Wearing Well
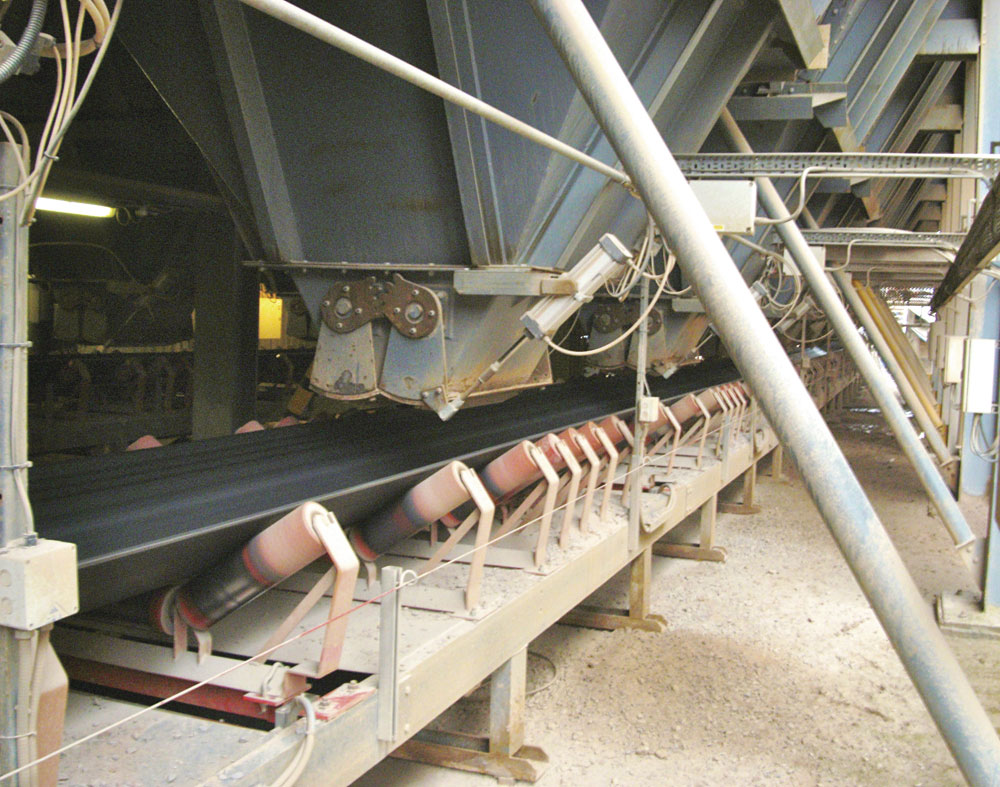
Ceramic, metallic and polymer wear protection systems deliver longevity to feeding conveying and storage plant
Wear resulting from sliding abrasion and impact is a constant problem across all quarrying plant involved in the feeding, conveying and storage of minerals and both semi-finished and finished products. But it is not a constant in terms of its effects, which occur to varying degrees in different parts of the plant. In a hopper, for example, the sloping section at the discharge chute suffers both impact and sliding abrasion, leading to higher wear rates than those experienced on the vertical hopper sides. However, the number of solutions actually used in quarrying to combat wear does not reflect this discrepancy in wear rates. There are a number of reasons for this. First: cost – traditional wear-protection methods are initially cheaper. Second: best-practice recommendations from industry associations. Third: existing contractual requirements for maintenance that mean a quarry is locked in to particular protection systems.
‘Added to the above is the issue of what level of wear protection is provided when the plant is new,’ said John Connolly of wear- protection specialists Kingfisher Industrial. ‘This often determines what the plant protection policy will be going forward. There is a dichotomy that exists between the needs of the original equipment manufacturer (OEM) and those of quarry maintenance managers and engineers. The OEM has to achieve the lowest installed cost for new equipment, in order to comply with project costs, while the maintenance manager is looking for minimized whole-life costs from improved equipment reliability and longer operating life. Unfortunately, the result of this conflict of demands is usually that the wear-protection system employed is often barely adequate, and will require replacing, sometimes within months.’
