Tough Choices Made Simpler
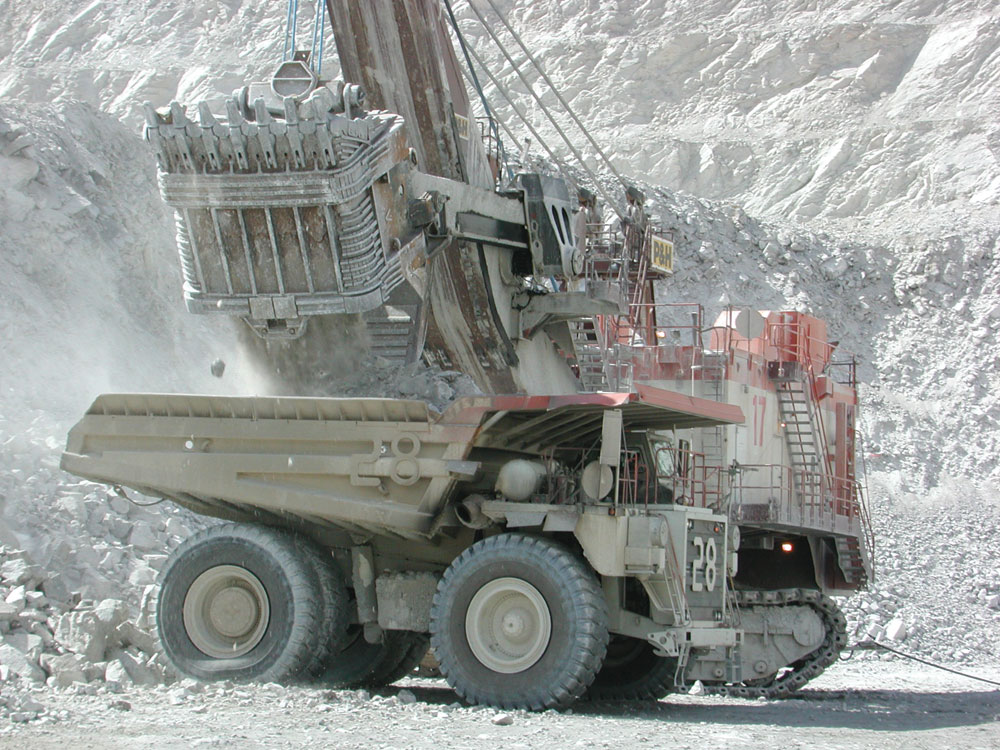
Assessing wear protection and wear plate service life
During the last two decades SSAB Oxelösund AB, market leaders in the production of quenched and tempered steel, have systematically built up a detailed knowledge of wear — to a large extent related to the company’s HARDOX abrasion-resistance product programme. As a result, wear technologists at SSAB have developed a wear theory which forms the basis of a wear-prediction model that is currently available as a commercial product known as WearCalc.
Selected customers can receive extra support in the form of an investigation of their mobile plant and/or process equipment from a wear perspective, resulting in a written report detailing the estimated wear life of the different steels used in various applications. This article presents an example of one such report which, although quite general in nature, does refer to a real case.
The objective of the report was to estimate the abrasiveness of the two types of rock handled and processed at an anonymous mine (referred to herein as the XAX Mine). Samples were taken from both the ore and the waste rock and two different assessments were performed and documented for each rock sample, one estimating ‘slide abrasiveness’ and the other estimating ‘impact abrasiveness’.
Such assessments are ‘relative’ in nature and lead to a ranking list showing the ‘relative wear life’ of the studied steel materials. The assessments were based on the ‘relative wear method’ developed by SSAB, which offers ‘engineering accuracy’ and involves both field trials and laboratory testing.
The two rock samples were petrographically examined to determine their mineral content as this governs their ‘abrasive-ness’. Based on the volume percentage of the minerals present, a relative wear assess-ment was performed according to the ‘relative wear method’.
MINERAL DESCRIPTION OF THE XAX ROCKS
Petrographical examination of the rock samples was carried out by an independent geological institute. The validity of the samples was not assessed by SSAB and, owing to the small amount of rock sampled, some uncertainty may be justified.
The samples were crushed to a very fine powder and then qualitatively and quantitatively analyzed using a Siemens D5000 diffractometer. The quantitative analysis was supported by a chemical examination partly performed at SSAB’s chemical laboratory in Oxelösund.
