Martin Engineering supply conveyor belt cleaners to TCI Manufacturing and Equipment
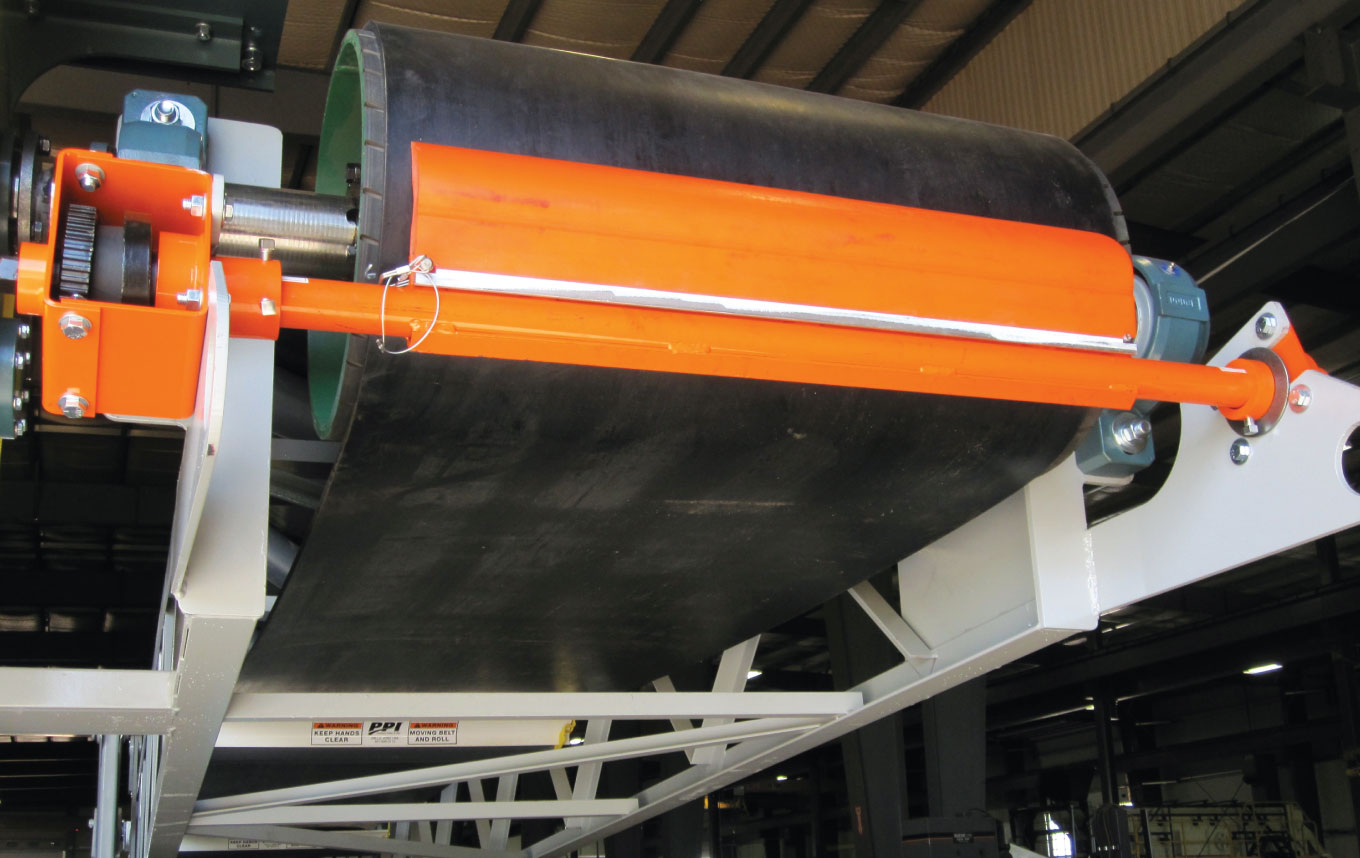
First published in the October 2013 issue of Quarry Management as Below the Belt
Midwest manufacturer specifies high-efficiency belt cleaners from Martin Engineering for standard and custom-designed conveyors
TCI Manufacturing and Equipment, Midwest-based manufacturers of innovative materials handling equipment, are specifying high-efficiency belt cleaners for their standard and custom-designed conveyors in order to deliver premium performance and longevity, even in difficult service environments. The company includes one or more belt cleaners from Martin Engineering on every model in its broad line of stacking conveyors, transfer conveyors, barge loaders, trippers and floating conveyors, as well as its specially engineered designs.
