Barrasford Quarry Goes Mobile
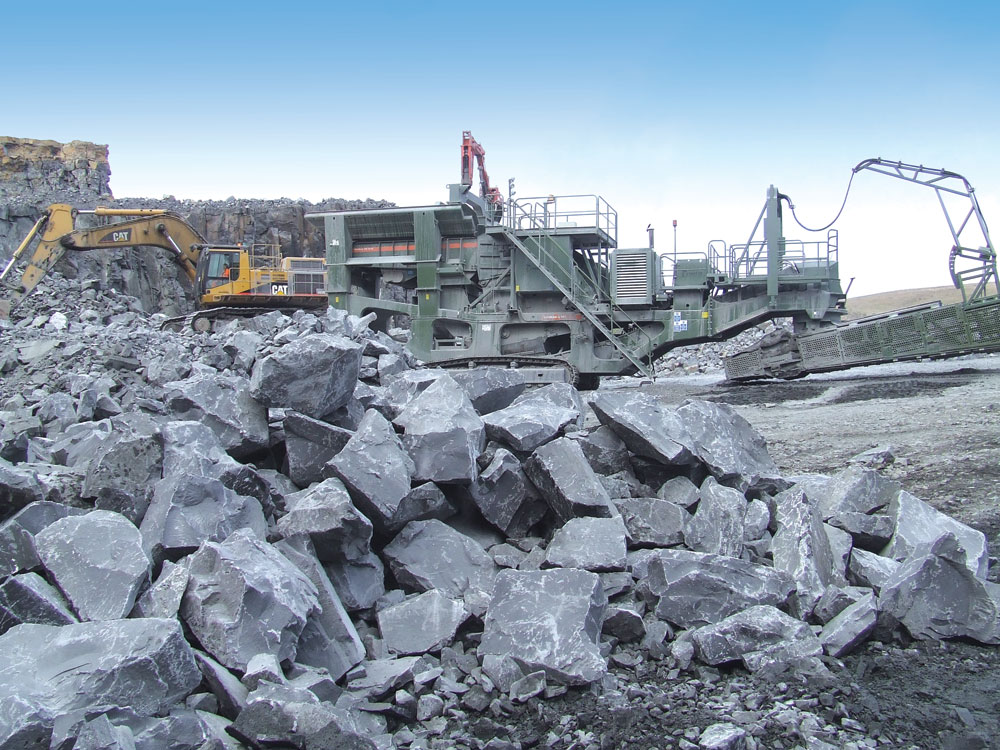
Metso Minerals help Tarmac overcome a number of challenges
A Lokotrain comprising an LT140 track-mounted mobile crusher, a pair of Lokolink mobile conveyors and several field conveyors is helping Tarmac Quarry Products to convert from static to mobile crushing operations at Barrasford Quarry in Northumberland.
The Lokotrain, which has helped reduce manpower and replaced a pair of static crushers and a rigid dumptruck haulage fleet at the 135ha site, has required considerable interaction between Tarmac and engineers from both Metso Minerals (UK) Ltd and from their parent company in Finland.
Extensive reserves
Located on land owned by the Duke of Northumberland, Barrasford Quarry boasts reserves of around 45 million tonnes. It has been in operation since 1880 and today produces around 500,000 tonnes per year of which around 85% is quartz dolerite (whinstone) for use in Tarmac’s road products. The remaining 15% comprises blue limestone for use as aggregate.
The quarry is currently 20m deep and there are plans to lower the base still further to around 35m. Material is won by blasting which takes place every three weeks, each blast releasing around 30,000 tonnes. There is very little environmental impact with regard to noise and dust as the quarry has no immediate neighbours, however, the site is monitored and water suppression is used at the face.
Benefits of mobility
The 110-tonne LT140 track-mounted mobile crusher was purchased to replace a pair of static jaw crushers that had clocked up more than 30 years’ service at the site.
‘We bought the LT140 in December 2006 to replace a pair of ageing static jaws and it worked for eight months as a stand-alone machine,’ said quarry manager Ed Dixon. ‘But, having experienced the benefits of mobility, we knew that we could achieve even greater levels of productivity, safety and cost-savings by making the entire operation mobile with the purchase of the Lokolink conveyors.’
In a single step, the arrival of the Lokolink conveyors and the field conveyors effectively replaced a pair of Cat 771 off-highway trucks and reduced the need for manpower at the face.
However, the move to mobility was not without its challenges. The floor of the quarry slopes at over 10° (east to west) to allow for the working of the beds, which required some additional input from Metso engineers in the UK and Finland.
‘This set-up was the first of its kind in Europe on such a significant slope, so the chief designer and engineers from Finland supervised the installation,’ explained Mr Dixon. ‘Even then, there were some initial issues with manoeuvrability. At first, it was taking more than 3h to get the crusher and the links just right. Now it takes a maximum of half an hour, which is just as well as we’re moving the entire train every other day.
‘We are very pleased with the set-up of the machines. Metso took a lot of trouble to ensure this installation was right. As a result, the crushers work far more efficiently and flexibly than ever before, and we’re regularly exceeding productivity levels of 400 tonnes/h.’
Minimizing impact
The quarry has an ongoing biodiversity programme to restore the land to its natural state and Tarmac have even consulted world-famous botanist David Bellamy to safeguard the future of the site.
According to Mr Dixon, when the quarry is exhausted it will be allowed to flood naturally, and there are long-term plans to restore the site to natural whinstone grassland. Indeed, this process began in 1996 and a large expanse of the western edge of the site has already been filled, graded and replanted.
Until then, Tarmac are using some unusual methods to reduce the visual impact of the quarry operations. ‘Part of the planning application to bring the LT140 on site involved minimizing the visual environmental impact, so the crusher and the links were all painted a drab green colour,’ said Mr Dixon.
‘The local population took a lot of convincing that the army weren’t involved in some secret enterprise on the site. But drab colour aside, I can’t fault the Lokotrain or the support provided by Metso. The mobile plant is far more productive than our original static machines and Metso worked tirelessly to ensure that the installation fully satisfied our very specific needs.’