Metso Cone Crusher Delivers Results for Brazilian Quarry
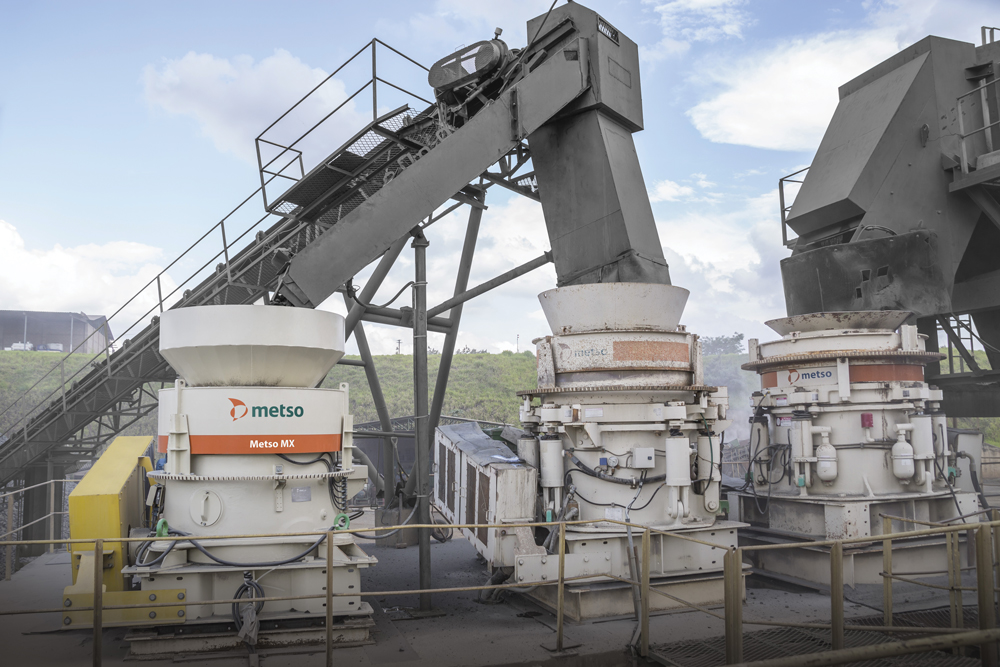
First published in the September 2017 issue of Quarry Management as Tertiary Triumph
New Metso MX4 cone crusher delivers 20% increase in productivity and more uptime for Minermix
A Minermix quarry located in the Brazilian state of São Paulo has been using Metso’s latest crushing technology since January 2016, as a result of which the life of the crusher linings is at least 30% longer, according to the company.
Boosting recrushing and improving quality
The Minermix Mineração unit, in the city of Capivari, is the newest of the three quarries owned and operated by Brazil’s Extrabase group. For the past seven years, the facility has had a nominal production capacity of 200,000 tonnes per month, employing a processing plant that is equipped for three-stage crushing – primary, secondary and tertiary. But with just a single stockpile – unlike the company’s other quarries, which have two stockpiles each – the tertiary-stage crushing operation at the Capivari facility was in need of a boost.
At the same time, Minermix wanted to reduce the presence of fine dust-like material in the production of manufactured sand. This product is directed primarily to concrete plants and the presence of excessive quantities of rock dust (fines) is a problem. Minermix also wanted to ensure the highest possible degree of standardization of this material, which, given the need to continually adjust the comminution equipment used, was a constant challenge. The operation could, in the company’s assessment, be more productive and require fewer adjustments by the equipment operator.
Twenty per cent increase in productivity
The Minermix crushing plant in Capivari is fed with basalt extracted from a site located approximately 1km from the facility. The primary crushing phase utilizes a Metso Nordberg C125 jaw crusher, followed by secondary crushing with a Nordberg HP400 cone crusher. All the material requiring further processing is crushed in two parallel tertiary crushing stages. Until January 2016, this job was performed by two HP4 cone crushers that had been in place since the quarry began operations in 2010. Today, a new Metso MX4 Multi-Action cone crusher works alongside one of the original HP4 crushers. The number 4 stands for the power rating – ie 400hp.
According to Minermix Mineração supervisor José Nilson, the MX4 cone crusher was installed with full support from Metso (including training of the operator), and, since its start-up, has demonstrated a 20% increase in productivity. In Mr Nilson’s assessment, the gain in productivity may even be as high as 30% with supplementary adjustments.
