Automation In Crushing
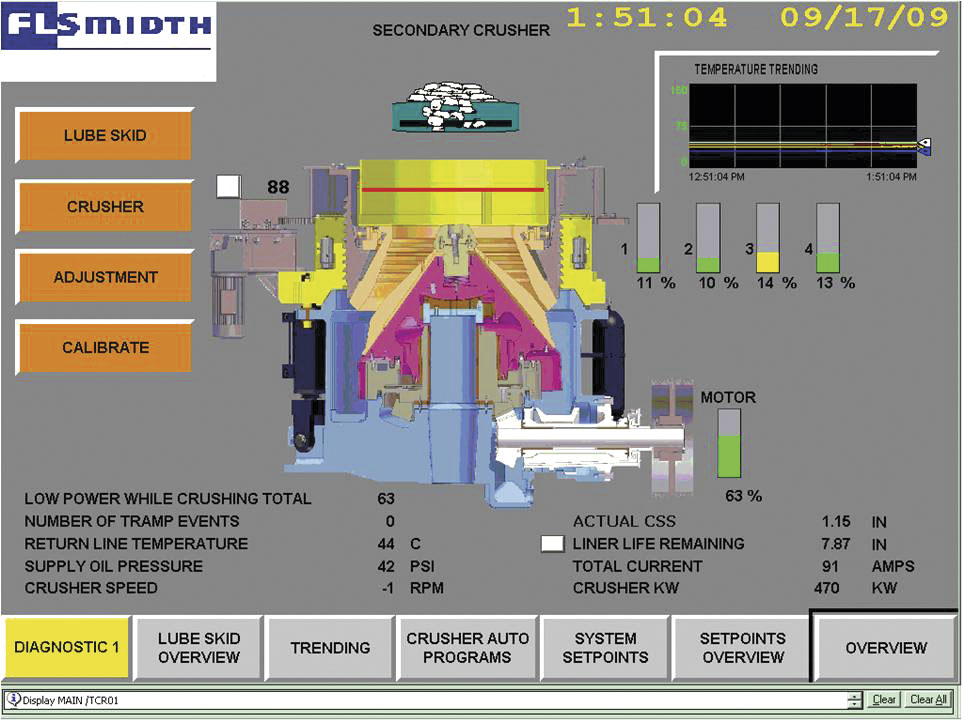
Automated systems offer greatly improved levels of plant control and support but such systems must themselves receive proper attention and maintenance
By Garrett Forkner, FLSmidth Excel, and Andy Rieland, FLSmidth Inc
It is safe to say that some of the greatest advances in aggregates processing equipment in recent years have been made in the automation arena. While the ability for producers to automate functions such as ticketing and invoicing has been around for at least 30 years, the past 10 years have seen tremendous progress in technology that allows for better equipment performance and more proactive equipment maintenance. Automation technology has improved plants’ abilities to produce material with more consistency, better quality and greater productivity. At the same time, real-time automated equipment monitoring helps reduce downtime by tracking maintenance needs. Indeed, there are even automated systems available today that can make some repairs remotely and automatically.
In short, automation has made all our lives and jobs easier.
A constant watchdog
In the past producers only added automation capabilities to their plants as part of a new equipment acquisition. Today, however, existing equipment can often accept automated controllers as a retrofit. Automation typically provides anything from basic machine control to a high level of process control to maintenance and service control.
Most companies, when seeking information about automation, are actually looking for assistance in maintaining the plant. At the most basic level, an individual automated plant will monitor operational hours to track scheduled maintenance.
However, depending on the package selected, an automation system will also allow the producer to oversee other things. A cone crusher package, for example, will allow the system to also oversee parameters such as differential pressure, coolant levels and filter condition in the coolant system, and temperature and flow differentials in the supply and return lines. By monitoring the level of lubricant in the system, the automation software can help maintain required temperature parameters. Cone crusher automation can track total motor hours, hydraulic pumps, lube pumps, main drives and bearing temperatures for longer bearing life. If the cone crusher is a bushing-type model, the automation system can often measure for bushing wear to prevent catastrophic failure.
