Continental Conveyor Developments
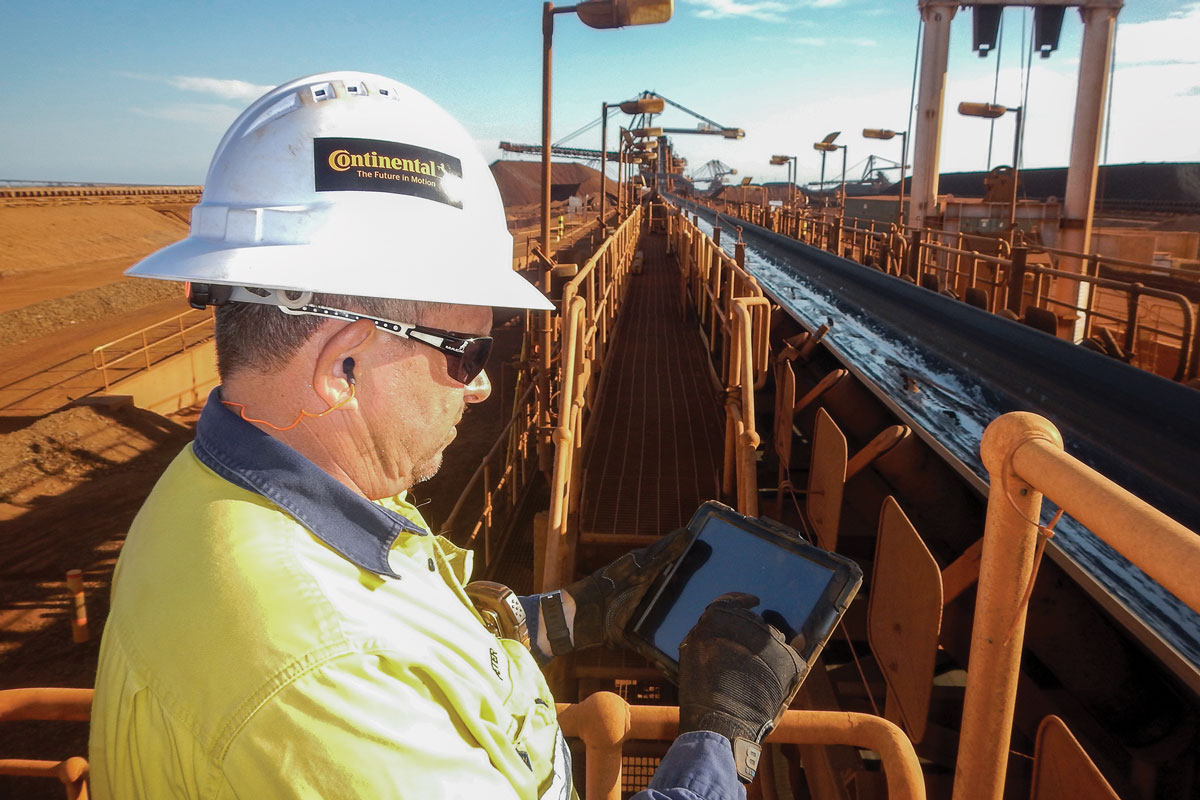
First published in the April 2021 issue of Quarry Management
Continental unify Conveying Solutions branding around the world and develop visual and acoustic technology-based inspection service for conveyor belt systems
Earlier this year, Continental announced a strategic sharpening their profile as providers of complete conveying solutions and service, with the news that all products, technologies, services, know-how and expertise from company-owned brands PHOENIX, IMAS, Kolubara, LEGG, Matador and National Belt Service have now been integrated into the broad Continental product and service portfolio in a unified, single-source approach.
Dr Michael Hofmann, head of key account management and marketing for Conveying Solutions, said: ‘In the past, we had a line-up of different brands and product lines. We are now simplifying our portfolio to provide our global markets with easier and faster access to our entire product line-up. This includes Continental’s outstanding know-how, technology, innovation and research and development resources, global production and service network.’
