Guide to the Types of Belt Edge used in Rubber Conveyor Belts
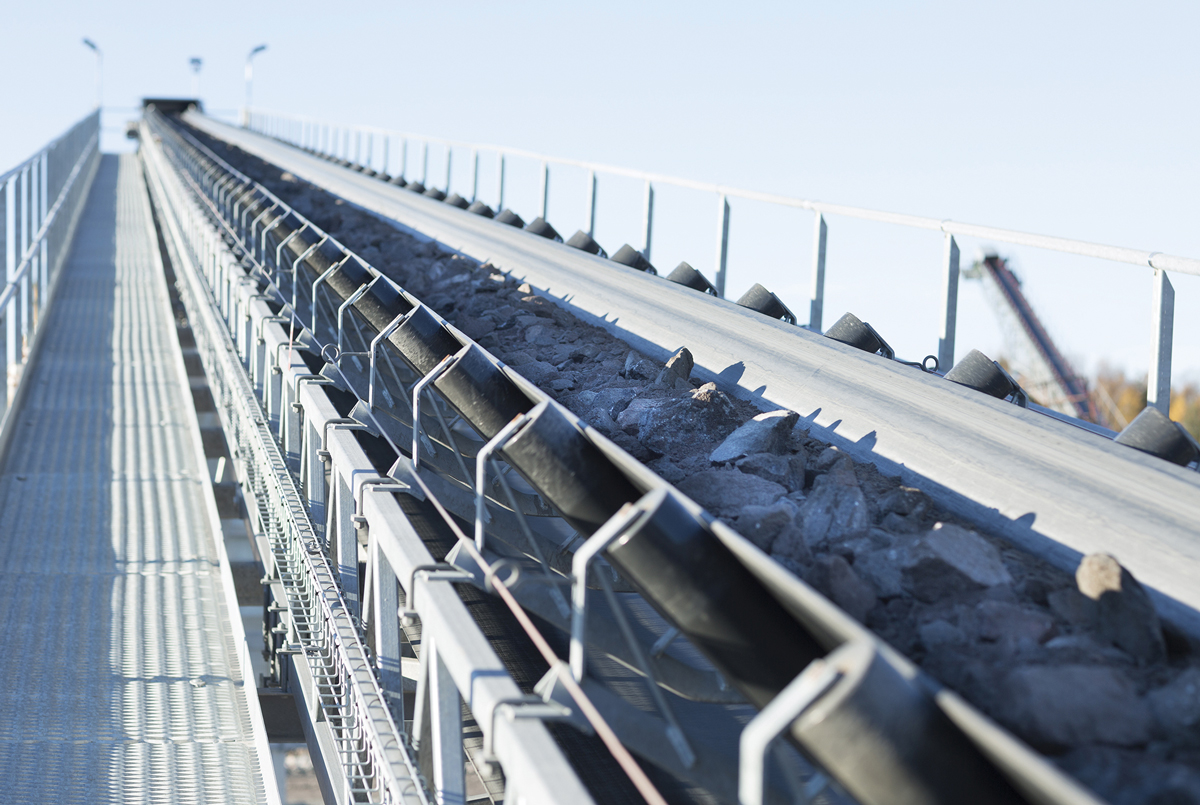
First published in the March 2020 issue of Quarry Management as The Edge of Reason
Dunlop Conveyor Belting’s Les Williams throws some surprising light on the subject and provides useful hints on how to potentially save a lot of money
Considering the huge amounts of money spent on conveyors and conveyor belting and the numerous challenges they can present, deciding on exactly what type of edge a conveyor belt should have does not sound particularly important. But strange as it may seem, selecting the right type of belt edge can have an enormous impact, especially in terms of cost.
For many years now there have been continual advances in the technology and the types of materials used to manufacture rubber multi-ply conveyor belts. Gradually, over time, misconceptions and myths are being put to rest. However, there is one persistent technical aspect of rubber conveyor belts where many conveyor technicians and conveyor belt buyers seem to retain outdated beliefs – belt edge types.
There are only three basic types of belt edge – moulded edges, sealed edges and cut edges. The importance of which type to use is vastly underrated. Choosing the wrong type continues to cost many conveyor operators a great deal of wasted money, both in terms of belt costs and also in repairs, maintenance and lost production.
