Microwave Blockage Detection Technology for Quarries
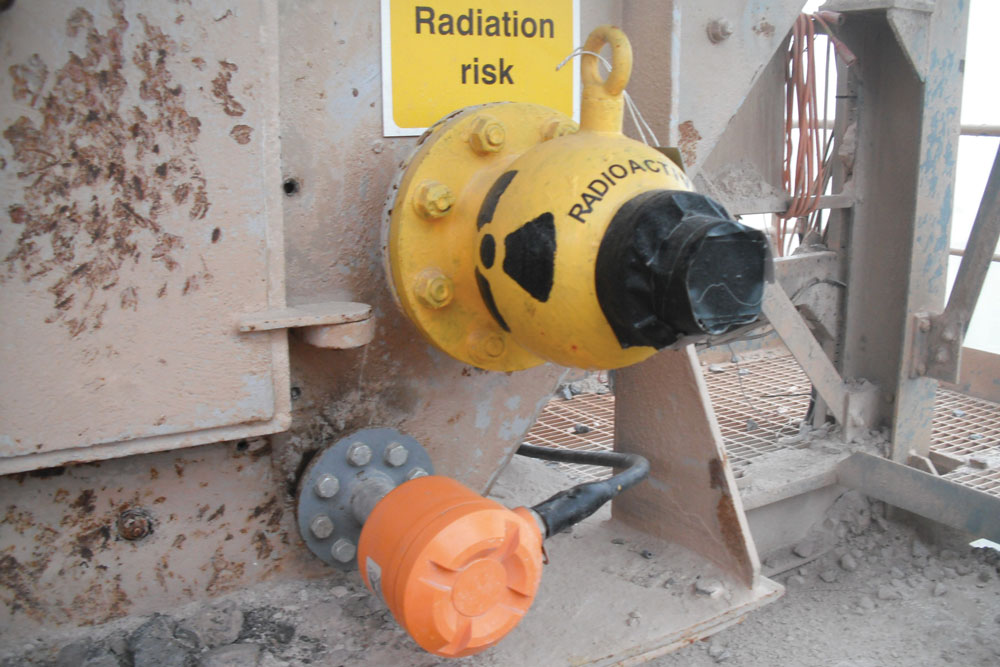
First published in the August 2017 issue of Quarry Management as The Non-Nuclear Option
Nuclear-based technology has long been thought as the only blockage detection technology robust enough to withstand harsh quarry and mining environments, but its radioactive nature means it is far from ideal. Level measurement specialists Hycontrol outline a robust and cost-effective alternative
It is well recognized that transporting irregular-shaped bulk solid materials over long or short distances presents a number of operational challenges in the quarrying and mining industries. Primary crusher crash boxes, conveyors, transfer lines, inlet/outlet chutes and inlet hoppers can all be prone to blocking, bridging or jamming, resulting in severe site problems, including: lost production; crippled/damaged plant; lost material; and extended/expensive downtime.
The reliable early detection of an imminent blockage in a chute before it reaches a critical level is, therefore, of major importance.
Nucleonics
Traditional optical methods for detecting blockages, such as proximity through-beam sensors, often cannot cope with the hostile environments encountered in these applications, where the extreme dust and high vibration culminate in repeated failures when sensitive optics are damaged or become coated in dust.
As a result, nucleonic devices have historically been considered the only reliable form of instrumentation capable of providing effective blocked chute detection in such demanding conditions. Although nucleonics provides technically competent technology, this measurement technique requires a radiation source from a radioactive isotope, such as caesium-137 or cobalt-60, for it to detect the presence of material in the hopper.
The radioactive source must be specially shielded so that radiation is only directed through the hopper wall towards the product. Levels of radiation detected on the opposite side of the hopper are then used to determine whether there is a blockage or not.
These devices are very expensive to install and, although considered relatively safe to operate, there is still concern about safety aspects and the long-term environmental impact. Not surprisingly, controls on the use of the radioactive devices are extremely strict and extensive training is required to operate them. They also need initial licensing and have to be periodically verified, either by the manufacturer or an authorized external authority.
