‘Fit And Forget’ Conveyor Drive
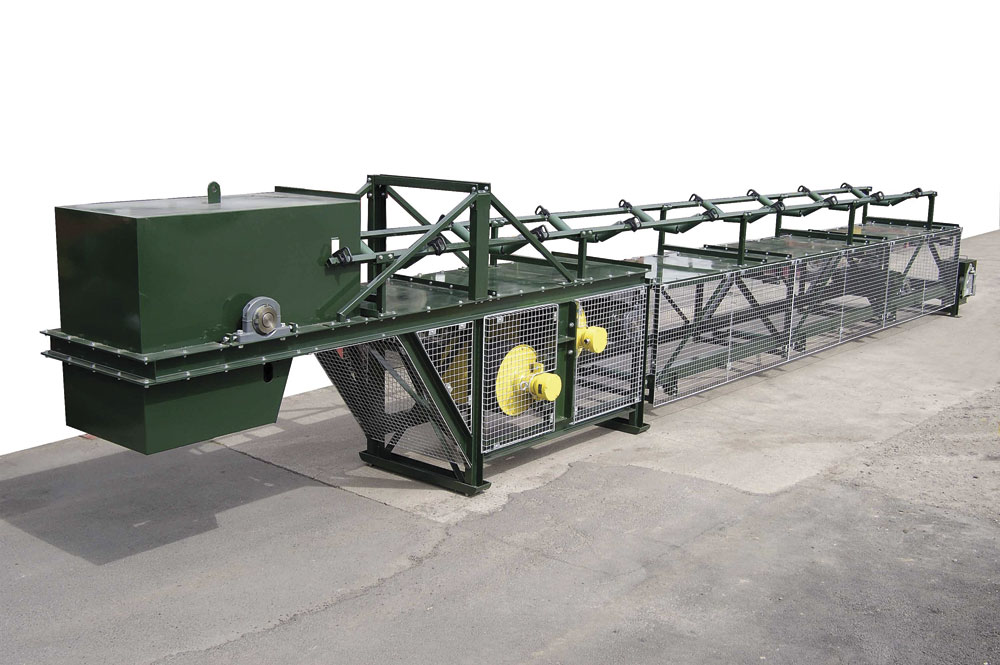
Canning Conveyor mark 40 years in business with the launch of SuperDrive
In September 2005 Worksop-based bulk materials handling specialists Canning Conveyor Co. Ltd celebrated their 40th year in business with a week-long programme of open days for customers past and present. The celebrations were held not only to mark the company’s 40th anniversary, but also to officially launch the new Canning SuperDrive conveyor drive system incorporating Rulmeca motorized pulleys, for which the company is now the exclusive UK stockist and distributor.
The new SuperDrive system is the culmination of Canning’s 15-year working relationship with worldwide bulk-handling equipment specialists Rulmeca. According to Canning, many of their customers are realizing that motorized pulleys offer an attractive alternative to conventional drives, providing both reliability and cost-effectiveness in challenging environments along with other advantages such as low noise, improved safety and compactness.
At the heart of the company’s new SuperDrive system is the SuperDrive jib head unit, designed specifically to power quarry field conveyors. Offering a purpose-built space-saving design, the jib head features an integral crash box with inspection hatch, primary and secondary belt cleaners as standard, and Cooper split roller bearings on all non-drive pulleys. According to Canning, the system has been designed so that quarry operators can ‘fit it and forget it’.
Mounted within the jib head unit is the ceramic-lagged Rulmeca motorized pulley, with its motor, gearbox and bearings all totally enclosed and sealed (to IP67) inside a steel shell, thereby minimizing the likelihood of failure due to water, dust, grit and other harmful environmental conditions. Because the drive unit and bearings are mounted internally, the unit takes up much less space than a conventional drive system and eliminates the need for chains, v-belts, couplings, bearings, support structures and special guarding. Moreover, because the motor is completely enclosed and the external shafts are always stationary (the only moving parts are the motorized pulley shell and bearing housings), the SuperDrive is said to be much safer than conventional drive systems.
Whereas exposed conveyor drive systems can require 10 or more separate components, the SuperDrive consists of the motorized pulley itself and two fixing brackets, making it much quicker and easier to install. End users are also expected to benefit from lower maintenance costs, because the SuperDrive requires no maintenance other than a recommended oil change every 10,000h and an oil seal change every 30,000h. Synthetic oil can also be specified to extend the service interval up to 30,000h.
All SuperDrive units with three-phase motors feature thermal protection and can be controlled by variable-frequency converters working in the 15Hz to 65Hz range. And because there are fewer friction losses owing to the direct drive from the electrical motor to the shell (pulley face), the SuperDrive is said to be capable of achieving efficiencies of up to 97%, resulting in considerable savings on electricity. Noise levels are also reduced to a maximum of 76–85 dB(A)) due to the totally sealed enclosure and the use of high-quality gears.
For many years Lafarge’s Mountsorrel Quarry has utilized Rulmeca motorized pulleys in critical areas where high throughputs and total availability are required. For the past nine years, the main shuttle conveyor on the quarry’s toast-rack storage system has been powered by dual 800mm diameter, 37kW motorized pulleys (one at each end). This reversible travelling conveyor carries in excess of 2,500 tonnes/h of crushed granite at speeds of 3.15m/s. Lafarge have been so pleased with the performance of this system over the years that a sister conveyor running alongside has now also been converted to motorized pulleys.
Meanwhile, at UK Coal’s Kellingley Colliery, a 295m long conveyor carrying 300 tonnes/h of coal at 2.0m/s is driven by an 800mm diameter, 75kW Rulmeca motorized pulley, which is said to achieve an electricity saving of £6,000 per annum and an annual repair bill saving of £30,000.
The complete range of SuperDrive motorized pulleys extends from units 138mm in diameter up to units 800mm in diameter and with power outputs from 0.25kW to 132kW (dual units up to 264kW). Canning Conveyor are offering standard units to cater for 600mm, 750mm, 900mm and 1,000mm belt widths, with single drives of 22kW and 37kW and dual drives of 45kW and 75kW being held in stock. Units from 15kW to 264kW are also available. Canning are also offering three-year parts and labour warranty on all their SuperDrive systems.
In addition to the main SuperDrive jib head unit, Canning also plan to maintain large stocks of related field conveyor equipment for use with the system, including hand-winch operated loop-take-up units, grading sections and tail-end units, as well as the company’s new and innovative intermediate field conveyor system featuring robust, easily installed steel structures and suspended idlers equipped with safety handles and lightweight, low-noise, wear-resistant high-density polymer rollers.
Canning Conveyor Co. Ltd, Sandy Lane Industrial Estate, Worksop, Notts S80 1TN; tel: (01909) 486166; fax: (01909) 500638; email: sales@canningconveyor.co.uk