Continental Conveyor Belts used in Swedish Infrastructure Project
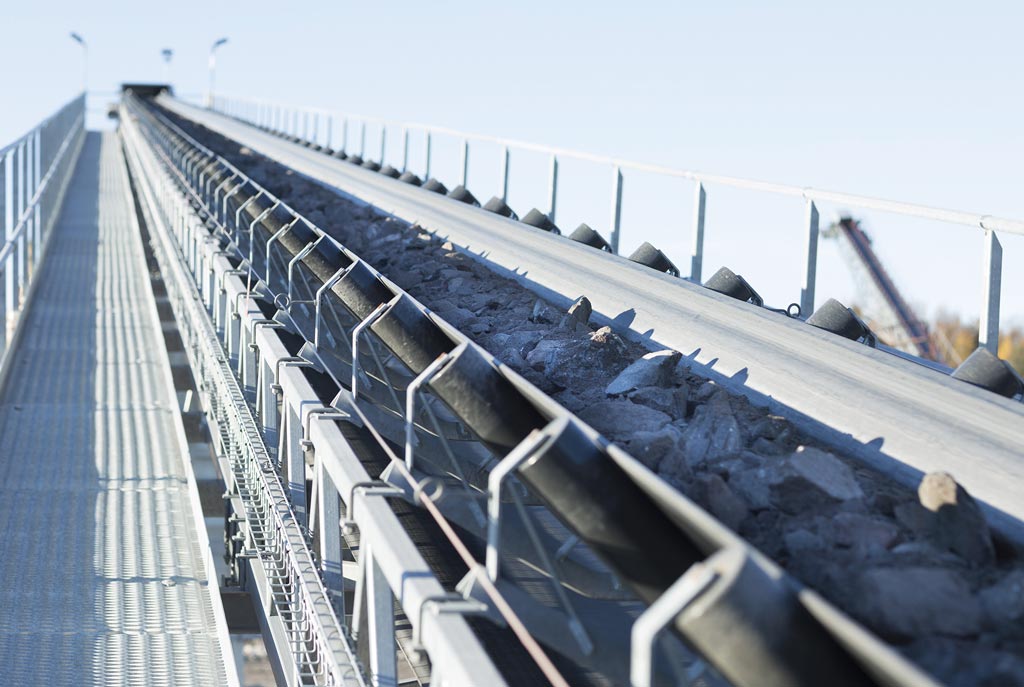
First published in the April 2019 issue of Quarry Management as Belts for the Bypass
Continental conveyor belts are currently working flat out on mega-tunnel project in Stockholm
Conveyor belts designed by technology company Continental are currently being used to transport millions of tonnes of rubble from one of Sweden’s biggest infrastructure projects – Förbifart Stockholm (Stockholm Bypass). The bypass, which is situated to the west of the Swedish capital, has been under construction since 2015 and most of it is being built underground. The bypass is intended as a north–south link to reduce the volume of traffic passing through the city centre. Aggregates firm Jehander, a HeidelbergCement Group company, are using Continental conveyor belt solutions at their Löten Quarry, near Stockholm, to allow rubble from the mega-tunnel project to be reused for road construction.
As the number of city dwellers grows exponentially around the globe, this urban growth has many consequences, including lack of space, limited living space, and congested road networks resulting in gridlock and poor air quality. It a common problem for megacities as well as for Stockholm. About one fifth of the Swedish population currently lives in the Greater Stockholm area. That is more than 2 million people – and the number is rising.
According to the Swedish Chamber of Commerce, Stockholm – which is situated on 14 islands and has been coined the ‘Venice of the North’ – is the most rapidly growing city in Europe. Moreover, around 500,000 of Stockholm’s residents are commuters. The new 21km Stockholm Bypass highway link is being built on the outskirts of the capital to cope with the city’s continuous growth and to make everyday life easier for residents by reducing traffic jams and improving air quality.
More than 18km of the bypass are up to 80m below ground level and pass under Sweden’s third-largest lake (Lake Mälaren) in three places. Once the bypass opens (scheduled for 2026), as many as 11,000 vehicles an hour (145,000 vehicles a day) will pass through the two separate tunnels travelling on three lanes in each direction. Whilst it would be easier to build an overground system of routes and bridges, Sweden is a leader in sustainable urban planning and is very focused on environmental preservation, so constructing a tunnel is regarded as the best approach under these circumstances. Moreover, the self-confessed goal of Sweden’s Ministry of Transport is to complete the project while creating the smallest-possible CO2 footprint in the process.
