Kleemann crushers and screens for World Cup and Olympic infrastructure projects
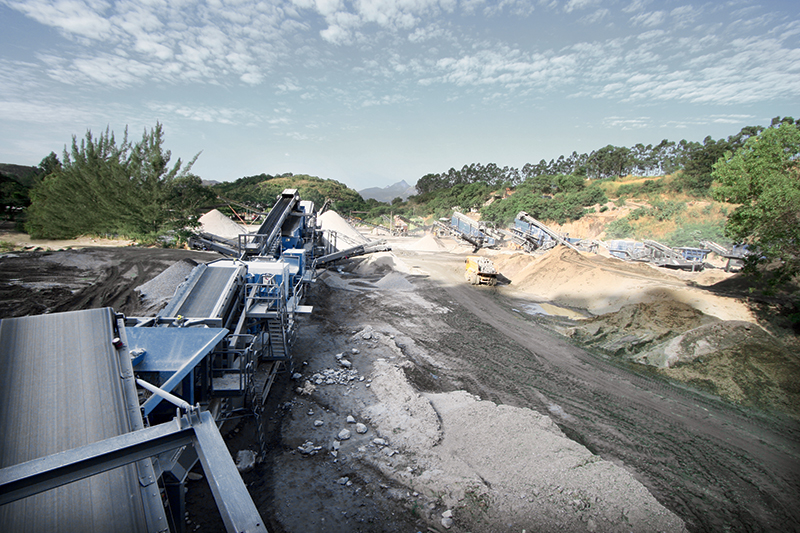
First published in the April 2014 issue of Quarry Management as Rocky Road to Rio
Brazilian quarrying firm using mobile plant fleet to meet World Cup and Olympic infrastructure requirements
WHAT might be the world’s largest mobile stone crushing plant commenced operations near Rio de Janeiro last year, producing aggregates for use in the construction of the 2014 FIFA World Cup and 2016 Olympic Games infrastructure.
Such huge sporting events often involve immense infrastructure projects, and Brazilian quarrying company Tamoio Minerao are well placed to help meet the burgeoning demand for materials, being located just a few kilometers from the centre of Rio de Janeiro and the sports arenas. Moreover, the company is the city’s only supplier of crushed hard rock.
To meet the growing demand for aggregates for road construction, the company decided to significantly enlarge its aggregate production capacity. The new plant had to be capable of producing 2.5 million tonnes a year at rates of up to 900 tonnes/h and in sizes ranging from 0–32mm.
While such project requirements often involve a stationary processing plant, in this case there were several reasons in favour of a mobile solution. First, the plant had to be commissioned as soon as possible; and secondly, it was important that the plant set-up could be flexibly positioned in the quarry in order to remain as close to the point of extraction at all times, thereby minimizing costs and material handling times.
With their expertise in the field of diesel-electric-powered mobile plant combinations, Kleemann were able to offer exactly the right combination and provide extensive support from the factory during the project planning phase. The solution they devised comprises two interlinked plant combinations with three crushing stages and one screening stage.
In the first crushing stage, two large jaw crushers – a Mobicat MC 140 Z with a crusher inlet of 1,400mm x 1,130mm, and a Mobicat MC 120 Z with a crusher inlet of 1,200mm x 800mm – perform the primary crushing and directly feed two downstream plant combinations simultaneously.
The subsequent plant combinations are identical; in the secondary crushing stage they comprise two Mobicone MCO 13 mobile cone crushers which reduce the material from approximately 280mm down to 0–90mm. In the tertiary crushing stage, two Mobicone MCO 13 S mobile cone crushers with integrated triple-deck screening units discharge the first end-product (22–32mm).
Final screening is undertaken by two Mobiscreen MS 23 D mobile triple-deck screening units. With screens measuring 8.0m x 2.3m, each of the two units delivers around 400 tonnes/h of the four other final grain sizes, all of which are less than 22mm.
For further information visit: www.kleemann.info
- Subscribe to Quarry Management, the monthly journal for the mineral products industry, to read articles before they appear on Agg-Net