Economies Of Scale
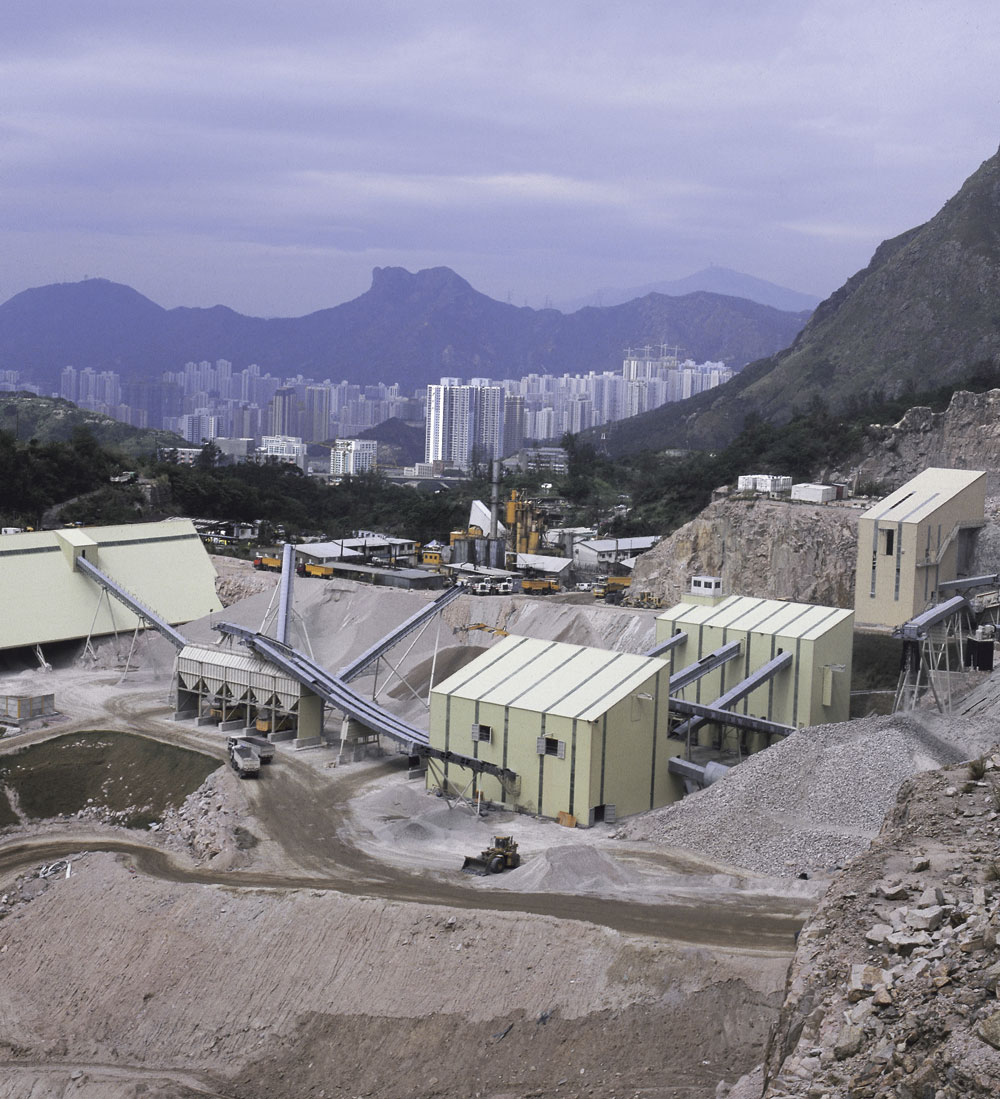
Having the right quality rock – at the right price – are the two main drivers of the global aggregates business. Here, Metso Minerals’ Jarmo Eloranta, Jouni Mähönen and Keijo Viilo discuss the importance of crushing circuit planning and efficient operation
Two pieces of news that will not surprise anyone in the global aggregates industry are, first, the real price of aggregate is falling; and secondly, the quality requirements for aggregates are becoming stricter. The reason these gems of information will cause little surprise is that they have been going on relentlessly for years – with few signs that this trend will stop anytime soon. The causes of this situation arise from both the supply side and the demand side of the industry and can be summarized as follows:
Supply side: Price reductions have mainly been the result of improved comminution processes, improved equipment availability and general cost cutting. New concepts, such as mobile crushing, have also made a contribution to more efficient crushing practice. These factors have collectively driven down the price per tonne of aggregate and yet allowed profit margins to remain largely static.
