Tackling The Difficult Stuff
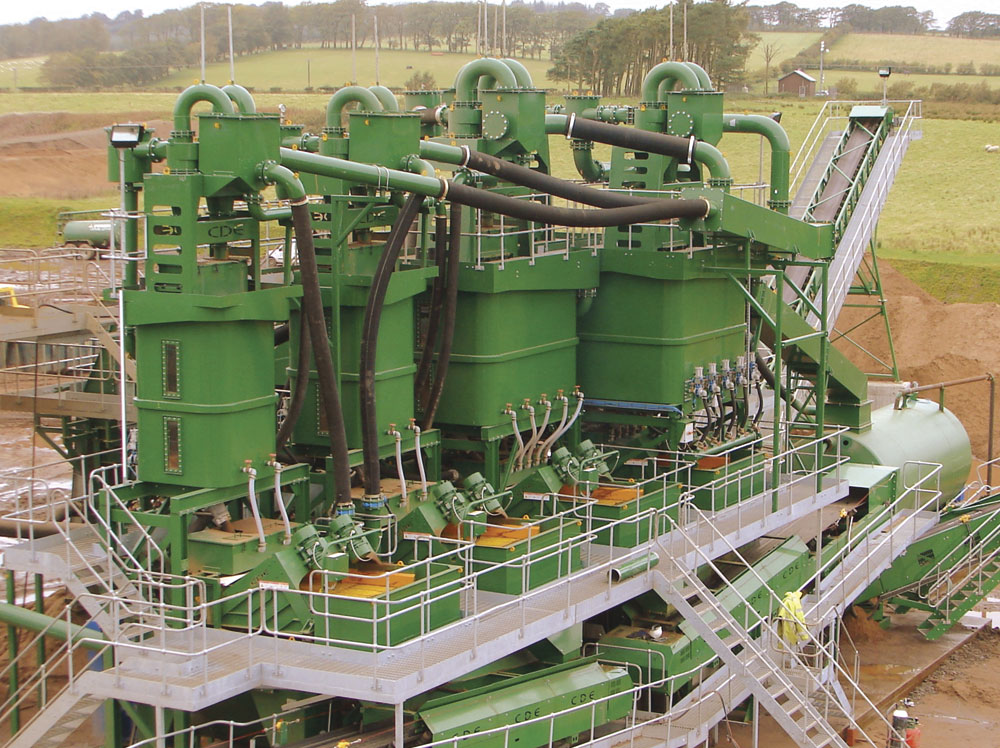
Tarmac Ltd’s sand and gravel plant at Snabe Quarry demonstrates how a new approach to the processing of lignite-contaminated materials can bring significant advantages
Everyone working in the UK quarrying sector is aware of the growing need to tackle materials that, in the past, would not have been considered for processing. As the time approaches when much of the clean and easily processed material has been exhausted, attention is starting to focus on how to effectively process more ‘difficult’ materials in the production of high-quality sand and aggregates.
The contamination of sand and gravel deposits with lignite, and the development of processing systems to deal with this contamination, is evidence that there is increasing pressure to process materials that were previously overlooked. Lignite, in itself, can be a very useful commodity, being a soft brown fuel, the characteristics of which are somewhere between coal and peat.
In Greece more than 50% of electricity comes from lignite-fuelled power plants, while in Germany deposits of lignite are concentrated around the Cologne area and stocks are believed to amount to more than 50 billion tonnes. These are currently being exploited and generate around 25% of the electricity produced in Germany.
Tried and tested system
However, when lignite is present in deposits of sand and gravel it presents a significant problem, as it compromises the final quality of the sand/aggregate products. In seeking to process this material effectively, the specification of a system that is tried and tested in the effective removal of lignite is crucial.
One company that has considerable experience in the design of such processing systems is CDE Ireland. The area surrounding Lough Neagh, in Northern Ireland, is another where there are significant lignite deposits, and the proximity of these deposits to the company’s headquarters in Cookstown, Co. Tyrone, means that CDE have developed significant experience with local quarry operators in the effective removal of lignite from sand and gravel deposits, to ensure the production of clean, high-quality building materials.
‘We are very familiar with the problems posed by lignite and have been asked the question about effective removal by several local operators over many years,’ explained Dermot Murphy, CDE’s technical manager for all lignite removal plants. ‘This experience has helped us to develop a lignite-removal system that we believe to be the most effective available for operators faced with this issue.’
