Continued Loyalty
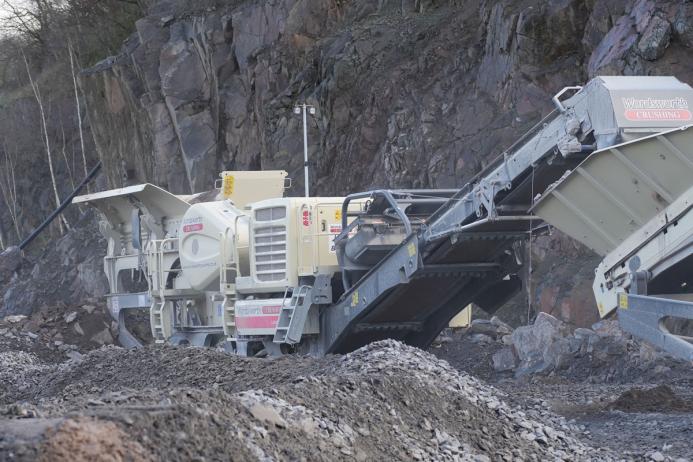
First published in the January 2024 issue of Quarry Management
Wordsworth Crushing address growing demand for quarried materials at Whitwick Quarry, in Coalville, by taking delivery of a new Metso Lokotrack LT116 mobile jaw crusher – maintaining a long tradition of operating the Finnish OEM’s Lokotracks in the aggregate contractor segment
Managing mobile equipment efficiently, improving operator safety, and delivering a combination of efficient crushing action, high output capacity, and lowest cost per tonne are some of the critical drivers for aggregates/earthmoving contractors when it comes to investment in the latest and most advanced heavy plant machinery across their fleets.
Established in 2003, family-run Wordsworth Crushing – alongside sister company Wordsworth Excavations – are established names in the quarrying and mineral products industry. The Barnsley-based business started out as a crusher hire specialist, but it was the company’s strategic move into contract crushing and materials processing some years later that put Wordsworth Crushing firmly on the map.
‘Diversifying our operations and expanding to become a nationwide contractor to the heavy building materials industry have clearly paid dividends for us,’ said Oliver Wordsworth, managing director of Wordsworth Crushing.
‘We have grown steadily since our inception over 20 years ago and the company is now considered to be one of the leading players in the aggregates contractor market. Working for blue-chip companies, we have earned an enviable reputation for building long-term customer relationships and helping quarrying firms meet business goals by developing material streams, reducing downtime, and increasing productivity.’
Operating across a wide range of industry market segments, including earthworks, waste-recycling, demolition, and ground stabilization, the company’s primary focus continues to be on contract crushing and aggregate production. With many of their quarrying and construction clients operating in a more sustainable manner, Wordsworth Crushing have seen a huge demand for projects that not only deliver on time and within budget, but also reap the benefits of increased efficiency, higher material productivity, and lower fuel costs.
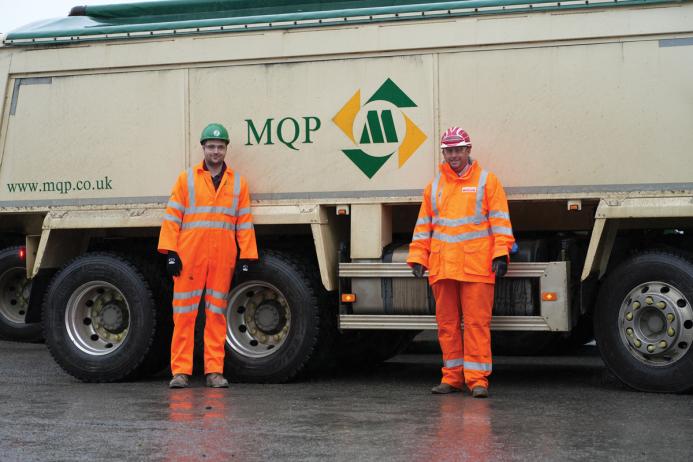
To meet these requirements, the South Yorkshire contractor demands a lot from its mobile plant assets and over the last 18 months has invested heavily across its large fleet of crushers, screeners, and earthmoving equipment.
‘As more quarry operators recognize the environmental benefits and substantial cost savings to be gained from recycling and sustainable productivity, it’s essential for us to have the correct mobile products and service offerings in place – and be able to match the right machine to the requirements of each customer’s individual needs,’ explained Mr Wordsworth.
‘For example, we recently took delivery of a new Metso Lokotrack LT116 mobile jaw crusher, which has been put straight to work at Midland Quarry Products’ Whitwick Quarry, in Coalville. I knew at some point we would have to upgrade our processing capabilities at Whitwick, which has some of the hardest granite in Leicestershire. Recognizing the need to replace the existing crushing equipment on site, the LT116 machine was the obvious choice to go with for our next investment.’
