Site Safety and Safer Aggregate Crushing Operations
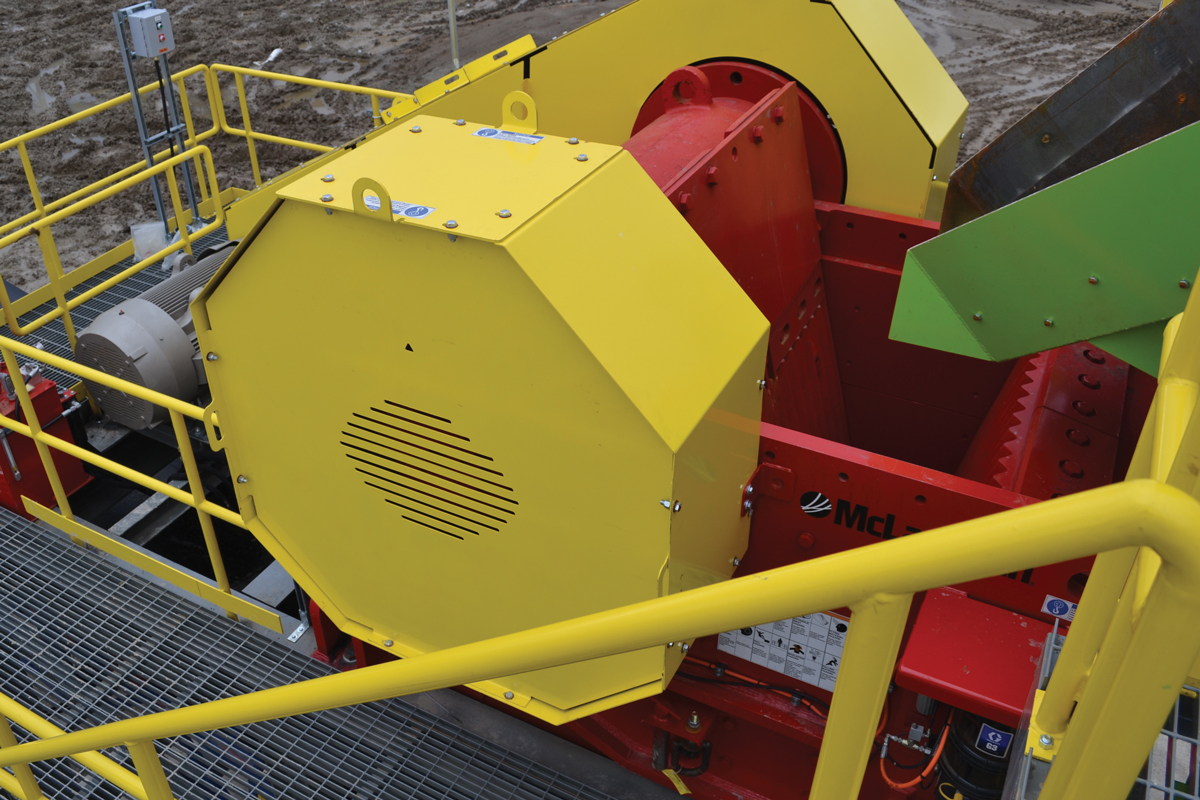
First published in the September 2019 issue of Quarry Management as Safe and Sound
McLanahan discuss the key priorities for ensuring overall site safety and safer crushing operations
Safety requires proactive intervention to prevent workplace accidents. Each company or site should have clear safety guidelines outlining best practices for the entire site, as well as for working with crushers. Before even stepping on site to work with a crusher, employees and/or operators must be trained on all safety procedures for both the site and the crusher. For instance, is the operator clear on the warning signs to look for, emergency stop locations, and appropriate walkways? Make sure the operator or maintenance personnel perform a hazard analysis before each new operation. Conditions such as the time of day, weather and the area around the piece of equipment can all affect the operation about to be performed. It is also a good idea to have a fresh set of eyes look at the conditions. Even when someone is experienced and well trained, it is very easy to see the same thing day-after-day and accept the way things are or miss something.
