Innovation in Conveyor Belt Design
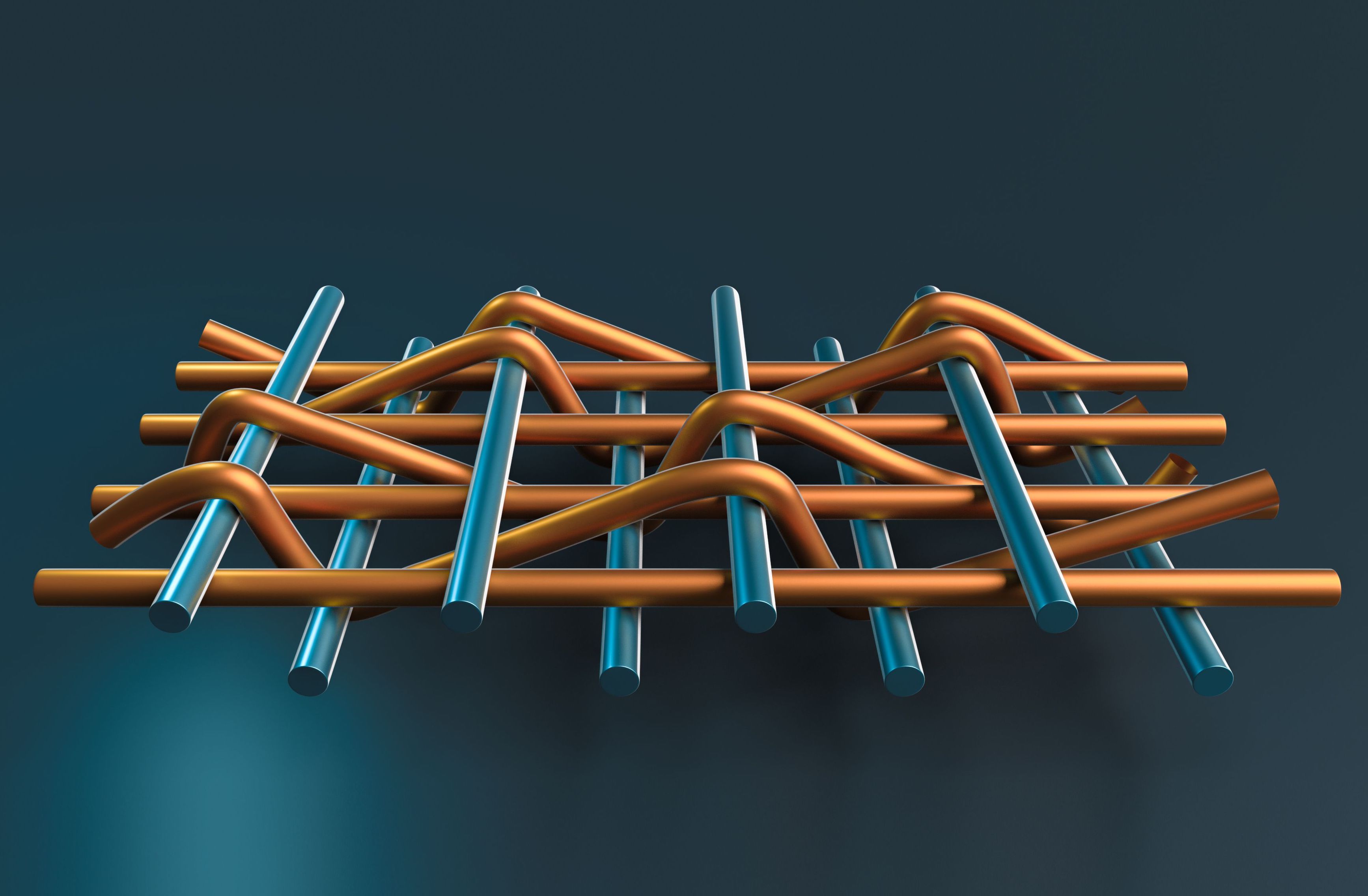
First published in the April 2019 issue of Quarry Management as Breaking New Ground
Conveyor belts perform an enormously important function in the quarrying industry. They are also a very significant overhead. Finding a belt that is genuinely durable and can handle the tough demands found within quarries but still be priced in line with standard belting might be regarded as seeking the Holy Grail. Until now it seems.