Moulded edges
Many years ago, moulded edges were the standard because cotton was used as the reinforcing fabric in multi-ply belts. A moulded edge was, therefore, essential in order to prevent moisture from penetrating the cotton fabric and causing it to rot. However, since the inception of synthetic belt carcasses using polyester and polyamide, this problem effectively no longer exists. Although belts without moulded edges are now the most commonly used, moulded edges continue to be needlessly specified in many requests for quotations.
Moulded edges can only be created when a belt is manufactured (assembled and vulcanized) to an exact width. This is a vitally important factor which will be touched on again later. During the calendaring of the belt, a small strip of un-reinforced rubber is attached to the side of the carcass. The strip is formed as an integral part of the belt during the vulcanizing process. This typically creates between 5mm and 15mm of un-reinforced rubber on the belt edge.
Moulded edges do not provide any structural advantage. Indeed, they can be susceptible to damage because they can very easily be torn off should the belt wander off-track for any reason.
Sealed edges
The alternative and most commonly used belt edge type is the ‘cut & sealed edge’ or simply ‘sealed edge’. The majority of fabric multi-ply belting is held in stock in a range of the most commonly used standard widths by manufacturers, distributors and traders. To maximize production efficiency and minimize cost, these standard-width stock belts are usually made as wide as the manufacturing machinery will allow. These are known as ‘slabs’, which are then cut to narrower widths. For example, 400m of 2,200mm-wide belt would be produced that could then be slit (cut) to produce 400m of 1,000mm-wide belt and 400m of 1,200mm-wide belt. The belt edges are then sealed.
Dunlop automatically create belts with sealed edges in a single process using special cutting knives that rotate at an extremely high speed. The heat created by the friction of the rotating knives melts the carcass fibres and a small amount of the rubber on the edge of the belt, effectively creating a seal. Technically, this is a ‘cut & sealed edge’, but is more commonly is simply referred to as a ‘sealed edge’.
Cut edges
Belts with cut edges that are not sealed in any way are produced in the same way but are slit using conventional cutting knives. Dunlop do not recommend the use of unsealed (raw) cut belt edges.
Apart from a better visual aspect, having a sealed edge means that moisture is prevented from being drawn into the carcass from the edge by capillary forces. Although modern synthetic carcass fibres are hardly affected by this, moisture can ultimately cause vulcanizing problems when making splice joints, so it is better to be safe than sorry. Having a sealed edge allows a belt to be used safely in wet conditions and makes it better suited to long-term storage outdoors.
Steelcord construction belts
In the case of steelcord and steel-reinforced fabric ply belting, it is necessary to use moulded edges in order to prevent moisture penetration into the carcass, which, over time, would cause the steel to corrode. All of Dunlop’s steelcord belts are manufactured to a specific set of specifications that fully embed the steel cords, so for these reasons they are always supplied with moulded edges.
‘Made to order’
Many conveyor belts are ‘made to order’ for the end-user. These belts are mostly either the more specialized cover grades (eg fire resistant), high-performance carcass constructions (eg steel-reinforced fabric ply) or simply a non-standard width requested by the customer. Custom-made belts will naturally have moulded edges.
Avoiding unnecessary cost
If the manufacturer is prevented from making a belt at the widest, most cost-efficient production width, this will have a negative impact on the selling price to the end-user. For example, to produce 600m of 800mm-wide belt, it is far more efficient to manufacture 300m of 1,600mm width belt and then cut and seal it into two 300m rolls of 800mm. Demanding a moulded edge rather than a sealed edge prevents this from happening, because 600m of 800mm-wide belt with moulded edges would have to be made to order and would take virtually twice the time to produce.
Unnecessarily prolonging the production time has to be reflected in the price. Requesting a belt to be made to order rather than being taken from stock also has a major impact on the delivery lead time. Taking a roll of pre-cut belt from the warehouse will invariably be a whole lot faster than scheduling a special production run.
The logical conclusion in all of this is that insisting on having a belt supplied with moulded edges, even when there is no practical or technical benefit, can be a huge waste of money. For further information visit: www.dunlopcb.com
- Subscribe to Quarry Management, the monthly journal for the mineral products industry, to read articles before they appear on Agg-Net.com
- Reply
Permalink