Making An Impact
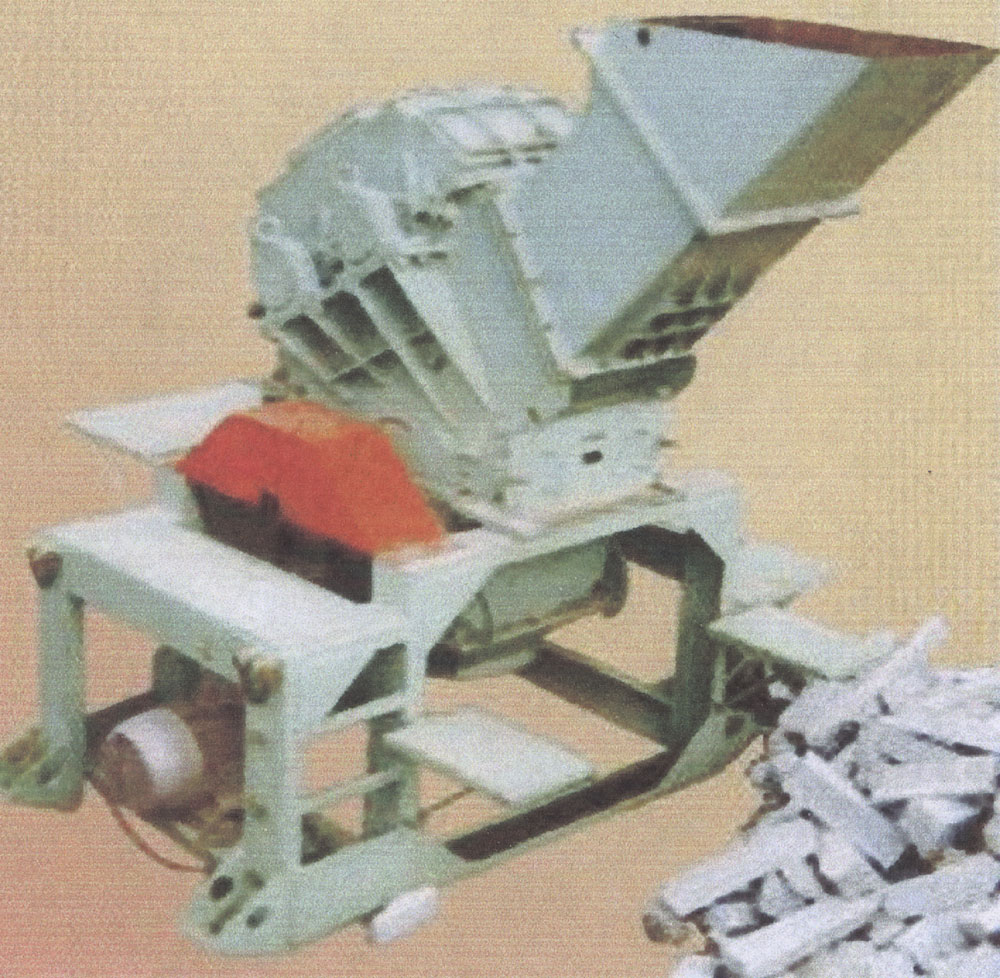
DAU technology — a new force in active impact crushing
The following article is based on information supplied by Steve Mellor, general manager of Chemex Pte Ltd of Singapore, authorized distributors of Russian-built DAU crushers
While it is true to say that modern technology has been able to improve the operational capabilities of crushing equipment, few new crushing technologies have been introduced in recent years. Of those that have, most have never progressed beyond the development and/or theoretical stage, but the improvements that have taken place have undoubtedly improved the performance, ease of operation and quality of the product, although almost all have been based on adaptations of existing designs rather than on the technology of the crushing action itself.
One exception to this has been the development of the active impact crusher (AIC) — led by Evarest Komarovsky, initially for Russia’s mining industry and subsequently for aggregate production to supply the construction industries — which is expected to be of great benefit to the mining and quarrying industries worldwide.
The AIC concept dates from the early 1980s when the then USSR Ministry of Geology had a requirement for crushers to process ore samples. More than 120 AICs were manufactured at this time and worked successfully on gold-bearing deposits. These small crushers, designated DAU-250, offered a relatively low throughput capacity (up to 2 tonnes/h) but demonstrated very high reduction ratios combined with low power requirements and economical use of wear parts.
Following analysis of the performance of these low-capacity machines, an extensive research and development programme was instigated in order to develop the AIC technology into an even more efficient crushing machine with a more usable throughput capacity. As a result of this programme, a prototype version of the DAU-500 was produced in the early 1990s (fig. 1). This model accepted feed material up to 350mm in size and was able to reduce it to 100% –5mm (or less) in one pass at a feed rate of up to 35 tonnes/h, using a 37kW motor for hard rock or a 30kW motor for soft and medium-hardness rocks.
About 20 DAU-500 units were subjected to extensive field trials before full production was launched. These were installed for the processing of such materials as gold-bearing and other metalliferous ores, sylvite and marble, as well as for the crushing of porphyry and granites for use in road construction.
In these and other tests the AIC technique demonstrated the ability to economically and effectively crush rock of virtually any hardness, as well as various slag materials, ferro-alloys, quartz, galena, clinker phosphates, and waste or reclaimed concrete, ceramics and bricks.
Subsequent to the above developments, the research and manufacturing company Daukom Co. Ltd was founded in 1995 by Evarest Komarovsky with the aim of developing these new methods, techniques and machines for the crushing of rocks and ores. The leading projects of the then Mining Institute served as the technological base for Daukom and many of its top specialists in the crushing and milling of rocks and ores were employed by the company. For manufacturing purposes, Daukom also established contact with leading production facilities in St. Petersburg.