The objective of the examination was to identify the volume percentage of the constituent minerals in the XAX ore and waste rock samples (figs. 1 and 2). The subsequent wear assessments were based on this volume percentage, where a high proportion of a particular mineral equates to an equally high probability that that mineral will come into contact with the steel surface.
Volume percentage of minerals in the XAX ore sample
Mineral Volume Hardness
(%) (HV)
Amphibole 16 360–725
Biotite 4 30–60
Chalcopyrite 42 100–150
Chlorite 4 20–30
Pentlandite 4 100–150
Plagioclase 13 725–940
Pyrrhotite 14 150
Quartz 3 1,070
Trace amounts of other minerals were also identified but due to their very low concentrations these were not included in this assessment.
Volume percentage of minerals in the XAX waste rock sample
Mineral Volume Hardness
(%) (HV)
Amphibole 7 360–725
Biotite 2 30–60
Chalcopyrite 1 100–150
Chlorite 13 20–30
Feldspar 7 725
Plagioclase 56 725–940
Quartz 14 1,070
It can be seen that the range of mineral hardnesses is quite wide and it should also be noted that some of the mineral names cover a group of minerals, eg amphibole is the name of a group comprising 10 different minerals.
SLIDE WEAR FROM THE XAX ROCKS
The waste rock appears to be more abrasive than the ore but this varies depending on the steel grade studied. For HARDOX 400 the waste rock is 2.1 times more abrasive than the ore while for HARDOX 600 it is 40% more abrasive.
General discussion on slide wear
A wear-resistant metallic material can be subjected to four different types of ‘surface damage’:
- micro cracking
- cutting
- plastic deformation
- micro-structural transformation
In very rare cases micro-cracking damage may occur, however this is more common in ceramics and some castings.
Cutting surface damage occurs when the abrading body has a ‘particular’ degree of sharpness and hardness. It has been found that the abrasive body has to be at least 1.8 times harder than the steel surface in order to maintain its ‘cutting sharpness’.
The red line on the graph in figure 4 demonstrates the relationship between plate hardness (HARDOX) and the relative wear rates when ‘cutting’ damage is the prevailing wear mechanism.
The most common form of surface damage is the ‘plastic deformation’ that occurs when the abrading body is ‘rounded’ or ‘soft’. The expression ‘soft’ is again a relative term. If the hardness of the abrading body is less than 1.5 times the hardness of the steel surface, plastic deformation will be the prevailing form of damage. The blue line on the graph shows the relationship between plate hardness and the relative wear rates for plastic deformation damage. A mild steel subjected to plastic deformation wear is given the relative wear rate of 1.0.
The fourth type of damage, defined as micro-structural transformation, occurs in all materials. Here, the severe heat and pressure generated during short but intensive abrasive contacts create ‘abrasive reactive zones’. The surface layer is sometimes ‘requenched’ and the following thin layers are annealed and, with increasing depth, also subjected to a gradual diminishing plastic deformation hardening. This type of surface damage occurs continually but is not yet included as a quantified relative wear rate.
The variety of minerals in a rock will create different types of surface damage in various HARDOX grades. Thus, the XAX ore, for example, results in an ‘abrasiveness curve’ somewhere in between the two outer surface damage curves (see fig. 5).
This curve can be transformed and expressed as a relative service-life curve, where relative service life is defined for any selected ‘reference grade’ of steel. In WearCalc mild steel is given as the first reference grade, however it is possible to select any preferred reference grade.
Relative slide wear of other wear-resistant materials
The relative wear method was developed to assess different HARDOX grades in various applications, so how can materials like high-chrome white-iron (HCWI) hardfacings and manganese plates be assessed? Although these two materials offer wear resistance based on material properties other than hardness, it has, through combined tests, been possible to find equivalent relationships for comparison within the relative wear method.
The following calculations are based on hardfacings with an optimized size and distribution of carbides. Also, it has been seen that the hardfacing layer tends to delaminate and once the mild steel plate is exposed, even in a limited area, the residual life of the wear part becomes shortened. The actual service life of hardfacing materials might, therefore, be shorter than that shown in the caluclations. No further explanation is given here, however the relative service life of both HCWI and manganese is presented in the various tables.
XAX ore
This rock contains a lot of ‘softer’ minerals. The abrasiveness calculated using WearCalc shows that HARDOX steels are mainly subjected to the lower-intensity ‘plastic deformation’ surface damage, although the total surface damage caused by the XAX ore does include a smaller contribution from the more severe ‘cutting wear’ form of surface damage.
