Feeder Flexibility
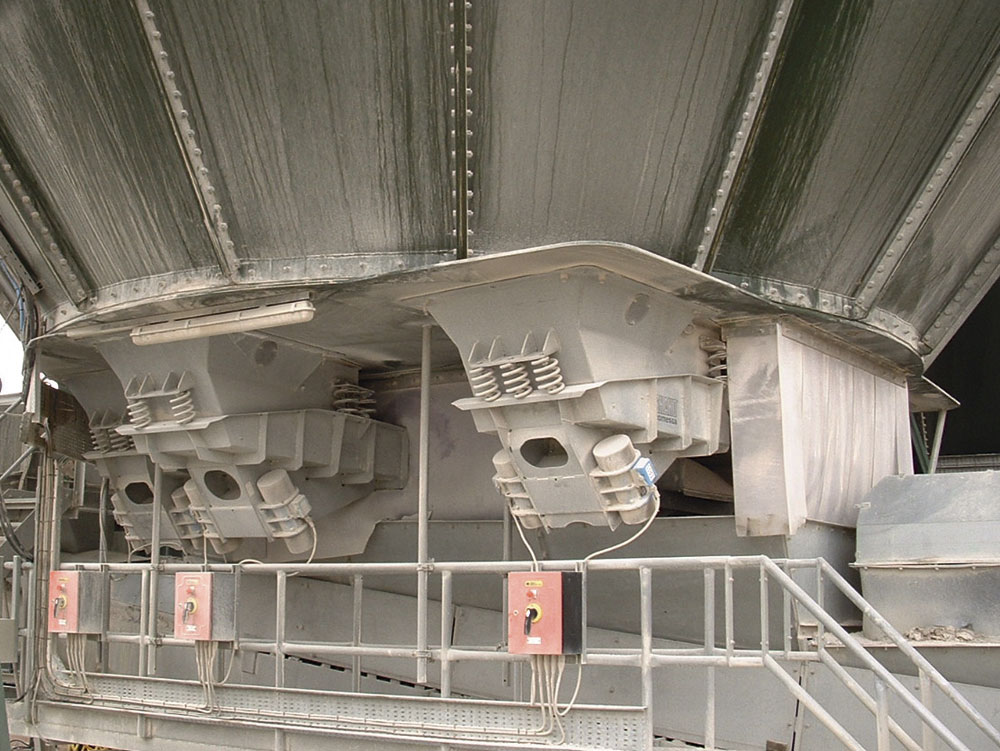
Selecting the best-suited vibratory feeder for material-handling applications
By Bob Hill, director of Skako Comessa Ltd
Discharging material from A to B at the required feed rate sounds a simple task, however selection of the correct-specification feeder can have a dramatic affect on the level of success achieved. While hardly ‘rocket science’, Skako Comessa, believe there is an important and significant scientific relationship between the engineered feeder itself, the raw material being handled and the operational criteria.
As a feeder manufacturer, it is not uncommon for Skako Comessa to be asked for a vibratory feeder capable of operating at 250 tonnes/h, handling rock with a maximum size of 100mm. However, this could easily cover more than a dozen material-handling scenarios, each of which would affect the type and specification of the best-suited feeder. The feeder manufacturer, therefore, needs to fully consider three distinct areas: the characteristics of the material being handled; the operational methodology, including locational parameters; and the feeder technology itself.
The starting point is the material being handled: type of material, bulk density, size distribution, shape, moisture content, abrasiveness, porosity, angle of repose, foreign particulate present, temperature, acidity etc.
The second key area is the operational methodology: capacity, level and method of feed regulation, accuracy, repeatability, frequency of stops/starts, position and location, environment, subjected impact, preceding and following equipment, power supply etc.
Having taken into account all the above relevant factors, the best-suited vibratory feeder needs to be selected from the available feeder technology. Basically, this can be split into four distinct categories: inlet hopper and skirt plate design, feeder tray method of construction, vibrator drive type, and selection of liner plates and ancillaries.
The above areas can be ‘mixed and matched’ to arrive at the optimum feeder specification and each will be discussed in greater detail later. However, natural combinations ‘fall together’ to create feeders that operate in general capacity and application ranges, as shown in figure 1.
The chart (fig.1) shows that, for a typical extracted bulk material with a bulk density of 1.6 tonnes/m3, feeders supplied by Skako Comessa have an operational range from
0 to 3,500 tonnes/h. Basically, this range is covered by three different drive methods, with three methods of fabrication. There is considerable overlap of feeder types, as factors other than capacity alone will determine the best-suited feeder design and specification.
