Manufacturing Sand
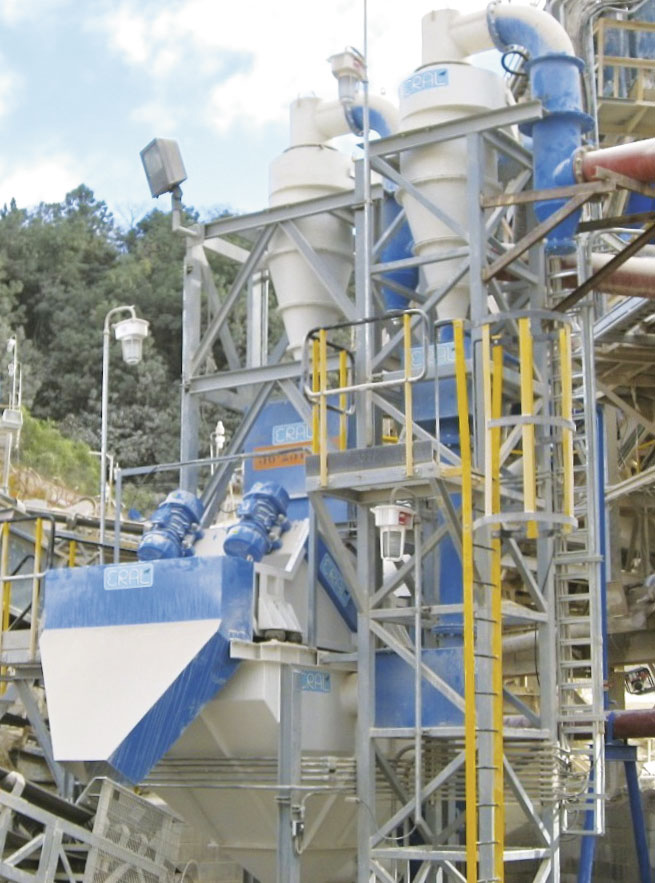
Manufactured sand is frowned upon by some quarry operators because of its variable grade and quality. However, by choosing the right equipment, consistent manufactured sand can be produced, as Steve Mellor explains
Worldwide, natural sand resources are being depleted because of exhaustion or sterilization of reserves, extraction or transportation cost, or environmental restrictions. Conversely, material requirements are becoming increasingly stringent and specifications tighter, with demands for consistency and high quality being prerequisites. This has led to a rethink in the use of manufactured sands.
Manufactured sand ranges from unprocessed quarry dust to carefully processed fine aggregate specifically designed for use in concrete. It may be gritty, flaky and full of filler or well shaped and graded, assisted, perhaps, by the nature of the parent rock, to produce well proportioned particles in the right size range.
To some, manufactured sand has a reputation for poor quality, but this is undeserved if the correct equipment is selected. Properly manufactured sand have the edge over naturally occurring material in terms of consistency, as many sand pit products are notoriously variable, leading many concrete producers to increase cement content to compensate for these variances.
The major problems in using crusher dust as concrete sand include particle size distribution and shape. Concrete producers need a specific, consistent gradation in their sand that is not typically satisfied by the fines produced in the traditional crushing process (coarse particles are abundant but there is a shortage of material in the crucial 150 micron to 1mm range, and an excess of filler).
To be of use as a concrete sand, crushed rock has to look, feel and behave like concrete sand, which means controlling the filler content and the particle shape (cubical with ‘rounded’ corners for minimal surface area).
Plant and equipment options
With abrasive feed stock, compression crushers – jaws, cones and rolls – are well suited to the production of coarse aggregates, but inferior when producing sand-like particles, producing flaky or elongated grains, angular and sharp-edged, leading to increased surface area, increased voids ratio and reduced workability in end use.