The following relative wear rates can be derived from WearCalc:
Mild steel 1.64
HARDOX 400 0.82
HARDOX 450 0.59
HARDOX 500 0.42
HARDOX 600 0.13
HCWI hardfacing 0.08
However, the ranking of materials in terms of relative wear life is preferable. The graph in figure 7 shows the conversion of the relative wear rates in the abrasiveness curve (fig. 6) into a relative wear life curve.
The relative wear life values converted from the table above are:
Mild steel 1.0 (chosen as initial reference)
HARDOX 400 1.9 1.00
HARDOX 450 2.9 1.52
HARDOX 500 3.9 2.05
HARDOX 600 12.4 6.52
HCWI hardfacing 20.5 10.70
Thus, if HARDOX 600 is used, wear life equal to HCWI hardfacing is reached if the HARDOX plate is 10.7 ÷ 6.52 = 1.64 times thicker than the hardfacing layer. This layer is usually 6mm thick, therefore a 6 x 1.64mm = 10mm HARDOX 600 plate would be expected to last as long as HCWI hardfacing.
XAX waste rock
The procedure is similar for the XAX waste rock and therefore only the results are presented here.
The following relative wear rates can be derived from WearCalc:
Mild steel 2.68
HARDOX 400 1.72
HARDOX 450 1.11
HARDOX 500 0.86
HARDOX 600 0.18
HCWI hardfacing 0.08
The relative wear life values converted from the table above are:
Mild steel 1.0 (chosen as initial reference)
HARDOX 400 1.6 1.00
HARDOX 450 2.5 1.56
HARDOX 500 3.1 1.93
HARDOX 600 15.1 9.43
HCWI hardfacing 33.5 20.90
In slide wear applications handling XAX waste rock, the thickness of HARDOX 600 equivalent to a ‘better than average’ HCWI hardfacing is 20.9 ÷ 9.43 = 2.2. Thus, a 15mm HARDOX 600 plate would last at least as long as a 6mm layer of HCWI hardfacing on a mild steel plate.
IMPACT WEAR FROM THE XAX ROCKS
The impacting action of a rock creates different sets of damage on steel surfaces. The criteria for creating these higher wear rates are somewhat different from slide wear. On a mineralogical level the mineral hardness has to exceed the hardness of the steel surface by 1.2 (relative hardness) in order to create the severe damage known as ‘platelet formation’. If the relative hardness of the mineral is less than 0.8 times the hardness of the plate surface, the milder surface damage known as ‘mangling’ will prevail.
However, at the level of individual rocks the relative wear model has not yet been verified. So far indications strongly point to the fact that rocks (golf ball size and larger) mainly create a specific plastic deformation (mangling) damage with only limited influence from the mineral content. Generally, the outer profile and compressive strength of the rock will be the main cause of damage. Those minerals in actual contact with the steel will cause some local damage.
During testing of the XAX rocks mineral composition was observed to have a 10–20% influence on impact wear, and therefore in this particular assessment a 15% mineral content influence has been assumed. The 15% reference relates to the type of surface damage caused by the mineral composition during impact wear situations, where the surface damage is very small in depth, eg the type of damage occurring in ‘erosive’ situations.
Generally, increasing the hardness of the plate has been found to lead to greater improvements in slide wear life than in impact wear life.
Impact wear from XAX ore
The graph in figure 10 shows the relative impact wear rate for a number of steel grades at different impact angles. The average relative wear rate is also calculated by this version of the WearCalc impact module.
The average relative wear rates (not shown directly in fig. 10) are:
Mild steel 0.21
HARDOX 400 0.12
HARDOX 450 0.10
HARDOX 500 0.08
HARDOX 600 0.05
Converted to relative service-life values:
Mild steel 1.00
HARDOX 400 1.75 1.00
HARDOX 450 2.10 1.20
HARDOX 500 2.62 1.50
HARDOX 600 4.20 2.40
Impact wear from XAX waste rock
The procedure for the XAX waste rock is similar to the procedure for XAX ore and therefore only the results are presented.
The average relative wear rates are:
Mild steel 0.28
HARDOX 400 0.21
HARDOX 450 0.19
HARDOX 500 0.17
HARDOX 600 0.14
Converted to relative wear life values:
Mild steel 1.00
HARDOX 400 1.33 1.00
HARDOX 450 1.47 1.10
HARDOX 500 1.64 1.22
HARDOX 600 2.00 1.50
Other materials subjected to impact wear from XAX rocks
Two other materials are of interest in a general comparison of wear-resistant materials — high-chrome white iron (HCWI) in hardfaced overlay plates and traditional manganese plates (12% Mn).