Metso understand the importance of helping customers find the most effective, sustainable, and cost-efficient mineral processing solutions, and their Lokotrack mobile crushing and screening plants are widely used around the globe.
‘The new Lokotrack LT116 jaw crusher has fundamentally resolved a challenging primary crushing application at Whitwick,’ said quarry manager Callum Robson. ‘Since reopening the quarry site in 2021, the main objective of MQP’s business plan was to significantly increase the production of quarried materials, together with high-quality building materials for the buoyant local construction products and recycling markets.
‘The LT116 is working really well for us and is proving to be a solid performer in crushing the hardest granite found in the region, whilst delivering cost-effective and safe operation and providing a very high reduction ratio with premium end-product shape and consistency.’
Mr Wordsworth added: ‘We have always had a good working relationship with Metso and cannot fault the quality and reliability of their equipment. The Lokotrack LT116 is one of the most efficient mobile jaw crushers available for demanding quarry and contract crushing applications.
‘Importantly, we also wanted a strategic partner that could add value to our operations by achieving excellent results and helping us meet demanding timelines. In the short space of time working with McHale Plant Sales (UK distributors for Metso), they have delivered on all counts – providing a high-quality bespoke solution for us and addressing our concerns such as prompt service, crusher spares and wear parts, and on-site backup, to ensure everything is running smoothly and that our production demands are met.’
Another major focus area for Wordsworth Crushing when operating front-line material processing equipment is safety, and the track-mounted LT116 jaw crusher is no exception. ‘The company has operated Metso equipment for over two decades and I have always been impressed by the Lokotracks. They are well-built, cost-efficient, operator-friendly, and have numerous built-in safety features as standard,’ said Mr Wordsworth.
‘Everyone working in the quarrying and mineral products sector has a moral obligation to operate to the highest health and safety standards. The operation of large crushing and screening equipment is often associated with an increase in potential danger to quarry workers, which is why my business, since the beginning, has made personal protection our highest priority.’
Indeed, safety and ergonomics play a major role in the operation and maintenance of Metso machines, and thanks to the Lokotrack LT116’s well-thought-out design all relevant service areas – including jaw crusher maintenance points – are easily accessible and facilitated by an extensive service platform.
Built around the proven Nordberg C116 jaw crusher, the high-performance LT116 is a versatile primary jaw crushing plant that can crush all types of materials from the hardest, most abrasive granites to C&D waste, either as a stand-alone unit or in combination with Lokotrack secondary/tertiary machines and mobile screens.
The C116 jaw crusher shares many of the same features as other jaw crusher models in the Nordberg C-Series, such as swinging motion for easy cavity clearance, a longer stroke and hydraulic setting adjustment, to ensure high throughput capacity/reduction and total control of product size.
Powered by a fuel-efficient Caterpillar C9.3B engine (415hp), the LT116 has a large feed opening of 1,150mm x 760mm and can be equipped with numerous optional features for optimized performance and extended wear life, including a longer, hydraulically folding discharge conveyor, feeder hopper extensions, a magnetic separator, and the latest Metrics remote monitoring platform, which allows central monitoring of the entire crushing fleet’s production and energy consumption.
Optimum transportability and a fast start-up on the LT116 jaw crusher were also key focal points for Wordsworth Crushing when looking for an all-in-one mobile processing solution.
The Lokotrack’s chassis design, with good clearance at both ends, ensures safe and easy loading on to a trailer, making the unit well suited to the quarrying, construction, and contractor segments.
Equipped with Metso’s innovative IC series process control system, aggregate processing on the LT116 can be customized to deliver optimum crushing results. It offers single-button start/stop and features in-built troubleshooting, as well as various parameter selections. All Lokotrack mobile equipment in the same crushing and screening process can also be linked via the Metso IC control unit.
Looking ahead, Mr Wordsworth is clearly excited by the further growth potential for the business and new possibilities and fresh opportunities in the quarrying and construction markets. ‘We are firmly committed to ensuring our mobile processing equipment and earthmoving fleet has the highest standards of safety, efficiency, and sustainability through our ongoing fleet-replenishment programme.’ he enthused.
‘Over the next two years, we will be upgrading and replacing our Metso jaw fleet and Nordberg HP-Series cone crushers with newer Metso products – effectively futureproofing our aggregates processing capability and ensuring we have a modern fleet of front-line contracting machines that is productive, efficient, versatile, and environmentally focused.’
Subscribe to Quarry Management, the monthly journal for the mineral products industry, to read articles before they appear on Agg-Net.com