The bundling of assets under one global brand goes hand in hand with optimization and extension of the company’s portfolio of belts and value-added digital innovations and services, and means customers and partners will now benefit from a stronger, trusted global product portfolio from one source.
Andreas Bakenhus, who is responsible for Continental’s newly created Conveying Solutions service segment, said: ‘We see fast-changing requirements in our markets. A few years ago, our customers asked for high-quality, long-life belts. Now, mining, quarrying and other bulk materials handling companies are looking for safety, quality, efficiency and productivity gains.
‘Our customers require integrated solutions covering the entire value chain around a belt, from commissioning, consulting and training to digital monitoring and on-site maintenance. Additionally, energy-optimized belts, new business models and sustainability aspects will play a crucial and competitive role in the future. Basically, it is our job to offer service levels that allow our customers to fully concentrate on their core business.’
Globally, Continental offer both an international network of 1,300 experienced service technicians and partners, but beyond this the company will extend support to regional distributors with an extended offering of service-related products and digital tools.
Continental are continuing to develop value-adding digital solutions and services, such as a new drone-based monitoring solution for conveyor belt systems that will be launched to market this year. This will permit early identification of weak points before any damage occurs, helping to prevent costly unscheduled downtime.
Sensor-based inspection service
This new technology-based approach, which was developed to the prototype stage in the incubator programme of Co-pace, Continental’s own start-up organization, offers a combination of visual and acoustic inspection, and also permits the efficient, data-assisted planning of maintenance intervals. It replaces the conventional and usually very laborious manual process with sensor-based technologies that permit a more precise inspection process, reduce the verification input and allow predictive maintenance.
In all belt conveyors, idlers are important components and essential in ensuring smooth conveying operations. According to Continental, around 30% of operational faults with belt conveyors are attributable to idler defects that were not identified in a timely manner. In response to this, the company’s new service offering comprises a hybrid solution that addresses different applications and sections of belt. Inspection of open sections and operations is carried out from the air using a drone equipped with infrared and RGB cameras that monitor both sides of the belt conveyor.
Once the drone has flown over the section under inspection, it returns to an autonomous charging station and uploads the data it has collected to the cloud, via an IoT (Internet of Things) module, during the charging process. The image data is processed with the aid of an artificial intelligence-assisted algorithm and analysed with reference to any detected idler defects.
Meanwhile, continuous maintenance in covered or underground sections is carried out using fixed microphones installed every 20–25m that capture frequency variations in the idlers. The audio recording is conducted twice a day, with the data uploaded to the cloud. Events that indicate a damaged idler are investigated using an artificial intelligence-based algorithm.
‘Conventional and often manual inspection methods can be very time-consuming, imprecise or even dangerous for service technicians because of the belt length or local circumstances, such as underground routing and enclosed sections,’ explained Clemens Panzer, who has played a leading role in this new development as a member of the interdisciplinary team set up for the project.
‘Documentation is also often performed manually, with reports having to be manually input subsequently into the relevant datasets. Maintenance intervals also frequently follow a fixed rotational principle, meaning that measures required on short notice to avoid or prevent conveyor failures cannot be carried out in a timely manner.
‘Sensor-based inspection, by contrast, permits data-assisted remote monitoring of system condition, with the result that potential damage can be detected at an early stage and avoided. Another benefit is that the data collected are automatically made available in digital form via a user-friendly interface.
‘The data can be viewed at any time and permit the demand-driven planning of relevant service periods. Changes in the conveyor condition over an extended period can be analysed significantly better using the stored historical data, and the anticipated service life of the components can also be better estimated,’ said Mr Panzer.
Having been successfully tested in field trials and pilot projects, the new system is due to become operational during 2021.
For more information, visit: www.continental-industry.com
- Subscribe to Quarry Management, the monthly journal for the mineral products industry, to read articles before they appear on Agg-Net.com