The Correct Dose
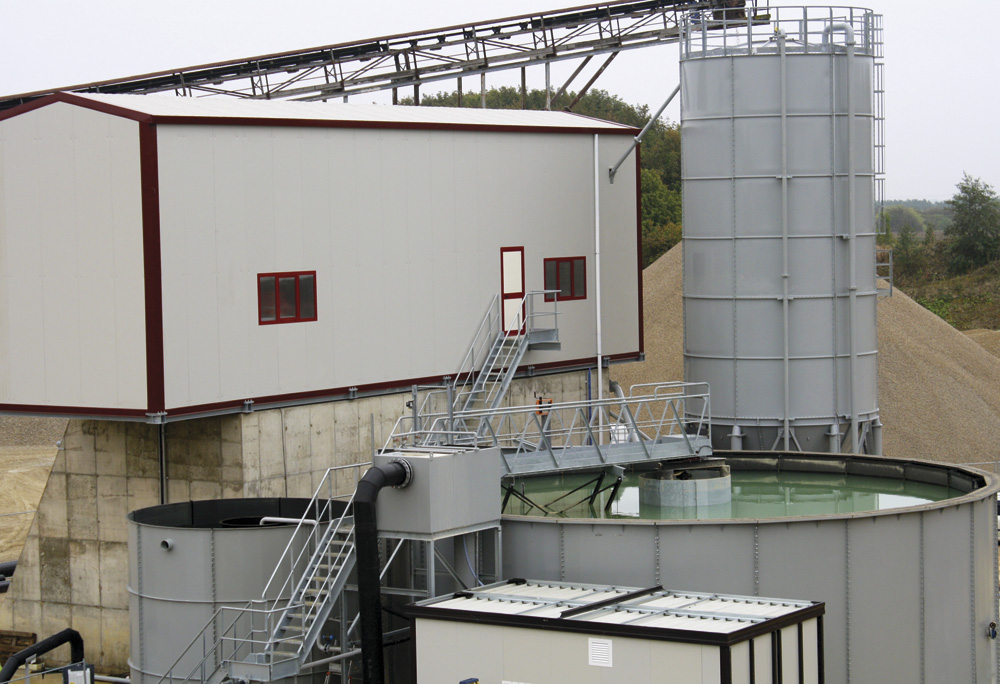
Finedoor install Sotres water-treatment system at Darrington Quarry
Darrington Quarries Ltd, part of the international infrastructure, environmental services and energy group FCC, are a long-established quarrying company operating in Yorkshire with six limestone quarries situated close to the A1 from Doncaster in the south to Tadcaster in the north. Together with a sand quarry at Hensall, the company offers a full range of limestone aggregates for road construction, house building, concrete production and civil engineering. In addition, Darrington Quarries offer recycled aggregates and certified Green-Tree topsoil, with inert materials being accepted at their Barnsdale Bar Quarry for recycling and restoration applications.
Last year the company instigated a procurement process for the installation of a water and silt treatment plant at Darrington Quarry, and following a competitive bidding process Finedoor Ltd were awarded the turnkey project contract to supply a Sotres water-treatment plant capable of processing up to 450m3/h (99,000 gal/h or 1,650 gal/min) of waste water from the quarry’s Sotres washing plant. Working eight hours a day, five days a week and 200 days per annum, and designed with low maintenance and running costs in mind, the new facility will produce easy-to-load dry mud for disposal and clarified water for reuse in the washing plant.
Finedoor were responsible for the construction of the new plant, including all steel erection, installation of machinery, electrics and commissioning; with the electrical work being sub-contracted to Specialist Electrical Systems Ltd. In addition, as the plant was constructed to current CDM regulations, Finedoor took on the role of CDM co-ordinator for the design and construction of both plant and civil works.
Treatment plant flow
Waste water containing suspended solids (–80 microns) from the quarry’s washing plant is pumped into a feed box where it is dosed with a dilute flocculant solution and subjected to high levels of agitation before being discharged into the centre of a 13m diameter thickener tank via a tripod pipe. Within the tank the flocculant effect causes the fines to settle to the bottom to form a sludge bed.
A peripheral scraper arm and central scraper device concentrate the sludge into the central cone of the tank, thus eliminating any water suction by the sludge pump.
Once the desired concentration of fines has been reached, the sludge pump, which is mounted in a tunnel directly beneath the thickener, automatically commences extraction, maintaining a homogeneous mixing of the slurry and avoiding any blockages within the central cone. The extracted sludge is pumped into a 200m3 capacity buffer silo equipped with a pump at the base of the silo cone. An ultrasonic probe monitors the amount of sludge within the silo and allows the pressing cycle to commence when there is sufficient sludge available to feed the filter press. The press itself is a Filmac unit featuring 1,500mm square plates, an adjustable four-point plate-shifting (shaking) facility and cloth-washing system.
Meanwhile, clarified water from the thickener tank overflows into the vessel’s peripheral trough and is fed to a buffer tank from where it can be pumped back to the washing plant for reuse. A separate fresh water tank, fed from an external source, provides the requisite top-up (50m3/h) and is used to feed the flocculant apparatus.
The water-treatment plant is operated from a dedicated control room via a finger-touch PLC system. This sits alongside the Controlfloc flocculant-dosing apparatus, which is equipped with two tanks to allow low-concentration flocculant preparation and ideal maturation. Waste water sampling in the supply phase together with measurement of sedimentation rates allows for adjustment of the flocculant dose as appropriate. An inverter allows the PLC to make these adjustments automatically by varying the flocculant pump velocity.
The installation is now in full production and proving very successful, despite having endured one of the UK’s worst winters in living memory. Darrington engineering manager John Dickinson commented: ‘Initial fire-up was good; just about every section of the plant worked first time. Last winter did highlight some problems with frost protection, but Finedoor worked to repair the damage as quickly as the parts could arrive. Frost protection has been extended and since this was completed the plant has performed as expected.’
For further information visit: www.finedoor.co.uk