The Direct Approach
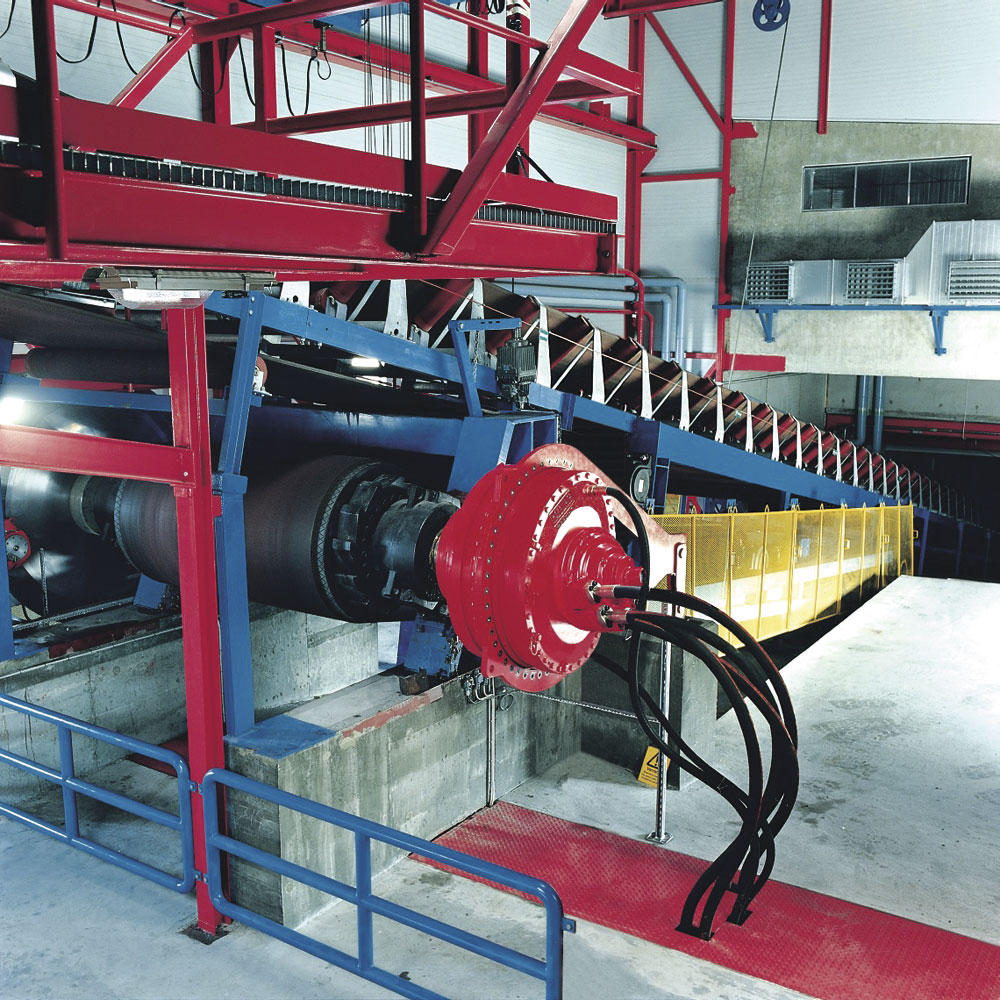
Brian Holmes, marketing and support manager with Hägglunds Drives, outlines the basic technology, characteristics and effects of the direct hydraulic drive approach to feeders and conveyors
When faced with a decision about low-speed drives for industrial plant and equipment, such as apron feeders or conveyors, there is a tendency to follow the traditional line of thinking and to opt for some kind of electric motor and a high-ratio gearbox selected for the final speed and torque required. This often requires other elements in the drive train in order to complete the installation, such as couplings, clutches, pulleys, belts and foundations. Sometimes these arrangements can be quite complex with high design, installation and maintenance costs, and with the risk of something going wrong. If variable speed is required, the situation becomes even more complex.
There is, however, an attractive and simple alternative – the use of direct hydraulic drive from a single source, which offers a robust and versatile system that can be easily understood and which is simple and straightforward to install on new or retro-fit projects.
Hydraulic motors have been used to drive all kinds of plant and machines for many years. Their excellent controllability, flexibility and user-friendly nature, together with an unrivalled power-to-weight ratio, have always been and are still powerful and attractive reasons for using fluid power.