Traditionally, metallic materials such as quenched and tempered steel (QT) and manganese plate and castings have been used as wear-protection solutions in the various quarrying operations where the product is handled and crushed down to a minus-sized aggregate. As further processing is undertaken for sand and small aggregate, polymer-type materials such as rubber and polyurethane operating in a hydraulic state have been used with success. As with all solutions to problems, careful consideration has to be given in identifying what unique issues associated with grades and mineral types are prevalent, as a ‘one size fits all’ approach very rarely succeeds.
In the area of feeders, steel-backed rubber lining plates have provided a traditional solution to wear from sliding abrasion. However, where the material is particularly hard (eg granite), feed size is large and throughput is high, these liners struggle to provide the operating life required for optimum plant efficiency. The solution to this problem is increasingly provided by ceramic liners, which are easy to cut and shape to fit, and provide far superior resistance to impact-induced abrasion and sliding friction from crushed rock and stone. However, this is not exclusive, as Kingfisher have also had great success with their metallic (K-CLAD or K-HARD) and polymer (K-TEX) materials.
‘Depending on the size of the product being fed or conveyed, we would use either metallic and rubber linings for handling +150mm product sizes, and ceramic and polymer for handling –150mm product sizes, processing rock, stone, gravel, grit and sand,’ said Mr Connolly. ‘Also, the height of loading needs to be factored into the decision-making process, as the longer the product is in free-fall, the greater the velocity and hence the greater the impact.
‘It is important for continuity of operation that metallic linings offer the benefits of being easy to install, initially, and simple to replace. Where the requirement is not only for excellent resistance to impact abrasion and corrosion, but also noise abatement, then we would offer a rubber (polymer) lining system.’
In the conveying area, protection against wear can be complemented by increased flow efficiency as a result of using ceramic lining solutions. On conveyor chute systems, the extreme hardness characteristics of ceramic liners prevents wear from compromising the integrity of the system as the liner surface becomes polished due to counteracting the constant abrasion. This results in a very low coefficient of friction, which improves efficiency and eliminates continual maintenance and unplanned cleaning operations from this part of the process. The combination of various grades of ceramic materials can also take into account the differing levels of wear at various points in the conveying system. The linings are supplied in various thicknesses, guaranteeing long-term protection (10–12 years or more) against perforation of the fabrication, and against any damaging discharges.
‘In addition to ceramics, we have also achieved particular success in quarry conveyor applications with our K-PLAS low-friction polymer lining system,’ said Mr Connolly. ‘Lightweight, quick and uncomplicated to install, the material provides a sacrificial liner that guards against wear while at the same time allowing total discharge of product, thereby allowing operators to achieve maximum efficiency of discharge versus load. In the correct application, a 10–20mm thick lining offers comparable performance to various grades of stainless and abrasion-resistant steel plate, and is well suited to materials such as chalk, limestone and gypsum.’
Ceramic lining solutions are generally the optimum for lining storage bins (or hoppers) against wear. However, they are generally part of a two-stage wear-protection system; this the result of the different levels of wear experienced on the vertical and sloping sides of the bins.
One combination that is proving itself over long operating periods is the use of traditional abrasion-resistant QT wear plate installed on the vertical walls, fused cast basalt lining systems installed in the non-impact areas of the top sloping walls of the hoppers, and high-alumina ceramic tiles installed on the high-impact and main wear areas of the discharge chute section. The fused basalt lining is designed for conveying and storage systems that require high resistance to friction-induced abrasion. The material has an extremely hard and smooth surface, which offers the added advantage of improving material flow.
In the sloping discharge section of the bins, the problem is both sliding friction and impact abrasion, which calls for high-alumina ceramic liners. These are easy to shape and fit, and have a smooth low-friction surface that progressively polishes during use, preventing material build-up and improving material flow.
The value of ceramic solutions is evidenced by an ongoing application at a major quarry in the east of England. Five years ago, Kingfisher provided their K-ALOX ceramic solution to the discharge sections of a number of storage bins at the quarry.
The K-ALOX tiles replaced steel liners that were not lasting six months, due to high levels of impact abrasion and sliding friction from handling granite. The installation was recently inspected as part of Kingfisher’s 10-year warranty and was found to have negligible levels of wear, despite having handled over 15 million tonnes of granite over the five-year period.
For further information contact Kingfisher Ltd on tel: (01384) 410777; or email: enquiries@kingfisher-industrial.co.uk