Delivering In The Desert
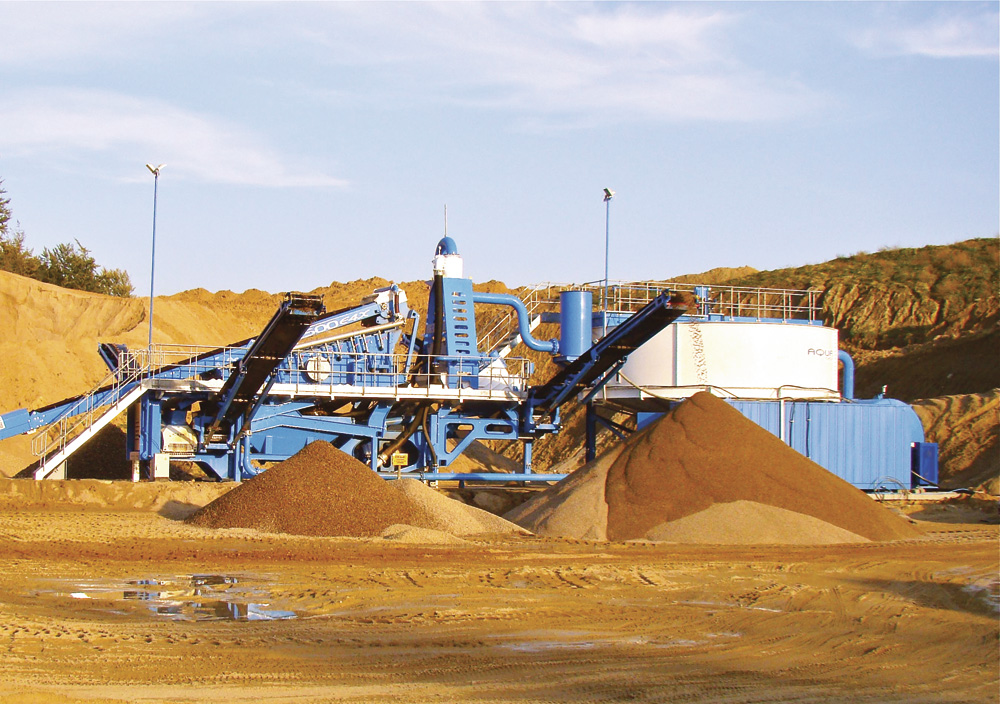
CDE technology provides enhanced sand production capability for the Gulf region
Washing is widely accepted to be the most efficient way of producing high-quality sands for use in a variety of applications, ranging from sand for use in concrete to specialist applications such as golf and silica sands. This is because of the limitations of traditional dry-screening processes, particularly with regard to the ability of these systems to effectively and consistently remove –75 micron material.
CDE Global, who have built a reputation for the delivery of efficient sand-washing plants throughout the world during the last two decades, have been working in the Gulf region for almost 10 years. Throughout this time the company has completed many sand-washing installations, including two 1,200 tonnes/h plants in Qatar, and there are numerous other CDE washing plants in operation in many other regions of the Gulf and North Africa, including the Kingdom of Saudi Arabi (KSA), Oman, Bahrain, Tunisia and Morocco.
‘Our entry into the Gulf came as a result of the demand for high-quality washed sands in the region,’ explained Iain Walker, CDE sales manager for the Middle East and North Africa. ‘This resulted in the two large 1,200 tonnes/h projects in Qatar initially, and since then there have been many other installations with capacities more in line with every-day requirements of between 50 and 150 tonnes/h.’
Over the years CDE have developed a long list of projects where they have replaced older, less-efficient traditional sand-washing plants, such as bucket-wheels and screw classifiers, with their hydrocyclone-based EvoWash system.
‘Old sand-washing technology has a number of issues, not least the loss of significant quantities of quality fines to the settling ponds or water-treatment phase,’ said Mr Walker. ‘In an effort to ensure effective removal of the –75 micron fraction, these inefficient systems take a lot of commercial-quality sand with them, which has a negative impact on the profitability of the operation.’
According to CDE, operators using inefficient sand-washing plants are suffering on two fronts. Not only is the final value of their sand product compromised by the presence of larger quantities of –75 micron material than is ideally the case, but operational costs are also increased as a result of the requirement to clean out settling ponds regularly in an effort to recover the good material that has been lost.
There are various design features on the EvoWash plant that prevent this problem from arising, with the choice of hydrocyclone technology being one of the key factors. According to CDE, hydrocyclones offer the most efficient means of delivering the required cut point, thus ensuring a sand product that meets the desired specification. The ability to guarantee a sand specification effectively maximizes the commercial value of the material and, thus, the profitability of the operation.
