Sundre Contracting choose Major Wire Screens
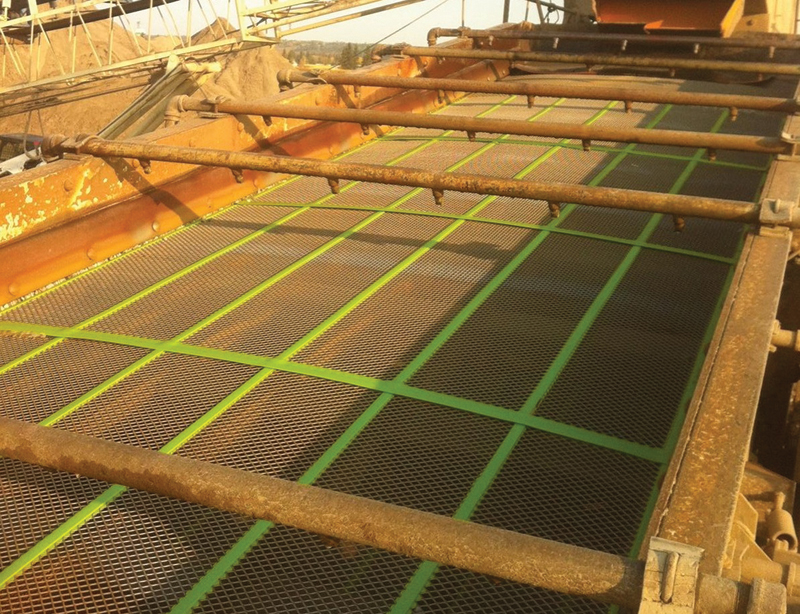
First published in the February 2014 issue of Quarry Management as Screening in the Rain
Advanced screening technology helps prevent rain delays from ruining profits for Canadian company
By Gary Pederson, vice-president of sales, Major Wire Industries Ltd
Family-owned and operated since 1978, Sundre Contracting Co., located in Sundre, Alberta, Canada, produce more than 30 different product sizes – from 1.6mm fine sand to 305mm screened rock and everything in between. Whether their customer is an Alberta road builder, concrete plant or any of a number of golf courses in Alberta, British Columbia and Saskatchewan, their products must meet tight specifications or be rejected. Dealing with severe screen media blinding and pegging from clay material and a rainy climate, Sundre needed an advanced solution. After exploring several screen media options, the operation found one that helped eliminate the production-crippling effects of these conditions, ultimately saving them thousands of dollars while waiting for Mother Nature to co-operate.
One instance of Sundre’s success with this advanced screen media is evident in a challenging road job they accepted. Using two 6m x 2m ELRUS screen decks equipped with conventional woven-wire screen media, the operation needed to screen the –20mm aggregate from the customer’s own highly clay-contaminated pit. With the addition of rain every second day, the operation was quickly losing quality because screen media throughput was being compromised. In addition, production time was significantly reduced due to the need to frequently shut down and clean the screens.
‘The wet, sticky nature of the material was causing severe blinding and pegging of the woven wire on our first screen deck,’ said Jason Harder, manager of operations at Sundre Contracting. ‘In order to meet customer material spec, we needed to dry the material, which took time away from producing new, profitable material.’
It was impossible to effectively screen while it was raining because this simply added to the stickiness of the material, so Mr Harder knew another solution was needed. The operation tried a variety of woven-wire and self-cleaning screen media options, but all were still experiencing severe blinding and pegging. At the recommendation of Matt Armstrong, dealer representative at ELRUS Aggregate Systems, Mr Harder installed Major Wire 22mm Flex-Mat 3 Series D tensioned screen media and saw dramatic results.
‘The operation went from not being able to produce at all in marginally rainy weather to being able to operate through heavy downpours,’ commented Mr Armstrong. ‘We’ve recommended Major Wire’s Flex-Mat 3 screen media before and knew it could stand up to the challenge of screening sticky, clay-ridden material.’
Good vibrations
Major Wire’s Flex-Mat 3 self-cleaning screen media allows producers to increase open area, create more screening action and eliminate blinding and pegging problems to achieve more throughput of spec material. Its distinctive lime-green polyurethane strips bond individual wires, allowing them to vibrate independently at different frequencies.
An increase in screening action was just what the Sundre operation needed. More properly sized material fell through instead of sticking to the wire, increasing production by 100% on rainy days since the operation no longer needed to shut down and clean the screens. Using Flex-Mat 3 tensioned screen media, Sundre screen between 250 and 300 tons/h, depending on the product they are making. That is a saving of nearly 2,000 to 2,400 tons/day that the operation would have been losing to rain delays. Jason Harder estimates that using Flex-Mat 3 during this particularly rainy month saved the operation at least 100 hours of production time previously lost due to the need to shut down and clean the screens.
A versatile screening solution
Sundre use Flex-Mat 3 screen media on at least five of their six screen decks in a variety of positions, depending on the material being screened. The operation also utilizes several Flex-Mat 3 wire configurations and opening sizes – 5mm to 22mm – to properly screen the wide range of products they offer customers. For example, the operation uses 11mm Flex-Mat 3 Series D tensioned screen media in its McCloskey mobile vibratory screener to pre-screen various sand products. The Series D configuration provides Sundre with precise sizing of passing material so it can produce the spec material needed by various customers. To screen larger aggregate material, Sundre use 10mm stainless steel Flex-Mat 3 Series LFM tensioned screen media.
‘We love the versatility of Flex-Mat 3,’ commented Mr Harder. ‘We make more than 30 different products in our operation, from golf course sand to concrete and roadbase aggregates, and decorative stone. Flex-Mat 3 helps us screen and wash all products more efficiently and saves us thousands in lost production each year. In addition, we estimate that its increase in open area provides us with up to 30% more screening capacity than before.’
Flex-Mat 3 screen media has also helped Sundre cut costs in other areas. For example, previously, when screening their coarser products, such as –20mm aggregate material, the operation was using a wash plant to screen off the sand that was causing blinding and pegging issues in the dry screening process. This required a large volume of water. Flex-Mat 3’s vibrating wire technology has virtually eliminated this blinding and pegging problem, which means most of the sand does not need to be sent through the wash plant, helping Sundre reduce their annual water consumption. While the wash plant deck is still used to clean many different products, the quantity of silt heading to the settling pond has been significantly reduced. Now that Flex-Mat 3 has reduced the amount of silt in the product when it reaches the wash plant, Sundre are able to spend more of their valuable time screening instead of cleaning.
‘We’ve not seen any type of screen media work better than this,’ said Mr Harder. ‘Major Wire seem to have this technology wrapped up and it will remain a staple in our operation.’
- Subscribe to Quarry Management, the monthly journal for the mineral products industry, to read articles before they appear on Agg-Net