Metso Impact Crusher for CEMEX Limestone Quarry
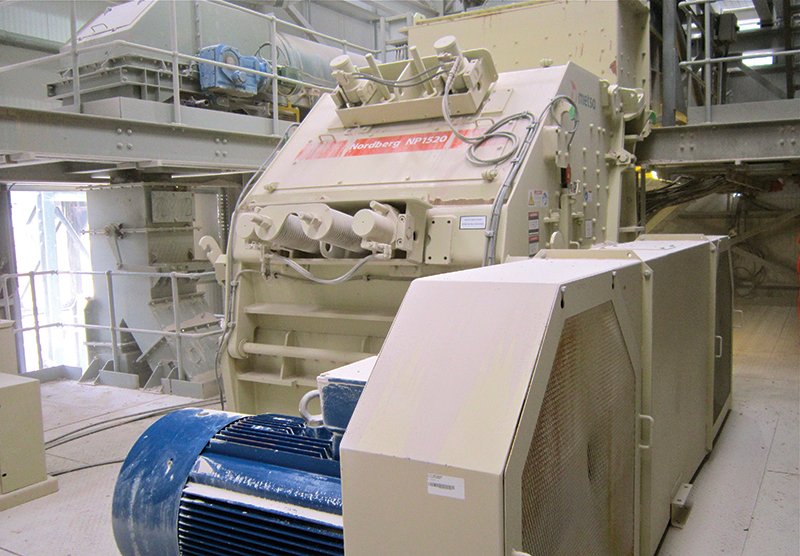
First published in the September 2015 issue of Quarry Management as ‘The Beast of Buxton’
Roltech Engineering deliver turnkey project to boost production at Dove Holes Quarry
Some call it ‘Oliver’; others call it BOB the ‘Beast of Buxton’. But to its creators, it is a Metso NP1520 impact crusher and it is boosting production at one of the UK’s most important limestone quarries.
CEMEX’s Dove Holes Quarry, near the Derbyshire Peak District town of Buxton, supplies up to 25% of the company’s UK aggregate requirement. With the rapid recovery in UK construction activity post-recession, demand for concrete, asphalt and aggregate has increased significantly.
Two years ago, in order to meet this surge in demand, CEMEX looked to increase production and charged their management team at Dove Holes with the task of identifying any features of the production process that might prevent the achievement of the increased output.
In 2014, the quarry management team compiled a list of plant and equipment that it thought would require enhancement. Top of the list was a new crusher, as production levels hinged upon the ability of the crushing and screening plant to process increased volumes within normal timescales.
In particular, the secondary crushing capability was identified as a critical area for upgrading. The hunt was on for a suitable machine and quarry manager Steve Leigh soon found the solution in the form of a Metso NP1520 impact crusher, which has a nominal capacity rating of 500 tonnes/h producing –40mm aggregate, with sufficient reserve power to process up to 650 tonnes/h safely and consistently.
Before making a final decision, Mr Leigh and his team visited another NP1520 which had been working at a quarry in a neighbouring county for the past seven years and were satisfied in their decision to choose this machine by the enthusiastic endorsement of the crusher by the management and staff of that quarry.
Having chosen the crusher, CEMEX then had to find a contractor capable of undertaking the installation at Dove Holes Quarry – highly specialized work that limited the choice of contractor to just a handful of firms.
The job was far from straightforward. CEMEX wanted a turnkey solution so they needed a company which not only had a track record in quarry plant installations, but also had proven design and project-management skills as well as general construction and civil engineering capabilities.
The search led to Roltech Engineering, headquartered in Newcastle-under-Lyme. Located only a few miles from Buxton, Roltech are a well-known name with many years of experience within the quarrying sector.
The main challenge for Roltech was to install and commission the new plant as quickly as possible in order to avoid interruptions to production. ‘We had to install the new crusher within the existing discharge area, which meant we had a shutdown period during which the old crusher was removed and the new one installed,’ explained Howard Austin, managing director of Roltech Engineering.
Production during this shutdown was transferred to a mobile crushing plant hired in for the purpose; therefore it was critical that the installation programme for the new crusher was as short as possible so as to minimize the hire costs.
The new Metso machine was significantly larger than the existing 40-year-old Sheepbridge machine, which, in the words of Howard Austin, had ‘outstayed its welcome’.
‘Space was an issue,’ he admitted. ‘The task required our company to not only dismantle and remove the old crusher, but also the building that housed it.’
The team at Dove Holes was adamant that the new machine should not be simply shoe-horned in to replace the existing crusher, but that the project should include the installation of a full-width feeder to optimize plant performance and even-out wear areas within the crushing equipment.
The project also required that the new crusher building should provide sufficient space to accommodate essential lifting equipment and provide a safe working environment for the maintenance staff. Roltech’s response to this requirement differed significantly from that of the other firms bidding for the £700,000 contract.
‘We were one of three contractors who bid for the job but we were confident that ours was the best design,’ said Mr Austin. ‘We fitted it into the existing line whereas the other contractors suggested taking it out of the existing line in order to gain more space. We could have chosen that option but we knew that it would exceed the budget. We made the decision to fit the new plant in-line without compromising the specification or exceeding the budget.’
After dismantling and removing the existing crusher and crusher building, Roltech Engineering worked in conjunction with Metso to design new concrete foundations to support the replacement crusher. The company was also responsible for the design and installation of new steelwork to support the crusher and its ancillary equipment, such as the feed conveyor and discharge conveyors.
Within the role of project manager, Roltech also undertook the design and installation of the new three-storey steel-framed building, including stairways, access walkways and overhead lifting equipment. The new building is 15m in length, 8m wide and 15m high, and is clad in profiled sheeting to meet with local requirements.
Work started on site at the beginning of November 2014 and was completed by the end of February this year. ‘As you can imagine, the weather high up in the Peak District, was pretty bad and some days it barely got light,’ said Mr Austin. ‘However, despite that, the project was completed within the tight programme.’
The new Metso crusher is now fully operational, reducing 200mm material from the primary crusher down to –30mm or –40mm, and helping to produce up to 20,000 tonnes of material every day compared with the 12,000 tonnes per day its predecessor could produce.
Roltech Engineering can now add this project to a list of successful recent installations for CEMEX. Back in 2013 the company carried out a complex job worth £400,000 to convert an existing asphalt coating plant at Dove Holes into a dry-products batching facility to produce shotcrete mortar for the Crossrail project.
So what about the new crusher’s nicknames – where did they come from? ‘I call it the Beast of Buxton because it’s such a powerful machine,’ said Howard Austin. ‘But the people at Dove Holes have nicknamed it ‘Oliver’ – because it’s always asking for more!’
- Subscribe to Quarry Management, the monthly journal for the mineral products industry, to read articles before they appear on Agg-Net.com