Flexible Future for Oconee County Quarry
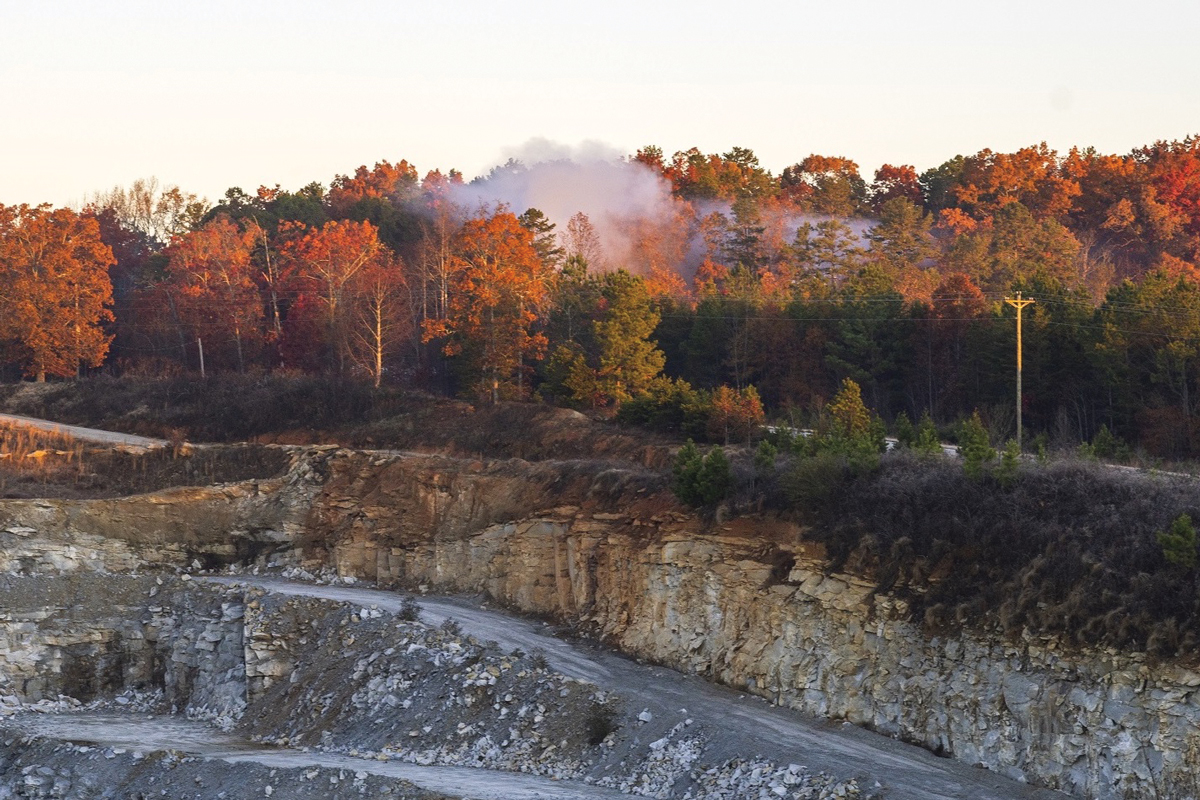
First published in the June 2020 issue of Quarry Management
New dual-powered mobile crushing plant more than doubles aggregate production, improves product quality and delivers unprecedented versatility for one of the few government-owned quarries in the US
In operation since 1948 and located outside the town of Walhalla in rural north-western South Carolina, near the Georgia and North Carolina borders, Oconee County Quarry extracts and processes blue granite – the state rock of South Carolina. The county-owned site currently has permission to operate until 2050 and its reserves are estimated to last until around 2100. Last year the quarry sold approximately 530,000 tons of stone.
