Raising Sand
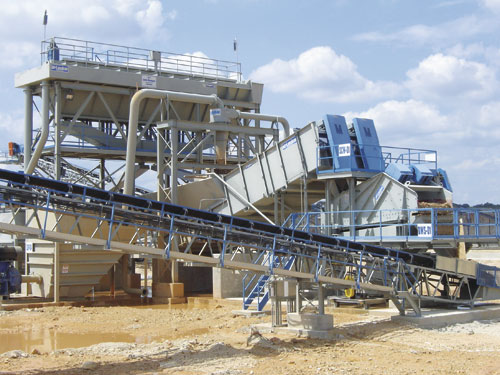
Sand production for construction grades and industrial specifications – the positives and negatives to consider when contemplating wet processing equipment
There are many equipment choices and system designs to consider when wet processing fine materials to produce sand that meets construction grade specifications for concrete, asphalt or mortar. Additionally, several factors pertaining to speciality sands for the glass, industrial and frac sand markets, including the quality of the sand itself, need careful review before designing a processing system.
The process design of the system and the equipment to be used should be based upon the following application factors:
- Particle size distribution of material, either from the deposit or from the crushing, screening and other processing upstream of the processing plant.
- Product specification(s) required for the market area.
- Extraction method of the material to be processed.
- Required plant mobility – portable or fixed.
- Planning constraints such as height or water use restrictions.
Previously discarded dust fractions (typically –5 or –6mm) from hard and soft rock quarries can often be washed, classified and dewatered to produce specification construction sands, thus maximizing use of the deposit. These finished products are often referred to as ‘manufactured sand’.
Sand-processing options
The simplest form of wet sand processing is the removal of fines from a typical –5mm natural/alluvial or manufactured (crushed) sand fraction followed by the dewatering of the washed product for stockpiling and transport purposes (fines permissible in construction sands commonly ranging from zero to 15% passing 63 microns). Sand washing and dewatering equipment includes hydrocyclones, syphon (vacuum) assisted hydrocyclones or Separators, dewatering screens, spiral-screw classifier washers and bucket-wheel dewaterers. The equipment that is most suitable for a particular process is dependent upon the previously stated application factors.
Spiral-screw washers are self-contained, low-profile units that sit directly on the ground and require minimum power. They may be slurry or dry fed (with a water addition) by gravity from an elevated sizing screen above and can be used in either portable or fixed plants. Limitations include limited water capacity, which often leads to an excessive loss of useful fines when incorrectly configured, and a product final moisture content of around 25% by weight.
The bucket wheel is another simple self-contained device. These units are typically slurry fed from a wash screen but also have limited water volume capacities, increasing the risk of fine sand loss. More modern units incorporate pump-fed hydrocyclones for fines recovery where necessary. Increased product fineness and/or marginally cold operating weather, which causes icing of the slots or holes in the dewatering buckets, can lead to excessive moisture in the sand product.
Hydrocyclone- and Separator-based washing plants can handle high capacities and slurry volumes and, if properly sized, are more deliberate in controlling the retention or removal of fines. Typically, these units are elevated on towers or situated within compact structures to allow direct stockpiling or further processing from the discharge. Hydrocyclones and Separators contain no moving parts, yet a correctly configured vacuum-assisted Separator will provide a consistently dewatered product at the underflow, with as little as 18% moisture by weight, irrespective of the feed solids content. Hydrocyclones, however, must be correctly pressurized at their inlet and fed close to their design feed rate to produce dense underflows.
Utilizing tangentially produced centrifugal force, hydrocyclones produce a high g-force on solids, which, in combination with greater attrition due to the scrubbing action and higher velocities experienced in the pumped feed arrangement, ensures a very clean product. The removal of adhered silts and clays from the surface of each particle leads to increased mechanical strength in the final construction sand product and the ability to handle dirty feed materials more effectively.
All the above technologies have limitations in respect of dewatering the final product. The most proven method in this area is the dewatering screen. A dewatering screen uses fine-mesh screening media that provides a mechanical acceleration to particles to break the surface tension and aid in the gravity drainage of the sand.
Dewatering screens are limited in their ability to accommodate large volumes of water, but are able to handle direct sand slurry feeds with solids contents above 35% by weight. For more dilute feeds, hydrocyclones may be utilized to achieve pre-concentration when necessary. Despite low power consumption, the dewatered sand moisture content is typically half that of most other equipment options, typically 12–15% by weight, which produces a drip-free sand product. All dewatering screens lose fines along with the water through the screen mesh. These fugitive fines may be recovered by recirculation back to the feed source or by using a small hydrocyclone to return the recovered fines to the discharge point of the dewatering screen.
Further removal of moisture can only be achieved by technologies such as stockpile dewatering or a thermal drying system.
When is sand-classification equipment required?
Due to inconsistent particle size distribution or grading deficiencies, many sands need to be classified to meet specifications for final use. Some deposits are suitable for the production of multiple products.
It is important to consider the nature of the sand product(s) required and the available market. The possibilities include a single, unchanging specification sand or a multiplicity of specified sands, first separated by sizes into discrete fractions, then either blended in-line or delivered to a storage hopper for blending by recipe according to specification. Recipe plants allow far greater versatility for varying market conditions and more efficient use of a feed whose particle size distribution varies. Such plants, however, with their inherent complexity and sophistication, are often more capital intensive.
