the late 1990s they started to wash crushed fines produced in the quarry, transforming them into concrete sand by using vibratory screens, screw washers, hydrocyclones and dewatering screens.
Manufactured sand was already accepted in the market, especially by concrete producers. The main favourable characteristic of the manufactured sand is its consistent quality, both in terms of gradation and lack of contaminants. The manufactured sand also meets concrete producers’ requirements in guaranteeing an alternative source of this important material, in both the medium and long term. In view of the increased restrictions in natural sand production this factor is considered extremely important.
With the success of this operation TCL decided to invest in a plant dedicated to the production of manufactured sand, not only to satisfy the increasing demand, but also to provide a superior quality product, particularly in terms of particle cubicity, which was not satisfied simply by washing the fine aggregate.
Another reason that TCL invested in this plant for manu-factured sand was the stagnation of the traditional aggregates market. Excellent growth potential for the business was forecast for the manufactured-sand market coupled with the increasing value of the product.
During the second half of 2002, TCL commissioned their first manufactured-sand circuit with a cone crusher and two Barmac B6100s (150hp each). With a combined hourly capacity of 120 tons, they produced sand passing the 4.5mm mesh.
For quality sand production, TCL adopted a combination of two technologies — cone and autogenous VSI crushers. These machines complement each other to produce quality manufactured sand. The combination of the two technologies is superior to traditional plants using only cone or VSI crushers, particularly in the feed conditions found at TCL’s quarry.
For screening, normally a critical process in sand production, two screens were placed in series each with a sieve area of 5m x 2m. The feed for this plant consists of five products generated by the crushing of conventional aggregates with a maximum size of 32mm and with the majority of the feed (about 50%) consisting of an 11–22mm fraction. A proportion of the feed consists of 4.5–7mm material originating from the washing plant, which increases the level of moisture in the feed. The feed varies in accordance with the market demand for coarse aggregates.
The main advantage of the concept adopted for the sand plant is the acceptance of coarse aggregate surplus, which prevents the excessive supply of products that the market has little demand for. The use of the cone crusher for first reduction to –11mm makes it possible to better use the high-reduction characteristic of this type of crusher. The two Barmacs are used in the final reduction phase, generating particles with suitable gradation and particle shape for concrete production.
Using this combination a plant was obtained that featured: high-production; low-circulating load; tolerance to load variation in the feed grading; high tolerance to moisture; excellent shape; and control over the generation of microfines.
As a result of an increasing demand for premium-quality manufactured sand, TCL decided to extend their capacity and to diversify their product. They invested in another crushing circuit, consisting of two Barmac B7100 VSI crushers (250hp each), for the production of mortar sand with a maximum size of 2.4mm. This line, producing 70 tons/h, has been operating since early 2003.
TCL still keep a washing plant in operation to cater for their traditional customers. However, about 25% of the manufactured sand for concrete is currently sold unwashed with high levels of microfines, a percentage that is still growing.
Eduardo Lanna, partner at TCL, commented: ‘Attitudes of our customers in relation to crushed sand are changing. Increasingly our customers are becoming aware of the advantages of unwashed crushed sand with high levels of microfines, especially from rock as clean and free of impurities as ours.’
Beyond normal aggregates, TCL see their future as being in the production of manufactured sand because of its qualities and the increased restrictions on natural sand production. Through their two dry-sand production lines, TCL are the biggest manufactured-sand producers in Brazil.