Moving Mountains
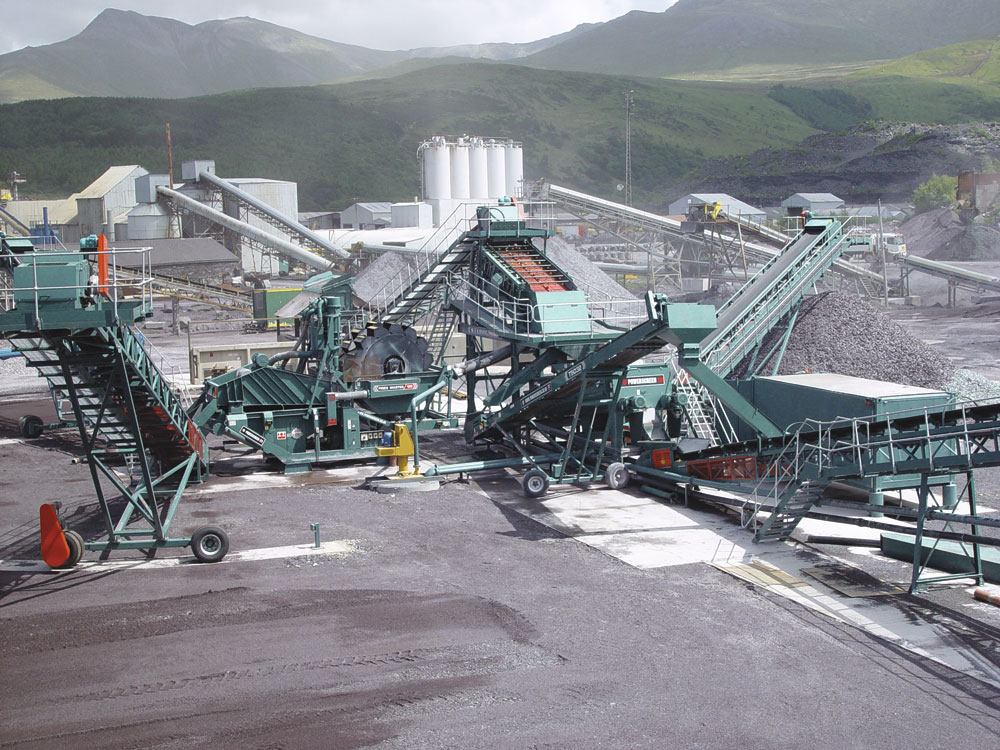
New washing plant boosts utilization of slate waste in North Wales
There are mountains of slate waste in North Wales. In fact, according to recent research, about 730 million tonnes of it. A considerable percentage of this belongs to Alfred McAlpine Slate Ltd (AMSL), who for the past 30 years have sold a small proportion to local markets for applications such as road building. But it was not until the introduction of the aggregates levy, from which slate is exempt, that it became economical to send the material further afield. Now, with the possibility of an increase in the tax on primary aggregates, the market for slate as a secondary aggregate looks set to continue to grow.
There are only three large-scale slate quarries currently active in North Wales, two near Blaenau Ffestiniog and the other at Bethesda. These produce mainly roofing slate as well as slate for work surfaces, paving, flooring, tiles and slabs. In total the three sites create nearly 6 million tonnes of slate waste each year, of which historically only around 275,000 tonnes was processed into secondary aggregate. The largest of the three quarries is Penrhyn at Bethesda, which is owned, together with one of those at Blaenau Ffestiniog, by AMSL, who produce by far the largest quantity of slate in North Wales and, as a consequence, the majority of the waste.
Since the introduction of the aggregates levy, and the exemption of slate, AMSL have doubled the amount of slate they crush to produce a range of products including Type 1 sub-base, drainage stone, fine aggregates to replace sand in concrete (slate has a high silica content), industrial minerals and granules used in the making of green roofing felt.
