Leaving No Stone Unturned
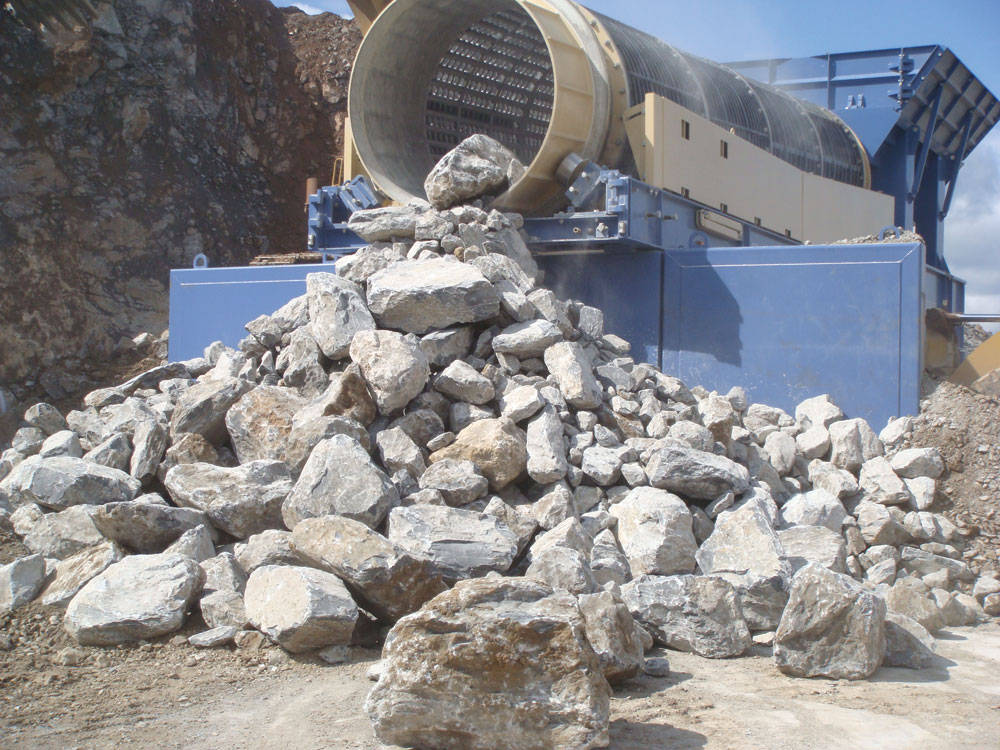
Nigel Moreton examines the evolution of the heavy-duty trommel and the recent upsurge of interest generated by quarry operators looking at more sustainable ways of maximizing profits by reworking waste stockpiles
Demand for good-quality stone has risen steadily in recent years and although much of the UK quarrying industry is currently suffering from the effects of the economic downturn, operators are still looking to maximize their potential reserves in order to make their operations both economic and profitable.
Restrictions on the opening of new quarries and the development of existing sites has meant that matching production to demand has become a challenging balancing act. Companies are now looking at the often vast hidden reserves of waste which were left behind as the quarrying of more easily accessible good rock became the prime objective. As good-quality rock reserves become less abundant, new methods for both cleaning and sizing have been developed to capitalize on these material assets.
The development of the heavy-duty trommel screen by Stelex Construction of Whitchurch, Shropshire, has been at the forefront of this recent trend and has resulted in very high recovery rates of good, clean rock from waste overburden. This, in turn, has helped quarry companies to increase their operating profits.
History
Trommel screens have been in use since mechanized quarrying began in the late eighteenth century. At this time the screens consisted of circular steel meshes bolted together to form a single barrel, which rotated around a long, central shaft set at a slight inclination.
Crushed material travelling through the barrel was graded out according to the size of the apertures making up the cylinders. These screens were used extensively until the 1950s, when vibrating flat-bed versions started to come on to the market.
