New Drying Plant for Anglia Lime
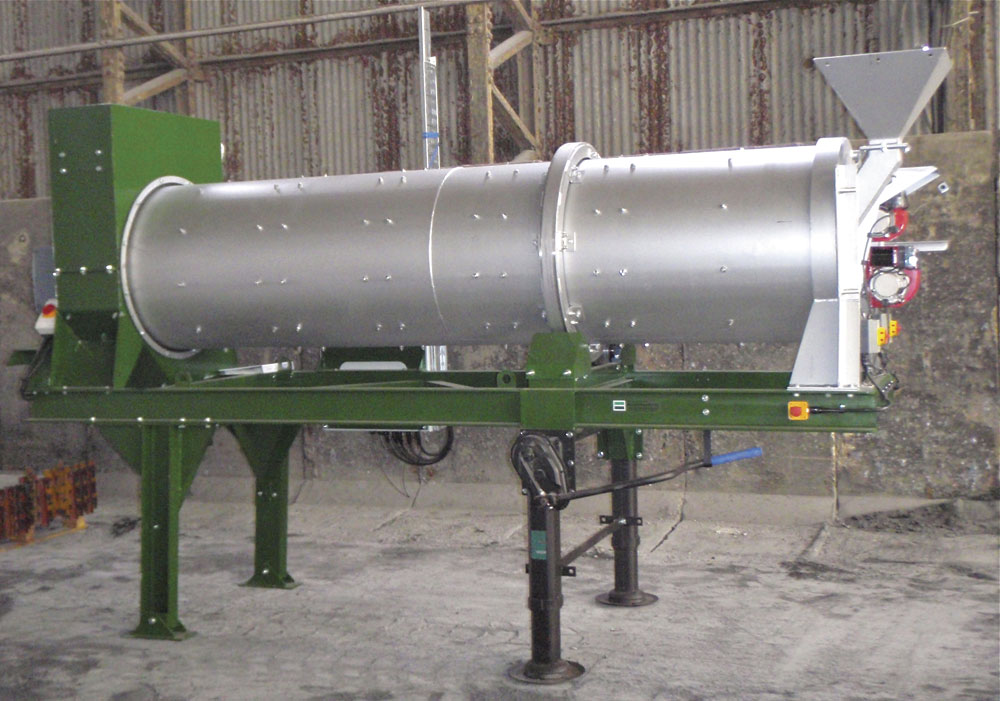
From their base in Sudbury, Suffolk, Anglia Lime Company have, since 1992, pioneered the use of lime in East Anglia through training courses and the distribution of lime materials. During this 20-year period the company has seen an increase in the awareness and use of lime in both restoring old buildings and developing new builds.
These circumstances have led to the development of lime-based products and systems that make the use of lime more efficient and convenient, while retaining all the beneficial properties of the material.
Combining abundant East Anglian local sands with hydraulic lime base binders, Anglia Lime Company offer sustainable lime-based solutions for plaster repairs, repointing brickwork, installing lime floors or even pre-coloured, spray-applied finishes for the most modern of buildings.
A growing market and increased demand has recently seen the company invest in a new drying plant, with the dryer and bag filter elements being supplied by BG Europa (UK) Ltd of Wickhambrook, Suffolk.
Drawing upon their long-standing experience within the low-temperature drying sector, BG Europa supplied an SD 0.8 parallel-flow dryer and an SFC pulse-jet bag house. This combination offers a low-capacity, versatile and cost-effective package for the drying of various sands, glass and mineral products.
Parallel-flow dryer
Nominally rated at two tonnes continuous feed per hour with 5% moisture removal, the dryer’s supporting base frame incorporates a hinged arrangement to allow the drum inclination to be adjusted between 0.5° and 3.0° to suit material specifications (factory set at 1.0°).
Manufactured by BG Europa from 6mm thick 50D boiler plate steel, the drum shell is finished with a coat of heat-resistant paint and fitted with a set of bolt-in replaceable flights manufactured from 5mm thick EN8 steel.
The dryer airplate incorporates an integral feed chute fitted with bolt-in replaceable liner plates. The hinged design of the airplate, which incorporates the burner mountings, allows easy access for servicing.
Completing the specification, a thermocouple is fitted within the discharge chute to measure the temperature of the dried material. Additionally, a second thermocouple is mounted in the base of the exhaust stack to measure the temperature of the dryer exhaust gases and provide alternative method of dryer temperature control.
Pulse-jet fabric filter
Well suited to low-temperature drying applications, the SFC pulse-jet filter incorporates an efficient cleaning mechanism which does not cool the incoming dryer exhaust gases.
All the dryer exhaust gases are filtered through the SFC 20 compact pulse-jet fabric filter unit, which features 20 factory-installed Nomex type (500mg/m2) filter bags to give a total cloth area of 9.0m2. A snap-ring collar secures the bags into the plenum plate to provide an airtight seal and an easy method of replacement.
With an electronic pulse controller allowing fine adjustment of the cleaning pulse duration and frequency to suit operating conditions, an inverter-controlled direct-drive filter exhaust fan installed on the clean-air side of the filter allows adjustment of the air flow within the dryer drum to suit the drying process.
Controls and commissioning
Mounted on the dryer base frame, a compact control panel contains the fan motor starter and inverter speed controls, drum drive motor starter and inverter speed control, temperature controller, over-temperature protection system, under-temperature alarm system, temperature displays, stop/start buttons and emergency-stop system.
Prior to delivery, the dryer and filter package was fully wired and tested within BG Europa’s workshop before being despatched to Anglia Lime.
Successfully installed in the allotted time frame, the new dryer and bag filter was fully commissioned by BG Europa engineers and then integrated with the plant’s feed controls and bagging system by the Anglia Lime team.
Anglia Lime director Philip Poels commented: ‘BG Europa’s delivery of the plant on schedule was not compromised thanks to their impressive flexibility of design in accommodating our specific requirements.’
Long-standing experience
BG Europa (UK) Ltd have provided specialist drying plants for many industries, including dryers for aggregates, sand, slag, minerals, glass and recovered aluminium. Dryer drums are designed specifically for each application in either a counter-flow or parallel-flow design, depending on the process requirements.
SD-series parallel-flow dryer drums are mated to SF-series pulse-jet fabric filters to provide efficient low-temperature drying at just above dew point. These drums are used extensively within the slag and sand-drying industries and, therefore, flight design and drum construction are aimed at providing long operational life given the highly abrasive nature of these materials.
A full turnkey package is available, including feed bins, conveyors, fabric filters, storage silos and all controls. Alternatively, a dryer can be incorporated within an existing production set-up to enhance production capacities and flexibility.
For further information visit: www.bgeuropa.co.uk