Molson Finlay help Hogan meet increased demand
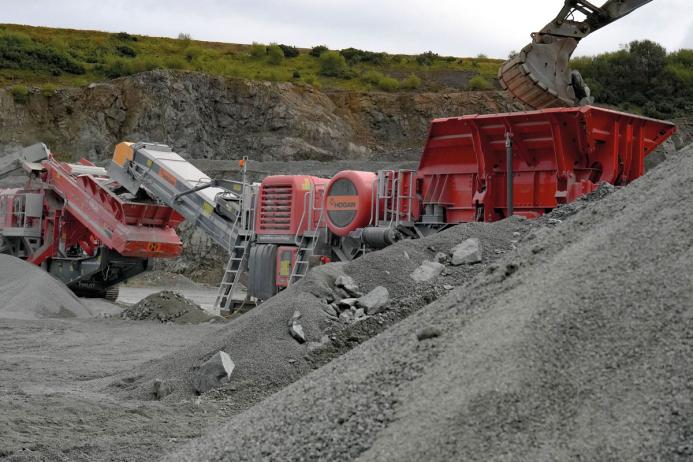
First published in the January 2025 issue of Quarry Management
New Finlay J-1170+ jaw crusher and C-1540 cone crusher boost output for Hogan Group
The rugged North Wales coastline is peppered with numerous quarries visible from the main arterial route from Chester to Holyhead. Whilst many of these quarries sit either centrally or to the east of the country, Ynys Mon (Anglesey) has one hidden gem supplying a large amount of material both locally and back towards the east and even as far as Manchester and Stoke-on-Trent.
Gwyndy Quarry sits almost in the centre of the island near the village of Mona and has been in operation for more than 50 years. The original operator of the quarry, Lewis Hutchings, sold the premises to the Hogan Group in 1993. Based just a few miles away in Bangor, they have continued to quarry the site ever since.
Hogan Group are a multi-facetted company supplying aggregates in their raw form as well as ready-mixed concrete and asphalt across North Wales and beyond. The company also undertakes road maintenance works across the region with their instantly recognizable fleet of bright orange vehicles a common site in both North Wales and north-west England.
The addition of Gwyndy Quarry, and more recently Gwynedd Quarry, has allowed Hogan to bring their requirements for high-quality aggregates for their concrete and asphalt divisions in-house. Whilst Gwyndy Quarry is at the forefront of this robust supply chain, the added benefit of being able to supply outside contractors with a steady source of high-quality material was one the company could not pass over.
Elfed Hughes is quarry manager at Gwyndy and has been at the helm for more than 40 years, having worked for the previous owner at the site. ‘We have been supplying materials locally for many years but under Hogan’s ownership we have increased our production not only to meet our own in-house requirements, but also to service those of others across the region,’ he commented. ‘We produce a range of aggregates from dust up to 50mm stone and rock armour, and supply many concrete and asphalt plants across the area. Whilst it may seem strange that we supply our rivals with materials, we are also their customer when it comes to our road resurfacing works and regularly purchase asphalt off them in large quantities when we are undertaking surfacing projects.’
The small and well-kept quarry has recently been in the process of upgrading much of its mobile plant to reduce its fuel bill and increase productivity and the quality of its material. ‘We have used a fixed crushing and screening plant for many years, but with increases in the orders for all materials, we decided that having a dedicated plant for dust, 6mm, and 10mm stone would allow us to meet orders more productively and cut down our internal haulage costs,’ said Mr Hughes.
To meet the increase in demand the company looked across the market for a suitable solution to its crushing needs. ‘There is a wide choice of crushing and screening products these days and we wanted to be sure we chose the right product not only in terms of material production, but also in terms of reliability, servicing costs, and residuals,’ commented Mr Hughes. ‘We spoke to our existing supplier and others before settling on a deal from Molson Finlay. We decided to go with them as their overall package was what we wanted, and from speaking to others in the industry, their backup and customer service was right on the money.’
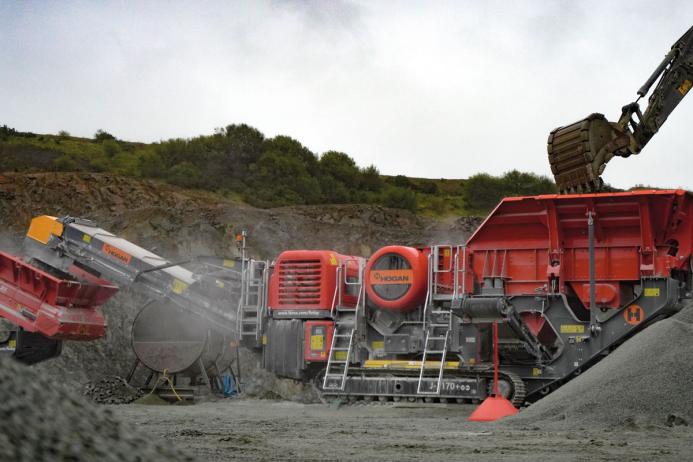
The deal was struck for a pair of crushers in the shape of a highly productive C-1540 cone crusher which is fed by the latest model in the Finlay range of jaw crushers, the J-1170+.