‘Investing in low-cost, old technology is a false economy as the return on investment takes much longer than is the case when our washing system is specified,’ commented Mr Walker.
Water recycling
The ability to offer operators water-recycling equipment to accompany the sand-washing plant has also been a key factor in the success that the company has enjoyed in the Gulf.
Given the climate in the region and a scarcity of water when compared with the northern European markets where CDE originally established their reputation, the specification of the AquaCycle thickeners and GHT filter presses that the company offers became more frequent as business grew.
‘You could say that Gulf operators led the way for the global washing industry in relation to the specification of water-recycling equipment,’ said Mr Walker. ‘We now include our thickeners and filter presses on 80% of all global washing projects, whereas as recently as five years ago this figure would only have been around 20%.’
The scarcity of water in the Gulf was a major factor that made the CDE water-recycling and sludge-management system a ‘must have’ rather than a ‘like to have’, as was the case in some other territories. Environmental concerns and subsequent legislation in this area have driven demand for water-recycling systems, but there is also a growing realization that the introduction of such systems can actually offer a more efficient way of operating.
According to CDE, when the costs of managing large settling ponds, the additional space required to accommodate the operation and the potential health and safety risks are factored in, water-recycling systems offer operators a way to ensure a much more efficient and easily managed washing plant.
A new dry processing option?
Just as the introduction of effective water-recycling systems was a response to the unique climate of the Gulf region, CDE have taken a further step with the introduction of new air-classification technology.
‘The introduction of our Sirocco air-classification system was a move inspired by the need to offer a solution to those operators not able to consider a washing plant due to water supply issues,’ explained Mr Walker. ‘Even with full closed-circuit water recycling reducing the volume of fresh wash water required to around 5% of the total volume, some operators are simply not able to ensure supply of the volumes needed to operate a wash plant.’
A question that arises from this decision is, how does it fit in with the previous assertion by CDE that dry screening of material is not an efficient process as washing? Answering this question, Mr Walker says that although a dry process, the Sirocco air-classification system is far removed from the traditional dry-screening process which has been problematic for those seeking to produce high-quality sand.
‘The key success of washing using our EvoWash system is the capability to efficiently remove –75 micron material,’ said Mr Walker. ‘We prefer to describe the Sirocco as a dry-wash system – or washing without the water, as it is able to achieve the same results as washing in terms of –75 micron fines removal.’
Prior to the introduction of the Sirocco air- classifier to the Gulf, operators wishing to produce quality washed sands were unable to do so because of a lack of water availability. With the introduction of the Sirocco, the option exists for these same operators to achieve the higher-specification sand products that will allow them to diversify into new sectors of the construction market.
‘We have several Sirocco units operating in KSA and Oman that are producing concrete sands to the same specification as those being produced by our EvoWash sand-washing plant,’ explained Mr Walker. ‘With each new Sirocco unit comes a growing acceptance of the technology and a realization that this dry-wash system is a viable alternative to a washing plant.’
An additional feature of the Sirocco system that has made it attractive to operators is the small amount of space required to accommodate the system. CDE offer the Sirocco as a stand-alone unit or as part of a turnkey package. The turnkey option includes a feed system, the Sirocco air-classification unit, two stockpile conveyors – one for the sand product and one for fines – and a dust-suppression system.
The fines product from the Sirocco is not a waste material but has a number of applications, including use in the manufacture of ceramic tile adhesives and grouts. This can provide additional revenue for operators from what many consider to be a waste material.
The Sirocco system is available in a variety of configurations from 50 tonnes/h up to 800 tonnes/h in a single unit. According to CDE, this differentiates the Sirocco from other air-classification systems on the market, which offer single units at 150 tonnes/h and multiples thereof should larger capacities be required.
‘Our washing plants are customized to the specific requirements of each project and our Sirocco units are built according to the same principles,’ said Mr Walker. ‘The specification of the right system needs to take account of the individual characteristics of the feed material, with the level of fines being the critical factor. Other systems take a ‘one size fits all’ approach, which can compromise final product quality.’
The future
With the suite of products developed by CDE, the company says it is confident of further growth in business during the months and years to come. ‘The introduction of the EvoWash and Sirocco units reflects the approach we take to all the regions in which we operate,’ said Mr Walker. ‘We will continue to respond to the specific requirements of the Gulf region as we seek to continue to offer operators the most efficient sand-processing systems available.’