‘We have a reputation for durable, high-quality equipment, and we apply that mindset to all components,’ explained TCI’s president, Mike Maynard. ‘We specify Martin Engineering belt cleaners to deliver reliable and efficient cleaning over a long service life, and our customers appreciate the easy removal and replacement when it comes time for maintenance,’ he said.
TCI have been supplying Martin Engineering belt cleaners as OEM equipment for more than a decade. Regardless of the type or size of the conveyor, TCI equip all of their models with the Martin PV Cleaner as a primary cleaning blade.
The durable, one-piece construction contains approximately 20% more urethane than comparable primary cleaners, yielding a better life and longer service intervals, despite challenging service conditions. The aggressive design is able to remove even wet, sticky sand from belts 18in (450mm) to 72in (1,800 mm) in width.
Engineered to simplify maintenance and reduce costs, the mounting system delivers ‘no-tool’ replacement, as the blades are simply dropped into place and secured with a wire lock pin. ‘This cleaner uses an aggressive angle of attack to the belt for improved cleaning efficiency,’ explained Dave Mueller, senior product specialist with Martin Engineering. ‘And the quick-replacement feature means never having to deal with corroded bolts or damaged fasteners during blade changes.’
The PV Cleaner can be fitted with a number of different urethane blades to suit specific operating conditions, including high temperatures or chemical/solvent exposure, as well as a low-adhesion formulation for tacky materials. They feature Martin Engineering’s patented constant-angle radial pressure (CARP) design for consistent cleaning throughout all stages of blade life. The specially engineered curved blade maintains the same contact angle, even as the belt wears, helping to retain cleaning efficiency.
When a customer’s application requires a secondary belt cleaner, TCI typically install the Martin Durt Hawg DH2, an effective, economical design with urethane arms to absorb the forces of passing belt splices, resulting in stress relief for both the belt and the cleaning edge. Available with tungsten carbide, stainless steel or mild steel inserts, the Durt Hawg can also be fitted with different blade formulations to match specific materials or conditions. It is suitable for use on belts from 18in (457mm) to 96in (2,438mm) in width.
‘Our customers have been very satisfied with the Martin belt cleaners,’ said Mr Maynard. ‘We install them on everything from the most basic transfer conveyors to the most complex custom-engineered designs.
‘There are three primary reasons,’ he continued. ‘Number one is quality and performance. We’ve always been satisfied with the Martin product line. There’s also a loyalty factor. We believe in working with suppliers who have the same values we do, and loyalty is a character trait that we value very highly. Proximity is an added benefit: Martin Engineering are close enough to us that we can quickly obtain components in an emergency.’
As a long-standing customer, TCI have had occasion to enlist Martin Engineering’s extensive technical support network, which can be critical in solving problems for customers in a timely fashion. ‘They are always ready and available to assist us when an issue arises,’ said Mr Maynard. ‘They will travel to a customer site to investigate problems and help us address them. We appreciate the fact that Martin stand behind their products and work with us to achieve complete customer satisfaction. It’s a relationship that has been very valuable to us over the years.’
Replaceable belt-cleaner tips
Meanwhile, in a move designed to reduce landfill waste from worn-out conveyor belt cleaners, while reducing labour time and the safety risks associated with blade changes, Martin Engineering have recently announced a new family of replaceable tips to maximize the amount of usable material on each cleaner blade.
Introduced in direct response to customer input, the replaceable belt-cleaner tips have increased wear life in secondary cleaners by as much as 50%, while cutting replacement labour time roughly in half. Also, because the new tips are pinned in position and require no hammers or other tools to remove and replace, the risk of injury during service is significantly reduced.