With regard to the provision of crusher maintenance, there are currently automation packages available for gyratory crushers that can include functions such as automated greasing systems, which will grease the bushings as a system sub-control. Moreover, because a primary gyratory crusher is sometimes located hundreds of yards or even miles from the rest of the plant, it can be configured to run independently or tied in to the rest of the plant, based on the producer’s needs. Its protective functions and alarms can still be set to provide alerts in the main control room.
In terms of operational controls, an automation system can manage the feed to the processing equipment and protect crushers from overload situations. Usually, it will handle the latter by sounding an alarm, correcting the loading or shutting down the equipment. The automation system can track pressure for clamping and the tramp release system. Most systems will automatically adjust crusher settings for production needs or to compensate for liner changes, and they will alert maintenance personnel when it is time to change liners. If the automated sensors detect problems, they can be configured to shut down the equipment, or they can work to eliminate the problem without shutting down the equipment by sensing variables and making adjustments.
With all of these capabilities, it might seem that an automation package would render human operators obsolete. But today’s automation packages really cannot replace the operator or field service personnel. They are, however, a big assistance in pinpointing and narrowing down the causes of problems. Additionally, automation systems provide safety benefits because remote sensing typically allows for measurement without contact. Even a basic automation package helps with troubleshooting because the data collected can (and should) be checked regularly for trending, which can be interpreted to pinpoint an issue. For example, if the operator notes that the system re-pressurizes repeatedly, he or she should realize it is not working properly and schedule a shutdown for service.
Improving performance and the bottom line
Automation packages can also help to improve overall plant performance. By logging production, the system allows the plant operator to track productive and unproductive time, so that he or she can analyze the data and compare it to the material produced. Any data can be trended, interfacing off the process equipment to provide operators and supervisors with information such as maintenance needs, schedules and downtime hours. The operator can then adjust the plant for better performance. Historical data can be tracked either remotely or on board for higher-level management of overall site performance. All of this also helps when tracking the bottom-line cost of an operation.
In essence, real-time monitoring maximizes productivity and reduces downtime by helping to identify bottlenecks, tracking equipment performance, scheduling maintenance and troubleshooting problems. From a proactive maintenance standpoint, an automated system helps schedule and plan preventative maintenance. From a service standpoint, trending helps operators to troubleshoot then plan a plant shutdown and order parts before a failure occurs.
IT issues and advances in technology
Advances in technology have created the ability for automation manufacturers to visit a plant’s automation system remotely to help maintain the software portion of the system. While remote service capabilities are not meant to replace a plant visit, remote software maintenance allows the manufacturer to provide system surveys, software product updates, software extensions and troubleshooting.
As is often the case with home computers, developments in information technology (IT) can create issues, rendering older software and hardware obsolete. Changes in software seem to happen at an alarming rate and it is important to keep PC and Windows-based controllers up to date with software and, less frequently, hardware, updates.
It is important to make sure that software updates are followed and regular checks for security risks are provided – to avoid the risk of viruses, hackers or even accidental harm, such as an employee downloading a game. The risks grow when the plant is connected to an intranet or the Internet. In the case of the latter, manufacturers usually recommend the implementation of a firewall.
Also, as a rule of thumb, Microsoft seem to come out with a new Windows operating system approximately every four years. New functionalities and features might mean there is a need to update system software or hardware – before it becomes obsolete.
The advantage of remote service capabilities is that the customer avoids downtime and the cost of a field service call, while usually realizing higher performance of the automation system. A DSL, fibre-optic or cable Internet connection is best for remote access to the automation system, although this is not always possible given the remote nature of some aggregate operations. In this case, a connectivity solution could be provided through a radio link or satellite connection.
System maintenance begins with the order
Without doubt, an automation system helps to maintain aggregate processing equipment, but in a rugged, arduous and dusty quarry environment, what is the best way to maintain the automation package itself?