Previously, a limitation on hydraulic drives was the size and power capacity required for large feeders and conveyors, but hydraulic motors have developed over the years and there is now a very wide range of direct drives available in small steps up to 250 litres/rev and 2,000kW in power from a single drive motor, completely eliminating the need for gearboxes and other awkward components on most applications.
It is now very easy to select a drive motor to give the precise torque required at a suitable operating pressure to give efficient operation. Hägglunds motors, for example, have an overall efficiency of around 96% when operating at or around their optimum torque and speed. To achieve overall system efficiency, the power unit has to be considered too, but usually this is comparable with other variable-speed systems. The great advantages of hydraulics, with their inherent simplicity and flexibility, can now be applied to heavy-duty industrial applications operating 24h a day, seven days a week, where efficiency, reliability and long life are prerequisites.
To choose a drive motor it is necessary to specify the torque required (Hägglunds can help establish this by analysing various factors) and then select a motor from the wide range available to give the torque needed at a suitable pressure for the life required. It is then necessary to select a power unit with a pump sized to give the flow needed for the speed required, or with an electric motor, to give the power needed including the efficiency of the drive system as a whole.
Hydraulic technology offers full control of power, torque and speed, ie all the aspects of a drive system. The use of axial piston pumps to supply variable oil flow to the drive motors in response to an electrical signal provides variable speed, which is becoming increasingly important in modern plants to improve the efficiency of processes. And by controlling pressure, it is possible to directly control the torque to protect the driven machinery (chains, sprockets, belts etc) from unwanted forces, thereby reducing the risk of failure and minimizing wear rates and damage. Both speed and torque feedback can be precisely and simply controlled and integrated into power control. Thus, complete control of the drive is available bringing high functionality to the drive and, therefore, to the plant.
On drives using a high-speed motor and gearbox, a very high moment of inertia is evident. If the machine is liable to shocks, such as when a hard object becomes jammed on a chain feeder, the transient forces experienced could damage the machine and the drive, causing costly repairs and lost production time. A direct hydraulic drive in the same circumstances would stop instantly, keeping everything safe. The forces, limited by low inertia and fast-acting pressure controls, would be kept within design limits so no damage and less wear would be caused, giving higher reliability and, therefore, lower maintenance costs. A simple pressure signal can be used to stop upstream plant to prevent flooding and to alert operators to the problem so local manual controls, such as the Hägglunds Spider control unit, can be used to relieve the situation. The Spider control provides drive control, start/stop logic and system health monitoring, all with easy customer interfacing.
Hydraulic drives are charged with oil, ie ‘cushioned’, and can therefore be applied on arduous applications involving vibrations and shock without encountering problems.
Variable speed
With variable-speed electromechanical drives, the torque at low speed is often time-restricted or may be reduced significantly. However, with a Hägglunds motor, for example, the mechanical efficiency of the motor is very high and high torque can be maintained indefinitely, even when stalling. There is no need to compromise the machine function; whatever speed is required, the full driving force is always available, even two or three times the nominal torque at start-up, if required. On many types of machine this can mean the difference between starting up without problems or not being able to start, resulting in hours of lost production.
To overcome this starting torque issue, in some cases an electromechanical drive is oversized, resulting in more expense, less efficiency and higher running costs.
Versatility
Drive direction is also not a problem for hydraulics, because there is no reliance on an electric motor; the drive can be reversed instantaneously and smoothly with a simple electric signal to a piston pump. This is very useful on applications such as shredders where jamming can occur and where reversing, particularly with full torque at zero speed, can un-jam the machine and keep production flowing. These characteristics are also important on constant-tension systems where the drive has to maintain a constant tension on a wire rope using a winch. These systems have been employed on conveyor belt tensioning systems on the surface and in tunnels and underground coal mines, thereby improving belt life by eliminating belt slip, particularly during starting when a higher belt tension can be applied.
Hydraulic drives, by their very nature, have perfect load-sharing characteristics, which is useful on a common shaft, drum or girth gear using multiple motors. The pressure from the common pump unit naturally provides equal pressure to the drive motors, effectively sharing the load, whereas two or more electromechanical drives sharing would involve some form of electronic synchronization, which can be complex and may lead to problems and vibrations.
