Quality Silica Sand Products Call For Specialist Process Treatments
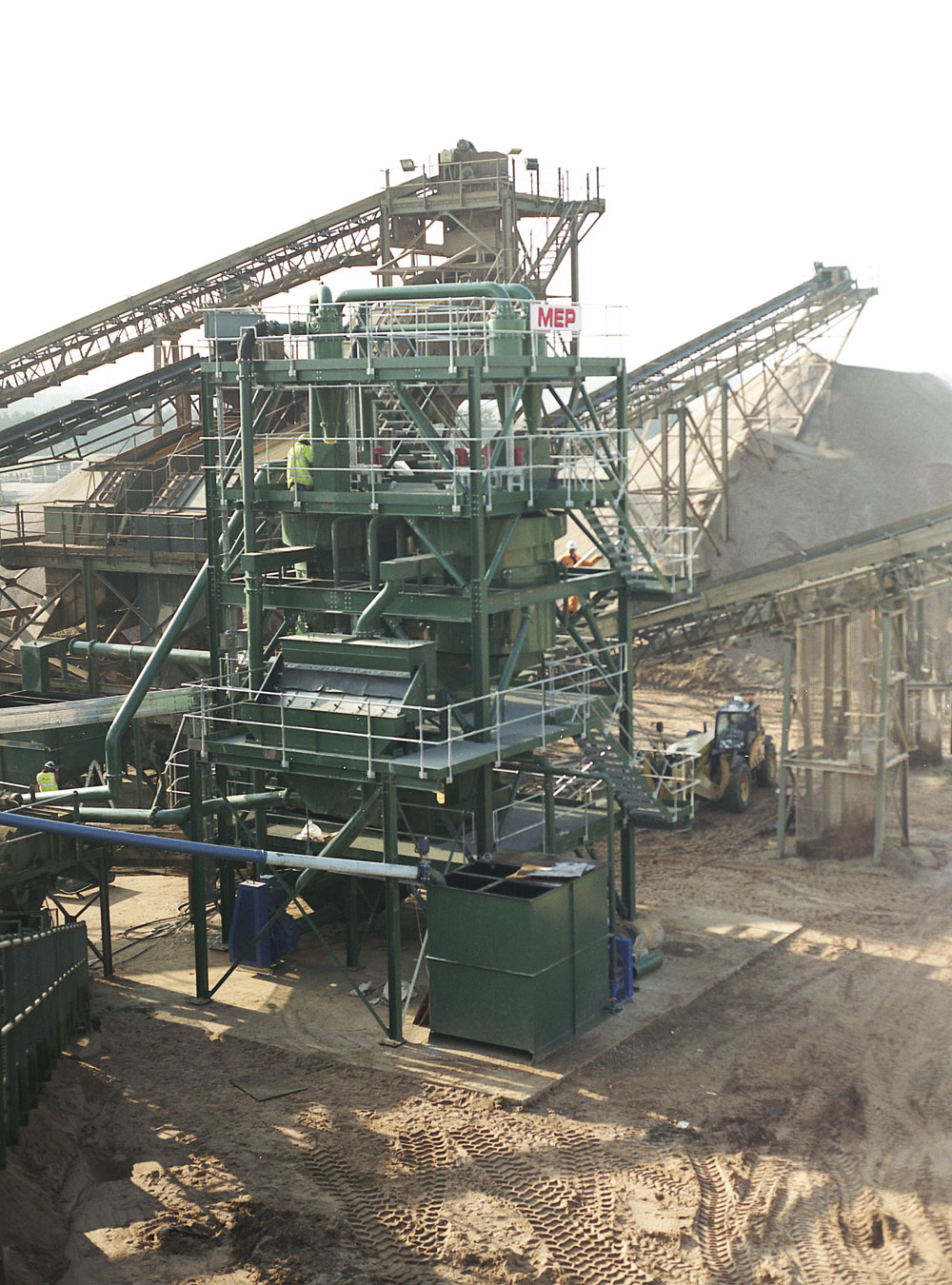
A look at the use of computerized systems in silica sand processing
In recent times one of the main developments in silica sand processing, as in many other industrial processes, has been the use of computerized systems to control and record the performance of production circuits. Computerized controls provide integrated and centralized facilities that can be housed in a suitable environment, which reduces the fatigue element for operators.