Microwave – the safe, low-power alternative
Hycontrol’s new-generation of microwave switches is proving to be an extremely reliable, robust and cost-effective alternative to nucleonics, offering operators a 100% safe solution for blocked chute detection.
The range of microwave level switches available provides a simple non-contact, non-intrusive option suitable for many solids applications. A typical installation consists of a transmitter and a receiver mounted facing one another on either side of the chute.
During operation, the transmitter emits a continuous, low-power microwave beam (24GHz) to the receiver and an output relay is energized or de-energized when this beam is obstructed by the material being monitored.
The switch trigger point is determined by the amount of microwave energy received and can be adjusted to cater for different products and applications. As microwaves easily penetrate any surface contaminants, the switches are particularly suitable for applications where there can be high build-up of material on the inner surfaces of the chutes or vessel walls. This also means this switch technology is immune to problems with airborne contaminants such as powders or dust.
As microwave power levels are well below any required industry standards, the device requires no special procedures for its operation and use. A wide range of flanges and connections make the range extremely easy to fit to new or existing installations, utilizing original process connections if required.
A key advantage of microwave technology is its ability to effectively see through low-dielectric materials, including refractory bricks, ceramics, plastics and polymers. This means that low-cost ‘sacrificial’ windows can be fitted into the sides of a vessel or container, keeping the process closed and not causing disruption to material flow.
The probes can then be mounted at some distance from the application, well away from damaging vibration and abrasion. The switch is adjusted so that the beam passes unaffected through the windows and falling products – only being triggered if the material being detected builds up and permanently breaks the microwave beam. If the windows suffer any physical damage or wear, they can be simply replaced, leaving the switch intact.
The potential health dangers, high costs and strict licensing requirements associated with the use of nuclear sources in industrial environments are extremely onerous. The straightforward cost comparisons alone are said to give microwave technology a favourable five- to ten-fold advantage, but additional costs of ownership for the nucleonics system have to factor in the added mandatory site security, strict operator training, provisions for checks from the authorities and annual licensing fees. Also, the nuclear source will degrade over time and its disposal must be carefully controlled, all of which increases the cost of ownership.
Detecting blockages in crushers
Primary crusher crash boxes at quarries are a vital part of a crushing process and it is essential that adequate warning is given to any potential blockages before they result in costly plant downtime. However, given the ferocity of the environment where huge rocks are being crushed, peripheral equipment is constantly being subjected to extreme vibration, impact damage and abrasion.
To overcome these problems in one such application, Hycontrol mounted the microwave switch components up from the floor beneath the crusher head, 200mm back from the walls to prevent the units being shaken to pieces by the intense vibration. A 60mm window made in each side of the crash box allows the microwave beam to pass from one side of the box to the other. In the ‘un-switched state’, the receiver detects the narrow beam from the transmitter. If the path of the beam is permanently interrupted by a build-up of material in the crash box, the internal relay is triggered, initiating the alarm.
Maintaining critical measurement systems
Given the harsh environments that blocked chute switches and other level measuring equipment is expected to work in, regular structured and preventative maintenance is essential. Unfortunately, all too often only cursory visual maintenance is carried out on critical equipment, exposing sites to potential safety hazards as well as premature and costly breakdowns.
All critical-level components should be independently tested and calibrated on a regular basis. A well-designed level system should take this testing requirement into consideration so that maintenance work can be carried out effectively and safely. If telltale signs of possible problems are uncovered during servicing; the root cause should be investigated and rectified.
Choosing the correct level equipment and ensuring it is professionally installed in the correct location are vital for the long-term reliability of quarrying and mining sites. It is now clear that microwave technology offers a reliable and cost-effective alternative to aging nucleonic systems. In parallel, a structured maintenance programme is essential to prevent unwanted and costly breakdowns, ensuring that new equipment continues to provide optimum performance.
For further information visit www.hycontrol.com
- Subscribe to Quarry Management, the monthly journal for the mineral products industry, to read articles before they appear on Agg-Net.com