The second-generation Finlay J-1170+ jaw crusher has been designed to deliver economical, high production figures in the most demanding of applications and is well suited to the aggregates sector. Powered by a fuel-efficient Scania engine delivering 345hp, the hydrostatically driven Terex 1100mm x 700mm high-capacity jaw chamber provides the crusher with consistent and effective reduction of material and has been upgraded in several areas to reduce downtime and increase productivity compared with the previous model. Blockages below the crusher have been minimized thanks to the generous 510mm clearance, allowing the largest of product sizes to be produced quickly and efficiently. Hydraulic close-side setting allows for quick and accurate adjustment of the jaws, which have been carried over from the previous model, whilst the chamber box housing the jaw has been significantly improved to provide additional stress relief and strengthening where required.
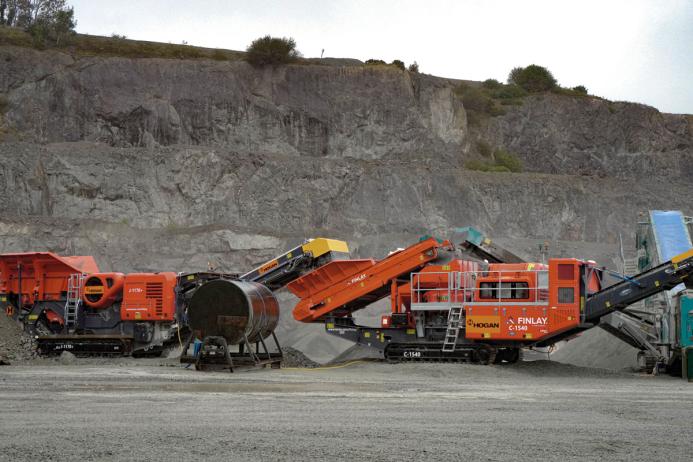
The J-1170+ is now fitted with a JW42 bearing arrangement on the jaw, a design taken from the larger J-1175 model to increase its strength and longevity. The bearing cartridges have also been positioned on the outside of the mainframe’s side plate for easier maintenance. Other aspects of the larger J-1175 have been carried through to the smaller model, including the use of the jaw wedges and cylinder which allows a minimum of 50mm close-side setting even with fully worn jaw plates. With new jaws in place and the jaw shim removed, the J-1170+ can effectively produce material up to 157mm in size.
The large, 10m3 hopper allows for a large volume of material to be loaded, ensuring a constant flow over the heavy-duty vibrating grizzly bars. At just 4.33m in height, the J-1170+ can be loaded from ground level by most excavators should the need arise. Hogan have opted to build a pile of material for the excavator to sit on making it easier, and with the standard flares fitted, the width of the hopper is increased to 2.48m. Optional extensions to the hopper increase both the width and load-over height and can add a further 2m3 to the hopper’s capacity.
The 1m wide material belt has a discharge height of 3.9m and is well suited to the accompanying C-1540’s hopper. Impact bars and wear-resistant liners at the head of the conveyor reduce machine downtime and costs. The lower sections of the conveyor have been fully tunnelled to aid material flow and reduce snagging points which is especially important in recycling and demolition operations. The conveyor can be raised and lowered to assist with the removal of any blockages, even whilst the machine is still crushing. The J-1170+ is also fitted with an overband magnet, ideal for the demolition and recycling industry, and can also be configured with a fines conveyor.
Material is blasted from the face before being transported to the crushing train where the J-1170+ is fed by a 22-tonne excavator. The rock is fed into the jaw crusher with all the resulting crushed material being fed into the 34-tonne C-1540 to reduce it to a maximum of 10mm. With a requirement to accurately produce material of this size, the cone settings took time to dial in correctly and consistently, according to Mr Hughes. ‘I have to hand it to Tom Pope at Molson Finlay for his persistence in setting the train up just as we needed it. With the set up now correct, we are consistently producing 10mm and below from the cone,’ he commented.
The C1540 is fitted with a proven Finlay 1000 cone crusher that is choke fed and fitted with an integrated level sensor, automatic tramp relief and hydraulic close-side setting adjustment to allow for easy resizing of material. Powered by a 350hp Scania Stage V engine, the C-1540 is an ideal accompaniment to the J-1170+ jaw, keeping up with the primary crusher’s steady output. Both crushers are linked together allowing a seamless flow of material between the machines and are controlled via a handheld remote-control unit in the excavator.
Material coming off the cone crusher’s belt is fed on to an inclined screen which was previously used in another part of the quarry. The screen separates the material into its final dust, 6mm, and 10mm sizes before another new investment, a 25-tonne wheel loader, stockpiles the material and loads it on to a stream of trucks coming down on to the quarry floor.
Both crushers have excellent access thanks to well-designed ladders and handrails. Engines and cooling packs are easily accessed for routine servicing with LED lighting providing a safe working environment in the darkest hours. The J-1170+ is designed around a Danfoss PVG hydraulic system allowing for better control and efficiency with variable pumps running at low-level engine loads. The entire hydraulic system is situated at low level allowing for ground-level access when servicing. Finlay have also increased the IP rating on the centralized electronics cabinet and have added a new touchscreen within the control cabinet to allow direct adjustment of the machine.
‘We have been very happy with the performance of the new crushers,’ said Mr Hughes. ‘They mark a significant investment in material production at the quarry and have been living up to their expectations so far. Also, the customer service we have received from Molson has been excellent; from the delivery and commissioning of the kit to the ironing out of settings, they have been first class.’
Subscribe to Quarry Management, the monthly journal for the mineral products industry, to read articles before they appear on Agg-Net.com