To reduce the current quantity of waste material and further increase their range of saleable products, AMSL decided to increase production by introducing a washing system into the production cycle, thereby providing more diverse products and greater product availability. A significant growth area recently has been the use of slate as a decorative aggregate in gardens, where it has found favour as a more resilient and colourful alternative to tree bark. Other complementary slate walling and paving products are also being produced and sold, via distributors, to garden centres and DIY shops.
Aggregate processing at Penrhyn
Processing of the slate is being carried out by McAlpine Asset Management (formerly known as AMPL) under a 10-year contract — their first in the UK for the recycling of slate. The plant itself, which was supplied and installed by Coventry-based Powerscreen Washing Systems (PSWS), eliminates the need for settlement lagoons due to the installation of a filter press that turns the whole operation into a closed-loop system.
PSWS supplied McAlpine with a system specifically designed to operate at 180 tonnes/h, this being governed to a large extent by the capacity of the silt-treatment plant, although the type of material being processed also has an effect on output. A wheel loader feeds the slate into a 30-tonne Powerscreen Commander 1400 that features variable speed control. This discharges on to an 80ft long static inclined conveyor fitted with a galvanized walkway along its full length and around the head drum. The conveyor is also equipped with a belt weigher to ensure accurate monitoring and control of production levels. From this conveyor material is fed on to a 16 x 5 twin-deck rinser equipped with a vibrating top deck fitted with polyurethane screen mats. Oversize material is fed directly to a radial stockpile conveyor to provide a 30mm finished product, while material passing the bottom deck is fed to a Powerscreen Fines Master 120 where it is classified and dewatered before being fed on to two separate radial stockpile conveyors to provide two grades of sand (building and concrete). All mid-size material passes from the rinser to a Powerscrub 120 log-washer that incorporates a by-pass facility. From here material is fed on to a 100ft static transfer conveyor, again fitted with a full-length galvanized walkway, which in turn delivers material to a 16 x 5 part rinser complete with two radial stockpile conveyors to provide 10mm and 20mm finished material.
The system is designed so that all fines from the log-washer and part rinser are recirculated back to the sand plant, while all water and silt from the Fines Master 120 is pumped, via the unit’s bottom feed, to the filter press.
In choosing the correct size of press for this application, PSWS had to consider such factors as the silt content of the raw material, settlement rates and throughput. Having explored all the available filter press options throughout Europe, PSWS specifically sourced a Tecnoidea multi-plate filter press (model 1300 x 1300) featuring 33 plates. This model was selected not only for its impressive technical specification, but also its build quality and technical support.
The silt-management system was also specifically designed and sized to minimize operator input and to maintain low running costs. As well as the press, the system includes: a foul-water pump with an automatic cooling system; an automatic flocculant mixing and dosing plant with a control system that minimizes the use of flocculant; an automatic anti-clog system; a 4m diameter deep-cone silt-thickener tank with pneumatic discharge valve; a silt buffer tank; a fresh-water tank; and all the associated support framework, walkways and access platforms. The entire system is fully automated and requires only occasional operator intervention to add flocculant powder and to remove the pressed silt cake using a loading shovel.
The flocculant mixing and dosing system has a continuous supply of clean water and automatically mixes a batch of flocculant solution when the level drops; the operator only has to add the flocculant powder to a storage bin. As the sludge is fed from the Powerscreen plant into the thickening tank its density is monitored every 50s. This allows the system to automatically adjust the feed rate of the flocculant solution, thereby guaranteeing clean water for recirculation and minimizing the amount of flocculant required.
Once in the thickener the silt settles to the bottom of the cone and is automatically discharged into the sludge tank when its density reaches 25% solids. This is constantly monitored to ensure that a consistent feed is pumped to the plate press. Once the press has finished draining the water from the silt, the plates open to allow the resulting silt cake to drop into a concrete bay underneath. The press then cleans itself ready for the next cycle.
Commenting on the new plant, which was commissioned in mid-July 2003, Paul Chambury, AMSL’s operations director, said: ‘It’s doing everything we wanted it to do and it’s to a high specification. We had strong co-operation between AMPL and Powerscreen Washing Systems all the way through the project.’