Performance guarantees
When dealing with a plant to process lignite-contaminated feed material, it is usually the case that quarry operators will seek guarantees regarding the extent to which the lignite can be removed. This is because of the detrimental effect that any significant volume of lignite in the final products will have on their commercial viability. This requirement also significantly limits the options available to quarry companies, as there is only a limited number of suppliers of equipment who will agree to performance guarantees for their plant. The CDE plant at Tarmac Ltd’s Snabe Quarry, in South Ayrshire, Scotland, has been custom built to specifically tackle the individual characteristics of the feed material at this particular site. The plant’s performance is measured by a set of pre-defined production requirements, including final levels of lignite in the sand and aggregate products.
The plant at Snabe Quarry has a capacity of 480 tonnes/h and produces two commercial sand products (a concrete sand and a building sand) as well as 5–10mm and 10–20mm aggregate products. The plant includes a wide range of equipment from the CDE portfolio, including Prograde screens, numerous feed, stockpile and transfer conveyors in various configurations, and CFCU system for the washing of the lignite-contaminated sand product.
The processing system
The location of the plant in relation to the material to be processed was the first issue at Snabe Quarry. This required the development of a feed system whereby the raw feed is first delivered on to a 34m long inclined transfer conveyor which discharges on to a stockpile. Two vibrating feeders located under the stockpile deliver the material to a 29m long tunnel conveyor.
This delivers the material to a Prograde P144 double-deck rinsing screen. The top deck removes the +20mm material, which is delivered to a crusher via a 20m long static feed conveyor, before being returned to the Prograde screening phase. Meanwhile, the 5–20mm material is sent to a Prograde P75 dry sizing screen for classification into 5–10mm and 10–20mm aggregate products.
Lignite removal phase
At the same time, the –5mm slurried material is sent from the Prograde P144 to the CFCU lignite-removal system. This comprises a complex configuration of upward-flow classification tanks, cyclones and dewatering screens which has been specifically designed to cope with the individual characteristics of the feed material, as well as Tarmac’s requirement to produce two high-quality sand products. The specification of these final sand products is, once again, controlled by performance guarantees.
‘Every lignite-removal plant is entirely unique,’ explained Dermot Murphy. ‘The plant has to be constructed around the specifics of the project – most significantly the required capacity, level of lignite contamination and the desired final-product specification.’
The slurried material is first delivered to a customized cyclone set up where the –63 micron material is removed. The –5mm to +63 micron slurry material is then delivered to the CFCU tanks where an upward flow of water forces the lightweight lignite particles to rise and overflow the top of the tank before being passed over a series of sieve bends and then on to a waste stockpile. This material is subsequently used for site restoration.
The remaining material is delivered to a series of dewatering screens where the sand is dewatered and stockpiled. The final moisture content of the sand products is another feature of the plant that is covered by the extensive performance guarantees specified by Tarmac, the requirement being that the final concrete and building sand products should have moisture contents not greater than 15%. These levels are being comfortably exceeded with the concrete sand moisture content being consistently around 10%, and the building sand product achieving a level of 6%. Total sand production through the CDE plant at Snabe Quarry is a minimum of 300 tonnes/h, of which 200 tonnes/h is concrete sand and 100 tonnes/h is building sand.
Minimizing waste
Following the production of the two in-spec sands, an additional processing step is included on the CDE plant to minimize the volume of waste material being sent to the on-site settling lagoons. This involves a NanoWash fines-recovery plant which receives the waste material from the main sand washing plant and recovers all +40 micron material. This step significantly reduces the volume of waste material in the lagoons, thereby reducing maintenance costs at the site.
The waste material is passed through a specially configured cyclone arrangement whereby the +40 micron material is recovered and delivered to a dewatering screen. This material is then discharged to an ultra-fine sand stockpile with the waste water being pumped to the on-site settling lagoons to be recycled.
Plant results
Since the plant was commissioned at Snabe Quarry it has exceeded the requirements detailed in the extensive performance guarantees drafted by Tarmac. First, and most significantly, lignite is being effectively removed – the final lignite content was required by the performance guarantees to be 0.05% by mass. This is being comfortably exceeded with Tarmac reporting levels of 0.03% by mass during the regular tests that they undertake on the final products.
Moreover, the requirements relating to capacity and the moisture content of the final products have never been called into question. With more than 12 months continuous production now having been achieved at Snabe Quarry, the plant is allowing Tarmac to deliver significant volumes of material to the local market that would otherwise not have been available.
For further information on this system or any of the other of the washing plants offered by CDE, tel: (028) 8676 7900; email: info@cdeglobal.com