Controlling sump levels has long been recognized as an important factor in maintaining pump performance stability – by using level controls and automatic valves to control the flow of ‘make-up’ water, and variable-speed pumps, the operator can substantially reduce the swings and variations of product gradings.
With a suitable ADSL connection the system can be interrogated by a specialist technician from a remote location, thus speeding up any fault resolutions etc, and in turn saving time and money.
The use of more sophisticated and accurate separating devices such as a hindered-settling classifier (eg the TBS Hydrosizer) allows the operator to maintain a constant size of classification of the product almost regardless of feed rates. It also offers the possibility of producing higher-quality products by identifying the deficient elements of a feed material and re-blending to achieve the required product grading.
Sand production has often been an art form where the ingenuity of the operator has been relied upon to allow producers of specialist products to maintain their markets, but now the consequential liabilities are such that the element of risk needs to be eliminated as far as possible.
Sand deposits that do not readily fall into the required specification, such as the Bunter sands and glacial deposits where the silt contents vary widely and where there are deficiencies in the gradings, can be successfully treated.
Contamination, such as lignite, is often present in river terrace deposits, particularly in the Trent valley where it is necessary, due to dwindling reserves, to excavate deposits that were previously rejected. Other raw materials, such as sea-dredged aggregate, can contain coal, coke, wood, roots, fish and seashells, which also cause problems and need to be removed.
None of the above problems can be resolved using cyclones and screens or other similar types of equipment, nor can they be solved using log-washers.
Traditionally, the removal of lignite etc down to 1mm size has been acceptable but now the demand is for cleaner material, eg down to 0.1mm. These problems can be solved by using two stages of the TBS Hydrosizer, which will separate and remove the low-density (eg <1.8 s.g.) materials from silica sand. It can treat material up to 6mm size or even 8mm in size and it can accurately classify at any size up to approx 0.7mm (classifications at greater than 0.7mm are carried out more efficiently by vibrating screens, whereas classifications lower than 0.7mm are more efficiently carried out using a TBS Hydrosizer).
Also available is the Hydrolig, which is a hybrid version of the TBS Hydrosizer. This machine has been adapted to treat and remove contamination from –40mm gravel. It is ideally suited to work in tandem with the TBS Hydrosizer to remove contaminates from gravel and sand products less than 40mm in size. This would involve three stages of treatment.
The demand for more accurately classified sand, eg for sports surfaces, has increased and this again calls for more sophisticated equipment with two stages of treatment, separating at, for example, 0.6mm in the first stage and efficiently removing the fines (<0.1mm) in the second stage.
Obviously, for overall commercial reasons, the producer will need to find markets for all of the products, including the discarded elements made during the production of the premium products.
The Health and Safety Executive has set ‘hard targets’ for the quarrying industry in general, and this includes sand processing plants. It has resulted in the design needing to include additional features to reduce accidents. Clear and adequately sized walkways, stairways instead of ladders, secondary egress, no head-high obstructions and safe working areas for maintenance are some of the points that need careful design. Any plant that compromises on the design to save space or to provide mobility will inevitably have a negative effect on the performance, efficiency and safety aspects.
Health and safety issues are having an increasing affect on the design/build of processing plants and there has been rash of new and revised standards. The principal requirement for the design of plant in Europe is to meet the ‘Essential Health and Safety Requirements’ of the revised Machinery directive 2006/42/EC.
Since the start of 2010, new machinery has had to comply with the latest standards. It is also worth noting that new plants that include assemblies of older machinery have to comply with the new Directive.
A risk assessment is essential and it needs to address the items in the ‘Essential Health and Safely Requirements’, as well as hazards identified in EN ISO 14121-1:2007.
MEP, who comply with the latest standards for health and safety in the design and construction of their plants, say plant purchasers have to recognize their legal responsibility under the ‘Provision and Use of Work Equipment Regulations 1998’ (PUWER Regulations) and accept that these provisions will increase the capital cost of plants, whether mobile or fixed.
For further information visit: www.ukmep.com