As well as producing aggregates to meet county government needs, including road building, storm drainage and slope protection, Oconee County Quarry serves more than 600 local customers, ranging from paving contractors to rural residents needing a little gravel for a driveway. ‘We’re able to support local government needs as well as the needs of the local citizens, and we’re very proud of that,’ said assistant quarry manager Thom Moxley.
In recent years, however, an aging crushing plant had left the quarry struggling to satisfy demand. Running at full capacity, the 30-year-old stationary plant could not produce more than 300 tons/h, and it often was not running at all. Unscheduled downtime was taking a toll on production. ‘We had got to the point where we were running the plant to try to meet production needs and not having enough time to do the preventative maintenance that we needed to do,’ said Mr Moxley.
Thus, in early 2017, together with colleagues at the quarry and the county administrator, Mr Moxley began discussing and researching replacement options, comparing both stationary and mobile plants. Later that year, both he and crew leader Billy Buchanan travelled to Sweden to inspect a dual-power mobile plant. ‘This was a real shift in our way of thinking – that instead of taking the rock to the plant, you take the plant to the rock; but the efficiency of that plant was impressive,’ commented Mr Buchanan.
In February 2018, Oconee County Council gave the go-ahead for US$7.5 million of improvements to the quarry. The quarry staff recommended the purchase of a mobile crushing plant and the county initiated a ‘request for proposal’ (RFP) process. The quarry needed a plant that would produce a minimum of 650 tons/h of finished product, including at least 200 tons/h of 1in #57 aggregate. ‘These were the stringent requirements that we had to meet for Oconee County to feel like it could make this investment,’ said Mr Moxley.
The quarry also needed the plant to be able to produce several other products, including #789, Class A rip-rap and asphalt sand, whilst the crusher run needed to meet South Carolina Department of Transportation specifications for gradation in order to be used on state roads, and both the #57 and #789 also had to meet state specifications for flat or elongated particles.
Mr Moxley and his colleagues were particularly intrigued by the flexibility of a plant that would allow the quarry to freely alternate power supply between onboard diesel generators and the main electric network. ‘Dual-power machines were very attractive to us because we can be at our most efficient if we are on the grid,’ he explained. ‘However, at certain times it’s costly to be on the grid, so we can use diesel to stay off of the grid during peak times, which should reduce the operation’s diesel budget. Also, electric power is quieter, so there were a lot of things that helped us to justify the dual-power system.’
Oconee County Council awarded the order to Sandvik, whose US$5.8 million proposed solution came in $750,000 under budget. This included a five-year extended warranty, local dealer service support, scheduled equipment inspections and an on-site parts consignment container, as well as comprehensive operator training.
‘We felt that throughout the whole process, Sandvik’s technology was on the cutting edge, plus they make very durable, strong products,’ said Mr Buchanan. ‘All the companies in the RFP sent us offers of their solutions, and Sandvik actually sent us four options. The one we went for has provided some solutions that we never even asked for and has the potential to grow. In the future, the quarry might need more capacity, so Sandvik were looking out for us.’
The quarry invested in a mobile plant primarily because it provides flexibility in pit design. The new plant can be relocated indefinitely, allowing the quarry to size, crush, screen and stockpile as close to the face as possible. ‘We’re never going to be in a situation again where we have a stationary plant sitting on rock that we need to extract,’ said Mr Buchanan. ‘It’s going to decrease the amount of trucking and equipment necessary to give the customer what they need, and when the time comes, we can just move our plant and won’t have to redesign a plant or start all over again.’
The new diesel-electric mobile plant was commissioned in November 2019 after Sandvik reconfigured it from 400V and 50Hz frequency to the North American 480V and 60Hz mains electric power. The county also upgraded the electrical system to provide the required voltage to support the new plant, which consists of a Sandvik UJ640E mobile primary jaw crusher, a Sandvik US550E secondary cone crusher, a Sandvik UH550E tertiary cone crusher, two Sandvik QA441e Doublescreen mobile screeners and three mobile stackers.