Type FCE – Electro-magnetic-driven feeders
These operate in the light-to-medium-duty ranges, generally handling material less than 200mm in size at between 0–500 tonnes/h.
The electro-magnetic vibrator drive is a resonance system which gives a linear displacement, generally accepted as a small stroke at a high frequency. The most widely used drives are 50Hz, corresponding to 3,000 vibrations per minute. These normally operate within the stroke range of 1.0–1.4mm, corresponding to 4.5–7.0g (multiples of gravity). Skako Comessa electro-magnetic drives have a natural tuned frequency above the power supply frequency (super-critically tuned), which eliminates any loss of capacity due to ‘material load damping’ and allows immediate and unlimited stops/starts.
The stroke of the electro-magnetic vibrator is regulated via a thyristor controller, giving ‘half wave’ electrical activation of the coil. Either a manual potentiometer or an external reference signal (usually 0–10V or 4–20mA) regulates the stroke between 0–100%. This allows fast and dribble operation for sensitive weighing/dosing/ proportioning applications. It also allows instant stop/start, which is especially applicable for maintaining the correct head of material when feeding cone crushers.
Electro-magnetic-driven feeders are, therefore, particularly suitable for applications where high levels of proportioning accuracy and an infinite feed range are required, and where automation requirements are at their highest and frequent and immediate stop/starts are necessary.
They are not suitable, however, for handling large material, nor are they designed to be subjected to impact conditions (they should operate with a head load). They are also not best suited to the handling of sticky or changeable ‘all in’ materials, as adhering material can adversely affect the tuning of the drive.
The tray sections of light-to-medium-duty electro-magnetic- driven feeders are always of total welded construction, as they can be designed to withstand the imposed dynamic loads, relative to their size. Over 90% of feeders of this type supplied by Skako Comessa are in totally modular form, where the inlet hopper bottom section is supplied to give a complete assembly (further details later).
Type FCU – Twin unbalanced motor-driven feeders
Unbalanced motor-driven feeders cover a wide operating range and are generally utilized within the capacity range of 100–1,000 tonnes/h, but capacities up to and exceeding 2,000 tonnes/h are also possible.
The drive principle involves the use of two rotating motors with unbalanced weights at each end of their rotating shaft. With the correct positioning of the motors and identical unbalanced weight settings, they are powered to run in opposing directions. The correct design of the vibratory feeder allows the two motors to synchronize, resulting in a linear displacement. Depending upon the feeder size and duty, either 4-, 6- or 8-pole motors can be used, corresponding to 25, 16.7 and 12.5Hz. As these feeders are often used in medium-to-heavy-duty environments, they are generally subjected to less dynamic force than electro-magnetic-driven feeders, usually within 4.0–5.0g. Therefore, on the smaller feeders 4-pole motors would be used, giving a stroke between 4–5mm, while on the majority of feeders handling between 400–1,000 tonnes/h, 6-pole motors would be utilized, giving a stroke between 7–9mm. For heavy-duty applications 8-pole motors are often selected, giving a stroke between 10–12mm.
Unlike electro-magnetic-driven feeders, unbalanced motor-driven feeders are not weight sensitive or frequency supply sensitive and do not need to be tuned to the vibratory weight. The resultant working stroke is a pure element of the prevailing vibratory weight (even one that varies due to operating conditions). This means they are extremely versatile and robust, and can easily cope with differing head loads, variable-quality feed material, and even impact loadings. They are, therefore, well suited to the handling of primary crushed material in tunnel recovery systems, where varying amounts of natural undersize could also be present, in addition to numerous other applications.
In their standard form, twin unbalanced motor-driven feeders are simply switched on and off via a direct on-line starter and operate at a predetermined fixed feed rate. This fixed feed rate can be varied from approximately 25–100% by manually resetting the position of the unbalanced weights on each motor when the feeder is switched off. Therefore, for nearly all fixed feed rate operations between 100–1,000 tonnes/h, this type of feeder is the most economic option. However, these feeders are increasingly being controlled via frequency inverters, which allows infinite variable feed rate control between approximately 30–100% of the preset maximum. This is generally ideal for quarry operations, including feeding on to screens and impact crushers. It has to be appreciated that the minimum feed rate possible cannot be guaranteed at a given level because the motors must synchronize at the reduced frequency for correct operation, and this can vary depending upon the feeder weight and design, and the application in which it is being used.
These feeders are not suitable for applications requiring frequent or immediate stops/starts, or where proportioning accuracy and automation requirements are at their highest (for these applications an electro-magnetic-driven feeder must be used).