The potential of AIC machines was obvious, and the need for increased capacity led to the development of a larger version. Thus, in 1999 the first DAU-800 (fig. 2) was produced, which was able to accept feed material up to 500mm in size at a rate of up to 105 tonnes/h, using a 75kW motor (see table 1). More recently, the DAU-500K model has been developed and built, expanding the AIC’s capabilities in the crushing of hard materials, while obtaining even more ‘fine’ product, if required.
Today, specialists with the company are developing even more effective crushers that can produce an end product of less than 0.04mm. Extensive research is also being conducted to improve still further the special alloys used in the manufacturing process, and a 300 tonnes/h version of the AIC is currently being developed.
The technology
The AIC technology employed in the range of DAU crushing and milling equipment has been patented in Russia, the US, the European Union, Japan, Korea and Australia, with patents applied for elsewhere. Figure 3 illustrates the major components of the AIC.
Active impact crushing makes maximum use of the kinetic energy of the crushed mass and impact elements to considerably increase the efficiency of the crushing process compared with traditional crushing methods. It has long been established that impact crushing gives the greatest intensity of comminution, but disadvantages have hitherto been the high operational costs in terms of either power or wear parts, or both. Furthermore, single impact crushers (both horizontal-shaft and vertical-shaft types) tend to be chaotic in their action, resulting in a lack of precise size control.
All crushing and milling equipment manufactured by Daukom is designed to offer medium-to-fine crushing and harsh milling in just one operating stage with low power consumption. Therefore, a single DAU crusher can replace two or three conventional crushing and milling stages, as well as any intermediate ancillary facilities, thereby greatly reducing capital expenditure and operational costs.
The AIC utilizes three synchronized rotors to generate enormous kinetic energy and inertia. These interact with the feed material to strictly control the crushing regime, the intensity of the forces applied being controlled by the speed of rotation. The crushing (milling) process and the principle of the DAU method are illustrated figures 4.1 to 4.4, where the kinetics of the serial interaction of the working elements of the crusher and rock material are shown.
In extensive field trials and numerous severe applications across Russia, it has been clearly demonstrated that the control over the finished product size is very high and not at all chaotic, with increased fines always following reduction in top size. This is of particular importance for certain market sectors where undersize material is regarded as waste. The photographs shown in figures 5.1 to 6.2 show ‘before’ and ‘after’ images of materials that have passed through the DAU crusher.
DAU crushers operate at a nominal speed of 1,000 rev/min, at which the most intense disintegration takes place. However, the 1,000 rev/min mode is not the only speed possible. The operational speed can be decreased to as low as 25% of the nominal speed. This lower rev/min mode is well suited to the production of aggregates with high cubicity for use in asphalt and concrete.
Typical results obtained from active impact crushers, with a 100–250mm feed processed in one pass, are as follows:
- marble: 84% –5mm at 100% of nominal speed
- clinker phosphate: 100%–3mm at 70% of nominal speed
- metallurgical slag: 93% –5mm at 100% of nominal speed
- quartz: 89% –5mm and 70%–1.25mm at 100% of nominal speed
- gold sulphide ore: 97% –1.25mm at 100% of nominal speed.
While crushing quartzite comprising 97–99% SiO2 with a feed size of 40–70mm, the following results were obtained (see table 2). The capacity achieved was 20–22 tonnes/h.
The results for cubical roadstone with rev/min lower than nominal speed and a 40–250mm granite feed stock processed in one pass are as follows:
- 100% –20mm and 89% –5mm at 80% of nominal speed
- 95% –20mm and 55% –5mm at 50% of nominal speed
- 93% –20mm and 37% –5mm at 37% nominal speed
- 80% –20mm and 30% –5mm at 27% of nominal speed
- 100% –40mm, 52% –20mm and 16% –5mm at 27% of nominal speed (with grids spaced back).
The operational speed, the size of the grids and their distance from the primary rotor are selected according to product requirements. Rapid adjustments to the settings can be made to suit various applications, thereby further contributing towards the versatility of the machine.
Furthermore, the AIC is able to process material with up to 12% moisture content. Indeed, some inherent moisture is helpful in reducing dust emissions (for very fine crushing operations some form of dust control system is recommended, drawing off from the integral dust spigot on the crusher body).
Although the crusher is of heavy-duty construction, it is of a relatively small overall size and weight, and well balanced, so that virtually no foundations are required to support the integral skid frame, further adding to the cost benefits of the DAU–ACI concept.
The bodies of the crushers are manufactured from very-high-quality steel and accurate machining ensures that all components are correctly aligned and located. Armour plates protect the inner walls of the crushers from the abrasive wear, and the rotors come equipped with shockproof and wear-resistant replaceable elements. The crusher is supplied complete with motor and drive, synchronizing assembly, access platform and feed hopper.
The main advantages of active impact crushers can be summarized as follows:
- high reduction ratio — up to 100:1
- production of desired product size with a single crushing stage
- reduced capital expenditure– one DAU crusher can replace two or three conventional crushers
- minimal power consumption– 0.002–0.2kWh/tonne
- cubical product with excellent surface texture
- low operating costs
- ability to process material containing up to 12% moisture
- no foundations required
- ease of maintenance and replacement of wear parts
- variable speed, grid size and grid position, making the crusher very effective in achieving optimum results.
The AIC is said to offer — for the first time — a method of impact crushing that can be described as fully controllable. Having been well proven in numerous arduous applications across Russia, the concept is now being launched throughout the rest of the world.
For further information contact Steve Mellor at: Chemex Pte Ltd, 8 Tuas View Loop, Singapore 637674; tel: +65 9670 7850; fax: +65 6873 3216; email: stevemellor@pacific.net.sg