Taking on Extra Ballast
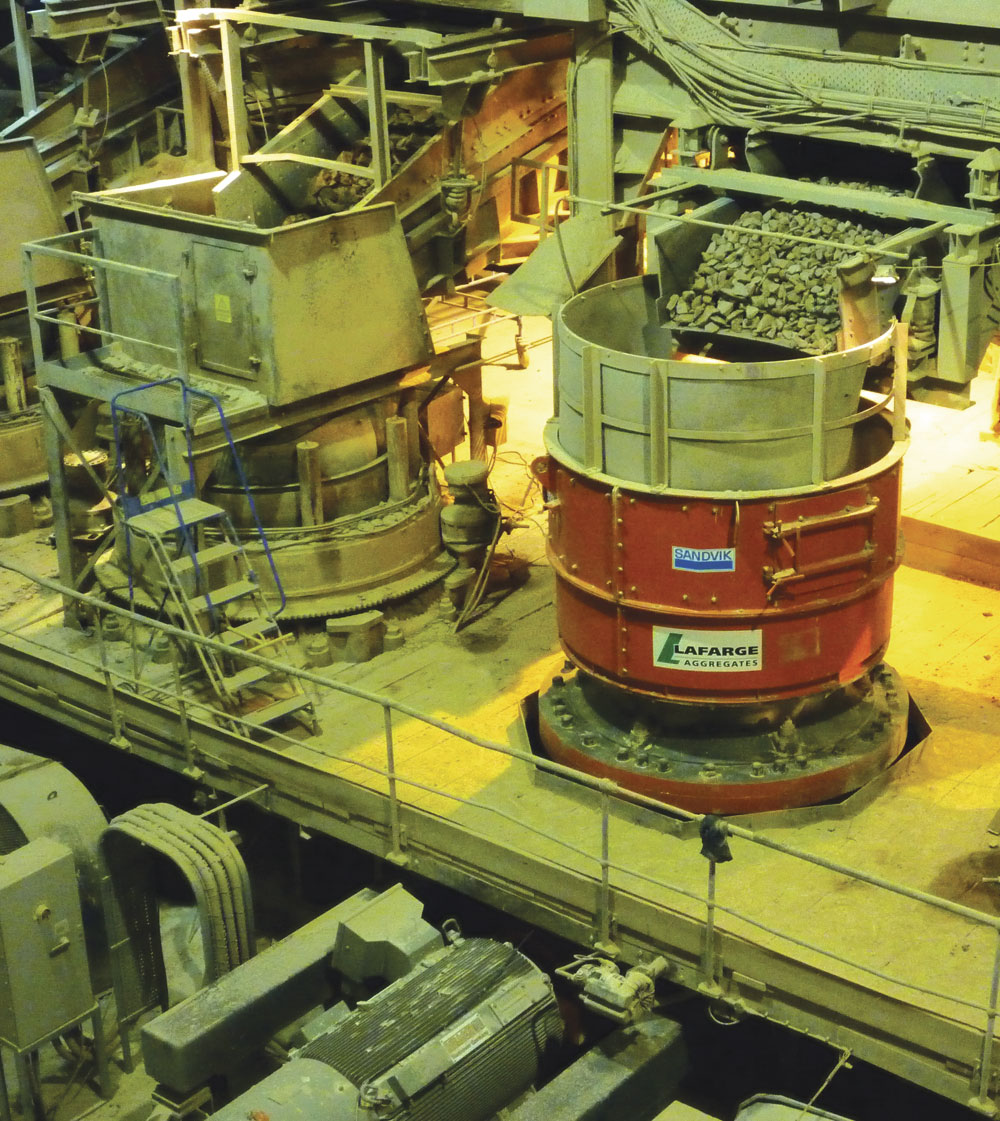
Sandvik CH870 cone crusher exceeds expectations at Mountsorrel
In more typical market conditions, unlike those being faced by the industry at present, Lafarge Aggregate’s flagship Mountsorrel Quarry, near Quorn, in Leicestershire, extracts around 4.5 million tonnes of high-quality granite each year – making it the largest granite production site in Europe. Highly valued for its strength and durability as a construction material, as well as its characteristic pink colour, the granite is processed into a variety of drystone aggregate products and is also used in the production of asphalt and ready-mixed concrete.