The development of bigger, more robust, high-capacity trommels in the 1980s, largely for the production of rip rap and armour-stone, paved the way for heavy-duty trommels purpose built to handle high tonnages of material and lump sizes of up to 1.0m. The rolling action of the barrel breaks up any unwanted clays to produce a clean product. The barrel itself is self-cleaning and the entire unit can operate without manual intervention.
In 2006, Stelex, with over 15 years’ experience in the manufacture of this type of screen, decided to redesign and expand the Hercules product range to significantly improve the machine, both in terms of its build quality and operating performance.
The resulting new generation of trommels features a ‘live drive barrel’, which eliminates the need for gear wheels and chains and offers smoother, more reliable and maintenance-free drive to the barrel.
Other features include a hard-steel feed hopper with highly wear-resistant internals, which can accommodate up to 160 tonnes, as well as a variable-speed reciprocating feed table, which is supported on rollers and moves material into the rotating barrel via hydraulic rams. The barrels themselves are manufactured from high-grade steel bars welded to form segments which are then bolted together.
Aperture sizes are produced to suit individual customers product requirements. As well as cleaning dirty and contaminated feed materials, trommels have been used in both quarrying and mining for taking out fines prior to material being fed to a crushing station. Other duties include the high-volume production of sea/river defence rock and sized material used to make up gabian baskets to support road and rail cuttings.
This year, Stelex have launched a new design of recycling barrel which features easily replaceable punch-plate aperture panels. The panels slide easily into the barrel and are locked in place by heavy-duty lifters. The benefits of machines equipped in this way lie in the recycling market where operators require a well engineered, compact, yet heavy-duty machine with ‘switch on and forget’ reliability.
Recent application case studies
Qatar
Here, the duty is to deliver 30 million tonnes of rock for the construction of a new breakwater to provide additional deep-water facilities for large container vessels at the Ras Laffan port.
The machines supplied for this task comprise two model HT232 units, which are the largest Hercules trommels operating outside the UK. Each has a barrel diameter of 2.3m and is capable of handling throughputs of up to 1,000 tonnes/h of as-dug rock. Working 24h a day, seven days a week, reliability and low maintenance are key to the success of this project.
Both machines supply clean, sized rock to a fleet of transport vehicles for delivery to the construction yards. Drive for the feeder and barrel on each machine is provided by a separate, remotely stationed electric/hydraulic power pack. As part of the contract, the machines were specified to be able to work in temperatures up to 50°C.
Southern US
Here, the duty was to clean as-dug quarried materials to produce rip rap sizes of 12in, 18in and oversize at a rate of 500 tonnes/h. The machine, a model HT182M, is the latest generation of the fully mobile trommel, designed to be brought in, set up quickly and put to work, then later towed to another site to repeat the operation.
The clean, graded rock was loaded from the quarry into large river barges, each capable of carrying 10,000 tons. The barges were linked together to transport the material down the Mississippi river to New Orleans, to repair the levees damaged by Hurricane Katrina. The contract called for over 2 million tonnes of rip rap to be supplied.
Germany
Here, a quarry operator needed a machine to clean and size as-dug materials from waste piles in a large limestone quarry in preparation for cement manufacture. A mobile HT182M with a 1.8m diameter barrel mounted on a special support frame to segregate products was supplied for this task.
France
Two customers with recycling plants were experiencing very high wear rates on their existing screens and were unable to cope with heavy builders’ waste, including bricks and concrete from industrial and domestic skips.
For primary sorting purposes, Stelex installed trommels fitted with heavy-duty perforated plate segments, together with chutes and bin walls, to eliminate contamination and to allow screened materials to be conveyed away for secondary sorting.
Future
The increasing requirement to reclaim and recycle a greater proportion of primary rock, and the need to clean materials containing heavy soils and clays will ensure that heavy-duty trommels continue to play a major role in a wide spectrum of applications within the extractive industries.