Demand side: Customers are not being unreasonable when demanding that aggregates meet exact specifications. There are clear economic factors which confirm the need for improved aggregate quality, mainly relating to the shape of end products (ie flakiness and elongation). Improved aggregate shape has the potential to significantly reduce the total cost of concrete and asphalt – two of the main uses for aggregates.
Despite constituting only a small percentage of asphalt’s total make-up (less than 10%), the high cost of bitumen determines the cost of the entire surface layer (see fig. 1). Therefore, if the use of higher-quality aggregates can extend the life of a road, or lead to a need for less bitumen, the added investment will more than pay for itself.
All aggregates are not the same
What is meant by the term ‘quality aggregate’? The answer is a product that has an angular shape but is not flaky or elongated. It must have an even gradation (ie gradual and progressive) and a high voids ratio (ie not too many holes that need filling with expensive bitumen when the aggregates is packed together in bulk material).
A good-quality aggregate, in terms of shape and size, has the ability to increase the wear resistance of the top layer. Not only does this save on maintenance costs (because the road lasts longer), but because the aggregates bond more securely to the bitumen this internal friction also increases the load resistance of the layer. Even at the construction stage, high-quality aggregates have better workability and are easier to pave.
These requirements are not just important for asphalt – they are also very similar for concrete. Here, a good-quality aggregate will have the impact of reducing the amount of (expensive) cement needed and the finished concrete will be stronger (see fig. 2). Again, the material will also be easier to work with and lay.
A good-quality aggregate for concrete should have a rounded or square shape with smooth surfaces – not flaky or elongated. Again it should have an even gradation with only a small amount of sand on its surface and little void space when packed in bulk. And because concrete involves a chemical reaction between cement and water, the aggregates should not interfere with this process. A controlled microfines content is necessary, as clay and other organic microfines can be harmful in concrete.
Unlike asphalt, there is a range of other requirements for aggregates where differing strength classes of concrete are required (see table 1). In practice, however, this is not always consistently controlled and concrete suppliers are known to produce their own ‘recipes’ with respect to aggregate requirements. These tighter requirements are based on these firms’ own development work.
The need to produce better- quality aggregate is obvious, but what does this mean in practical terms for quarry owners? Taking a typical three-stage plant as an example – where 0–16mm fractions are needed; where there are no specific quality requirements; and where production can range from 210 tonnes/h to 321 tonnes/h, depending on the running parameters of the crushers and screens in the process (see fig. 3) – minimum capacity is achieved using large settings on the crushers, thus creating high circulation at the tertiary stage. Maximum capacity is achieved by tightening the settings in the crushers for lower circulation; screening is optimized and the setting corresponds to the maximum yield for the 0–16mm fraction.
The difference in financial impact between these two extremes is dramatic, for with an investment of just 9%, the corresponding improvement in sales revenue is over 53% (see table in fig. 3), much of which is due to process optimization.
The key to effective process optimization is twofold. First, operators should run equipment constantly with the optimum parameters; modern automation can make a major contribution to this. Secondly, plant availability should be maintained at a high level. This requires the removal of all kinds of process-based disturbances (such as oversize material entering the crushers). Proper process planning and management as well as preventive maintenance are the key elements.
Quality does not happen by accident
The remainder of this article considers two different process configurations and reviews the proportion of the final product (0–16mm) that is produced at different stages of the process.
From figure 4, it can be seen that much of the final product (4–16mm) is produced in stages other than the tertiary. Indeed, 20% of the final product originates either from the feed or primary crushing, which explains the poor flakiness of the final product; the flaky primary product spoils the higher-quality aggregate emerging from the tertiary stage.
However, this configuration is not the only option. The process could be conducted differently, as shown in figure 5. Here the tonnage of 0–16mm is 100 tonnes/h less than in the previous example, but its quality is considerably better. As can be seen from the tables in figure 5, the reason for this lies in the fact that 94% of the 4–16mm product originates from the tertiary cone, while the 4–16mm fraction from the feed and primary crusher is not allowed to enter the final product and thus spoil it. On the contrary, this product is re-crushed to achieve a better shape, which, since this uses up capacity, leads to the reduction in hourly tonnage.
Optimal parameters
These examples clearly indicate two main findings: first, that the system configuration must be correct in order to produce the right amounts of aggregate and to fulfil the specifications. If this is not done correctly in the first instance, later modifications, although possible, will be expensive. Secondly, running the process using optimal equipment parameters can make a real difference in terms of financial success, but achieving this requires continuous monitoring and adjustment of the equipment and process. Additionally, high availability and utilization rates are crucial, as changes in utilization have a significant impact on profit.