Hadley Invest in New DUO Plant
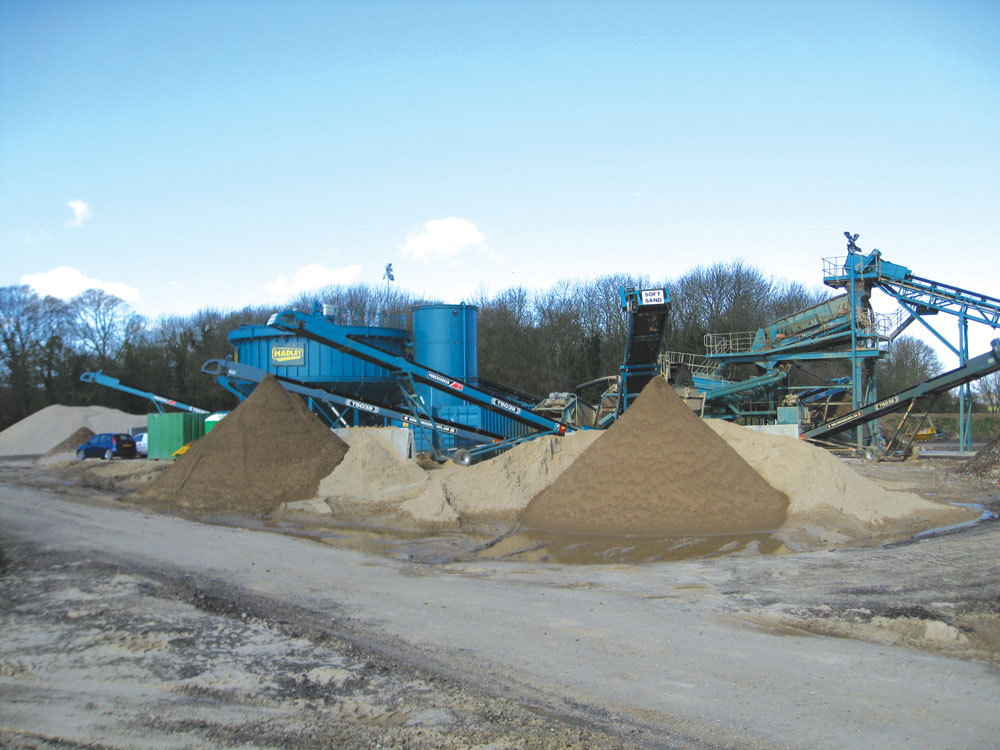
Berkshire-based firm invest in new aggregate washing facility
Maintaining a firm belief in sustainable solutions, together with a desire to utilize the latest technology and integrated processes, Berkshire-based waste-management and recycling firm Alan Hadley Ltd have recently invested in a new aggregate washing facility in a move to develop higher-quality recycled materials and, at the same time, reduce the company’s operating costs.
Supplied by DUO Equipment of Coventry, and located at the Alan Hadley’s Moore’s Farm site in Pingewood, Berkshire, the new plant will provide the company with the ability to raise their recycling rates and divert more of their waste from landfill. The prime objective of the investment is to recycle excavation waste from construction sites into five grades of high-specification recycled sand and aggregate.
Waste material is fed to the plant by means of a feed hopper equipped with a vibrating head and variable-speed drag-out belt. All +125mm oversize material is rejected, while the –125mm material is fed on to an inclined conveyor, rated at 200 tonnes/h, which, in turn, discharges on to a 16 x 5 rinsing screen.
Any material greater than 40mm is rejected by the rinsing screen, while all –40mm material is fed to a Powerscreen Powerscrub, before being discharged over a dewatering screen and then conveyed, via an inclined conveyor, to a 16 x 5 dry screen. This screen grades the material into 10mm, 20mm, and 40mm single sizes, which are sent to their respective stocking areas by three stockpile conveyors.
Meanwhile, waste water from the Powerscrub unit is passed over a dewatering trash screen to remove any foreign materials from the system, while the water/sludge is collected in a sump tank before being pumped to a Finesmaster 120 sand-classification plant. This unit produces two grades of dewatered sand (soft and sharp), which are delivered to their respective stocking areas by two stockpile conveyors.
Process water from the sand-classification unit is pumped into a deep-cone thickener and simultaneously treated with flocculant to allow the recovery of clarified water for subsequent reuse by the wash plant, while the silt-laden underflow from the thickener is discharged into a nearby silt lagoon.