Raising The Standard
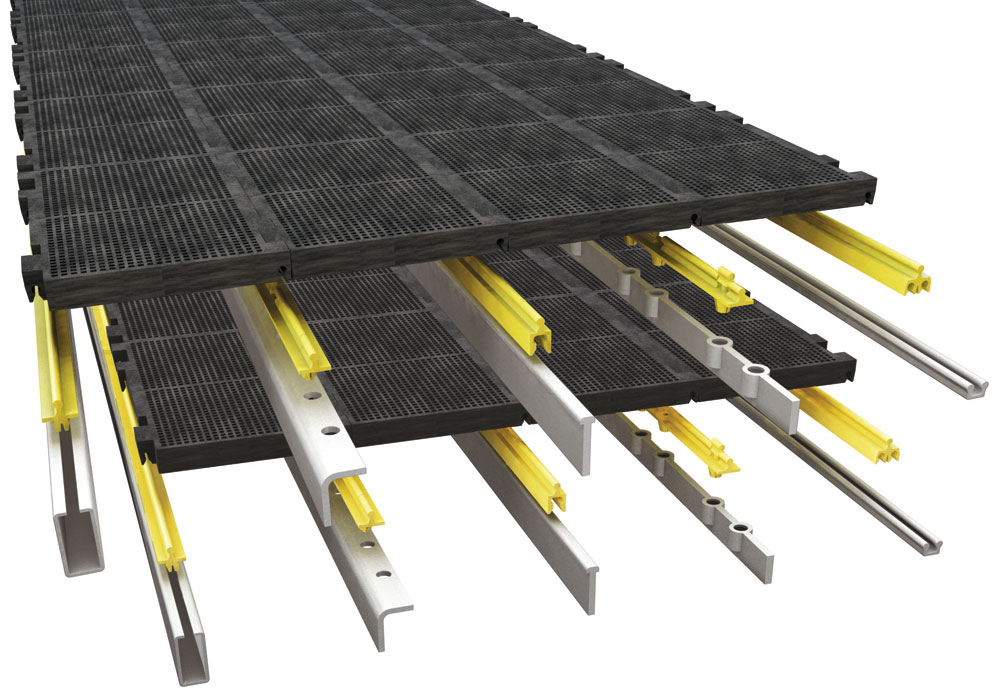
Trellex’s Modular Screen Solutions range offers increased options and benefits
Metso Minerals’ Trellex range of screen media has been complemented with new modular components that have been designed to upgrade systems currently using other manufacturers’ standard fittings.
Screen media installations generally fall into one of four key sub-frame categories and Metso Minerals are now in the position of producing solutions to fit virtually all of them. One of these four key standards is their own patented design and until these patents expire, Metso say they will be the only one-stop-shop for all four types.
Metso add that upgrading to Trellex Modular Screening Solutions will give considerable benefits for customers. Claes Larsson, screening media product line manager, commented: ‘They will now be able to take advantage of the superior features of the Trellex range in performance and handling. Customers can use us as their sole supplier, which is becoming an increasingly important issue in these days of ever-larger organizations.’
Trellex Modular Screening Solutions is the family name for a system that includes a full range of components. Existing products such as stepped modules will remain a very important part of the family, but they are now joined by new additions that will allow Metso’s products to be directly compatible with other standard sub-frames in use. The new range is easily retrofitted to existing systems with no need to weld or cut steel rails. A new profiled strip is simply fitted to the rail and it is then ready to take Trellex modules.
The benefits of upgrading
The new system has been designed with a number of improved features, including lightweight rubber or polyurethane modules, easy snap-on connections and an emphasis on recycling. Another benefit is that the range is said to have a better open area than other solutions on the market, giving better performance.
The strips that the modules are fixed to are narrower than those traditionally used on WS85 installations. This means there will be a smaller blind area at the intersections between panels.
Customers will be able to opt for a special tapered strip to allow them to mimic Metso’s existing system by introducing a step to the deck. This is particularly recommended for applications with a lot of fines.
New range
The new range is divided into three families, depending on the spacing between fixings of 300mm or 305mm and whether they are snapped on transversely or longitudinally. Options include material, size and aperture arrangement, as well as fittings such as deflectors to steer the flow. All are sold under the Trellex brand name.
Individual products are identified by a logical code following the name. This includes letters and numbers that clearly indicate the sub-family: 300LS, 305LS or 300TS. The code also describes the width, length, material composition, aperture type, recycling properties etc. When a customer gets an order acknowledgement, he or she can read from the designation exactly what the product will do.
Literature has also been developed to make choices easier. Metso have used ideas from mobile phone catalogues that use icons to show all the key features, allowing customers to make choices at a glance. Properties of the Trellex modular system can be grouped by factors such as the fixing mechanism, whether it will withstand mining duty, its operating temperature limits, hardness, aperture properties etc.
Maturing market
The use of modular systems is growing and the market is becoming more mature. Better wear life is the biggest factor that has been encouraging customers to move from custom-made steel wear cloths to rubber or polyurethane modules. ‘In extreme cases, a steel wear cloth might need to be changed every week; the rubber equivalent could last eight months or more,’ said Mr Larsson. He added that there are also environmental benefits to using rubber or polyurethane products, as they can reduce noise, and sections can be rotated or replaced as they wear out, instead of having to discard an entire steel cloth.
Challenges for the customer
With a vast array of different systems and products on the market it can be difficult for customers to choose, or to change, their systems. Customers may have screens of more than one design and there are many brand names. It is often hard to tell which components are compatible with their installed framing. Metso say they have detected a trend in that customers are starting to want a group-wide deal with a single supplier of screen cloths. They are looking for someone who can supply all their sites, including systems made to a variety of standard designs.
There are no national or international standards, but modules fall into one of four standard groups, based primarily on width and the sub-frames needed. The four groups are A, B, C and D, with the Trellex system classed as D. This standard Trellex module is 300mm wide by 600mm long and uses a transverse snap-on fixing arrangement. Standard A uses a width of 305mm and varied lengths — most commonly 610mm — and a variety of locking arrangements including pins. Standard B was initially used in Europe but is now used worldwide. Its width is 300mm and the two most common lengths are 1m in Europe and 1.2m in the US. Different methods of attachment include longitudinal wedges or longitudinal snap-on fixing. Standard C is wider than it is long — 610mm by 305mm — and attached to longitudinal stringers; it will be available as part of the Trellex Modular Screening Solutions in the near future.
Every part of the world is dominated by a different combination. A supplier in the US needs to have supplies of A, B and D, in Australia A, C and D, while Europe is dominated by B and D.
The next step
The expanded Trellex range was initially launched in Europe, with the US market following at the end of this year.
The launch of the new range, however, is not the end of development. Environmental protection issues are growing in importance and Metso are keen to promote recycling. Polyurethane can be incinerated without any problem but many rubber products include steel, making recycling difficult. Metso are exploring the possibilities of using carbon fibre or glass fibre as reinforcement, which would greatly improve the recycling of spent modules.