EvoQuip introduce new impactors at Hillhead
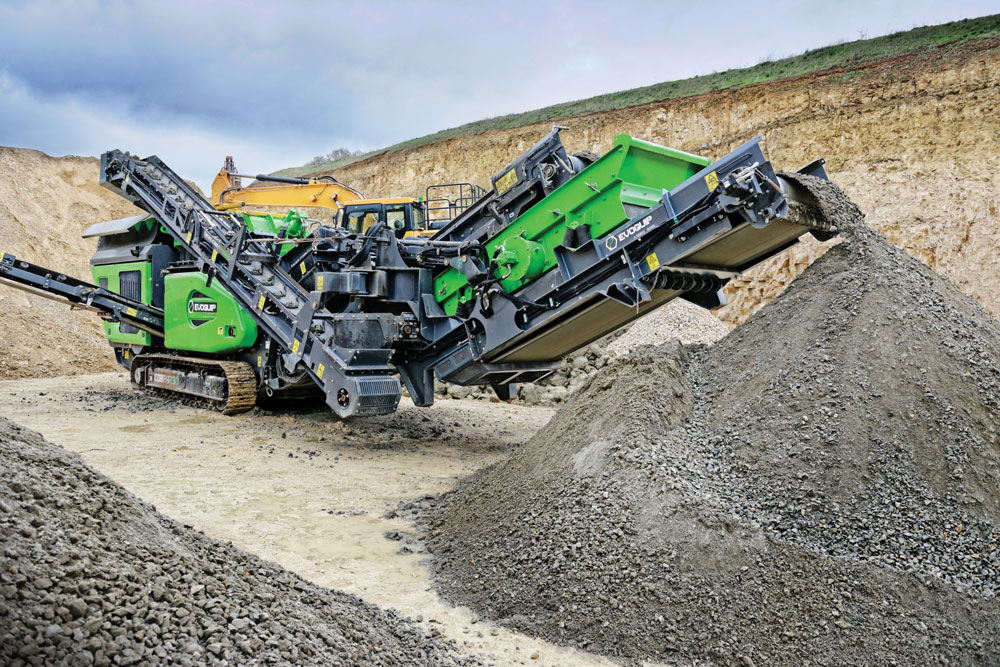
First published in the September 2018 issue of Quarry Management
Compact crushing machine portfolio expanded with the launch of the Cobra 230R and Cobra 290R
Terex brand EvoQuip launched two new impact crushers at Hillhead 2018 – the Cobra 230R and Cobra 290R, with the former shown on static display whilst the latter was put through its paces on live demonstration duties feeding a Colt 1000 scalping screen in ‘Crusher Alley’.
The EvoQuip range of mobile crushing and screening equipment provides a compact and versatile solution capable of operating in the most demanding of applications – including reinforced concrete, recycled asphalt, construction and demolition waste, coal, natural rock etc – and well suited to on-site recycling in urban areas, with all machines being easily transportable from job to job.
According to EvoQuip, the Cobra range of impactors provides class-leading productivity, unmatched versatility and excellent fuel efficiency. The machines are designed with the operator in mind, in terms of ease of use and serviceability, incorporating features such as ground-level access to the engine, hydraulics, service and refuelling points, as well as a hinged radiator pack, hinged diesel tank and product conveyor that can be removed quickly for major maintenance. In addition, the operator has the ability to move the machine via remote control from the excavator cab without shutting down the crusher.
Building on the success of the Cobra 230 launched in 2017, the new Cobra 230R is a closed-circuit version incorporating a quickly detachable 2.44m x 1.2m (8ft x 4ft) post-screen and oversize conveyor that ensures the required product specification is achieved, with oversize material either being recirculated back to the crusher or stockpiled.
The key design features in the Cobra 230R ensure an optimal material flow through the crushing process. As material moves from the feeder through the impactor and on to the product belt each section becomes wider, thereby ensuring an unrestricted flow. The generous under-crusher clearance and the short distance from the crusher discharge to the magnet make the Cobra 230R an effective solution in all applications.
At the heart of the machine is the proven Terex CR004 impact chamber with an inlet opening of 800mm x 615mm. Feed material is impacted by blowbars fitted to the 830mm wide x 860mm diameter rotor, before being smashed against primary and secondary aprons until the desired product size is achieved. The machine is capable of throughputs up to 250 tonnes/h, depending on the feed material and apron settings.
The Cobra 230R uses a fuel-efficient, high-performance direct-drive system to power the impact crusher. This system uses a 260hp John Deere engine or a 275hp Volvo Penta engine, depending on the region of sale. This, along with the two independent hydraulically controlled aprons, allows the operator to optimize material throughput and reduction whilst ensuring the best fuel efficiency.
The larger Cobra 290R also builds on the strengths of the Cobra 230, incorporating a 1,000mm x 1,034mm (40in x 41.5in) diameter Terex CR055 impact crusher developed using proven components and technology from some of the larger impact crushers within the Terex range.
Ready to crush just minutes after arrival on site thanks to its rapid ground-level set-up and intuitive two-button start-up sequence, the Cobra 290R is a versatile and easy-to-use impact crusher capable of operating in the most demanding of applications, including reinforced concrete, recycled asphalt, C&D waste, coal and natural rock.
With a throughput potential of up to 290 tonnes/h, depending on feed material and apron setting, the Cobra 290R utilizes a 315hp Volvo engine to power its fuel-efficient, high-performance direct-drive system.
Fitted as standard is a hinged inlet lid that greatly reduces the risk of material bridging at the feed-in point, and, like the Cobra 230R, the Cobra 290R also has two independent, hydraulically controlled aprons that allow the operator to optimize material throughput and reduction.
Moreover, the machine’s patented hydraulic overload-protection system not only protects the crusher in the event of an uncrushable item entering the chamber, but also minimizes apron bounce and reduces the amount of oversize material passing.
In addition, the tip speed of the rotor can be varied depending on the application and product requirements. Throughout the crushing process, the Cobra 290R constantly monitors the engine load and automatically regulates the feeder speed as required.
Below the impact crusher, customers can choose between the full-length conveyor design and a vibrating underpan feeder, which offers complete belt protection in heavy-duty recycling applications.
As with the Cobra 230R, the generous clearance from the rotor to the belt, the short distance from the crusher outlet to the magnet and the ability to hydraulically raise and lower the conveyor all ensure optimal material flow through the machine.
A single-deck after-screen system is available as an option. This incorporates an aggressive 2.74m x 1.5m (9ft x 5ft) screen that provides a sized end product. The ability to quickly detach the complete after-screen system, including the oversize conveyor, allows the customer to run the machine in standard mode or transport this system separately. This option can be purchased and retrofitted at a later date.
All EvoQuip models can be fitted with the T-Link telemetry system, which provides the customer with real-time information on the performance of their machine(s), maximizing uptime, parts and service availability, and providing factual up-to-date information direct from the field. For more information visit: www.terex.com/EvoQuip
- Subscribe to Quarry Management, the monthly journal for the mineral products industry, to read articles before they appear on Agg-Net.com