Just over a year ago Dunlop Conveyor Belting in the Netherlands and their sister operation in North America (Fenner Dunlop Americas) rather quietly introduced a new and unique design of belt. They claim it is not only considerably more durable and tougher than conventional ply belting but also extremely competitive on price, which is certainly not an approach that Dunlop are renowned for.
In Europe they have branded their creation Ultra X. The following article reveals more about an innovation that some industry insiders believe will, ultimately, change traditional thinking on conveyor belt design.
The conveyor belt market
In order to appreciate the significance of what Dunlop are doing it is important to first look at the market backdrop. The majority of rubber conveyor belts being used in quarries are purely required to cope with abrasive wear. The addition of an element of heavy-duty belting that is specifically used in demanding applications, such as feeding primary crushers, more or less completes the range. At first glance, buyers of conveyor belts might appear to be spoilt for choice because there are so many manufacturers and traders competing for a share of the market.
The market is dominated by ‘economy’ belting imported from south-east Asia. The very best that can be said for it is that ‘It does a job’. This market dominance is actually much greater than many might think because it is not uncommon for European belt manufacturers to import from Asia to supplement their own production, thus allowing themselves to offer low-price belting to their often-unwitting customers in Europe.
Dunlop Conveyor Belting in the Netherlands have always categorically refused to go down this path. Instead, their approach is based on ‘lowest cost’ rather than lowest selling price, by offering belting that gives a much longer operational lifetime. This includes the development of specialist heavy-duty belting (Dunlop UsFlex) designed to handle large, sharp rocks and high impacts.
Although this strategy has served the company well for many years, the UK quarrying industry has tended to be a tough nut to crack because it is particularly price driven. Dunlop’s heavy-duty problem solver, UsFlex, is regarded as virtually unbeatable and the belt of choice at the tough end of the site for those who can afford it. However, Dunlop have largely been unable to compete for routine belting such as 400/3 and 630/4, because quarry managers have to balance the books in the short term rather than take a longer-term view.
With this situation very much in mind, Dunlop management continued to encourage their R&D teams to search for a super-tough, high-quality belt that could also compete at the ‘economy end’ of the market.
An age-old dilemma
It is a fact of life that even the strongest, heaviest belts can be ripped, torn or punctured by heavy, sharp materials or foreign objects, either falling from height or becoming trapped.
‘Accidental belt damage is something that all quarries and mines have to contend with,’ said Dr Michiel Eijpe, Dunlop’s development director in the Netherlands. ‘Large pieces of sharp rock or foreign objects in the materials being conveyed get trapped and can destroy a belt in the blink of an eye. Using low-grade ‘sacrificial’ imported belts invariably proves to be a false economy because although they are very cheap to buy, you have to balance that with the ‘invisible’ costs of lost production time and the cost of more frequently fitting replacement belts plus the costs of more running repairs and higher maintenance. It’s an age-old dilemma.’
According to Dr Eijpe, Dunlop solved the problem of rapid abrasive wear and cutting and gouging of the belt covers long ago: ‘Our belts are well recognized as being the longest-lasting belts on the market. That was the easy part. The biggest challenge was designing a ‘problem-solver’ belt that could really handle impact, ripping and tearing, but which could still be priced economically.’
Back to the drawing board
Rip, tear and impact resistance primarily comes from the belt carcass and not from the rubber covers, so what the Dunlop engineers and technicians did was to go back to the drawing board. What they came up with was a new and unique super-strength ‘breaker weft construction’ single-ply belt. The whole concept is based on an incredibly tough patented polyester fabric that is exclusively made at the company’s own in-house fabric-weaving facility in the US.
What is the big secret?
Dunlop engineers openly say that the strength of Ultra X is created by the specially woven carcass, which has more than three times greater longitudinal rip resistance and up to five times better tear resistance, and a far superior resistance to impact compared with traditional three-ply or even four-ply belting.
This fabric design uses crimped warp polyester yarns to provide high strength and low stretch. These are combined with strong ‘binder’ and ‘filler’ yarns to provide strength and stability under load and it is these that create the exceptional resistance to ripping, tearing and impact.
The tear resistance is strictly measured according to the international EN ISO 505 standard. Throughout its development, sections of Ultra X were repeatedly tested to destruction.