Manganese plate
Different types of manganese steel are commercially available but the most common form is the traditional 12% composition. The 18 % grade is increasingly being used in crusher castings.
The initial hardness of 12% Mn grade steel is usually 260–280 Brinell. Its wear resistance may partially be described by its ability to be deformed and transformed to a higher hardness. If 12% Mn steel subjected to higher levels of abrasive surface deformation is locally hardened to its maximum hardness (550 Brinell), it performs like a quenched and tempered (QT) steel plate of 550 Brinell initial hardness. When the deformation of the surface is low, the 12% Mn plate reacts more like a QT plate of 280 Brinell hardness.
In this impact abrasiveness assessment of the XAX rock, an initial conservative estimate of the Mn plate as a 550 Brinell QT plate has been adopted. This gives the following relative wear life values:
XAX ore XAX waste rock
HARDOX 400 1.0 1.0
HARDOX 500 1.50 1.22
HARDOX 600 2.40 1.50
12% Mn (550HB) 1.93 1.39
High-chrome white-iron hardfacing overlay plate
The assessment of the HCWI overlay plate is more complicated. During erosive testing it has been found that when the mineral particles are very hard or small enough to create preferential wear, the relative wear rate of HCWI may be 2.0 at 90°, whereas mild steel is 1.0 and HARDOX 600 is 1.25 (a very surprising mechanical response, but for very hard particles at higher velocities the ductility of the mild steel seems to be beneficial). Below a 45° angle of impact, a harder material always seems to be better than a softer one, irrespective of the particle hardness.
In the case of ‘round’ or ‘soft’ particles, the relative wear rate of the HCWI was observed to be in the very low region of 0.0125 to 0.0375. These wear rates have to be related to the reference relative wear rate of mild steel (1.0) subjected to very hard particles at 90° (platelet damage). The relative wear rate for mild steel in this model is 0.25 when subjected to less-aggressive plastic deformation (mangling).
In a more detailed analysis, the size of the minerals in the rock has to be related to the distance between the carbides in the HCWI. Since this can seldom be measured, all minerals harder than the ‘bulk hardness’ of the HCWI have to be regarded as ‘hard’. These will generate ‘platelet damage’ with a relative wear rate of 2.0 in the HCWI. All other minerals will generate ‘mangling’ damage with relative wear rates between 0.0125 and 0.0375.
The bulk hardness of HCWI hardfacing overlay plates is usually in the region of 850–950 HV. If all minerals above 950
are considered as ‘hard’ in relation to the HCWI bulk hardness, only quartz in the XAX rocks will have the capacity to cause more severe surface damage.
The following relative wear rates are assumed according to previous experience and the reasoning above:
HCWI HARDOX 600
XAX ore 0.020 0.05
XAX waste rock 0.059 0.14
These relative wear rates can be compared to the values of the other steel grades shown earlier in this section. The relative wear life values of HCWI are shown in the following summary:
XAX ore XAX waste rock
HARDOX 400 1.00 1.00
HARDOX 450 1.20 1.10
HARDOX 500 1.50 1.22
HARDOX 600 2.40 1.50
HCWI hardfacing 6.0 3.55
12% Mn plate 1.93 1.39
CONCLUSIONS
In optimizing the running of a quarry operation a key task is to find the best wear parts for the particular conditions within the quarry. The service life of wear parts is very much dependant on the hardness of the rock, how the operation is run and the hardness of the materials used to make the wear parts, however wear part selection should always be made in such a way that minimum total cost is achieved.
Knowing the hardness of the rock or mineral being handled, it is now possible to calculate relative wear when choosing between different hardnesses of wear-resistant products. The wear situation within a quarry can vary however, with slide wear and impact wear being the two main components. In both cases there are calculation models based on wear theory and laboratory and field tests.
The relative wear life values deduced from these models are ‘mechanical estimates’. Other factors affecting the function of wear parts, such as corrosion and temperatures exceeding 400°F, are not taken into consideration in these estimates. In the case of acidic mine water, the relative wear life values may have to be adjusted. In an active chemical environment the expected advantage of a HARDOX grade, as estimated by WearCalc, may be partially reduced. For example, under moist or mild acidic conditions the corrosion rate of wear-resistant steel is roughly equal to mild steel.
Nevertheless, as the basis for an initial assessment, the estimates from WearCalc have, during the last 10 years, shown an acceptable level of accuracy.
The authors, Ulf Bergkvist, Claes Lowgren and Morgan Lofvenholm, are application engineer, market developer and research engineer, respectively, with SSAB Oxelosund AB