‘We were looking for a way to reduce the amount of urethane going to landfills from worn-out cleaners,’ observed Martin Engineering’s global research & development manager, Adam Childs. ‘At the same time, we wanted to find a way to simplify blade replacement, helping customers reduce or eliminate injuries during the replacement process and shortening maintenance times. The new blade tips accomplish both of these objectives.’
Mr Childs cited as an example one of the company’s heavy-duty primary cleaners. ‘The standard design has more than eight pounds of urethane in each blade,’ he explained. ‘Approximately one-third of that is in the tip or wear surface, with the rest making up the base. The result is more than five pounds of urethane per blade going to landfill at the end of the cleaner’s useful life.’
In test runs on a standard primary cleaner blade, Mr Childs said researchers logged 681h of run time. Each time a blade reached the end of its life, the old style base had to be removed with a hammer and a new blade installed. The process typically took around 35min.
‘The new primary cleaners with replaceable tips use just over eight-and-a half pounds of urethane,’ Mr Childs continued, ‘but the ratio of blade material to base is nearly reversed. About five-and-a-half pounds of urethane is used in the tip, with only around one-third of the total weight in the base. Furthermore, the replaceable tips delivered 719h of run time in primary cleaning applications, an increase of about 5%. Each reusable blade base is good for 10–12 tip change cycles before it has to be replaced.’
The blade-mounting system underwent a redesign as well, with a patented single-pin configuration to simplify replacement. The new tips can be replaced by hand without tools, significantly improving safety and cutting the service time to just 15min. Because the frame slides out on a track for servicing, no confined space entry is involved. ‘The belt cleaner comes out instead of a worker going in,’ said Mr Childs, who added that a patent is pending on the design.
Taken together, these innovations result in longer service intervals, shorter maintenance times and less downtime, as well as a reduction of nearly 50% in landfilled material. With less frequent replacement and the long service life of the blade bases, customers are also finding they can cut down on their spare blade inventories.
High-speed roller cradle
Martin Engineering have also introduced a new high-speed impact cradle designed to reduce roller and frame damage from heavy conveyor loading conditions in mining, coal handling, aggregates and other applications involving dense materials and/or high volumes. The rugged EVO high-speed impact cradle is engineered to withstand extreme operating conditions, reducing roller failures and service requirements.
‘Under high-volume conditions, standard OEM impact idlers in the load zone simply can’t withstand heavy loads and lengthy drops, resulting in downtime for repairs as well as the expense of replacement components,’ said Martin Engineering service technician Doug Brown.
The new cradles use Martin Engineering’s Trac-mount technology to slide in and out easily for maintenance. The modular components are light enough to be removed by hand, without using a crane or other equipment to handle them.
‘The new cradle design only requires one person to change the rollers,’ said Mr Brown. ‘The biggest problem solved is downtime. In the past when customers needed to change rollers or frames, they had to shut down the conveyor for an extended amount of time,’ he explained. ‘Old-style frames can be difficult to remove, requiring that maintenance personnel pull the arms down, then jack up the assembly to pull it out.’
‘We wanted something that was slide-in/slide-out,’ added Martin Engineering’s global product manager, Chris Schmelzer. ‘These new cradles were designed using finite element analysis, so we could confirm that they’d be strong enough, without having to overbuild them. We can make them as strong as they need to be, without adding excess weight, so workers can remove and replace components without using heavy lifting equipment,’ he said.
The innovative load zone design uses an elastomer bar suspension system that absorbs and distributes the material load being transferred, greatly reducing the stress on the idlers’ rolling components and support structure. One patent-pending design innovation is the use of connecting brackets near the top of the idler frame to hold the three rollers together. These special brackets are designed to allow multiple modular cradles to be tied together, so that the idlers throughout the entire load zone work together as a system.
‘This cradle is simple to install, and the easy access to the centre roller makes maintenance a one-person job,’ added Doug Brown. ‘In addition to greater durability, it’s intentionally designed to facilitate service, making the task of changing rollers safer and easier.’
For further information visit: www.martin-eng.com
- Subscribe to Quarry Management, the monthly journal for the mineral products industry, to read articles before they appear on Agg-Net