The quarry’s primary drystone product is railway ballast, which accounts for around one million tonnes a year or nearly a quarter of the site’s total annual output. Until last year, production of this –63mm +40mm material involved the use of an ageing 7ft shorthead tertiary crusher, but in a move designed to improve production flexibility at the site, this has unit now been successfully replaced by a Sandvik CH870 cone crusher (formerly known as the H7800), which has brought with it a number of additional and unexpected benefits.
‘Over the next few years we are looking to replace a number of our existing crushers, many of which are around 30 years old, with new technology that will deliver greater flexibility and allow us to achieve our goal of just-in-time production,’ explained Mountsorrel Quarry’s operations manager, Angus Shedden. ‘We want to get to the stage where we can maximize the percentage of first-pass products in line with the sales demand at any given point in time.’
As part of this strategy, in December 2008 the Sandvik CH870 unit was installed on a six-month trial basis as a direct replacement for one of the site’s existing 7ft shorthead tertiary units. The new machine was targeted with achieving a number of key performance parameters during the trial period, after which, depending on the results, Lafarge would have the option to buy the crusher, extend the trial or return the machine to Sandvik.
Ballast production at Mountsorrel
To produce railway ballast, Mountsorrel’s –300mm primary crusher-run product is first passed over a vibratory scalping screen to take out the bulk of the –40mm material before being sent to the quarry’s 140,000-tonne primary surge pile. From here, clean –300mm +40mm product is recovered via a reclaim tunnel and fed to a high-capacity weigh hopper located in the quarry’s Phase 2 processing plant. Material from the weigh hopper is fed in equal proportions to two 7ft standard secondary cone crushers, before undergoing primary screening to remove any existing –63mm +40mm railway ballast and fines, which are sent for further crushing and/or screening, as appropriate. Meanwhile, the +63mm material rejected by this screening stage is sent to the recently installed CH870 for tertiary crushing.
According to Sandvik, the 50-tonne CH870 cone crusher is well suited to both secondary and tertiary applications. The machine has the capacity to handle throughputs ranging from 280 tonnes/h to 1,510 tonnes/h and offers hydraulically adjusted close-side settings (css) ranging from 10mm to 70mm. At Mountsorrel, the unit is routinely operated with a 42mm css for railway ballast production and currently produces around 750–850 tonnes/h.
The machine is choke fed by a Mogensen vibratory feeder and driven by an unusually large 600kW motor featuring direct drive and inverter control, which allows the crusher countershaft to be run at variable speeds.
The machine is also equipped with Sandvik’s ASRi automatic setting system, which monitors the load on the crusher and helps to optimize its operational efficiency by automatically adapting the machine to variations in feed conditions. The system also allows close-side setting and countershaft speed adjustments to be made, either locally or remotely from the Phase 2 control room, while the machine is running.
‘The primary role of the CH870 is to make railway ballast, but if a ballast train is cancelled or we don’t want to produce this particular product for any reason, we can speed up the machine and tighten the close-side setting to reduce the amount of –63mm +40mm produced and create more single-size products,’ commented Mr Shedden. ‘Likewise, if two trains are due to arrive back to back and we need more first-pass product than normal, we can slow the machine down and open the css to increase ballast production.
‘As well as giving us far greater production flexibility than our previous machine, we have found that the CH870 is actually delivering a 10% increase in the production of first-pass product, which is a real bonus.’
Increased yield aside, the new unit has provided another and this time unexpected benefit for the Phase 2 operation at Mountsorrel. The CH870 has not only directly replaced the quarry’s existing 7ft shorthead tertiary cone crusher, but has also allowed another similar shorthead machine to be shut down.
‘As well as having sufficient capacity to take material from the existing feed bin, the Sandvik unit has also proved itself capable of accepting the material from an adjacent bin, which has allowed us to switch off a second 7ft shorthead machine. This has been a huge and unexpected benefit as we have one less machine to operate and maintain,’ explained Mr Shedden.
Another significant advantage of the new machine is that it generates far less dust than the shortheads, which is resulting in a safer and more comfortable working environment for staff at the site, and contributing towards Lafarge’s stated aim to become one of the world’s safest companies. Moreover, although still in its early days, maintenance requirements on the CH870 have been minimal, apart from a few routine liner changes carried out by Sandvik during the trial period.
‘The CH870 really did exceed all our expectations during the six-month trial period,’ commented Mr Shedden. ‘It achieved everything we asked of it – and more, and as a result we had no hesitation in deciding to purchase the machine at the end of the trial. Since then is has continued to impress, delivering excellent results and providing the improved production flexibility we were seeking.’