The supervisor credits this improvement mainly to the fact that the equipment allows adjustments to be made while operating at full load capacity – in other words, without the need to shut down the equipment and during its use at maximum power. ‘The equipment reaches 95% and, when it reaches peak production, the equipment itself makes the adjustments to balance production,’ said Mr Nilson. The stability of production has also allowed for a 5–10% reduction in the production of rock dust, an unwanted by-product in the production of manufactured sand used by concrete plants. ‘It may not seem like much, but the reduction has a notable bearing and impact on daily production,’ explained Mr Nilson.
More uptime with patented Multi-Action technology
The MX4 is based on Metso’s patented Multi-Action crushing technology that combines the piston and rotating bowl into a single crusher. Thanks to the way it has been designed, the crusher provides the maximum utilization of the wear parts leading to extended maintenance intervals.
‘The MX4 works throughout the day, self-adjusting the crusher opening/setting or power to our specifications,’ added
Mr Nilson. This kind of dynamic adjustment underload means more uptime, as it is carried out while crushing. An audible alarm informs the operator that the temperature and pressure conditions, oil level etc, are in conformity with previously established parameters.
Mr Nilson notes that the MX4’s automation is another feature that has improved the operation overall. ‘The operator turns on the equipment with a single touch of the crusher automation screen, which also allows the crusher operation to be monitored throughout the day and gives us a final report when the equipment is turned off.’
On a weekly basis, the MX4 crusher is calibrated by initiating an automated procedure that takes five minutes at most. Calibration determines the degree of wear in te wear parts and adjusts the settings based on those findings. This assessment also allows the correction of any parameter that is not aligned with what has been pre-established by Minermix. The replacement of wear parts is performed after around 1,200h of operation, which is more than one-third longer than before, whilst the lifetime of the crusher’s linings is at least 30% greater, according to the company.
About Extrabase
Established in 1984, Extrabase are members of the Base Group (Grupo Base) focusing on civil construction. Specialized in the extraction, sale and distribution of crushed stone, gravel and sand, Extrabase have 12 operating units in the state of São Paulo, Brazil. Strategically located, the company’s quarries ensure the supply of construction aggregates to the regions of Sorocaba, Piracicaba, Campinas and Porto Feliz, which are among the most affluent in Brazil’s wealthiest state.
The company’s own fleet of transport vehicles ensures a logistics system capable of serving customers within a radius of approximately 30km from the respective cities covered. As well as investing in the continuing development of their production processes, Extrabase also remain alert to environmental issues and seek ever-more efficient means to lessen the impact on nature, engaging in conservation, re-utilization of natural resources and reforestation as their main environmentally focused actions.
Patented Multi-Action crushing technology
Metso say the launch of their new Metso MX cone crusher represents the introduction of revolutionary and industry-changing rock-crushing technology.
Based on the company’s patented Multi-Action crushing technology, which combines the piston and rotating bowl into a single crusher, the new machine is said to provide a giant leap in profitability, cutting operational costs by 10% and delivering 10% more uptime compared with traditional cone crushers.
Jouni Mahonen, vice-president of global sales and product support at Metso, explained: ‘Aggregate producers are facing increasing pressure on efficiency and cost management. In order to meet these demands, we rethought the crushing basics and combined our long experience in different cone crusher technologies with our extensive engineering knowledge. Two individual crushing methods based on the piston and rotating bowl were conjoined, and, as a result, we created the MX cone with Multi-Action technology.’
Designed for particularly demanding rock conditions and with a special focus on automated adjustment features, the robust Metso MX is said to deliver extremely cost-effective and safe operations, providing a very high reduction ratio with premium end-product shape and consistency.
A key benefit of the Metso-patented Multi-Action technology is the ease of setting adjustment and wear compensation under load, without having to stop the process. This can be now combined with extended wear life and better mechanical protection.
Optimal cavity design, stroke direction and effectively distributed crushing action are said to result in the optimum rock-on-rock crushing motion. This combined with the innovative Multi-Action technology results in extended maintenance intervals and higher production.
According to Metso, the new Metso MX also provides maximized tramp release distance with high protection against uncrushable objects and overloading. Moreover, the crusher can utilize up to 70% of the mass of new wear parts – a record-breaking utilization rate – and thanks to the intelligent crusher design, the quality characteristics of all sized end-product fractions remain consistent throughout the lifetime of these wear parts.
Jouni Mahonen concluded: ‘After 10,000h of rigorous testing, we are proud to say the Metso MX meets our targets for increased profitability by allowing 24/7 crushing with minimum downtime.’
- Subscribe to Quarry Management, the monthly journal for the mineral products industry, to read articles before they appear on Agg-Net.com