The great cover up
As Dr Eijpe explained earlier, protecting the carcass with hard-wearing rubber covers was the easy part. Ultra X belts are produced with Dunlop AA anti-abrasion covers as standard.
‘Using this grade of rubber ensures that the belt has excellent resistance against the cutting and wearing caused by coarse materials and a resistance to abrasion that outperforms typical DIN Y requirements (average loss of less than 150mm3) by as much as 20%,’ explained Dr Eijpe.
‘All of our cover rubber qualities are extensively tested in compliance with EN ISO 1431 for ozone resistance (50 pphm, strain 20%, 96 hours no cracking) and resistance to the damaging effects of UV light. We know from experience that for belts operating out in the open, these are essential design characteristics that are vital in helping to avoid premature replacement of the belt due to cracking of the belt surface.’
Apparently, the standard compound can also handle temperatures as low as –30°C, so even the extreme temperatures experienced in more northerly locations such as Scotland do not present a problem.
Dr Eijpe was also keen to point out that every type of Dunlop rubber cover is produced in compliance with REACH (Registration, Evaluation and Authorisation of Chemical substances) regulation EC 1907/2006: ‘REACH compliance for rubber conveyor belts is an often-overlooked health and safety factor,’ he said. ‘You will hardly ever see any belt manufacturer even mention the subject but it’s very important, especially for those who are actually fitting and handling belts. Obviously, quarry management have to see that budgets are achieved. However, in our experience, especially in the UK, health and safety is given first priority.’
A question of strength
Ultra X is available in abrasion-resistant rubber and in two strengths – Ultra X1 (Type 330), which is designed for users of EP315/2 and 400/3 conventional ply belts, and Ultra X3 (Type 550), which is designed to replace EP500/3, 500/4, 630/3 and 630/4 ply belts.
The fact that Ultra X is a single-ply construction designed to replace conventional two-, three- and even four-ply belts has already raised quite a few eyebrows, and questions, amongst traditionalists. The first question is how can a single-ply belt provide sufficient tensile strength and yet still have such high levels of rip, tear and impact resistance?
Rob van Oijen, manager of application engineering in Dunlop’s Drachten headquarters, is not only well versed in explaining the hows and whys, but is also adept at throwing in some not inconsiderable additional benefits too: ‘We keep coming back to the genuinely unique fabric that we are using,’ he said. ‘Besides being able to withstand the kind of punishment that would destroy a normal belt, Ultra X has amazing tensile strength. The longitudinal tensile strength of the X1 is 330N/mm whilst the X3 has a longitudinal strength of 550N/mm. The fact is that we stepped away from the conventional range of multi-layer belting for good reason. A single-ply construction requires a finger-splice joint to be made and the big advantage of finger-splice joints is that they retain up to 90% of the belt’s tensile strength, whereas a two-ply step splice only retains a maximum of 50% and a three-ply step joint can only achieve a maximum tensile strength of 67%.
‘When such a high level of splice efficiency is combined with the X1 and X3 tensile strength, then at the very least it effectively creates equivalent tensile strengths and belt safety factors that would be expected from comparable three- or four-layer belting. Belt safety factors are one of the prime selection criteria so this is a really important advantage.’
Mr van Oijen freely admits that finger splices do take longer to make (initially about 30% longer in his experience, but such a difference would be expected to reduce quite significantly with growing experience) and that they are a turn-off for some vulcanizers, especially those who do not have the presses and only want to use cold-splice techniques. However, he is convinced that this viewpoint can be changed with a little help and encouragement.
‘Finger splicing is straightforward for the more experienced splicers out there and the technical and economic arguments in favour of finger splicing are unquestionable. Finger-splice joints are immensely strong and durable, and when you consider the fact that Ultra X has an appreciably better performance compared with conventional ply belt, it means that the need to repair and re-splice joints will be significantly less frequent. Do it once and make it strong,’ said Mr van Oijen.
To help their customers and the vulcanizing companies that they use, Dunlop supply splice kits that include finger-pattern templates, materials and tools, a guide manual and a training film. They even provide training and supervision where warranted.
There certainly does not appear to be any question mark against the overall strength of Ultra X, because as Dunlop’s promotional film proudly states, an Ultra X3 single-ply belt is able to pull up to 56 tonnes in weight.