The trough sections on unbalanced motor-driven feeders are usually of totally welded construction, and are of either standard or heavy-duty design, usually determined by the application. For some heavier-duty applications they can be a mixture of welded and bolted construction. As with the previous type of feeder, the vast majority of feeders of this kind supplied by Skako Comessa are in totally modular form.
Type FCD – Mechanical vibrator-driven feeders (geared synchronous exciters)
Mechanical vibrator-driven feeders are only utilized in heavy-duty applications because, without exception, they are the most expensive feeder option. However, they can be designed to operate under the harshest of operating conditions, allowing mined and blasted materials to be handled and even coping with severe impact loadings. While they normally operate within the capacity range of 1,000–3,000 tonnes/h, larger capacities are readily achieved and individual rock sizes of up to 2,000mm can be handled.
The method of feeder construction and the drive type allow these extreme operating conditions to be easily accommodated. The drive principle involves two geared shafts with fixed unbalanced external weights. One shaft is directly driven via a cardan coupling and the two shafts are geared together, thus revolving in opposing directions. This means that the drive is totally synchronous at all speeds and there is a resultant linear displacement. The drive synchronization is of critical importance because it eliminates the high unbalanced dynamic forces that occur with unbalanced motor-driven feeders when they are not synchronized during starting and stopping. The operating frequency is either 16.7Hz or 12.5Hz, the lower frequency always being used for the heaviest-duty feeders. The dynamic operating forces are kept to a minimum, usually around 3.0g. The operating stroke is normally within the range of 10–16mm. The bearings, which are dimensioned to accept continuous operation in the harshest conditions, are ‘oil mist’ lubricated from the oil in the synchronous gearbox; the oil needs to be changed at set intervals, depending upon the operating conditions.
These feeders are usually powered by normal industrial electric motors, although hydraulic drives can also be used. They can be used at a fixed speed, giving a fixed feed rate, or teamed with a frequency inverter to give variable feed rate control. Because the mechanical vibrator is synchronous, it is normally possible to cover a wider feed rate range than unbalanced motors, with 25–100% generally achievable.
In order to minimize fabrication stress factors for these heavy-duty feeders, their bodies are of total compression-fit ‘Huck-bolted’ construction, thus eliminating any weld stresses.
Inlet hopper and skirt plate design
Selection of the best-suited drive and construction method for the feeder tray is essential for feeding success. However, of equal importance is a properly designed inlet/hopper section directly above the feeder tray, allowing the correct product discharge. If this is incorrectly designed it could easily reduce the required capacity by over 30% or promote ‘self/gravity’ feeding.
Traditionally, the hopper or silo manufacturer would have been responsible for this section, often resulting in conflict with the feeder manufacturer if the feeder did not perform as expected. However, over 25 years ago Skako Comessa pioneered the complete feeder modular assembly, which included the hopper bottom section, complete with a simple square connection flange, skirt plates, bed depth regulation gate, and a captive support spring interface between the feeder tray and the inlet hopper section. This resulted in design responsibility being taken solely by the feeder manufacturer. The inlet hopper design eliminates the varying effects of head load and material damping, as there is a fixed imposed pressure on the feeder tray. This is achieved by utilizing empirically proven reactionary force principles to stabilize both the static and dynamic forces. The super-critical tuning method of the Skako feeders also allows the load to sit directly above the feeder tray. Vibration is therefore passed directly upwards into the material, helping to keep it ‘live and conditioned’ and drawing it downwards.
The complete feeder modular assembly also facilitates simple dust encapsulation, utilizing a ‘knock-on’ sealing system.
Selection of liner plates and ancillaries
The correct selection of liner plates helps to complete the ‘best-suited’ feeder specification. It is normal to bolt replaceable liner plates into the tray (and into the integral hopper bottom section), allowing for both ease and speed of replacement, although bonded ceramic tiles or rubber can also be considered.
Depending upon the characteristics of the material being handled, a variety of steels can be used, including chromium carbide, Hardox 400 (or equivalent), stainless steel,
Domex or mild steel. For moist or ‘sticky’ materials, plastic liners have been used successfully, including special, harder, wear-resistant versions. Skako Comessa pay particular attention to the liner design, often including radiused sides to prevent initial build-up in blind corners, as well as rear rubber seals to prevent spillage and ingress from moist materials.
Within modular feeder assembly designs, a number of standard ancillaries can be included to complete the ideal feeder specification. These include rod gates, cut-off gates, ‘no flow’ switches, material locks and chain curtains.
This article gives an insight into the many options available when selecting a vibratory feeder and will hopefully help end-users, consultants, specifiers and main contractors to work in partnership with the feeder manufacturer to determine the best-suited vibratory feeder specification.