Compact and space-saving
Conventional low-speed gear train drives are very heavy and can take up a lot of space around a machine, thus inhibiting maintenance. Direct hydraulic drives, however, mount directly on to the drive shaft of the machine. There are no foundation requirements and no alignment problems. The power unit is positioned conveniently out of the way with just the hydraulic pipework connection to be taken care of. The whole machine look and concept can be transformed, improving machine performance, reducing weight and allowing better operator access. This reduces maintenance effort which, in the case of hydraulic drives, really only involves changing the filter elements and checking the oil condition. Noise levels are also lower, usually well inside normal regulations.
Operating environments
If the environmental conditions are particularly hot or cold, oil flushing can be used to either cool or warm the motor to protect it from extremes of temperature, and the power unit can also be provided with heaters and coolers, as required. Rugged designs can be exposed to dusty, humid and even underwater conditions, while for explosion-proof areas the standard hydraulic motor is normally acceptable. Hägglunds can, however, provide power units to ATEX requirements if necessary.
Power electrics
The electric motors used with hydraulic drives are standard squirrel-cage induction motors that run efficiently at constant speed. The pumps are controlled by a simple electrical signal and the customer interface is simple and easy to understand using the Hägglunds Spider controller. There are, therefore, no problems with regards to EMC or distortions on the power supplies, which can be a major and costly concern with AC variable-speed electromechanical drives.
Hägglunds motors are developing all the time and, thanks to probably the largest hydraulic motor development laboratory in Europe, the size of their drive motors has been reduced significantly over the years to provide some of the most compact units on the market.
Some weaknesses of hydraulic drives
The Hägglunds hydraulic motor design is heavy duty as standard and, therefore, may not be competitive on price if applied on low-power, light-duty, fixed-speed applications, unless there are other issues to consider, such as the need for special duty or drive techniques, multiple drives from a common power unit or difficult environmental conditions.
In some applications, high inertia is a positive benefit, such as on crushers processing very hard materials where a hydraulic drive would not be as effective; or where the exact synchronization of drives with varying loads and speeds is required under all circumstances, for example on steel rolling mill tandems; or where the gearbox has to be designed into the actual machine it is driving, thus incorporating the sheer bulk of the gearbox into the structural integrity of the machine, eg crushers and extruders.
Hydraulic systems have, in some cases, been associated with leakage, although since gearboxes also need to be lubricated, they too can be a source of leakage. Nevertheless, with good design practice and regular attention, leakage can be eliminated or at least reduced to infrequent episodes at a satisfactory level.
Summary
Direct hydraulic drive provides a variable low-speed drive solution with a number of unique features and, when properly applied, offers a very reliable system with real competitive advantages. It can easily be up-rated and adjusted to suit changing requirements, and on critical applications, eg cement kilns, it can provide redundancy in the event of a pump failure, thus eliminating the likelihood of stopping the machine. Several drives and auxiliaries can be supplied from a single power unit adding flexibility to the options available. The layout, types and permutations of power units are endless, but companies such as Hägglunds Drives tend to use modular systems with standard components and controls that are well matched specifically for drives, and can also take full responsibility for the complete drive, which offers security advantages for the end-user and allows quick delivery when necessary.
Hägglunds Drives offer a wide range of hydraulic drives that are increasingly being used in low-speed applications in the quarrying and mining markets, due to their improved suitability and basic technology, which suits the industry very well. The company can now provide feeder drives suitable for small belt feeders right through to large apron feeders moving up to 12,000 tonnes/h in massive open-cut mining operations, as well as belt conveyor drives suitable for relatively small units through to very long, high-powered conveyors using multiple drives. Other successful applications include bucket-wheel reclaimers, shredders, mills, mixers, winches, drilling rigs, kilns and crushing plant.
Key characteristics of hydraulic drives
- Low inertia and fast pressure controls allow instant response and control of forces.
- Variable speed adjusted to suit conditions to optimize plant performance.
- Full torque effectively available from zero to maximum with no limits to stops.
- Shockproof capabilities cater for all heavy-duty applications as standard.
- Perfect inherent load-sharing between two or more hydraulic motors.
- Environment-proof so can be applied in almost any conditions: hot, cold, dusty etc.
- Compact and weight-saving simple drive arrangement directly on the driven shaft.
- No problems with EMC, no distortions to power supply and no complex electrics.
- Redundancy or standby where necessary in critical applications.