‘Each of these items was selected for future growth and to be able to network with other models that may be added to the plant, so it was a very well thought-through process that the whole Sandvik team worked on,’ said Mr Moxley. ‘Sandvik ensured that the jaw crusher was not going to be the bottleneck in our operation. We can actually grow with the jaw over the coming years. We wanted about 650 tons/h, which would more than double what we made previously, but we feel like there’s 850 tons/h there in the future.’
The quarry’s Sandvik UJ640E features an 18m3 feeder hopper extension to allow faster loading and provide a surge pile to ensure a continuous feed to its Sandvik CJ615 single-toggle jaw crusher, maximizing throughput and efficiency. ‘It is a very deep jaw that can accommodate larger 38in rocks,’ said Mr Moxley. ‘It has been designed in such a way that all of the vibration is absorbed through the track system. And with it being upsized and not having to work as hard as a jaw normally would, it just methodically does its work without very much effort.’
Until the quarry opens up the face, material from the jaw is trucked from the base of the 300ft deep pit to a stockpile, where a large wheel loader feeds the Sandvik US550E. The secondary crusher’s dual interlocking and intelligence system is integrated with Sandvik’s Automatic Setting Regulation (ASRi) control system to automate process optimization and help predict maintenance issues, thereby maximizing uptime. ‘The Sandvik plant is something you can just set and forget,’ said Mr Buchanan. ‘We have confidence in the ASRi system. It’s made life easy. There’s very few manual tasks that we have to do anymore, and all that is available through the technology that Sandvik offer.’
The US550E feeds into the Sandvik UH550E. Both cones feature a screenbox that allows them to make a final product. ‘We don’t even have to push it forward to our screeners, so that gives us much more versatility,’ said Mr Moxley. ‘We’re actually thinking about maybe adding a product or two that we don’t currently do.’
Not only have the reduction ratios of the secondary and tertiary cones proved impressive, but Mr Buchanan, who oversees the quarry’s quality-control programme, confirmed that the stone produced by the new mobile plant is also measurably more cubical – an essential characteristic for road sustainability.
‘We have to hit our production goals, but the product can’t be flat or elongated,’ said Mr Buchanan. ‘There are multiple studies that show that roads will deteriorate much quicker if flat or elongated products are used. The feeder on both cones has a level sensor, which eliminates the possibility of human errors. The feeder always provides the cone with the exact amount of rock it needs, to make sure that it’s crushing rock on rock and getting a cubical product. With the old plant, this was simply impossible.
‘The ability to choke-feed the new cones more efficiently has virtually eliminated this issue,’ continued Mr Buchanan. ‘Our flat and elongation rate on the old plant was roughly 14%, but so far, with the Sandvik plant, we’re around 4% – a massive improvement.’
A splitter on the back of each Sandvik QA441e Doublescreen separates product from the tertiary cone and, in conjunction with the patented Doublescreen system, allows the quarry to produce #57 and #789 simultaneously. Each of the three 80ft mobile stackers is capable of creating a 6,000-ton stockpile, which reduces the need to move the product. ‘We can actually sell directly from these stockpiles,’ said Mr Moxley.
Some two months after the obsolete stationary plant was decommissioned, Mr Moxley said the new mobile plant was exceeding expectations. ‘We have a lot of versatility with this new plant. We can push materials in a different direction to optimize output for the production we need. Each day we find new things we’re capable of doing that we didn’t have the ability to do in the past. Modern technology is amazing and we’re now very fortunate to have a new plant that is capable of more than doubling the production we were previously achieving.’
Echoing these sentiments, Mr Buchanan added: ‘We were looking to better ourselves through technology and I think that’s what we’ve done with Sandvik. They’ve been fantastic from the start and I’m very confident in our relationship going forward. We looked at several companies but Sandvik had the best products. I’m very confident that we have a partner who is going to be with us for the next several decades.’
- Subscribe to Quarry Management, the monthly journal for the mineral products industry, to read articles before they appear on Agg-Net.com