Bespoke TWS wash plant for Clarence Sands
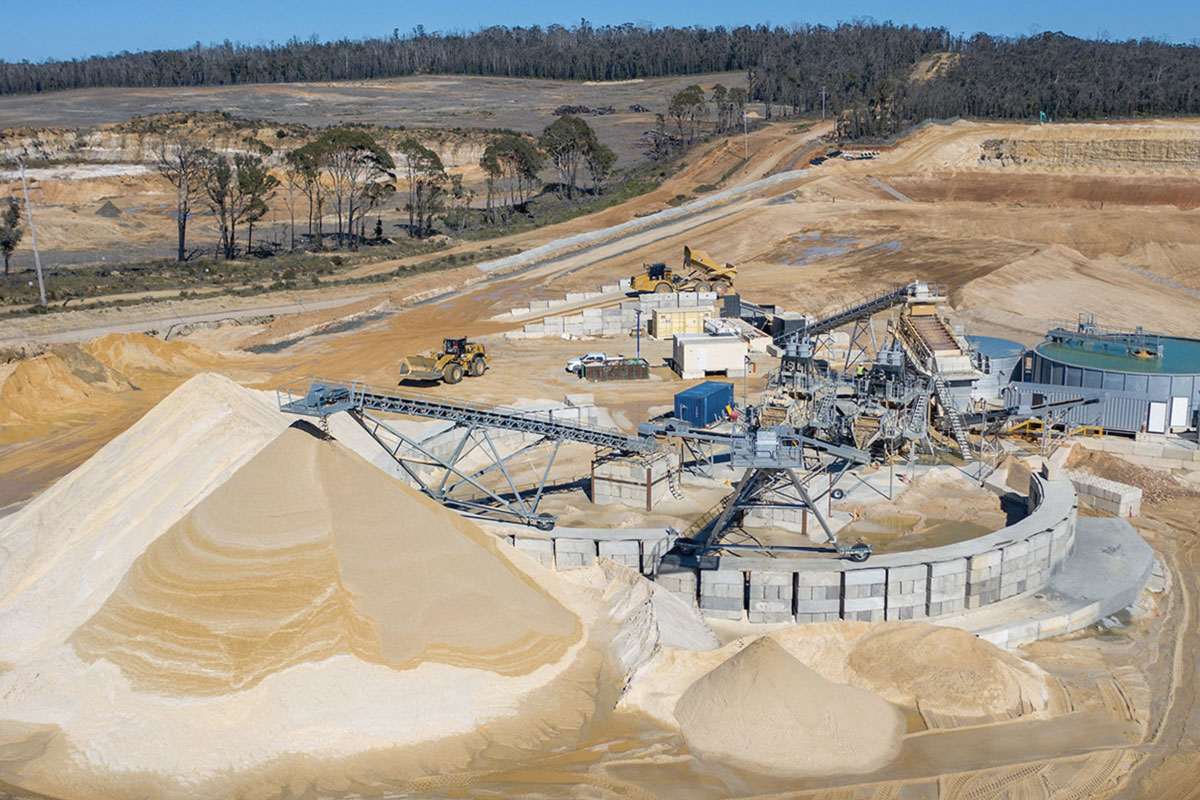
First published in the August 2022 issue of Quarry Management
Terex Washing Systems deliver 300 tonnes/h sand washing plant for new site near Sydney
Terex Washing Systems (TWS) have recently delivered a sand washing plant for Clarence Sands – a newly established operation that is now one of the premium sand quarries near Sydney, Australia.
The sandstone deposit located in the Blue Mountains produces premium-quality construction sand that is washed and classified using a state-of-the-art TWS wash plant. The bespoke design of the plant can produce up to 300 tonnes/h of quality sand and recycles approximately 90% of the water used during the washing process.
The wash plant features an H30 (50-tonne) feeder that receives the raw feed material and distributes it evenly on the main conveyor. Any rock fragments larger than 100mm are removed from the feed by the grid covering the feeder. The H30 feeder also features a hydraulic tipping grid that can be controlled from the loader cab, so that any material stuck on the bars can be cleared.
The feed material on the main conveyor makes its way up to a modular 20ft x 8ft twin-deck rinser screen, which has been specifically designed to handle the tonnage needed for this operation. A total of 19 spray bars give the material an initial rinse as the vibrating screen shakes the sand and stone through the durable polyurethane classification decks. Any large sizes are fed on to aggregate/oversize conveyors for stockpiling as products for sale.
Meanwhile, any sand, silt, clay, or other fine impurities that were present within the feed material are washed to the screener’s split catchbox. TWS catchboxes have adjustable paddles, which assist in blending the correct amount of fines into the coarse fraction, to ensure the required spec is always achievable.
The material is gravity fed into one of two FM 200C sand plants. Each receives a separate split, one coarse sand and one fine sand. For this application the standard units were upgraded to separators, rather than the standard hydrocyclones, to cope with larger volumes of fines, as well as to deal with potential variation in the feed stock.
The separators use centrifugal force to remove the sand from the silt and clay so that it can be transferred on to the high-frequency dewatering screens, which remove the remaining water within the sand so that only 10–15% moisture remains. The sand that is now up to spec is transferred on to a 26m radial stacking conveyor which offers a large stockpile capacity that is well suited to the needs of the customer.
The water that, up until this point, has been used to rinse the feed material and wash the sand within the FM 200C, and has been recovered from the dewatering screen, is pumped into a 17m diameter thickener tank, which allows the silt and clay particles within the sludge to settle at the bottom of the tank, while the clean water weirs over the upper edge for reuse.
Integral rake scrapers aid transportation of material from the outskirts of the tank to the central outlet, to accelerate the removal of sludge from the thickener. This process is further enhanced with the use of a flocculant dosing unit, which doses the sludge on its way to the rake thickener.
No wash plant can do its job without water, which can be a difficult resource to manage in Australia, so TWS advised the customer of the need for a robust water-management system that would be both environmentally friendly and save on running costs.
Neil Rooney, engineering manager with Terex Washing Systems, explained: ‘Over the last number of years, we have developed our water-management product range to the point where we’re confident we can meet the needs of any application.
‘Our wash plant for Clarence Sands is a good example of how an efficient water-management system can take an operation to the next level. For Clarence Sands, settling ponds maintenance is drastically reduced, freeing up valuable machinery and time.’
According to Terex Washing Systems, their engineers were faced with some unique challenges during this project but managed to overcome them to deliver a wash plant that meets the tonnages required by Clarence Sands.
For more information, visit: www.terex.com/washing/en
- Subscribe to Quarry Management, the monthly journal for the mineral products industry, to read articles before they appear on Agg-Net.com