Latest Developments at Telestack
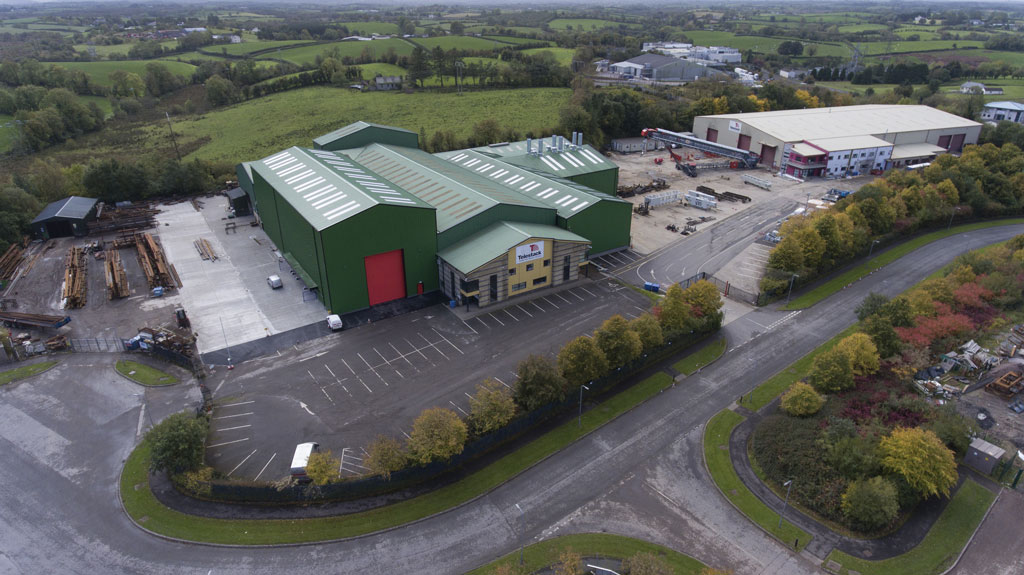
First published in the April 2019 issue of Quarry Management as Reaching New Heights
Dan Gilkes reports on the recent rapid growth and latest developments at Northern Ireland-based material-handling equipment manufacturers Telestack
Increased global demand and the company’s biggest ever order book are driving rapid expansion at Northern Ireland-based material-handling equipment manufacturers Telestack. The company, which has seen turnover grow by around 20% year-on-year over the last decade, is investing £5 million in a new production facility close to its current site in Omagh, Co. Tyrone.
The additional floorspace, which will mirror the assembly processes of the main Bankmore site, will add 4,180m2 of manufacturing capacity to the firm’s existing 9,750m2 factory. As well as manufacturing, the site will incorporate a modern office suite and a dedicated research and development centre. It will help the company to cut lead times for customers and add to what is already a world-leading line-up of equipment.
‘We have the largest range of tracked conveyors on the market, around 30 models to meet varying customer requirements for tonnes per hour,’ said international sales manager Carl Donnelly. ‘We only focus on conveyors, not crushing or screening, that’s our full focus. We are by far the market leader in mobile conveyors.’
While tracked machinery will be of most interest to aggregates producers and mining companies, Telestack are involved in a far wider range of industry sectors, from ports and terminals, to rail distribution and cement production. The company also produces ship loaders and unloaders, radial telescopic conveyors, mobile hopper feeders and reclaim hoppers and link conveyors. Equipment can handle any form of free-flowing material, from ore and aggregates, to fertilizers, grains, woodchips and pellets.
The business is mainly split between the aggregates and mining market and the shipping and ports industry, though given the larger scale of equipment involved in dock handling, the quarrying models are built in far higher volumes. The two sectors also have differing routes to market, with port equipment primarily sold direct or through specialist agents, while quarry machinery is marketed and supported by an extensive network of dealers across the world.
‘We deal mostly through local distributors as our customers need that local support,’ said Mr Donnelly.
Telestack are currently producing around 25 machines per month, with many specifically built for individual customers, with custom dust management just one of the options available. The business has doubled in size since 2015 and, with the current planned investment, is on course to double again over the next three years.
Telestack have been investing heavily in the existing facility in Omagh for some time, putting almost £4 million into the site over the last two years. That includes installing one of the largest shot-blasting facilities in Northern Ireland in 2017, along with two paint booths and additional manufacturing capabilities. All shot is collected, recirculated and recycled to be used again, cutting the site’s environmental impact.
Thanks to scale of the facility, it is possible to take complete assemblies from the shot-blast area straight into undercover storage, maintaining the clean finish prior to heading to the paint area. The shot-blasting process takes the metal to a specified roughness, to allow the paint to adhere more effectively and provide a stronger, more resilient finish.
‘The paint finish is particularly important to our customers, especially in port operations with salt water, but also for construction equipment,’ said Mr Donnelly.
Telestack use a fully automated process to cut steel, increasing efficiency within the plant. The cut steel is transferred on to rollers and carried into a high-speed, multi-spindle drilling-milling machine, keeping as much of the fabrication work in house as possible.
The company also invests in its staff, with the site currently employing more than 160 people. All of Telestack’s welders, for example, are certified to ISO quality standards. The production facility incorporates every stage of the build process, from steel cutting and fabrication through to complete machine assembly, with every conveyor fully built and extensively tested prior to shipping.
Many of the company’s mobile conveyors can be ordered with a dual-power source, using diesel engines and electric drive. However, forthcoming updates to European emissions standards will add an additional layer of complication for the production line, as Stage V engines may well be different to Tier 4 Final units.
‘We are seeing an increase in demand for dual power, with diesel used for movement of the machinery and electric drive for the conveyors,’ said Mr Donnelly. ‘It’s going more and more that way from an environmental point of view.’
‘Having outgrown our current facility, we needed to extend our manufacturing footprint to meet the international demand for our products,’ said Telestack’s managing director, Martin Dummigan.
‘We made a conscious decision, even in the face of Brexit uncertainty, to invest locally. We have a unique skill base in Omagh and we need to protect Telestack’s engineering acumen. As we move through 2019, we will be recruiting for a variety of disciplines, including manufacturing, design, sales and after-sales support.’
With the new site adding much-needed capacity, the company should be well placed to further increase its sales across the world, capitalizing on demand for its class-leading products.
- Subscribe to Quarry Management, the monthly journal for the mineral products industry, to read articles before they appear on Agg-Net.com