Overall site safety
While the safety aspects of a piece of equipment such as a crusher are extremely important and will be discussed further, companies should start by prioritizing overall site safety. The aggregates industry is heavily regulated, but regulations alone will not make managers, workers, contractors etc, safer or better safety stewards. To achieve high safety and environmental standards, companies cannot rely on the fear of retribution for non-compliance to achieve these goals. To be successful, the industry must rise above the regulations, inspections and penalties and focus on safety, because achieving this goal is the right thing to do. Tips for keeping a safe site include ensuring effective signage, keeping the site clean, walking the site daily, and maintaining quarry faces and haul roads.
No one should ever turn a blind eye to a hazard or hazardous situation. Do not say: ‘It’s not my job’, or ‘I’m not the one who left it there’, or ‘someone else will fix it’. Every incident, accident or hazardous event should be investigated. Through these investigations, recommendations can be made to improve safety and to prevent the event, incident or accident from occurring again. It is vital that these recommendations are implemented, as without implementation sites are destined to repeat past mistakes.
Crusher safety
While new technologies and equipment to make the workplace safer are emerging every day, a company’s best resource is its workforce. It is important to make sure employees are not only trained on safety procedures within the workplace, but also on proper use of their machine. Untrained, unknowledgeable staff can lead to an unsafe work environment. Just because a person on site works with other types of equipment, it does not necessarily mean they are trained on the proper use of a crusher or a breaker. For example, do they know the correct feed size and capacity? Not knowing these can lead to oversize material entering the crusher, causing a malfunction.
Crusher safety starts with the person feeding the plant. This person needs to be trained on crusher best practices specific to the machine they are working with. An operator may have years of experience of operating and loading a cone crusher, but that does not translate into experience of loading and operating a jaw crusher. Operators also need to be trained on what to look for to prevent unnecessary maintenance. Spending time and resources to train the operator will not only lead to a safer workplace, but, ultimately, will increase production too.
When operators are proactive in keeping their crusher running safely and effectively, the more productive it will be. A couple minutes spent on cleaning or maintenance can lead to hours of extra productivity later and an overall safer working machine. Operators should always keep detailed records of maintenance and other issues.
Once confident that an operator is fully trained on his or her machine, as well as on site-specific safety policies, it is time to look at crushing safety in more detail. Some of main things to look for include ensuring the operator is wearing their protective clothing, and making sure all guards and safety devices are in place, secured and functional before operating the crusher. It is important to ensure that operators review and follow all lock-out, tag-out, try-out (LOTOTO) procedures for the crusher when performing equipment maintenance, repairs or adjustments, and keep the crusher working safely and efficiently by performing regular maintenance inspections. This will allow them to pinpoint any problems that may make the machine unsafe to use. Tips for keeping a safe crusher include operating the crusher at its appropriate capacity, keeping platforms and areas around machine clean, and ensuring lubrication, flow, temperature, wear and pressure are all monitored.
Safety is something that can be carried out and planned for daily, monthly and yearly. Every day, operators should try to make themselves and their workspaces safer. They should clean away any debris that may be a hazard and walk to their workstation by a different route to see if they notice anything unsafe. Good housekeeping is synonymous with a well-organized, professional and safe workplace. Poor housekeeping is synonymous with a disorganized, less professional and hazardous workplace. In the aggregates industry, hazards are everywhere owing to the nature of the business and the equipment and tools used. When less-than-desirable housekeeping practices obtain, they add unnecessary hazards to the workplace. Housekeeping can take up a lot of time if it is carried out only once in a while, but virtually no time at all if it takes place continuously. All employees should be expected to conduct good housekeeping on a daily basis to eliminate unnecessary hazards.
It is important to make sure that crusher operators follow all operational guidelines and that all safety best practices are in place, but also that the entire workforce is properly trained in site safety procedures and best practices. Regular safety meetings should be held to review new procedures or address any safety concerns. Yearly safety goals should be set and operators should be commended for years of safety excellence. Each person on site is responsible for safety and can improve the safety of their workplace. Properly trained operators will lead to a safer workplace and increased production.
- Subscribe to Quarry Management, the monthly journal for the mineral products industry, to read articles before they appear on Agg-Net.com