New Cone And A Smart Screen
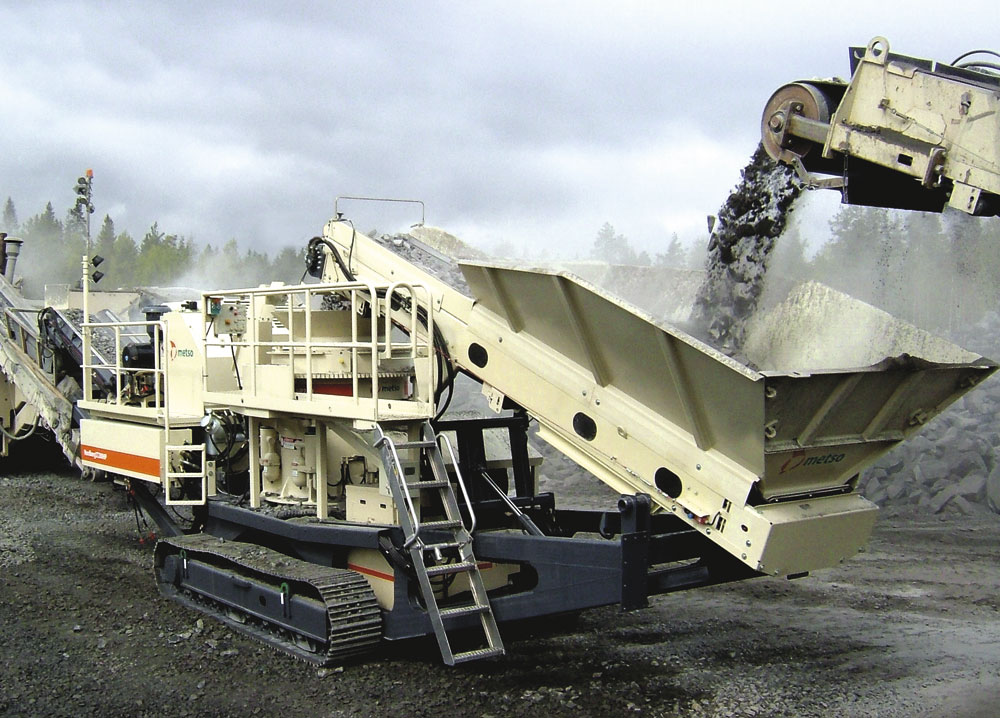
Metso Minerals mark 20 years of the Lokotrack concept with two product launches
In 1985 Metso Minerals became the first manufacturer in the world to commence serial production of mobile crushing and screening machines with the launch of their ground-breaking Lokotrack range. In the 20 years since then mobile crushing and screening has become the fastest-growing part of the company’s business, with worldwide sales amounting to some 2,500 mobile crushing units and over 4,000 mobile screening units.
Today Metso’s Lokotrack product line, which comprises 10 mobile crushing plants and nine mobile screens, encompasses a wide range of crushing and screening applications involving the production of single or multiple end products. Individual machines in the range are designed and engineered to work either in isolation or in tandem (in open or closed circuit) with other mobile crushing and screening units.
Coinciding with the twentieth anniversary of the Lokotrack concept, Metso Minerals have recently launched two new machines — the LT200HP track-mounted cone crusher and the ST352 tracked mobile screen featuring SmartScreen technology for increased efficiency and reliability, higher production and easier operation —both of which were unveiled in Januaryat an international launch event held in the UK.
Lokotrack LT200HP
Designed for secondary and tertiary crushing applications, the 30-tonne Lokotrack LT200HP is built around the tried and tested Nordberg HP200 cone crusher, over 650 of which are currently in operation around the world. With its large 210mm feed opening, the HP200 is capable of processing up to 275 tonnes/h.
On the LT200HP unit a 425hp (317kW) Cat C-12 diesel engine with hydraulic drive provides variable crusher speed, allowing the user to optimize production to suit specific liners and feed stocks. The machine is equipped with a 5.0m3 feed hopper, a 6m long x 1,000mm wide belt feeder and a 10m long x 800mm wide main product conveyor. A metal detector and crusher feed level sensor are also included as standard.
Another standard feature of the Lokotrack LT200HP is its interactive IC600 intelligent control system. Based on the proven technology of Metso’s IC300 and IC500 systems, this monitors and controls the entire crushing process to ensure continuous and stable material flow to the cone crusher at all times. The IC600’s simple but functional user interface displays all essential information and allows process parameters, such as crusher speed, to be optimized and adjusted. The system also offers built-in troubleshooting as well as single-button start/stop control of the crushing process.
The LT200HP is designed to integrate with other Lokotrack LT-series crushing units and ST-series mobile screens. For example, the unit’s feed hopper and discharge conveyor match with the LT105 primary crusher and the new ST352 mobile screen respectively. And with the IC600 system, the control systems of all three units can be interlocked together.
According to Metso Minerals, competitive studies have demonstrated that the LT200HP is up to 20% more productive than its nearest rivals and offers improved product quality.
Lokotrack ST352
Designed for fine screening and maximum output of multiple products in quarrying, construction and recycling applications, the new Lokotrack ST352 mobile screen features Metso Minerals’ advanced SmartScreen technology. The machine’s IC300 intelligent controller not only controls the start-up and shutdown processes, but also supervises and adjusts the unit automatically for optimum continuous screening results. By controlling the feed rate and screen performance, maximum screening efficiency is achieved. In addition, the IC300 monitors all key functions and components to help ensure longevity and reliability.
Powered by a 110hp (83kW) Deutz diesel engine, the Lokotrack ST352 is equipped with a 7.5m3 hopper and Metso Minerals’ proven 3.7m (12ft) x 1.5m (5ft) two-bearing screenbox featuring adjustable screen angles and end-to-end crowning. This is said to offer higher production (250–350 tonnes/h) and more efficient separation than other flat screens of comparable size. The machine is also available with a wheeled bogie and a direct-feed system for applications where the hopper and feed conveyors are not needed.
Metso say the ST352’s heavy-duty construction provides increased stability in difficult applications, while the unit’s remote and radio controls, which are fitted as standard, provide ease of movement around the job site. In addition, the machine’s modular design makes servicing quick and easy as well as allowing customers to select different conveyors, power packs etc to suit their own particular screening requirements. Weighing just over 25 tonnes, the machine is mounted on 400mm wide hydraulically driven tracks and equipped with hydraulically folding side conveyors for ease of transport.