Maintenance of the automation system begins at the ordering stage. Producers should be familiar with the location and operating climate within which the system will be expected to work. This information should be specified and provided to the automation manufacturer or contractor so he or she can design the correct type of enclosure for PLCs (programmable logic controllers) and terminals. The MCC (main or mobile command centre) building can also be protected against the environment. Temperatures should be kept in mind for high-end and low-end tolerances. Additional environmental control features can be added to the system, such as heaters for winter working and air-conditioning for hot climates. This could indicate a need for specific ductwork.
Also, when specifying the order, producers should bear in mind where the HMI (human machine interface) will be located – whether in the central control room or in a remote area. Location can determine a need for a climate-controlled enclosure. While it might seem that a PLC would be more cost-effective, future needs should be borne in mind when placing an automation order. For example, a touch-screen monitor will be easier to swap sometime in the future than a manual panel that will need diagnostics and greater work at replacement.
At the planning stage, good communication with the system developer will ensure the installation takes place more smoothly for everyone involved – ie when both parties not only know what is on site and the facility’s climate, but also what is being integrated with the automation. Good communication will ensure return on investment, ultimately protecting equipment assets down the line.
Installation interests
Good housekeeping should start with the installation. For purposes of smoother installation and easier inspections over time, the installation contractor should clearly labels all cables. While it might take a little longer to lay all the cables neatly, this will pay off in the long term if a need arises for troubleshooting.
Today’s sensors are very rugged sensing elements. Different sensors are made for different environments, so, as long as the designer/manufacturer knows the environmental parameters, the system’s sensors should be designed to withstand the daily conditions in any given setting. However, no matter how rugged a sensor might be, misuse or abuse will cause failure. Something as simple as a hose rubbing against a sensor limit switch will ultimately ruin the sensor. During installation it should be ensured that sensors are placed in an area that will minimize their contact with the environment, albeit accepting that there are some limits as to where sensors can actually can be placed. An enclosure for the sensors is the best scenario.
Regular maintenance tips
Daily: As part of a pre-startup routine, verify that the system is reading and providing information; verify that there are no issues between the sensor and the HMI system – ie the computer. Any parameter that might cause the machine to shut down should be checked daily – eg lubricant pressure.
Weekly: Monitor trending. For example, if a bearing temperature is rising, it could signal impending failure. Schedule the maintenance before it causes unplanned downtime. Check for dust build-up, corrosion and other environmental effects on sensors, controls and equipment units. If the controls and/or sensors are dirty, clean them.
Monthly: If control enclosures are exposed to any sort of climatic extremes (heat, cold, moisture etc) a thorough visual inspection should be carried out on a monthly basis. General housekeeping should also be borne in mind as time goes on. All cables and lines should be protected, not only from dusty environments, but also other equipment. For example, oil dripping on cable labels will disintegrate the labels and render them unreadable when the time comes for troubleshooting or maintenance.
Annually: Every installation is different because every application is different. From the size of the material to be processed, to the environmental and climate conditions, all of these parameters work together to create different conditions for the automation system that helps to run the processing equipment. Most manufacturers recommend an annual preventative maintenance visit for automation systems. During a maintenance visit, the specialist will test system’s functionality, revise configurations if necessary, adjust and calibrate the system, update the software and provide additional training for the daily system users.
Conclusion
Producers are adding automation to their operations – not only with new plants, but also by retrofitting systems to existing operations. Automation can provide anything from basic machine control to a high level of process control to maintenance and service control. Automated packages help improve the bottom line through real-time monitoring, maximizing productivity and reducing downtime by tracking performance, scheduling maintenance and troubleshooting problems. It is important that the automation package is installed with the correct specifications for climate and environmental protection; and by following recommended system checks, operations can ensure their systems function properly for the long term with minimal problems.
For further information tel: +1 262 968 9095 or visit: www.FLSmidth.com/Raptor