Endless opportunities
Yet another advantage of Ultra X is that despite its much greater strength, being thinner and lighter allows it to be used on smaller drive pulley diameters. The dynamic stress placed on the inner carcass and on splice joints by continual flexing over small-diameter pulleys has, until now, been a long-standing problem because the pulley size effectively determines the strength and thickness of multi-ply belt that can be fitted.
‘The X1 drive pulley diameter for over 60% rated tension can be as small as 315mm and the X3 drive pulley diameter, again for over 60% rated tension, can be as small as 400mm,’ said sales and marketing director Andries Smilda. ‘This means that Ultra X is also ideally suited to run on equipment such as mobile stackers, crushers and screening machines that are notorious for having small pulley diameters. The problem is that design tolerances and the dynamic stress placed on the inner carcass and the splice joint by continual flexing over small-diameter pulleys seriously limits what can be fitted. Ultra X overcomes this problem.’
Dunlop in Europe are so confident that Ultra X will prove to be a game-changer for OEMs that they have geared up their endless-belt production capacity in Drachten and also in their service facilities in Poland and Italy.
Under the radar
Dunlop actually launched Ultra X more than a year ago. It was a deliberately low-key affair and under the radar of most of the market. Mr Smilda explained that there were many reasons for taking a cautious approach: ‘We knew from the years of research and intensive laboratory testing that went into the development of Ultra X that we were on to something special. But we still wanted to prove it in the field, so we have been working with several tried and trusted end-users across a wide cross-section of industries.’
Dunlop appear delighted with their successes in Europe so far, including in the highly price-driven Spanish region and a very competitive market in France. Ultra X is already the belt of choice in the biggest quarry in Europe, whilst OEMs are finding that Ultra X has more than doubled the average belt lifetime. ‘We have sold many thousands of metres in the past year and we are recruiting more and more production staff for our factory in Drachten so that we can keep up with demand,’ said Mr Smilda. ‘Ultra X is all that we thought it would be and more. The fact that we have not had a single complaint or technical issue should reassure everyone that Ultra X is now a tried and tested winner.’
Competing on quality and price?
There has been a surprising openness about the need to be able to ‘slug it out on price’ and Dunlop are keen to explain why and how they are able to offer prices that are at least comparable to (and often lower than) multi-ply belting.
‘We would never compromise on quality for the sake of competing on price. That is simply not our culture,’ said Mr Smilda. ‘But, actually, there are several reasons why we can price Ultra X so competitively. First, the single-ply carcass is made from fabric that we manufacture in house. That’s a big advantage in terms of both quality and cost. Having a single-ply construction also allows for maximum efficiency of production because there are fewer calendar runs. And having no rubber skim between the plies not only results in a thinner, stronger carcass, it also keeps the cost down.’
Dunlop are making longer, more cost-effective production runs than usual at a maximum width of 2,000mm and are only selling Ultra X in full-roll lengths of 300m. Endless belts and pre-prepared ‘ready-to-spice’ belts need to be ordered in multiples.
‘Cutting and shipping short lengths creates additional costs that impact on the selling price, but for all customers starting out with Ultra X for the first time we are, of course, trying to be as flexible as possible,’ said Mr Smilda. ‘We now know that they will be coming back for more once they see what Ultra X can do.’
A cultural change
There is no questioning the belief and enthusiasm that everyone at Dunlop Conveyor Belting seems to have for Ultra X. There is also no question about the company’s history of innovation when it comes to conveyor belts. From creating the first-ever fire-resistant belts through to heavy-duty application belting such as Dunlop UsFlex, it is clearly part of the company’s culture.
At the same time, what is also clear is that Dunlop are looking for something of a cultural change. To many, the notion that a relatively lightweight, single-ply construction belt can provide the necessary tensile strength together with considerably more resistance to ripping, tearing and impact, and have a much greater splice strength, is difficult to comprehend. To do all of this whilst competing on price with all but the lowest grade of belt being imported from Asia is, perhaps, an even bigger ask. But if the quarry industry is able look just a little beyond its long-held beliefs and old practices, then it is very likely to see that Ultra X really could be a game-changer. For further information visit: www.dunlopcb.com
- Subscribe to Quarry Management, the monthly journal for the mineral products industry, to read articles before they appear on Agg-Net.com