Hawaiian Cement use Sandvik VSI technology to manufacture construction sand
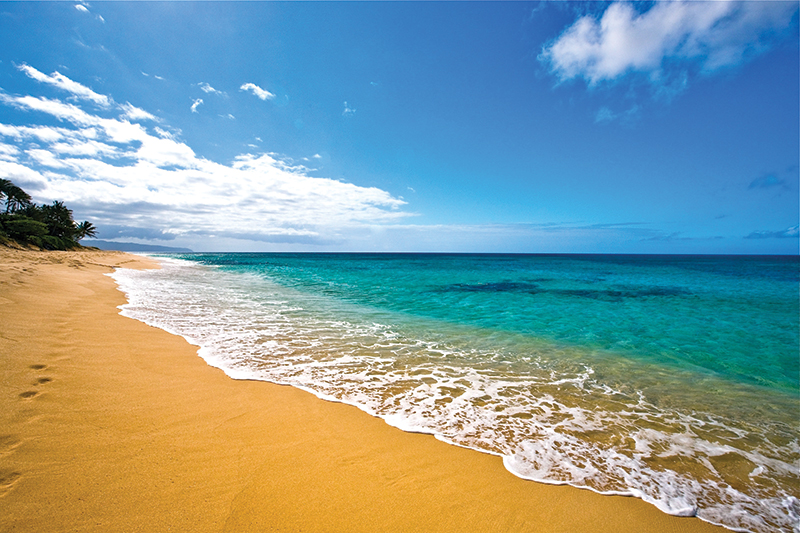
First published in the July 2014 issue of Quarry Management as Sustainable Sand
A revolutionary vertical-shaft impact (VSI) crusher from Sandvik Construction is helping Oahu-based company Hawaiian Cement supply badly needed aggregates and cement products for the island’s construction industry. Before adopting the CV229 from Sandvik, the company had been forced to import sand from British Columbia, more than 2,000 miles away. Hawaiian Cement are now able to supply materials of the highest quality for the island’s infrastructure projects, while reducing their own carbon footprint by being able to use naturally occurring resources.
The island of Oahu and the capital, Honolulu, possess more than 75% of the population and produce most of the economic output in the state of Hawaii. Despite its idyllic geographical location, the island has not been immune to the hardships of the recent economic recession, but has generally managed to weather the storm. This has been due to investment in infrastructure and residential property projects by the State of Hawaii, the Federal Government, as well as the Department of Defense (the island of Oahu is home to the headquarters of the US Pacific Command).
A key contributor to these projects has been Halawa Quarry. Now owned by Hawaiian Cement, this site has been in existence since the late 1940s and is one of the biggest quarries on the island. The company, and the quarry, have both played a critical part in supplying materials for the residential, commercial and public construction projects that have allowed the island to cope with the economic crisis.
Hawaiian Cement, part of the Knife River Corporation, and its predecessor companies, possess a history of supporting the state’s construction needs going back nearly seven decades. Currently, the company leases seven quarries on three of the main Hawaiian islands, employing 200 people in a variety of roles. The business now has four operating divisions – Cement, Aggregates, Ready-mixed Concrete and Coloured Concrete Products – and nine offices throughout the state. Within the Aggregates division, Hawaiian Cement rank among the three biggest aggregate suppliers in Hawaii, with Halawa Quarry being one of the largest on the island of Oahu.
Modern production at Halawa began in the 1960s, and until recently some of the equipment installed at the quarry dated back to this time. Fifty years on, however, the expectations of the customer base have dramatically veered towards obtaining high-quality sand particle shape; a demand that outdated technology could not satisfy.
Strength derived through particle shape
Particle shape has become increasingly important in the cement industry as it is the key factor influencing sand quality, and therefore concrete strength. The tighter the sand particles sit together, the fewer the number of voids and the lower the amount of water needed. This allows for sturdier concrete, thus directly influencing the strength and durability of built roads, and maximizing the return on investment of a construction project. The cubicity of the sand is also essential, with the desired shape producing strength; this contrasting with round or elongated particles which can have a higher number of voids and, therefore, result in spongy and weaker concrete.
Although the shape of some natural sand available on Oahu suited Hawaiian Cement’s expected quality standard, this particular type of sand is very scarce on the island. Additionally, the use of Hawaii’s naturally occurring sand is limited by legislation due to environmental factors. Therefore, Hawaiian Cement had to source it from outside the island, in this case from British Columbia, Canada. However, the need for a self-produced material which would not harm the islands natural resources spurred the development of an on-site solution to produce the required materials for concrete production.
The Sandvik solution
A CV229 impact crusher from Sandvik Construction was chosen by Hawaiian Cement after a demonstration of the machine in the field. This demonstration was supported by analysis of crushed particles in Sandvik’s laboratories in Sweden and Wisconsin, and material-flow studies using Sandvik’s Plant Designer software. The machine is equipped with an HP85 rotor, which has the lowest number of wear parts within a closed rotor of its size on the market. Jason Macy, vice-president of operations at Hawaiian Cement, said: ‘We liked the simplicity of the Sandvik crusher. Other VSIs we looked at had many more parts than the Sandvik crusher.’ This simplicity makes the crusher easier to run in terms of manpower needed and the number of spare parts stocked; both key factors in the smooth and continuous running of a complex operation.
Introduced in 2002, Sandvik’s line of autogenous crushers, of which the CV229 is one of the more recent developments, utilize a rock-lined rotor to accelerate the feed material. This is impacted in a highly energized rock-lined crushing chamber and impacts with material falling through the biflow system. The crushers in this range incorporate the Sandvik Hurricane rotor, which was a major breakthrough in VSI autogenous rotor design due to its decreased vibration levels and wear part design, which results in increased crusher bearing life combined with reduced maintenance. In addition, standard Sandvik VSI crushers are fitted with a timed trapped two-key system, which ensures the safety of maintenance personnel, combined with electrical isolation. Also supplied and fitted as standard are a vibration-detection switch and a pre-start alarm siren.
These and other features have enabled the CV229 to deliver an impressive performance for Hawaiian Cement. ‘Since its installation in December 2012 the machine has produced 200,000 tons, at an average rate of 40,000 tons per month. Considering the rotor wear, there is at least another 200,000 tons that can be crushed before the parts need to be replaced,’ said Kevin Bohanon, sales manager for Sandvik Construction in the US. Steve Pegler, sales manager at Elrus, Sandvik Construction’s distributor of stationary crushers in the State of Hawaii, explained how the high production rates at lower costs can also benefit non-Sandvik crushers: ‘Sandvik offer a Rotor Retrofit Programme, which makes it possible for customers with various makes of autogenous VSI crushers to achieve the benefits Hawaiian Cement are seeing on their CV229.’
Future developments
Explaining future developments at Halawa Quarry, general manager Don Matsumura said: ‘Our goal is to get rid of importing the Canadian sand and produce our own number 4 product (–40mm) with the CV229. This machine asks lots of questions of us, like the feed it needs and the moisture it can handle. We need to figure out how the rest of the plant has to work to keep up with the production rate of this new crusher. The cost of the Canadian sand alone, however, validates the capital expenditure, as do the savings the CV229 will give us, comparatively, in terms of production. The low parts wear further validates this investment. Changes of parts on the older models were made every month. With this one, no changes have been needed for five months.’
- Subscribe to Quarry Management, the monthly journal for the mineral products industry, to read articles before they appear on Agg-Net