With less-abrasive materials, horizontal-shaft impactors (HSIs) are cost-effective as they can take a large feed size and yield high reduction ratios. Product shape is good and fines production is high, sometimes too high with excess filler (which has to be removed for use in high-quality concrete). The shape of the sand particles is good and will remain consistent throughout the life of the wear parts but production may drop as wear increases. The HSI’s drawback in fines production is with highly abrasive materials, such as quartzite and flint, as operational costs escalate and downtime for wear parts replacement increases.
Traditional autogenous vertical-shaft impact (VSI) crushers tend to produce better particle shape, with rounded edges, at the expense of additional filler generation. The VSI can produce high tonnages of fine material and at a consistent grade irrespective of wear, albeit with an upper limit on feed size, depending on feed type and duty. Where HSIs compete
well on less-abrasive materials, once wear parts are worn down efficiency is lost and gradings can fluctuate, losing the consistency required. Normally, the requirement for fines is from the more difficult and abrasive materials, so the VSI is the better choice. It is the only machine to produce the correct product throughout the wear life of parts, as grading and consistency are unaffected by wear in rock-on-rock machines.
Conventional VSI crushers have difficulties in producing particles below 1mm in sufficient quantities to make well-graded sand, often including surplus filler, and crusher dust is therefore usually regarded as only suitable for incorporation in a blend with natural sand, if it is of reasonable quality and low cost. This solves the problem of waste material disposal but yields a low-grade ‘manufactured sand’.
Simple, inexpensive system
Using surplus dry crushed rock as feed, Ore Sizer and ERAL have developed a simple, inexpensive system to produce a sand conforming to international specifications for concrete sand, with superior particle shape throughout the size range, controlled filler content and an ability to maintain consistency despite variations in feed (fig. 1). Other requirements were that the process should be automated, environmentally acceptable, have a minimal plant footprint and require little maintenance.
The first step was to incorporate a crusher able to produce sufficient quantities of the deficient particle size mentioned earlier. Ore Sizer are specialists in multi-port rotor technology for autogenous VSI crushers and have available rotors of a low head design, with three to eight ports, to suit specific applications and duties. The combination of carefully engineered rotor geometry, to provide a short grinding arm, and restricted rotor outlet allows multi-port rotors to achieve the reduction required (in excess of 3:1 being possible) without the need to run at high speeds, at which they generate excess unwanted filler. The benefit of a five-port rotor over a three-port rotor, using identical feed and crusher rev/min, is clearly shown in figure 2.
In a conventional autogenous VSI, the energy transfer necessary to break already small particles is difficult to attain, and increasing the particles’ speed and kinetic energy has little effect beyond creating unwanted powder. This process improves particle shape by breaking off or abrading protuberances, but does not provide significant size reduction. The design of the Ore Sizer crushing chamber ensures that all particles are subject to multiple impacts before they escape as product, thereby overcoming this problem.
The second stage in the design was to use equipment that could select the desired product while removing unwanted filler. The inclusion of an ERAL compact plant (hydrocyclone, dewatering screen, sump and slurry pump) addresses this, with the components sized to optimize the desired product fraction. This is not a ‘one size fits all’ approach; careful component selection and sizing is necessary for each application. This equipment design is specific in terms of the material removed and can be adjusted to give an accurate cut point. It is also economical in the water use, and after-treatment of effluent is minimal. This allows the Ore Sizer/ERAL system to produce the necessary amount of 150 micron to 1mm grains for an ideal particle size distribution. The surface moisture on the recirculating oversize also complements the internal airflow system within the Ore Sizer to prevent dust emissions and avoid the inclusion of a costly, complex bag filter.
The inclusion of such a circuit, either as part of a new plant design or as a satellite operation on an existing plant, will provide a first-class manufactured sand that can be marketed as a premium product at economical production cost.
For more information visit: www.oresizer.com; www.eralgroup.com; or email: steve@crushing-asphalt.com
This article first appeared in Quarry, the official journal of the Institute of Quarrying Australia, and is reproduced here by kind permission.