Constructing mega-tunnels such as the Stockholm Bypass project generates millions of tonnes of rubble. A series of conveyor belt systems are being used to transport the extracted rock to three temporary ports that have been set up for the project. The rubble is transported across the waterways by inshore vessels from the construction site in Stockholm to Jehander’s quarry in Löten. Transportation by sea has proven to be a much more efficient mode of transport than using truck fleets, as ships can carry between 1,500 and 3,000 tonnes of rock per load, whereas trucks can manage only 35 tonnes. As many as four fully loaded ships a day arrive at Jehander’s port facility.
The rubble is reused in concrete, mostly for use in road construction, including the new bypass itself, or for the construction of houses and offices in Stockholm and the surrounding area. But first the rock has to be washed, crushed and treated at Löten Quarry – one of six strategically located quarries that Jehander operate in the Stockholm area.
‘Here at Löten Quarry, our textile conveyor belts are currently working at full speed as a result of the major bypass construction project,’ explained Continental’s Daniel Grimes. ‘They have proven to be an exceptionally reliable solution on numerous projects that building materials company HeidelbergCement and their subsidiaries have worked on in Sweden, as well as on projects all over the world.’
Substantiating these comments, Jehander’s Niclas Pettersson said: ‘So far we have taken roughly 7% of the total 5.5 million tonnes of rock that need to be processed out of the tunnel. For this undertaking we can count not only on the quality and long service life of Continental’s conveyor belts, but also on the smooth operation of the systems. Service plays just as big a role as the high-quality products and systems in our long-standing partnership.’
Service partner Continental’s tight-knit network means that they can offer their customers a local service with everything from a single source – from technical advice, extensive planning and engineer-driven development through to the manufacturing, installation, commissioning, maintenance and monitoring of complex conveyor systems and the delivery of conveyor belts and components.
‘Our range of round-the-clock services also includes assistance with conveyor belt replacement and arranging for the belts to be vulcanized or repaired with local partners, where required. This is how we ensure that the systems keep going. It is this combination of quality products, professional expertise, customer focus and our understanding of the local culture that makes us successful in this market,’ said Mr Grimes.
Moreover, Continental say they have a suitable conveyor belt in their range to meet customers’ construction requirements, whatever they may be. For example, steel-cord conveyor belts are suitable for particularly high-stress transportation requirements, whilst corrugated-sidewall belts, which take up very little space, are particularly suitable for building suburban rail networks. They emit very low noise levels, which is especially important in cities, and can convey bulk material at vertical angles and lifting heights of 400m and clear away up to 6,000 tonnes of rubble an hour. Conveyor belts also have clear advantages over trucks when it comes to tunnel construction. Using them means that no extra exhaust systems have to be installed during the tunnel works, because conveyor system solutions do not produce any emissions.
Sweden demonstrates its capacity for innovation time and again with construction projects such as the bypass, large parts of which are being built underground. This fact is also confirmed by this year’s Global Innovation Index in which Sweden is ranked third out of a total 126 economies, behind Switzerland and the Netherlands. ‘For my whole team here in Sweden, it is really special for Continental to be involved in this major pioneering project,’ said Mr Grimes.
Continental products are also passing the acid test for the tunnel expansion part of the project. Stockholm is built on top of solid rock, which poses some real challenges for the tunnel builders. Drilling equipment from Epiroc, one of the leading productivity partners for the mining, infrastructure and natural resources industries, is being used to drill the blastholes. It can cover transverse sections of rock in excess of 100m2, which makes the process as economical as possible. The drill rigs use as many as three extension arms, placing a huge strain on the tyres when the machines are in motion, which is why they are fitted with Continental DrillMaster premium tyres.
High cut resistance, good traction and stability are qualities that are essential for tyres under these working conditions, and the Continental DrillMaster with its V-ply design is said to be the perfect choice here. A highly cut-resistant rubber compound protects the carcass of the tyres in environments where there is freshly blasted rock. The tyre carcass is also specially equipped for the heavy loads and its innovative zig-zag tread design features a maximum number of gripping edges in all directions. These features allow the machines to cope with extreme gradients and downhill slopes, and to undertake cornering manoeuvres safely. For further information visit: www.continental.com
- Subscribe to Quarry Management, the monthly journal for the mineral products industry, to read articles before they appear on Agg-Net.com