Typically, sand-classification equipment will be considered when one or more of the following conditions exist:
- Two or more specification products are to be made.
- Excess intermediate sand grains in the –2mm to +150 micron size range exist.
- Accurate grading or specifications are demanded.
Types of classifiers include:
- Multi-station sand-classifying tanks (trajectory classifiers).
- Hydrosizers or flat-bottom classifiers (density separator).
- Up-current classifiers (elutriators)
All of these devices are at their most efficient when the slurry feed is consistent in terms of solids concentration and flow rates, and is within the limits specified by the manufacturer.
Multi-station sand-classifying tanks perform best when the feed contains no more than 10-15% passing 63 microns. Pre-conditioning the feed to meet this criterion may be achieved most simply by a hydrocyclone. Hydrosizers and flat-bottom classifiers perform best when the feed is concentrated to approximately 50% solids content by weight. In both cases, pre-conditioning the feed to meet this criterion may usually be achieved by use of a hydrocyclone.
Multi-station sand-classifying tanks, while widely used in North America for classifying sands into construction grades, have seen limited use in the global marketplace. Automation by means of computer-controlled systems allows this equipment to optimize construction sand grades used for typical concrete- or asphalt-grade specifications. For optimal classifying performance it is important that the incoming slurry remains at a consistent solids feed rate. Single units are suited for processing up to 350 tonnes/h. For high-capacity requirements, multiple sand-classifying tanks are installed side by side above dewatering equipment.
Hydrosizers and flat-bottom classifiers are capable of making sharp single cuts in the size range of 800–100 microns. Equipment selection is dependent upon the average feed particle size distribution and the sand products required by the market. These classifiers are often the principle size separation equipment used within an in-line blending or fractionated sand plant. Two or more units may be employed, in parallel or in series, to create differing or successive cuts, whether for the production of construction sand, frac sand, glass sand or in support of another mineral-processing operation.
Is contamination present?
As new high-quality deposits are becoming scarcer, previously uneconomic materials with poor particle size distribution and/or contamination in the form of peat, root, wood and lignite (coal) are now often being processed.
Flat-bottom classifiers, sometimes known as density separators or sortifiers, are used in the removal of low specific gravity contaminants such as lignite. Any coarse-sized, low specific gravity contaminant fractions are first removed by sizing screens, while the ‘throughs’, comprising all the sand and the fine contaminant, are directed to the flat-bottom classifier for purification.
Within the classifier, a gentle up-current maintains a heavy, non-turbulent but fluidized sand bed and creates conditions in which low-density particles float. A PLC-resident control algorithm closely controls the underflow discharge valves such that all of the fine contaminant, but very little (if any) fine sand, reports by way of the classifier’s overflow to waste.
Hydrosizer-type classification units, commonly used for wet processing of frac sands (sands for hydraulic fracturing of oil bearing rock), are now widely in demand in natural gas and oil extraction. To meet the stringent requirements for strength and sphericity, these sands must be sharply classified to specific sizes and then dewatered for further processing to meet final requirements.
Water management and fine silt and clay dewatering
After the sand has been washed, classified, dewatered and stockpiled, the resultant remaining waste stream, containing primarily –63 micron solids, is commonly sent to large settling ponds consuming many hectares of land. This method of handling fine, slow-settling solids either just for disposal or to permit reuse of the water, can incur considerable operational costs and management time. Even if planning constraints allow such practice, silt lagoons may present an ongoing environmental hazard. Access to fresh water sources is now commonly restricted by local authorities. This restriction provides an incentive to recover the water and to remove the solids waste in a safe, handle-able form.
Ever greater numbers of wet processing facilities utilize thickening/clarification equipment to dewater waste streams that contain fine solids, producing a dewatered fines ‘cake’ and clear water suitable for rapid reintroduction to the process. Such incoming slurries are commonly dilute (around 5% solids) and require a two-stage treatment process, the first stage being a thickener. Carefully controlled flocculent dosing encourages the fine suspended solids to coagulate and then settle to the bottom of the thickener tank where a slow-turning rake or deep cone gently directs the resultant paste concentrate towards the underflow discharge point located bottom centre within the tank. Meanwhile, clear water (as much as 90% of that entering the thickener) is permitted to overflow the unit’s weir before being electrostatically neutralized ready for recycling to the plant.
The ‘thickened’ solids underflow is generally in the order of 35–50% solids by weight. These ‘volume-reduced’ fines can be pumped to smaller, permanent storage/disposal areas or further dewatered by a variety of press equipment. Today, recessed-plate and membrane filter presses offer a simple and efficient solution with low operating costs.
Recessed- and membrane-plate filter presses use little or no further chemicals, utilizing high pressure for dewatering thickened solids and discharging a resultant cake comprising up to 80% solids by weight. Lacking any free water, the silt/clay cake solids can be belt conveyed or transported by truck immediately.
Summary
As with many material handling problems, developing an efficient system for sand processing can be more art than science. While many operators have tended repeatedly to utilize the same methods over the years, refinement and development by equipment manufacturers continues to provide ever more efficient and innovative solutions, making possible both the rapid recovery of effluent water for reuse within the plant and the recovery of previously rejected ‘waste’ for value-added use within the product stream.
Input to this article was provided by Craig Dewsnap, Charles Grocott and Dave Schellberg of McLanahan Corporation. For more information visit: www.mclanahan.com